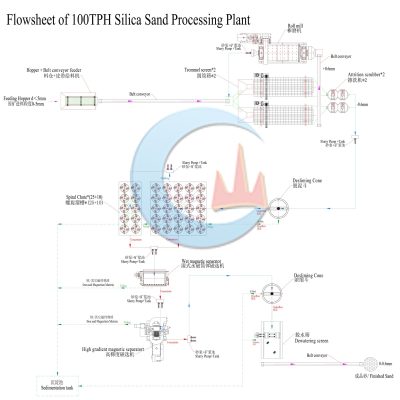
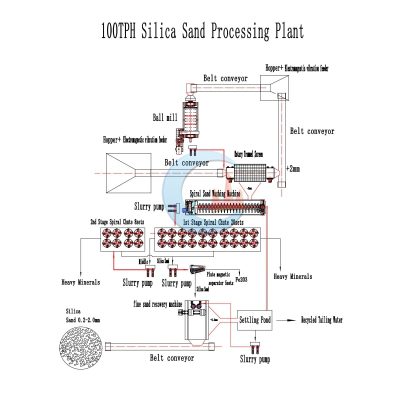
Silica Sand Processing
Silica sand processing plants are mainly aimed at removing impurities and improving the grade and particle size uniformity of silicon dioxide. Common silica sand beneficiation methods include washing, grading, scrubbing, gravity separation, hydraulic beneficiation, magnetic separation, flotation, etc.
Silica Sand Processing Plant
Introduction
About Silica
Silica (SiO₂) is a chemical compound of silicon and oxygen and is the most abundant mineral found on Earth. It exists in various forms, each with different properties and applications.
Properties of Silica
- Hardness: Silica is a relatively hard material, ranking 7 on the Mohs hardness scale.
- Chemical Resistance: It’s resistant to most acids (except hydrofluoric acid) and alkalis.
- Thermal Stability: It has a high melting point and good thermal stability.
- Insulating Properties: Depending on its form and purity, silica can exhibit good insulating properties.
- Optical Properties: High-purity silica is transparent and used in optical fibers.
Applications of Silica
- Glass Manufacturing: A primary use, forming the backbone of most glass products (e.g., windows, bottles, fiberglass).
- Concrete and Construction: Used as an aggregate in concrete and other construction materials.
- Electronics: Used in integrated circuits, semiconductors, and optical fibers.
- Abrasives: Its hardness makes it useful in abrasive blasting, sandpaper, and polishing compounds.
- Fillers: Used as a filler in paints, plastics, and rubber.
- Food Industry: Used as a food additive (e.g., anti-caking agent).
- Water Filtration: Used in water filters to remove impurities.
- Cosmetics and Personal Care Products: Used as an abrasive or thickening agent.
Silica Sand
Silica sand is a naturally occurring granular material composed mainly of silicon dioxide (SiO₂), in the form of quartz. It’s essentially sand where the majority of the grains are quartz particles. The color can vary depending on impurities, ranging from white or colorless to shades of yellow, brown, or even red. Its properties, such as grain size and purity, determine its suitability for different applications.
Mineral Processing
Silica Sand Processing
Silica sand processing involves several steps to transform raw silica sand into a product suitable for specific applications. The exact process varies depending on the desired purity and particle size distribution of the final product. Here are the general steps:
1. Crushing and Screening
- Crushing: Large chunks of rock or oversized sand particles are crushed to a manageable size using jaw crushers, cone crushers, or impact crushers. This step is often skipped if the raw material is already of a suitable size.
- Screening: Screens (sieves) of various mesh sizes are used to separate the sand into different particle size fractions. This ensures consistent particle size in the final product, which is crucial for many applications.
2. Washing and Classifying
- Washing: This removes clay, silt, and other impurities from the sand. This is often done using water jets or in large washing drums.
- Classifying: Further separation based on particle size and density might occur at this stage. Techniques include hydrocyclones or spiral classifiers.
3. Drying
The washed sand is then dried to reduce moisture content. This can be done using rotary dryers, fluidized bed dryers, or other drying methods. Low moisture content is essential for many applications to prevent clumping and improve handling.
4. Magnetic Separation
If the sand contains significant amounts of iron or other magnetic impurities, magnetic separators are used to remove them. This step is crucial for applications requiring high-purity silica.
Silica Sand Gravity Separation
Silica Sand Purification & Drying Plant
100TPH Silica Sand Processing Plant
Raw ore & Requirement
- Raw sand contains 5% clay.
