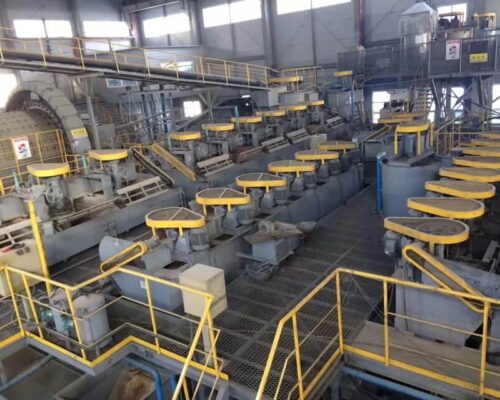
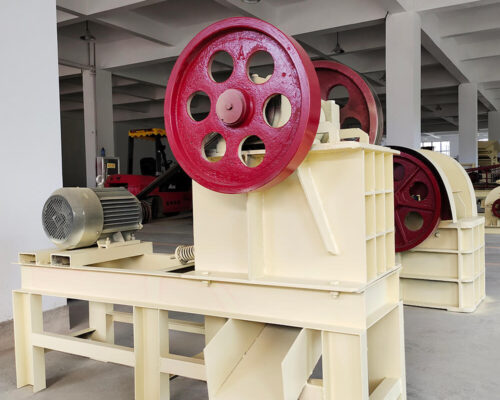
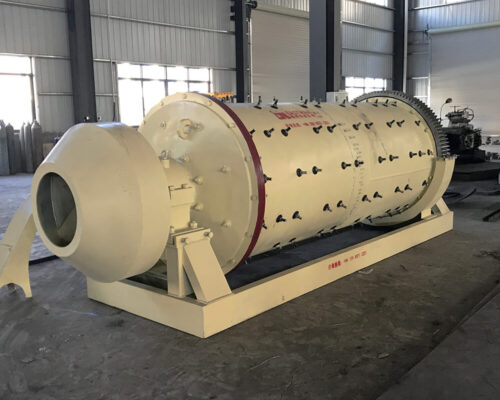
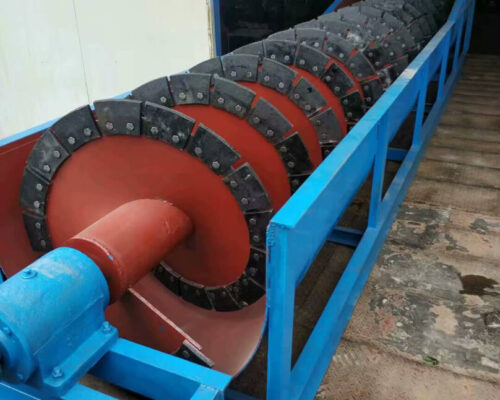
Pb-Zn Mineral Processing
Lead-zinc(Pb-Zn) ores are often symbiotic together, and the flotation method is generally used for beneficiation. After the Pb-Zn ore is crushed to a certain particle size, the heavy medium is used to remove the large and low-grade waste rock, and then the enriched ore is processed by the flotation method.
Pb-Zn Beneficiation Process
Introduction
About Pb-Cu
Lead and zinc are extremely close in nature, especially in primary deposits, and often coexist. Most of the lead-zinc minerals are sulfides and sulfates, and galena and sphalerite are the primary Pb-Zn ores.
Non-sulfide: It is formed due to hypogene and supergene weathering. Mostly oxide ores like zincite, and cerussite may fall under this category.
Mixed sulfide-oxide: It mostly occurs in the transition and occasionally in the oxidized zone of the deposit.
Pb-Zn ores divide into sulfide Pb-Zn ore and oxide Pb-Zn ore. The most widely used in separating sulfide Pb-Zn ore is flotation. The sulfide Pb-Zn ore process divides into priority flotation processes, mix-separating flotation, asynchronous flotation, and equal flotation process.
