Gold Carbon-in-leach(CIL) Process
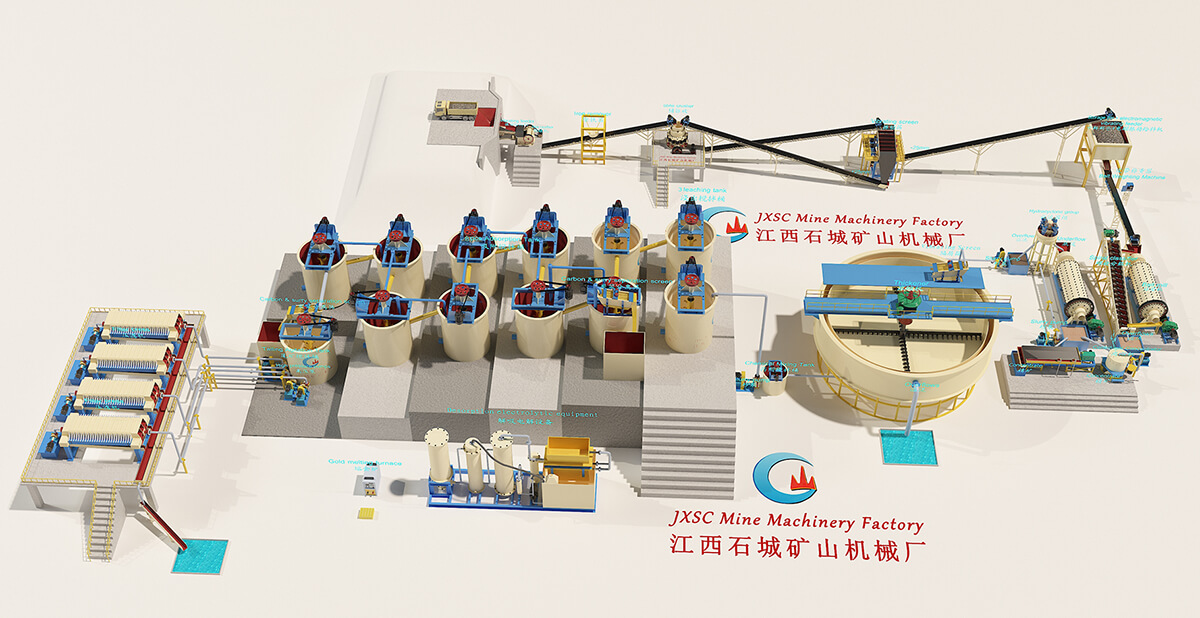
Gold CIL (Carbon in Leach) is a key part of gold extraction plants and is the preferred method for modern gold mining. The CIL process extracts gold from ore by simultaneously leaching and absorbing the gold onto activated carbon. It’s particularly effective for ores with a grade of over 1g/t and large bearing ore volumes. CIL can also extract other minerals like silver, platinum, and copper.
Gold CIL Solution
Introduction
About Gold CIL
CIL is a method of treating water by placing activated carbon adsorbents directly into the water. It is suitable for treating water bodies with high concentrations of organic matter and suspended particles. The gold CIL (Carbon In Leach) process is a commonly used method for extracting gold from ores. It is an advanced process that combines leaching and adsorption into a single operation. It is highly efficient and widely used in the mining industry.
The principle of Carbon Infiltration Leaching (CIL) is based on the principle that by crushing and grinding gold-bearing ores and immersing them in a cyanide-containing solution, the gold is oxidized by the cyanide to [Au(CN)2]- ions, which form gold cyanide dissolved in the solution. Then, the strong adsorption property of activated carbon is used to adsorb the cyanide gold ions in the solution to realize the extraction of gold.
The main advantages of the Carbon In Leach Process (CIL) include high efficiency, low cost, and environmental protection.
