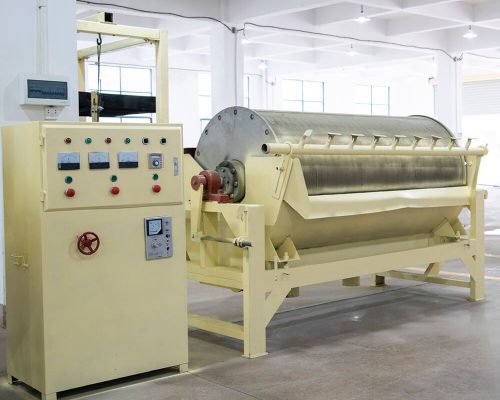
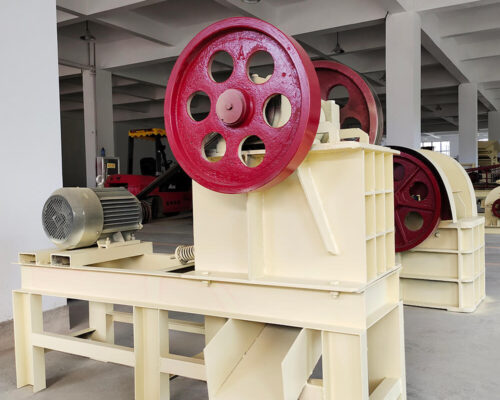
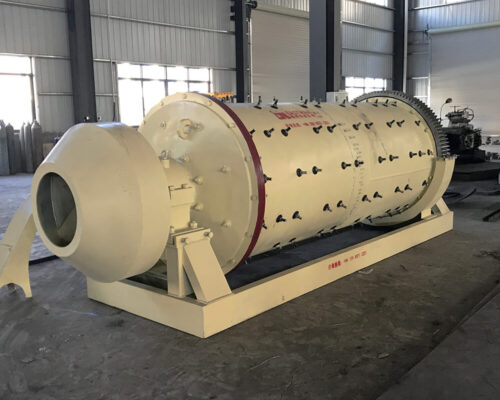
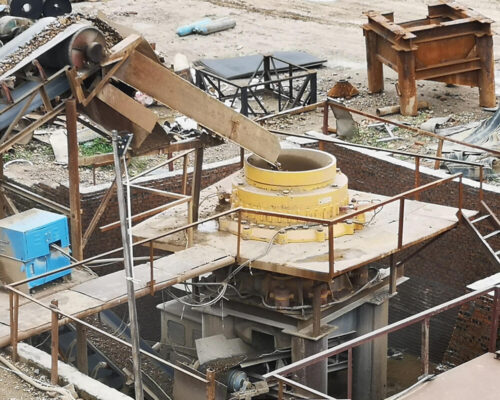
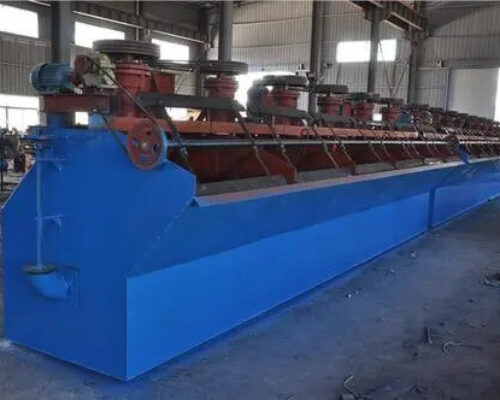
Quartz Beneficiation Process
The mineral beneficiation steps are generally crushing, grinding, sorting (purification), and concentration. The quartz ore beneficiation process also revolves around sorting and purifying the quartz sand. Quartz refinement is a complicated separation technology removing the bit or microimpurity and then gets concentrated quartz or high-purity quartz. The purification technologies of Quartz Sand are washing, classifying & desliming, scrubbing, magnetic separation, flotation, acid leaching, microbial leaching, etc.
