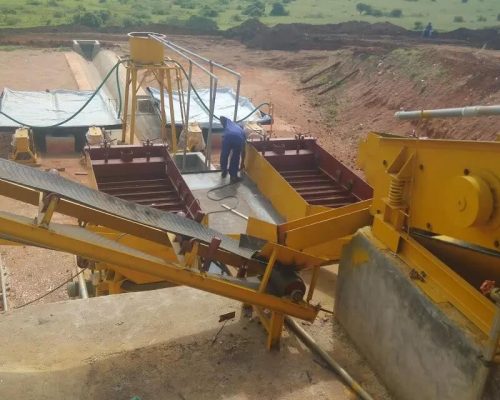
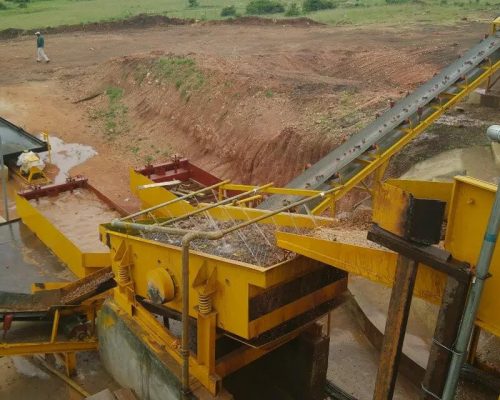
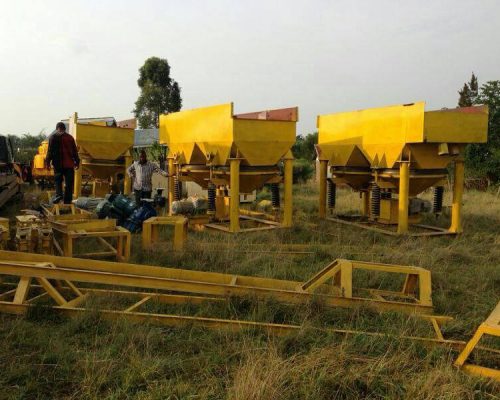
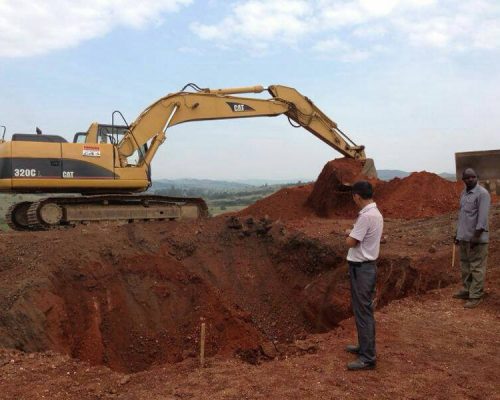
Coltan Ore Process
Coltan is short for columbite-tantalite, a dull metallic ore. Approximately 80% of the world’s supply of Coltan is found in the Democratic Republic of Congo. Before coltan is mined by hand in the Congo. The beneficiation process of tantalum niobium ore usually needs to go through 4 stages: crushing, grinding, classification and magnetic separation.
Coltan Ore Mining Process
Introduction
About Coltan Ore
Coltan is short for columbite-tantalite, a dull metallic ore. When refined, coltan becomes a heat-resistant powder, metallic tantalum, which has unique properties for storing electrical charge.
Coltan occurs in granitic pegmatites, pockets where the deep-seated molten rock crystallized last. Pegmatites contain many rare metals, as well as enormous crystals of some common minerals.
Coltan is used in many electronics today around the world due to its unique electrical properties. The two-man products include cell phones and laptops, though it is found in other electronics as well.
Mineral Processing
Coltan Ore Processing
1. Rock Coltan Processing Plant
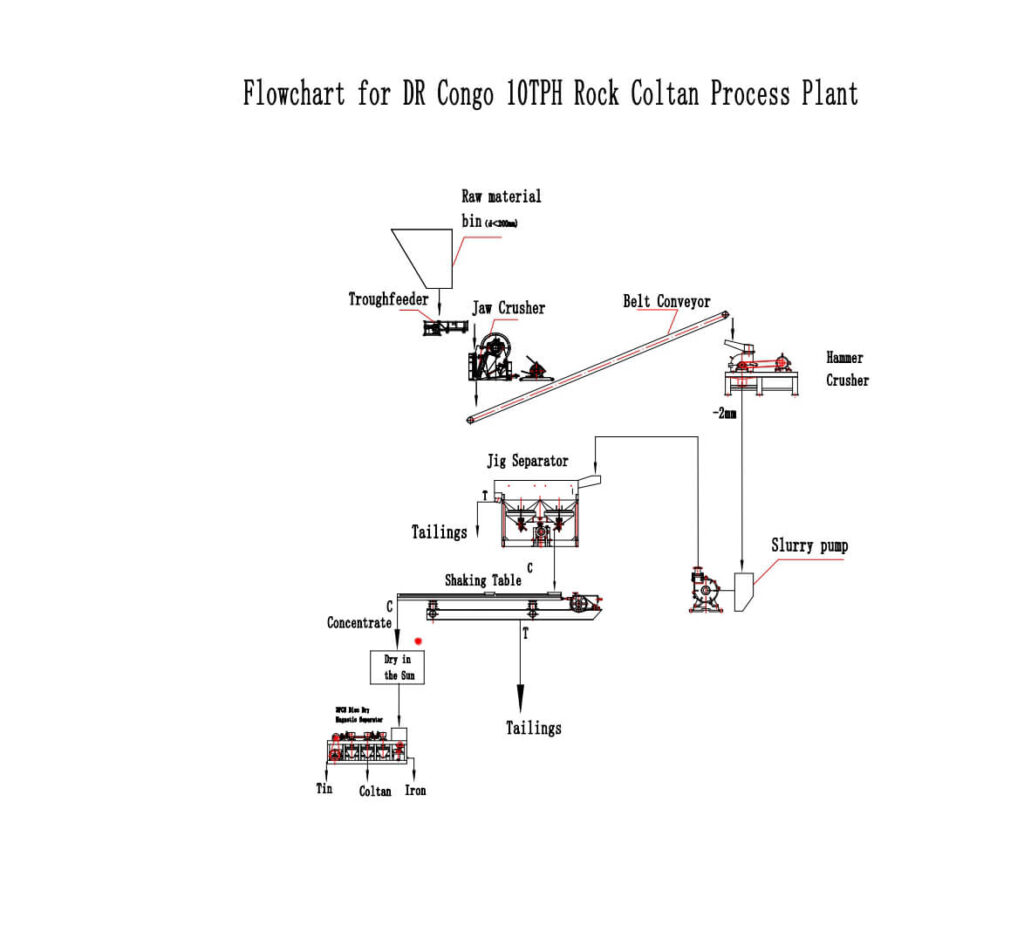
This setup is for a rock coltan ore processing plant. The Flowchart Explanation is as below.
