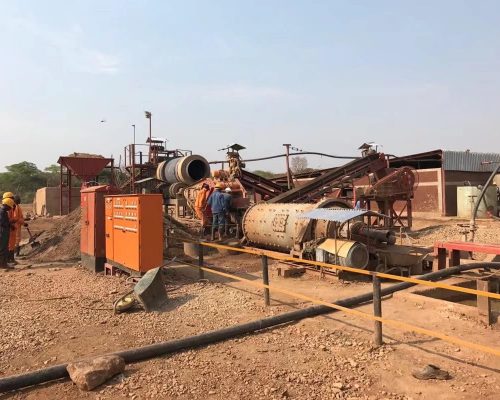
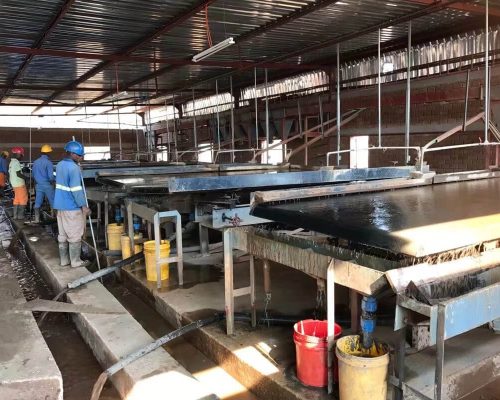
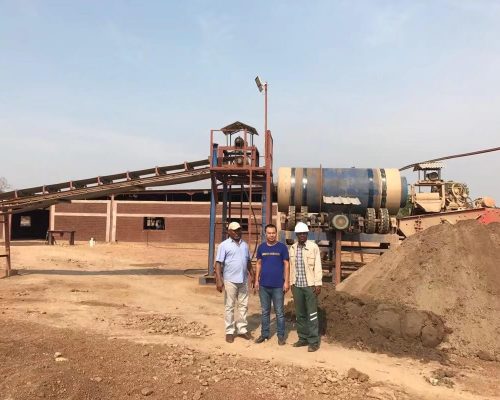
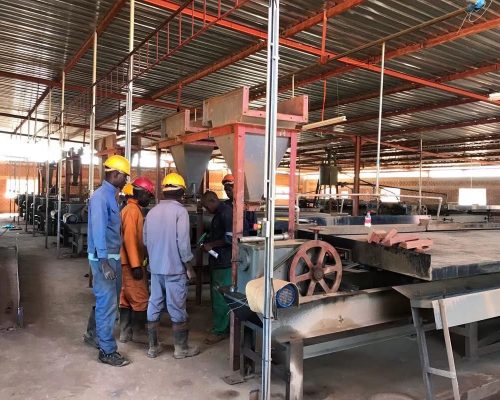
Copper Beneficiation Process
The copper ore can be divided into oxide ore(more than 30% copper oxide), sulfide ore(less than 10% copper oxide), and mixed ore(10%-30% copper oxide). The main beneficiation process of copper is the flotation, hydrometallurgy process is also used in the copper extraction process to treat refractory mixed copper ore and the refractory oxide ore.
Copper Extraction Process
Introduction
About Copper Ore
Copper ore is generally an aggregate composed of copper sulfide or oxide and other minerals, which react with sulfuric acid to produce blue-green copper sulfate. The industrial minerals of copper include natural copper, chalcopyrite, chalcocite, tetrahedrite, chalcocite, malachite, etc.
According the copper oxide rate, copper ore can divide into ore sulfide(less than 10% copper oxide) ,ore oxide(more than 30% copper oxide) and mixing ore(10%-30% copper oxide). The main process for copper ore is flotation, for refractory mixed copper ore and refractory oxide ore, normally use the hydrometallurgy process.
Mineral Processing
Copper Extraction Processing
1. Copper Flotation
As a commonly used process for copper ore beneficiation, flotation can be used for the separation of copper sulfide and oxidized copper ores. The main process of copper ore flotation is rough as follows: ore crushing and screening → stage grinding stage flotation → concentration and dehydration → copper concentrate.
