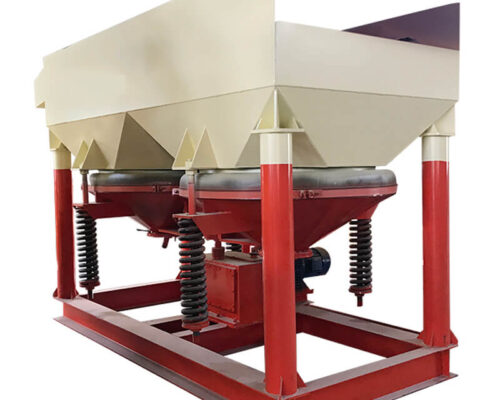
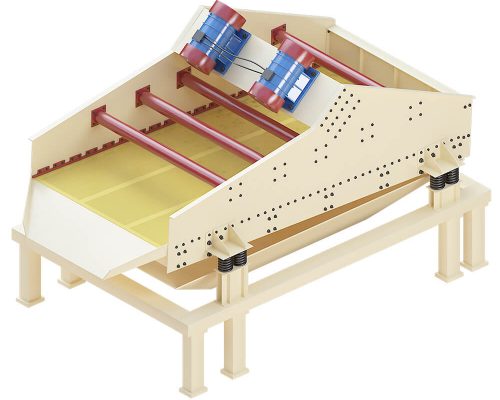
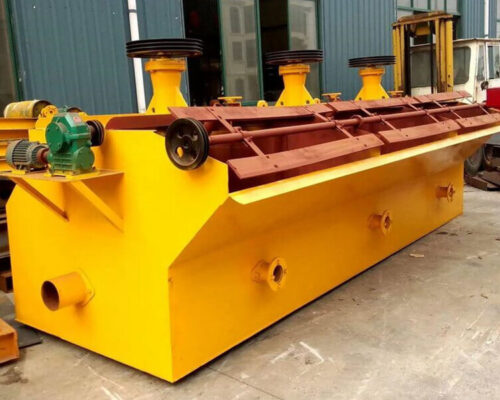
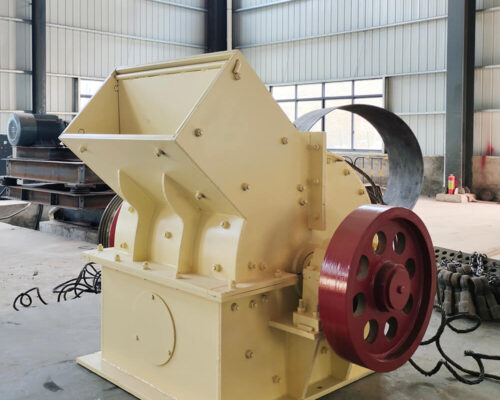
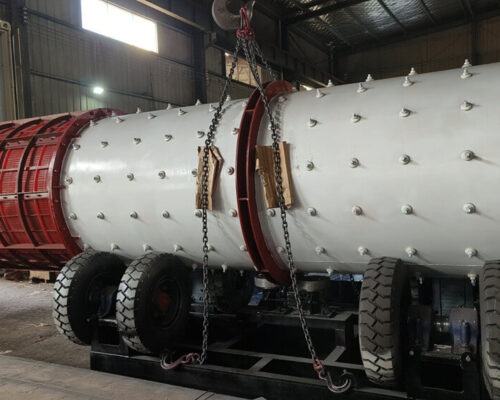
Fluorite Beneficiation Process
The fluorite ore beneficiation methods are gravity separation and flotation. Fluorite ore gravity separation is suitable for higher-grade fluorite ore blocks and particle ores with a particle size of 6-20mm. Fluorite ore flotation is suitable when the raw ore has a high mud content, is accompanied by impurity minerals, or when the valuable minerals are embedded in finer particles.
Fluorite Beneficiation
Introduction
About Fluorite
Fluorite, or fluorspar, is composed mainly of calcium fluoride (CaF2). It belongs to the halide minerals group and is found in various geological environments.
Fluorite Key Points
- Crystal Structure: Fluorite crystallizes in the cubic system, forming often transparent or translucent crystals. Its crystal structure is characterized by calcium ions coordinated by eight fluoride ions.
- Color and Varieties: Fluorite exhibits many colors, including purple, blue, green, yellow, pink, and transparent. The color variations are often due to impurities or radiation exposure. There are also banded and multicolored varieties. The most common colors are purple and green.
- Industrial Uses: Fluorite has several industrial applications. One of its primary uses is as a source of fluorine for producing hydrofluoric acid. It is also used to manufacture aluminum, gasoline, uranium fuel, and certain types of glass and ceramics..
Mineral Processing
We can use gravity separation and flotation to separate fluorite ore. The choice of a fluorspar mineral processing method needs to be comprehensively considered based on many factors, such as fluorspar properties, fluorspar use, and the grade of fluorspar concentrate.
- We can use the gravity separation when the raw ore is coarse-grained fluorite lump ore.
- When the raw ore has a high mud content and is accompanied by impurity minerals or the valuable minerals are embedded in fine particles, we can use the flotation process.