- High Efficiency
CIL can complete the dissolution and adsorption of gold in a relatively short time, greatly shortening the production cycle and increasing the treatment capacity. Due to the synchronization of cyanide leaching and activated carbon adsorption, gold ions are adsorbed onto the activated carbon as soon as they are formed, reducing gold loss. - Cost-effectiveness
Carbon leaching simplifies the operation process, reduces equipment investment and maintenance costs, and lowers overall operating costs. In addition, the reduction of intermediate links saves energy consumption and further reduces production costs. - Environmentally Friendly
Although the use of cyanide carries certain environmental risks, the charcoal leaching method can effectively control the amount of cyanide used, reduce wastewater discharge, and reduce environmental pollution by optimizing the process flow.
Mineral Processing
CIL Process
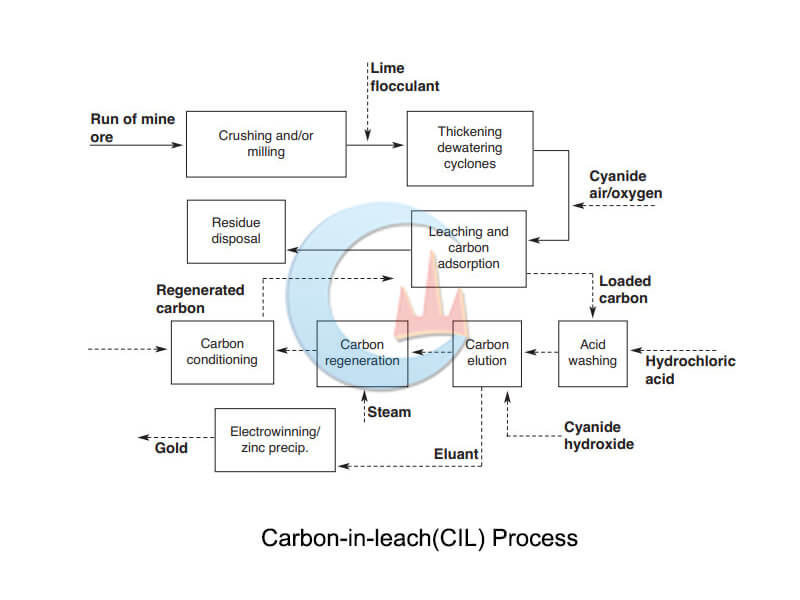
The gold CIL process includes seven operation stages: raw ore preparation, removal of impurities from the slurry, concentration before leaching, leaching and carbon adsorption, desorption electrolysis, smelting, and activated carbon regeneration.
1. Raw Ore Preparation– Crushing and Grinding
We should prepare the raw ore before the gold CIL extracts the gold ore. The process of preparation mainly includes crushing and grinding. The gold-bearing ore is crushed and ground into fine particles to increase the surface area for leaching. According to the ore dressing test report to determine the fineness of grinding, the fineness of the material is usually 85~90% in -200 mesh after crushing and grinding.
2. Removal of Impurities From The Slurry
Before leaching, it is necessary to remove impurities such as wood chips from the slurry to avoid these impurities from adsorbing gold from the slurry and preventing it from mixing into the rich charcoal, as well as preventing the wood chips from clogging the pipes and the charcoal separator screen. During the debris removal operation, the descaling agent can be added appropriately, the function of the descaling agent is to reduce the scaling on the surface of activated charcoal and the screen.
Chip removal is generally carried out in the grinding process, which is accomplished at the overflow of the one- and two-stage grinding classification, respectively. Commonly used debris removal equipment is the medium frequency linear vibrating screen, the initial debris removal operation can also be used spiral screen and cylindrical screen. The sieve hole size of the debris removal screen needs to be as small as possible under the premise of ensuring that the screen surface does not run off.
3. Concentration Before Leaching
The concentration of the slurry will affect the leaching time and the suspension state of activated carbon. The milling and grading of a residual concentration are usually between 18-22%, so the slurry needs to be dewatered through the thickener before leaching. We recommend using a high-efficiency thickener because it has a small footprint and high thickening efficiency.