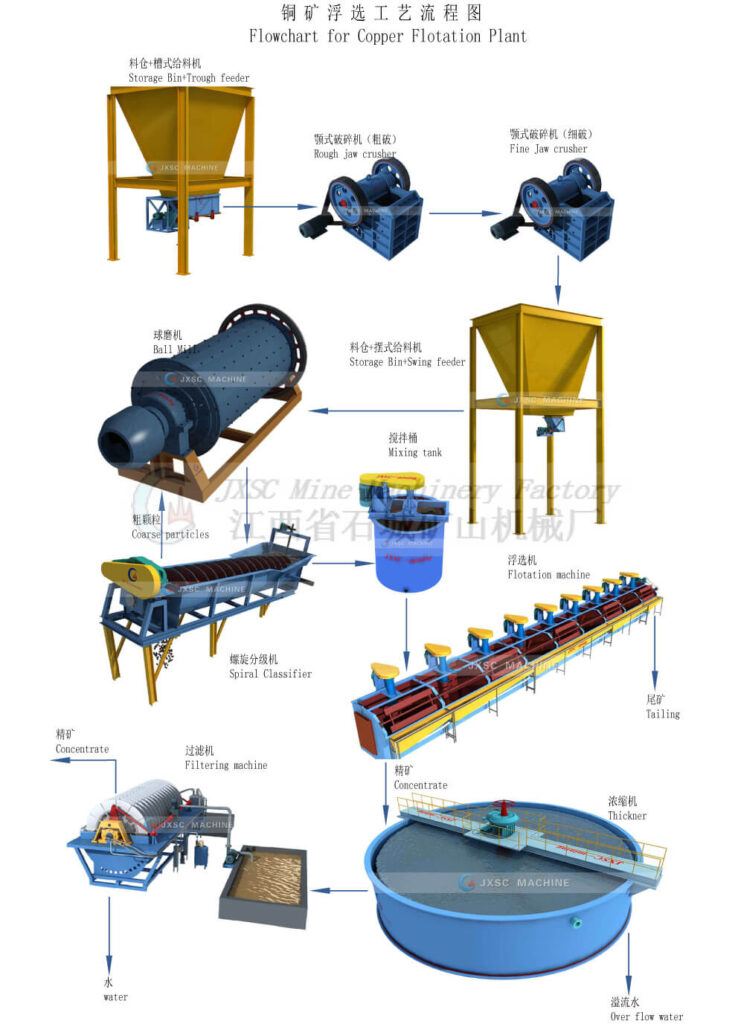
The material is fed to the rough jaw crusher by a feeder and then send to the fine jaw crusher for the second crushing.
After the crushing, the material is going to a ball mill for grinding. And then classified by the spiral classifier. The coarse particles from the spiral classifier return to the ball mill for grinding.
The fine particles from the spiral classifier come to a mixing tank for mixing fully. And then the slurry sends to the flotation.
The concentrate from the flotation comes to a thickness to improve the grade. And then send to the filtering machine for dewatering.
The flotation of copper oxidized ores and sulfide ores is almost the same. But for copper oxidized ores there are leaching process can be used too.
2. Copper Leaching Process
The common leaching processes of copper oxidized ore include heap leaching, pool leaching, in-situ leaching, and agitation leaching.
- Heap leaching process
The mined ore is crushed to a certain size by the crusher. Because the leaching stage does not need to reach the same small particle size as the flotation process, the heap leaching process does not need a grinding stage, the ore can be directly sent to heap leaching after crushing. The oxide ore (mix with partial sulfide ore) is placed on a leaching pad and sprayed with the strong acid solution to permeate the crushed ore. As time goes on, the copper in the crushed ore is leached into the solution as the pregnant solution, and then pumped into solvent extraction equipment for further purification.
- Pool leaching
The pool leaching process is a common leaching method used in early wet copper smelting. Using the strong sulfuric acid solution to leach the 1-2% copper-contained oxidized ore (particle size is -1cm). Because the concentration of copper in the leach solution is high, it can be directly used for the copper electrodeposition.
- In-situ leaching process
During in-situ leaching, the well spacing is generally 30x30cm (or 15×7.5m), and the diameter of the borehole is 15-25cm. A plastic pipe is set in the hole through the ore body, and the leaching agent flows into the ore body along the plastic pipe, the leaching solution is pumped back to the ground from the bottom of the ore body.
The in-situ leaching process can be used to treat the residual ore of old mines or the unmined oxidized copper ore and lean copper ore. The in-situ leaching process has better potential than other processes for those abandoned mines or uneconomical copper mines with other processes.
- Agitation leaching process
Agitation is carried out in the leaching tank equipped with the agitation leaching device. The fine grains (-75um accounts for 90%) oxidized ore or calcined sulfide ore are leached by high concentrated sulfuric acid solution. There are two ways of leaching: air agitation and mechanical agitation.
Because of the small particle size and sufficient agitation, the agitation leaching process has a faster leaching speed and higher recovery rate than the pool leaching process. Therefore, the agitation leaching process can treat high-graded ore or the ore with lower-graded tailings (Cu < 1%).