The vibration feeder is for feeding raw material to the jaw crusher smoothly and stably.
A jaw crusher primary crushes big stone to a smaller size less than 100mm, then output goes to cone crusher by conveyor.
The cone crusher is a secondary crushing machine for crushing rock coltan tin to about 30mm, then output sends to vibration screen.
The vibration screen(with 30mm screen mesh size) for screening out below 0-30mm sending to the storage bin, oversize +30mm send back to cone crusher to crush again.
The 0-30mm material on the storage bin will go to hammer crusher as fine grinding machine to grind material 0-2mm fine powder, so to release the coltan and tin from rock.
The output 0-2mm slurry from the hammermill will be pumped to the jig separator to concentrate heavy coltan tin.
The primary heavy concentrate ore discharged from the jig separator will be sent to the shaking table to concentrate again.
The shaking table has an extremely concentrated effect for heavy minerals, in order to get a higher purity of coltan and tin, the middling from the 1st stage shaking table will go to the 2nd stage shaking table to concentrate again, so can reach the highest recovery ratio and high purity coltan tin mixture.
All the 0-2mm coltan tin concentrate ore discharged from two stages shaking table will be sent to dewatering screen for dewatering water, then the concentrate ore will be sent to drying machine or dry in the sun depends on the customer.
The dry heavy minerals mixture will finally be sent to a high-intensity 3pcs disc dry magnetic separator, the gauss is adjustable to separate out each heavy mineral, such as iron, ilmenite, hematite, coltan and tin concentrate, etc. so as can get high-grade coltan and tin ore, usually, final coltan and tin grade can reach about 60-65% maximum depend on raw material conditions.
2. Alluvial Coltan Processing Plant
3. Alluvial & Rock Coltan Processing Plant
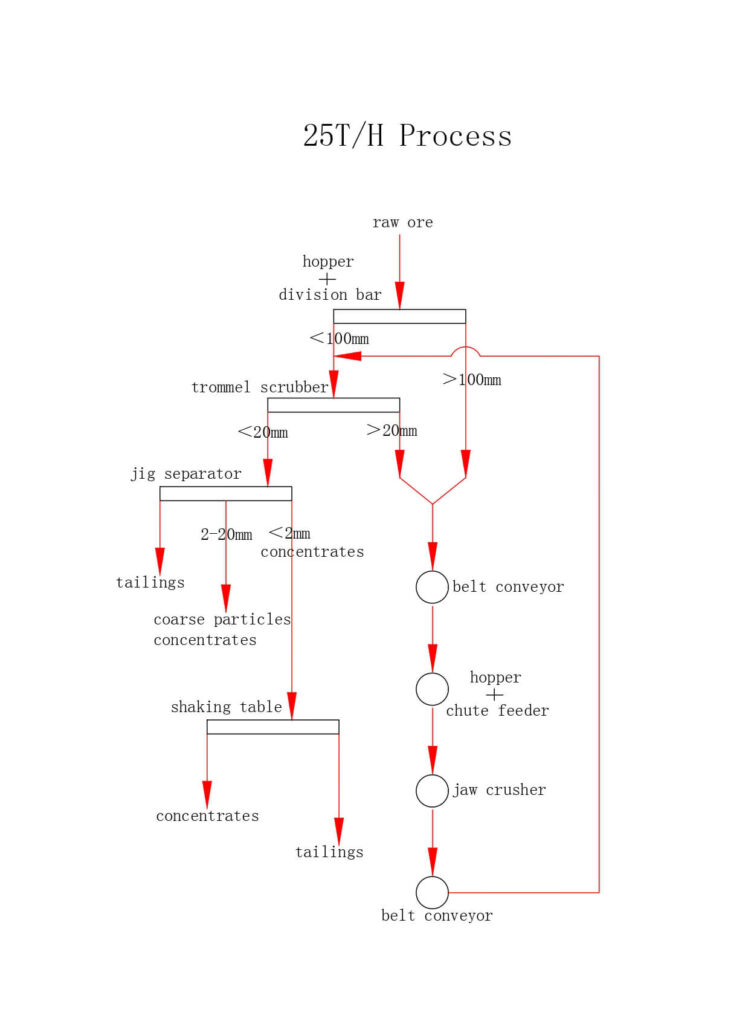