Fluorite often coexists with quartz, barite, calcite, sulfide ore, and other minerals. According to different ore properties, the specific flotation process is also different.
Fluorite Gravity Separation
Gravity separation is one of the common methods used for the beneficiation of fluorite ores. This process exploits the density differences between different minerals to separate them.
The fluorite gravity separation process
- Crushing and Grinding
The raw fluorite ore is first crushed into small particles to liberate fluorite crystals from the gangue minerals.The crushed ore is then ground to achieve a finer size for efficient separation. - Washing and Screening
The crushed and ground ore is washed to remove fine particles and impurities.Screening is performed to separate the ore into different size fractions. - Gravity Separation
Dense media separation or jigging is often used for the gravity concentration of fluorite ore.
In dense media separation, the crushed ore is suspended in a medium with a specific gravity between fluorite and the gangue minerals. The heavier fluorite particles sink, while the lighter gangue particles float.
In jigging, a pulsating water flow separates minerals based on their density. The denser fluorite particles settle faster. - Dewatering
The concentrated fluorite obtained from gravity separation may undergo dewatering processes to reduce moisture content.
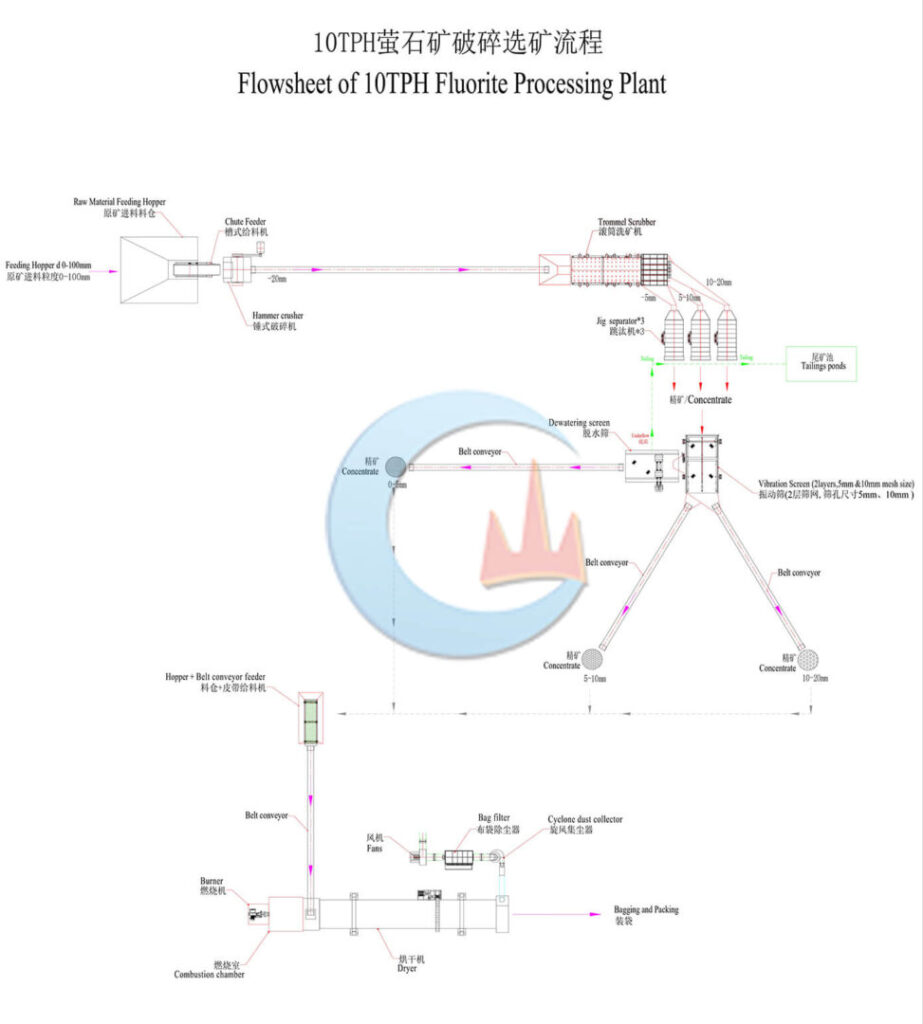
Fluorite Flotation
Flotation is a widely used method for the concentration of fluorite ores.
The fluorite flotation process
- Crushing and Grinding
- Conditioning
The ground ore is mixed with water and various reagents to create a pulp. The reagents typically include collectors, frothers, and modifiers.
Collectors are chemicals that selectively attach to the surface of fluorite particles, making them hydrophobic and facilitating their attachment to air bubbles.
Frothers are added to create a stable foam, allowing the air bubbles to carry the hydrophobic fluorite particles to the surface.
Modifiers may be used to control the pulp’s pH level and improve the process’s selectivity. - Flotation
The conditioned pulp is introduced into a flotation cell, typically equipped with agitating mechanisms.
Air is bubbled through the pulp, and the hydrophobic fluorite particles attach to the air bubbles, forming a froth on the surface.
The froth, containing the floated fluorite particles, is then collected and further processed. - Dewatering