Mineral Processing
Pb-Zn Beneficiation Processing
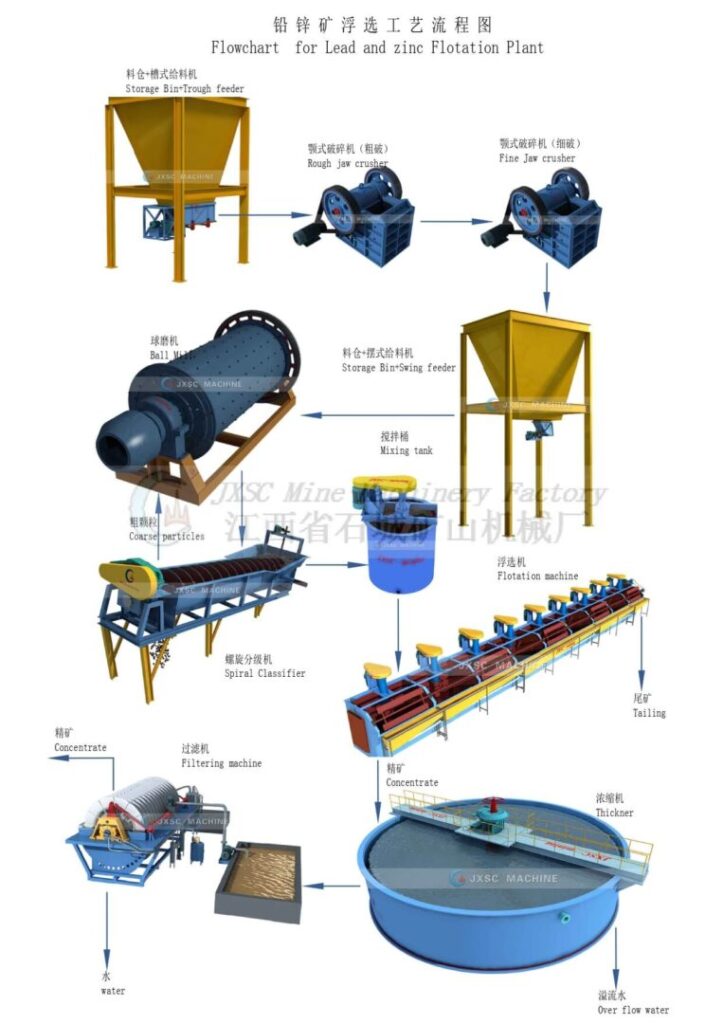
Preselection Discard
It is very economical to discard the waste rock as much as possible before the lead-zinc mine grinds. As long as the ore properties are suitable, adopt the preselection and discarding process measures as much as possible. The rejection rate of lead-zinc ore in heavy medium separation is generally 30% to 40% of the original ore.
Crush More and Grind Less
It is helpful to save energy and improve the production capacity of the ball mill, and both at home and abroad are studying to reduce the particle size of the final product of crushed ore.
Sorting of lead-zinc ore
The flotation method is still the primary method of lead-zinc dressing plants. The flotation process can summarize as a priority flotation process, a mix-separating flotation process, an asynchronous flotation process, and an equal floatation process.
- Priority flotation process
The process is to recover lead, zinc, and sulfur products by sequential flotation according to lead-zinc-sulfur floatability and flotation speed to obtain lead concentrate, zinc concentrate, and sulfur concentrate. This process has the advantages of reducing the volume of the flotation cell and saving flotation reagents.
- Mix-separation flotation process
The process is to select all sulfide lead and zinc minerals into the mixed concentrate and directly discard the tailings. Then, carry the process of separating lead and zinc after the mixed concentrate is demedicated, and the flotation separation effect of this process is better.