Quartz Sand Beneficiation
Introduction
About Quartz
Quartz is a kind of mineral formed into crystals due to extreme pressure. As a chemical compound, it consists of one-part silicon and two-part oxygen. It is considered the most abundant mineral found on Earth’s surface. Through its unique properties, it became among the most useful minerals. Meanwhile, this mineral comes in varying colors, transparencies, and varieties. Amethyst, rose quartz, onyx, and tiger’s eye are some of the popular varieties of quartz. It is very abundant in sedimentary, metamorphic, and igneous rocks. It is known to be highly resistant to chemical and mechanical weathering.
When it comes to uses, the quartz’s color, diaphaneity, and luster make it ideal as a gemstone and for glass making. Since it has heat resistance and electrical properties, this mineral is helpful in electronic products.
Quartz Sand
Quartz sand is a kind of quartz grain produced by crushing quartz stone. Its color is milky white or colorless and translucent, and its hardness is seven on the Mohs scale. Quartz sand is an important industrial mineral raw material, non-chemical dangerous goods, widely used in glass, casting, ceramics, fireproof materials, ferrosilicon smelting, metallurgical flux, metallurgy, construction, chemical industry, plastics, rubber, abrasives, filter materials, and other industries.
Mineral Processing
Quartz Ore Beneficiation Process
The quartz ore beneficiation process is to crush the mined quartz ore. The qualified materials crushed by the crusher are evenly sent to the inside of the quartz ore ball mill through the elevator and the ore feeding equipment. The quartz ore ball mill will continue to crush and grind the materials. , the material ground by the ball mill is sent to the spiral classifier for cleaning and classification. The magnetic separator is used for preliminary separation and the flotation machine is used to separate the desired minerals from other substances. Finally, the concentrator is used to remove the minerals contained in the material. The moisture and drying equipment can dry the material, and then the quartz stone raw material required for production can be obtained.
Crushing
The jaw crusher, cone crusher, and other crushing equipment are used to form the crushing production process, and the quartz ore is crushed to a specific particle size, and the particle size of the quartz ore can reach 25mm, which is precisely the feed particle size of the next step of the quartz ore ball mill for grinding (of course crushing The particle size is better than 25mm, the more beneficial to the grinding operation).
Grinding
The crushed quartz ore is ground with a special grinding ball mill for quartz ore. After grinding, quartz ore powder within the range of 0.074 mm-0.89 mm can be obtained, which is convenient for the next step of grading and purification. In order to achieve the expected target more quickly in grinding quartz ore powder, the personnel who operate the quartz ore ball mill must strictly implement the requirements for feeding (≤25mm).
Purification
The purification production line composed of a classifier, magnetic separator, and flotation machine follows the principle of rough separation first and then fine selection. The quartz ore powder is cleaned and classified by the classifier first, and then the magnetic separator is used for preliminary separation. Finally, the flotation machine is used further to separate the quartz material from the complex minerals.
Concentration
Concentrators and dryers can concentrate and dry the separated quartz material, and dry, high-purity quartz products can be obtained, which can be directly applied in the industrial field.
30TPH Quartz Rock Crushing & Impurities Removal Processing Line
Quartz Sand Purification
Washing and classifying desliming
The SiO2 grade in Quartz Sand decreases by Quartz Sand size becoming finer, so washing and desliming of crude Quartz Sand are necessary before the next step.
Scrubbing
Scrubbing is the way to remove film iron and impurity minerals on the surface of quartz by mechanical force and crush these mineral aggregates. The Quartz Sand gets further purification by classification. There are two kinds of methods rob scrubbing and mechanical scrubbing.
Flotation
The separation of mica and quartz is difficult, the effective methods are an anionic collector in acid conditions and an anionic – cationic collector in alkaline conditions. The purification of Quartz Sand can reach 99% after scrubbing, desliming, magnetic separation, and flotation.
Acid Leaching
Dilute acid significantly affected removing iron and aluminum, concentrated acid for removing titanium and chromium, and mixed acid for mineral impurities. Control of various factors of acid leaching should be based on quartz final grade requirements, and as far as possible reduce the acid concentration, temperature, and dosage to achieve quartz purification.