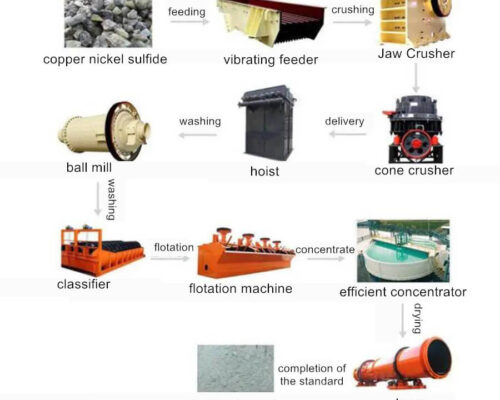
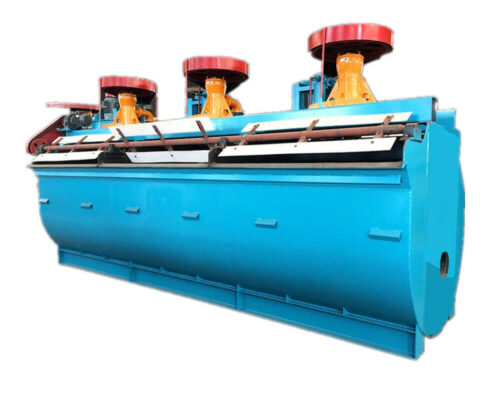
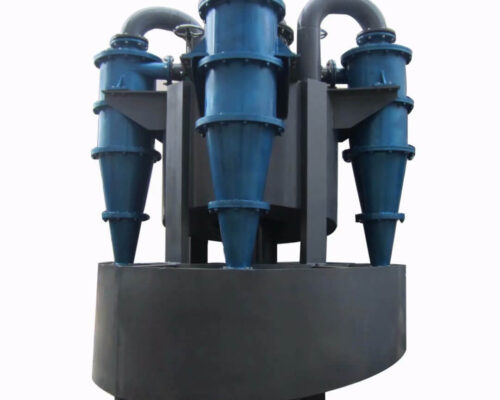
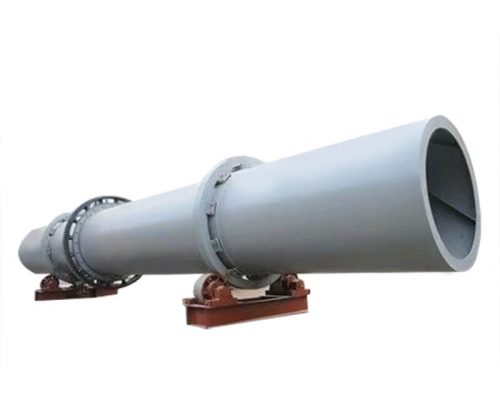
Nickel Ore Processing Plant
Nickel ore divides into nickel sulfide ore and nickel oxide ore(laterite nickel ore). The Main beneficiation process of nickel sulfide is flotation, and the subsidiary process is magnetic and gravity separation. Nickel oxide ores usually use pyrometallurgy and hydrometallurgy to process.
Nickel Ore Processing
Introduction
About Nickel Ore
Nickel is an indispensable metal element in the world, which is a silvery-white lustrous metal with a slight golden tinge, a hard and ductile transition metal. It is an essential raw material in military manufacturing, machinery manufacturing, atomic energy, ultrasonic, and communication.
Nickel Ore Type
At present, there are more than 50 kinds of nickel-containing minerals known. However, it is mainly divided into nickel sulfide ore and nickel oxide ore (laterite nickel ore).
Nickel sulfide ores
Nickel sulfide ores, such as pentlandite and pentlandite, exist in the form of free nickel sulfide, and a considerable part of nickel exists in pyrrhotite in the form of isomorphism. The nickel sulfide ore that exists widely in nature is (Ni, Fe)S, with a specific gravity of 5 and a hardness of 4, followed by NiS (specific gravity of 5.3 and hardness of 2.5).
Nickel oxide ores
Among nickel oxide ores, nickel laterite ore contains high iron, low silicon, and magnesium, and nickel content is 1% to 2%; nickel silicate contains low iron, high silicon, and magnesium content, and nickel content is 1.6% to 4.0%. The development and utilization of nickel oxide ore are mainly based on nickel laterite ore, which is developed by weathering ultrabasic rocks. Nickel primarily exists in nickel limonite (seldom crystalline to non-crystalline iron oxide).
Mineral Processing
Nickel Ore Beneficiation Process
The conventional nickel ore beneficiation process is divided into four stages: crushing & screening, grinding & grading, flotation, dehydration & drying.