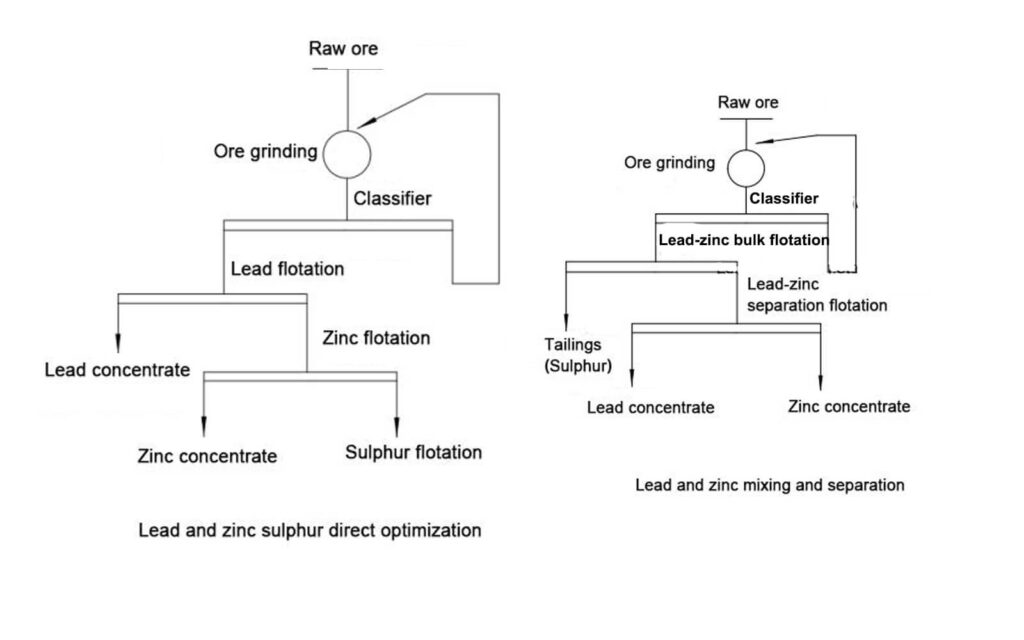
- Equal flotation process
When a small part of galena has similar flotability to most sphalerite, it can use an equal flotation process. During the preferential flotation of lead, let an amount of the zinc minerals with good floatability float simultaneously, and float the remaining lead minerals at the same time as the flotation of zinc. Then the lead concentrate is dezincified, and the zinc concentrate is deleaded to obtain lead and zinc concentrate.

- Asynchronous flotation process
In the flotation process, different minerals may have the same floatability, and the same mineral may have different floatability. The asynchronous flotation process is to carry out the mixed flotation of lead and zinc in stages to ensure the most effective floatability of minerals in a suitable condition.
Aiming at the inhomogeneity of the inlaid particle size of various minerals in the ore, the process flow of stage grinding and stage separation has been developed. To reduce the over-grinding of the fine-grained galena that dissociated from the monomer in time, we added a sorting operation to the grinding and classification circuit to improve the sorting index.
10TPH Lead, Zinc, Barite, and Various Sulfide Ores Flotation Process Plant
Raw material conditions
1. Raw ore is a mixture of sulfide ore lead, zinc, and barite
2. Processing capacity 10tph
3. Max feeding size 200mm
Process explanation
1. Excavator or loader send raw ore into raw ore bin, through chute feeder to feed jaw crusher. Here jaw crusher is primarily crushing big rocks to 40-100mm medium size.
2. Output of primary jaw crusher through belt conveyor goes to fine jaw crusher for further crushing to 20-60mm small size. Here secondary jaw crusher is fine crushing 40-100mm rock to 20-60mm
3. Output of fine jaw crusher through belt conveyor goes to vibrating screen for sieving above 20mm and below 20mm. Here the vibrating screen is with 1 deck sieve 20mm hole size.
4. Above 20mm from over screen are back to fine jaw crusher for reprocessing via belt conveyor.
5. Below 20mm from under-screen through belt conveyor go to fine ore silo, through the electromagnetic vibrating feeder to feed ball mill. Here ball mill can grind 0-20mm ore to powder size 0-1mm
6. Output of ball mill flow to spiral classifier form a closed grinding system so that above 90% output is 200mesh which meets with flotation condition.
7. Underflow of the spiral classifier goes to one slurry tank, then use a slurry pump to send it to 1st mixing tank, then to 1st flotation machine for separating out the lead.
8. The concentrate of 1st flotation machine goes to one slurry tank, using a slurry pump to send it to 1st thickener, underflow of the thickener through the slurry pump goes to 1st disc vacuum filtering machine for dehydration, and the final product is the lead concentrate.
9. The tailing of the 1st flotation machine goes to one slurry tank, use a slurry pump to send it to the 2nd mixing tank, then to the 2nd flotation machine for separating out zinc.
10. The concentrate of the 2nd flotation machine goes to one tank, uses a slurry pump sends it to the 2nd thickener, underflow of the thickener through the slurry pump goes to 2nd disc vacuum filtering machine for dehydration, and the final product is zinc concentrate.
11. The tailing of the 2nd flotation machine goes to one tank, and using a slurry pump sends it to the 3rd flotation machine for separating out the barite.
12. The concentrate of the 3rd flotation machine to one tank, use a slurry pump to send it to the 3rd thickener, underflow of the thickener through the slurry pump goes to 3rd disc vacuum filtering machine for dehydration, and the final product is barite concentrate.