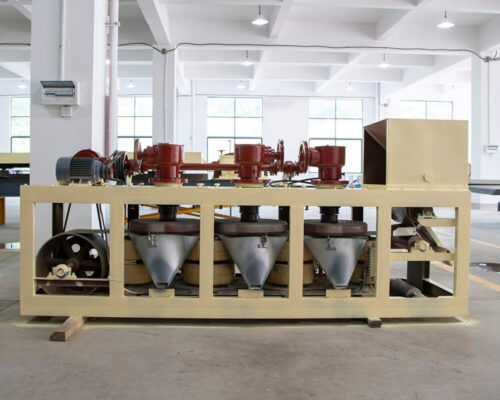
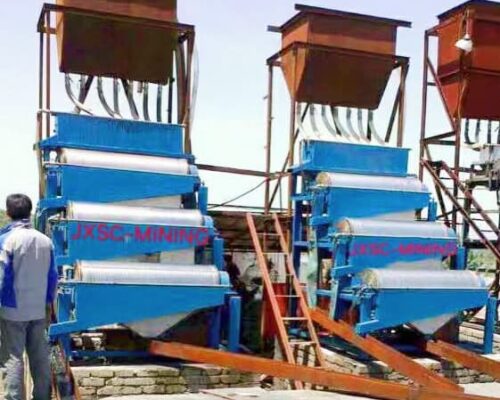
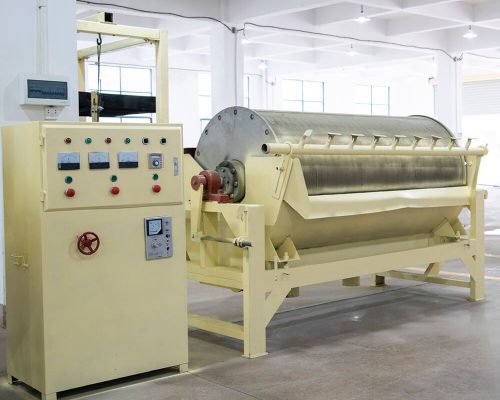
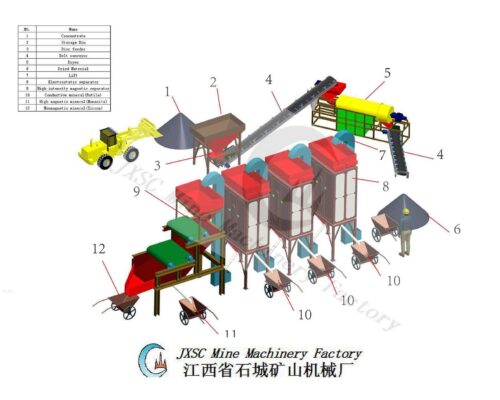
Zircon Beneficiation Plant
Zircon sand beneficiation is removing impurity minerals from zircon sand ore and increasing the content of zircon sand ore. We determine the beneficiation process and equipment configuration according to the zircon placer’s specific mineral composition and properties. The common zircon sand beneficiation process is a composite beneficiation process, including gravity separation, flotation, electric separation, magnetic separation, etc.
Zircon Mining Plant
Introduction
About Zircon
Zircon is common in the crust of Earth. It is a mineral belonging to the nesosilicates group and a source of the metal zirconium. Zircon is fairly hard (with a Mohs hardness of 7.5) and chemically stable, so it is highly resistant to weathering. It is also resistant to heat, so detrital zircon grains are sometimes preserved in igneous rocks formed from melted sediments. Its resistance to weathering and relatively high specific gravity (4.68) makes it an essential component of sandstone’s heavy mineral fraction. Zircon is a common accessory mineral in igneous rocks, metamorphic rocks, and as detrital grains in sedimentary rocks.
The natural color of zircon varies between colorless, yellow-golden, red, brown, blue, and green. Zircon is mainly consumed as an opacifier and used in the decorative ceramics industry. It is also used in refractories, foundry casting, and a growing array of specialty applications such as zirconia and zirconium chemicals, including nuclear fuel rods, catalytic fuel converters, and water and air purification systems. Zircon is one of the critical minerals used by geologists for geochronology.
Zircon Sand
Zircon (zirconium silicate) sands are naturally occurring, rounded sands used in foundry, ceramic, refractory, and precision investment casting applications. They are critical components in producing glazes, ladle brick, wall tiles, coatings, shell molds and cores, and metal chills.
Zircon is one of the two core product streams from “mineral sands,” the other being titanium minerals (ilmenite, leucoxene and rutile).
Mineral Processing
Zircon Beneficiation Process
Zircon sand beneficiation is removing impurity minerals from zircon sand ore and increasing the content of zircon sand ore. This process must determine the beneficiation process and equipment configuration according to the zircon placer’s specific mineral composition and properties. The commonly used zircon sand beneficiation process is a composite beneficiation process, including gravity separation, flotation, electric separation, magnetic separation, etc.