4. Leaching and Carbon Adsorption
Carbon in Leach is characterized by simultaneous leaching and adsorption of gold. The decontaminated and thickened slurry is pumped into highly efficient leaching tanks arranged in a stepwise manner, generally configured in a series of 5-12 leaching tanks. Cyanide is added to the first one or two leaching tanks, and activated carbon is added to the rear leaching tanks. Each leach tank is equipped with a carbon screen to separate the activated carbon from the slurry. The activated carbon and the slurry are adsorbed in a counter-current manner, with fresh activated carbon being added from the last leach adsorption tank and gold-loaded carbon being discharged from the first leach adsorption tank. After adsorption, the slurry containing the gold-carrying carbon is sent through an air lifter to a charcoal lifting screen, which separates the slurry from the activated carbon. After screening and rinsing, the slurry is sent to the desorption electrolysis operation, after this method of adsorption of the slurry solution gold grade is generally 0.01-0.03g/m³.
5. Desorption Electrolysis
Desorption of gold-carrying carbon is usually carried out by high-temperature and high-pressure desorption method, i.e., under high-temperature and high-pressure conditions, an anion that is easily adsorbed by activated charcoal is added to the desorption system to displace Au(CN)₂- to obtain the gold sludge and depleted charcoal, to realize the desorption of gold. The desorbed gold sludge is used to recover gold by electrolytic deposition or other methods.
6. Smelting
The gold mud obtained can be directly smelted into dore bars after simple acid washing and removing impurities. By using wet metallurgy, the gold ingot can reach a purity of more than 99.99%.
7. Activated Carbon Regeneration
The desorbed activated carbon is firstly washed with acid to remove the aggregates, and after several times of return to use, it needs to be thermally activated to restore the adsorption activity of the carbon, and then it can be recycled for use.
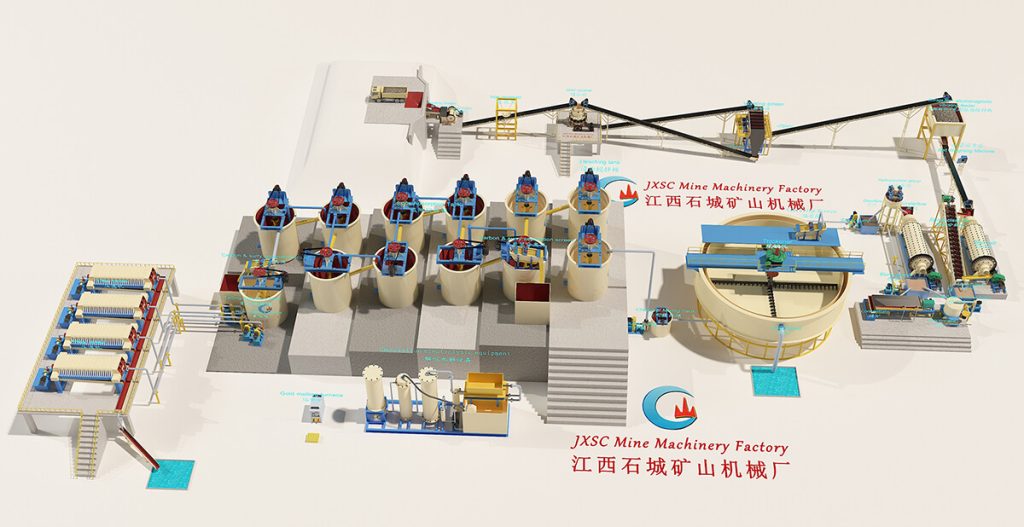
Gold CIL 3D Videos
300TPD Rock Gold Gravity Beneficiation & CIL
Tanzania 200 TPD Rock Gold CIL Process Plant
500TPD Rock Gold CIL Processing Plant