- The maximum feeding size of raw sand is 20mm.
- The finished silica sand size the customer needs is less than 2mm.
- Raw sand contains 1% Fe2O3, the customer’s requirement for removing Fe2O3 is less than 0.02%.
- Feeding capacity is 100 tons per hour.
- Over 2mm size proportion in raw sand is 20%.
According to this raw sand information, our engineer designed an efficient flowchart solution as follows:
Equipment
Electromagnetic vibrating feeder, belt conveyor, trommel screen, ball mill, spiral classifier, sand pump, spiral chute, plate magnetic separator, and fine sand recycling machine.
Flowchart
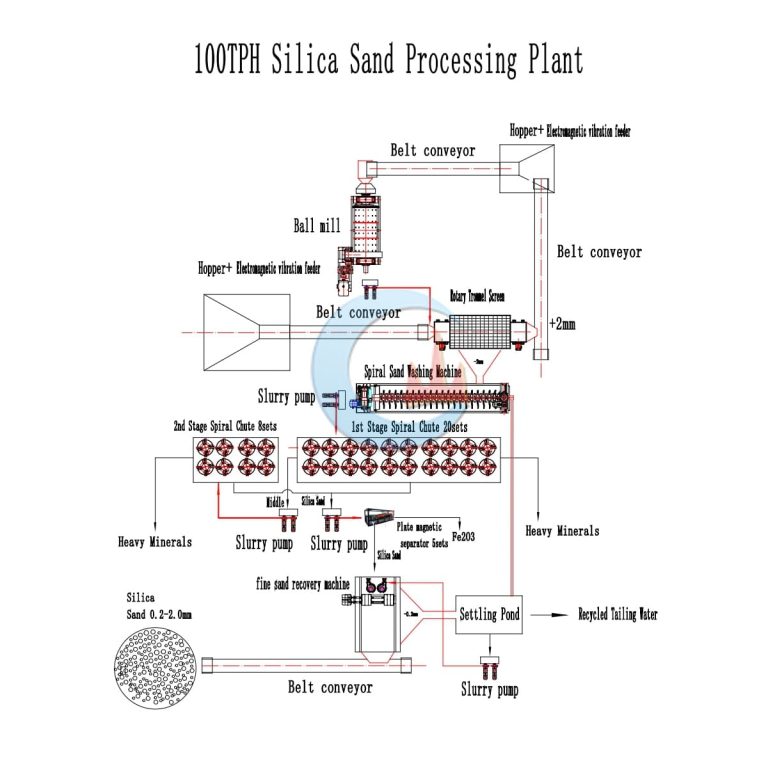
Process
- An excavator or loader sends raw sand to the raw material hopper, through an electromagnetic vibrating feeder evenly feeds sand to the belt conveyor, then to a trommel screen.
- The trommel screen with its hopper, has a screen with a 2mm hole size, screening out over 2mm and less than 2mm.
- Over 2mm of trommel screen go to one transit hopper via belt conveyor, then through an electromagnetic vibrating feeder, evenly fed to the belt conveyor, then to a ball mill for grinding to 2mm below. The output of the ball mill is sent to the trommel screen hopper with a sand pump.
- Less than 2mm of trommel screen flows to the spiral sand washing machine by gravity. Spiral sand washing has the function of washing clay and removing mud water. The washed sand goes to one tank, and using a sand pump sends it to 1st stage spiral chute.
- The function of a spiral chute is to separate heavy minerals from sand-like iron etc. The spiral chute generates three outputs: concentrate, middling, and tailing. Middlings may still contain some silica sand.
- The concentrate of 1st stage spiral chute goes to the concentrate tank, and middlings go to 2nd stage spiral chute with a sand pump for reprocessing.
- All concentrations from two stages spiral chute are sent to a plate magnetic separator with a sand pump for further removing Fe2O3, at this step the iron content will be reduced to less than 0.02%.
- The output of the plate magnetic separator is sent to a fine sand recycling system with a sand pump. The fine sand recycling system includes a hydrocyclone, dewatering screen, belt conveyor, and slurry pump. The function of the fine sand recycling system is recycling fine sand and dehydration and tailing water recycled use. The tailing water goes to the settling pond.
- Dewatered fine sand will be transported to the stockpile by belt conveyor. This is finished silica sand.
The whole process includes washing, gravity separation, and magnetic separation to make the finished silica sand clean and meet with customer’s requirement for iron content.