1. Gravity separation
Gravity separation is a commonly used beneficiation method for zircon placer. Due to the relatively large proportion of zircon sand, the proportion of associated gangue impurities is relatively small, and the content of zircon sand in coastal placer is relatively low. Therefore, in the roughing stage, most zircon sand beneficiation adopts energy-saving gravity separation methods, using the jig concentrator, shaker table, and other gravity selection equipment.
2. Flotation
Flotation is also a method of separating gangue and associated impurities of zircon sand. Commonly used collectors are fatty acids, regulators are sodium carbonate, and activators are sodium sulfide and heavy metal salts. Due to a large number of associated minerals, the flotation method also needs to design the process and flotation system according to the specific composition of the minerals.
3. Electric separation
The electric separation uses the difference in magnetic permeability between minerals to separate zircon sand from associated point minerals such as ilmenite, hematite, chromite, cassiterite, and rutile, and non-conductive minerals such as zircon, monazite, garnet, and phosphorus isolated from limestone. The electro-separation method requires high mineral requirements and usually requires desliming, grading, and drying before beneficiation.
4. Magnetic separation
The magnetic separation method separates the magnetic substances in the zircon sand heavy concentrate, and the separation generally adopts a wet magnetic separator. According to the specific mineral composition, designing a suitable magnetic field mechanism and magnetic field strength greatly influences the effect of magnetic separation.
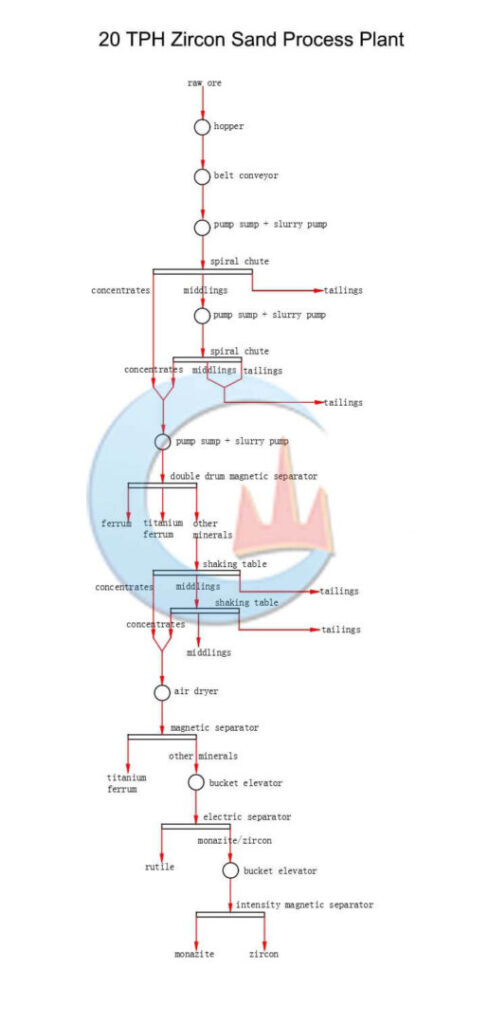
100TPH Beach Sand Processing Plant
Zircon Sand Separation
The properties of zircon-associated minerals are different, and various beneficiation methods such as gravity separation, magnetism, flotation, and electric separation are used. The specific beneficiation process is related to the types of associated beneficial minerals.
Accompanying organisms and their beneficiation methods
- Rutile, zircon: Electric separation – magnetic separation – flotation;
- Monazite: Magnetic separation – shaker table – magnetic separation;
- Cassiterite, monazite, rutile, zircon: Magnetic separation – shaking table – magnetic separation – shaking table – electric separation – magnetic separation.
The beneficiation and separation of zircon sand and other heavy minerals usually include two processes stages-wet beneficiation and dry separation.
The placer ore is first sieved to obtain the ore size suitable for wet gravity separation. Usually, coarse particles larger than 2nm are removed (heavy minerals are generally below 0.3mm). Wet gravity separation aims to minimize the loss of valuable minerals and obtain heavy mineral enrichment (coarse concentrate). The commonly used gravity separation equipment is a cone concentrator or a spiral washer.
IIlmenite usually has the highest total content in rough concentrate. The most significant difference between it and rutile and zircon is that it has strong magnetism. In some beneficiation plants, strong magnetic separators separate them; in other beneficiation plants, dry the coarse concentrate first and then use a magnetic belt separator to separate the ilmenite. The rest are non-magnetic minerals such as zircon sand and rutile. According to their electrical differences (zircon has no conductivity, while rutile has strong conductivity), usually using a high-voltage electric separator Zircon, rutile, and monazite. The number of process stages or complexity of the beneficiation and purification process depends on the content of various minerals in the rough concentrate and the technical requirements for the concentrate product.