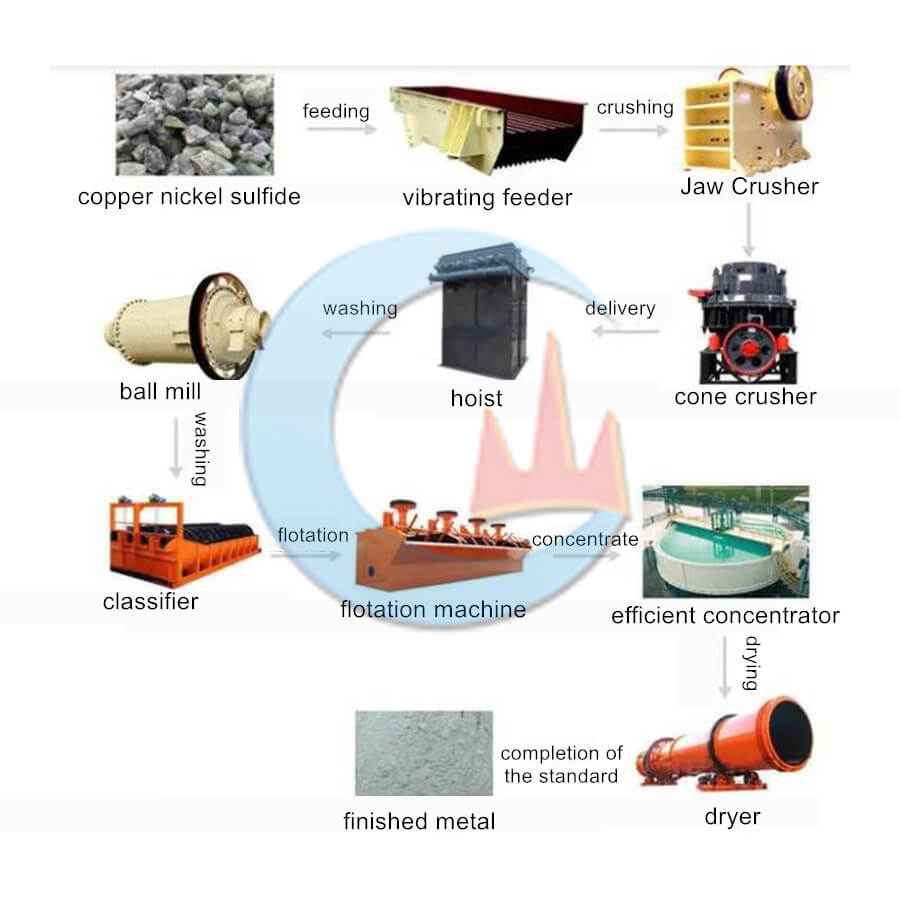
1. Crushing & Screening
The raw ore enters the jaw crusher through the feeder for primary crushing and then enters the cone crusher for medium crushing. After the vibrating screen screening, the materials under the screen enter the grinding process while the screened materials enter the fine-crushing process. And select the cone crusher for the fine-crushing operation.
2. Grinding & Grading
It often uses a stage grinding process when processing nickel ore. The crushed products enter the ball mill for a stage of grinding and then enter the spiral classifier for pre-classification. If the ore particle size of nickel ore is too coarse (greater than 0.1mm) or too fine (less than 0.006mm), it is unfavorable for the subsequent flotation. Therefore, after the pre-classification, set up a hydrocyclone to control the pulp classification. The overflow part of the hydrocyclone is qualified ore particles, and the bottom flow is unqualified ore particles that need to enter the ball mill for regrinding. To improve the grinding efficiency of the ball mill, we install a ball mill after the hydrocyclone for regrinding.
3. Flotation
In the flotation of nickel ore, to improve the utilization efficiency of materials and the grade of concentrate, it can generally be divided into flotation operations of high-grade concentrates and flotation operations of ordinary concentrates.
- High-grade nickel concentrate flotation
When sorting high-grade nickel ore concentrates, the flotation process of “one rough and two fine” is generally adopted.
Process: The slurry pump pumps the qualified ore pulp(after classifying) into the flotation machine for a roughing stage(rough). The obtained roughing concentrate enters the beneficiation process, undergoes two concentration(fine) flotations, and finally obtains high-grade nickel ore concentrate. - Ordinary Concentrate Flotation
After a rough selection, the tailings also contain a certain amount of nickel ore concentrate. In order to improve the recovery efficiency of concentrate ore and the utilization efficiency of materials, it is necessary to sort tailings again.
Process: Classify the tailings of the primary roughing of nickel ore first. The underflow materials enter the ball mill for secondary grinding, and the overflow materials enter the flotation machine for roughing of tailings. For the flotation of ordinary concentrate, the technological process of “one rough, three fine, and two sweeps” is generally adopted. The tailings of a roughing stage and the ore pulp after grinding will enter the hydrocyclone to classify. The tailings roughing concentrate enters into three beneficiation operations. The remainder goes to two sweeping operations for the tailings. After three times of beneficiation, it can obtain nickel ore concentrate.
4. Dehydration & Drying
The water content of the material after flotation is relatively large. In order to speed up the drying speed of the product, usually use a concentrator to dehydrate, and a dryer to dry the material to obtain a finished product.