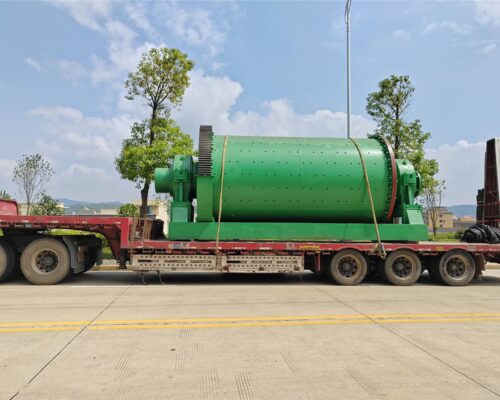
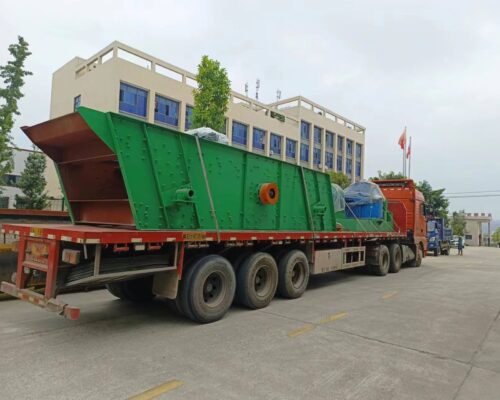
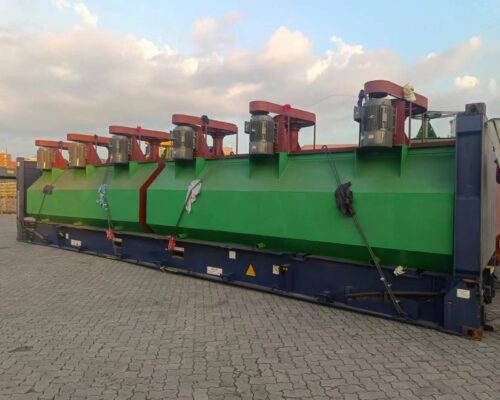
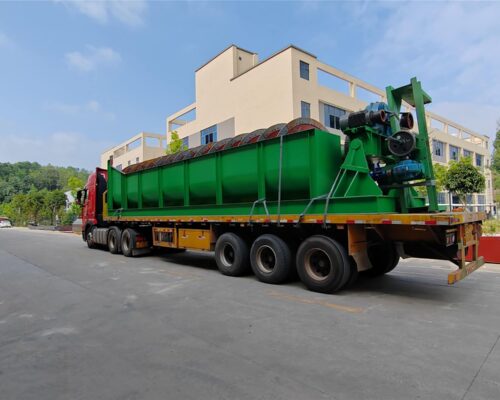
Lithium Ore Mining Process
Lithium ore is widely used in batteries, electronics, chemicals, materials, medical, and other fields as the primary raw material for energy development. As demand continues to increase, lithium extraction technology has also developed rapidly. Because there are different types of lithium ores, their beneficiation processes are also different. The main lithium ore beneficiation methods include flotation, magnetic separation, heavy media beneficiation, and combined beneficiation.
Lithium Ore Mining Process
Introduction
About Lithium Ore
Lithium is valuable for producing glass, aluminum products, and batteries. It is mined from ores of petalite (LiAl(Si2O5)2, lepidolite K(Li,Al)3(Al,Si,Rb)4O10(F,OH)2, spodumene LiAl(SiO3)2 and also subsurface brines.
Lithium is found in very low concentrations in igneous rocks. The largest concentrations of lithium-containing minerals are found in granitic pegmatites. The most important of these minerals are spodumene and petalite. Spodumene has a theoretical Li2O content of 8.03%. Due to its high lithium content, spodumene is the most important lithium ore mineral. A typical run of mine ore can contain 1-2% Li2O, while a typical spodumene concentrate suitable for lithium carbonate production contains 6-7% Li2O (75% – 87% spodumene). Higher-grade concentrates with 7.6% Li2O and low iron content are used in ceramics and more demanding industries.
Mineral Processing
Lithium Ore Processing
1. Lithium Flotation Processing
Applicable minerals: Lithium ores have industrial value, especially lithium ores in fine-grained disseminated form.
Main process: Common lithium ore flotation methods include forward and reverse flotation.
Positive flotation method: After the lithium ore is finely ground (avoid over-grinding that may cause mud formation), add a strong alkali for flotation. Add oleic acid after high concentration, strong stirring, and multiple scrubbings to desludging the lithium ore in an alkaline medium. Its soap salts are used as collectors to directly float out the lithium concentrate, leaving gangue minerals in the tank. This process does not require the addition of inhibitors.
Reverse flotation method: With the help of the alkaline environment created by lime, starch, dextrin, and other substances are added to inhibit the floating of lithium ore, and at the same time, a cationic collector is used to float the silicate gangue minerals to the surface of the slurry. The product is lithium concentrate. If lithium ore contains iron minerals, a foaming agent (such as HF or resinate) can be added to help further remove iron minerals and other impurities.
2. Lithium Magnetic Separation
Applicable mineral species: Spodumene containing iron impurities.
Main process: Because spodumene contains iron-containing impurity minerals, these minerals have weak magnetism and must be removed through strong magnetic separation to obtain low-iron spodumene concentrate.
Process features: Simple operation, easy to control, and strong adaptability.
3. Lithium Heavy Media Beneficiation
Applicable minerals: Spodumene with relatively coarse crystal grain size. The difference in specific gravity between lithium ore and gangue minerals is not greater than 0.2-0.5g/m3.
Main process: Mix the lithium ore after washing and desliming with heavy medium (heavy medium includes heavy liquid and heavy suspension, here mainly refers to heavy suspension), and feed the heavy medium cyclone at a pressure of 0.05-0.20Mpa. The machine is used for sorting, and heavy and light products can be separated. The heavy product becomes lithium concentrate after remediation through a remediation screen, and the light product becomes tailings after remediation through a remediation screen. Its main components are quartz, feldspar, biotite, and other gangue minerals.
4. Combined Beneficiation Method
Applicable mineral types: Lithium ores with complex associated components.
Main process: It is sometimes difficult to obtain qualified lithium concentrate using a single beneficiation method for lithium ores with complex associated components in nature. In this case, choose a combined process for lithium ore separation, such as flotation- Magnetic separation process, flotation-gravity separation-magnetic separation process, flotation-chemical treatment process, etc.
Flotation-magnetic separation method: First, oxidized paraffin soap and naphthenic acid soap are used as a combined collector, NaOH is used as a pH adjuster, and a coarse and fine flotation process is used in alkaline slurry to obtain spodumene. The concentrate is then subjected to strong magnetic separation to remove iron to obtain spodumene concentrate with low iron content.
Flotation-magnetic separation-gravity separation method: After the ground material is slurried, it enters the gravity separation stage (removing tantalum, niobium, and other products). After the gravity separation, tailings are concentrated and declined by the thickener, oleic acid, and oxide stone are added. The wax soap is slurried, and the spodumene concentrate is floated out under high alkalinity conditions and then undergoes strong magnetic separation to remove iron impurities for further purification.