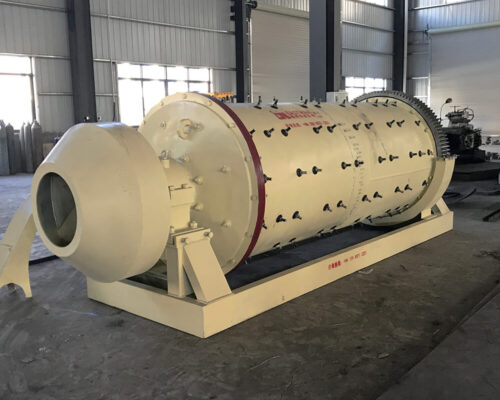
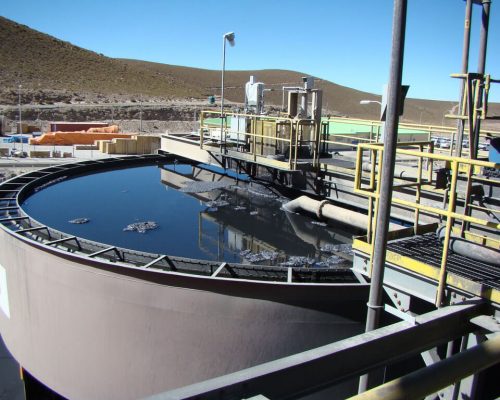
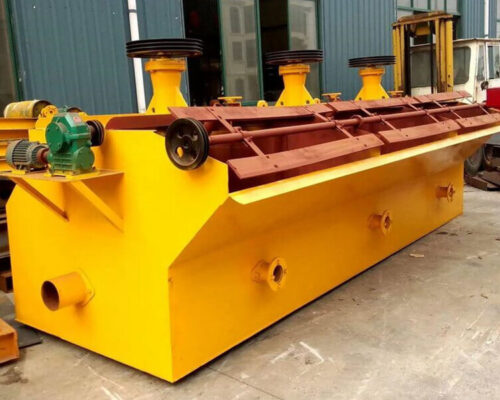
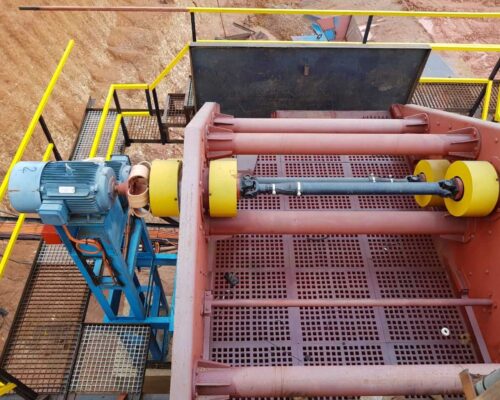
Barite(Baryte) Beneficiation Process
Barite, a mineral composed of barium sulfate (BaSO4), is brittle with large tubular crystals. Barite beneficiation aims to remove impurities and improve the properties of barite for its intended applications. There are generally gravity separation, magnetic separation, and flotation for barite beneficiation.
Barite Beneficiation Process
Introduction
About Barite
Barite, also known as barytes or heavy spar, is a mineral composed of barium sulfate (BaSO4). It is a relatively common mineral with a wide range of industrial applications. Here are some critical points about Barite.
Chemical Composition: Barite consists of barium sulfate, where barium (Ba) and sulfate (SO4) ions form a crystal structure. It is chemically inert and does not react with most chemicals.
Physical Properties
- Color: Barite can be colorless, white, light shades of blue, green, yellow, or red, depending on the impurities present.
- Hardness: Barite ranges from 3 to 3.5 on the Mohs scale, making it a relatively soft mineral.
- Specific Gravity: Barite has a high specific gravity, typically around 4.5, making it heavy for its size.
- Occurrence: Barite is found in various geological settings, including sedimentary rocks and hydrothermal veins, and as a gangue mineral in metallic ore deposits. Major barite producers include China, India, Morocco, the United States, and Mexico.
Mineral Processing
The main processes for barite beneficiation include gravity separation and flotation. The gravity separation process uses the different specific gravity of barite and gangue minerals to improve their grade and purify them. At the same time, flotation is suitable for processing barite with fine particle size and uses the flowability of minerals for separation.
The gravity separation process is simple. Commonly used barite beneficiation equipment includes jaw crushers, circular vibrating screens, spiral classifiers, jigs, hydro cyclones, dehydration screens, etc. Sometimes, heavy media separation is also used. Machine, shaker, spiral chute, etc.
The flotation process is relatively complex and requires more equipment. Commonly used equipment includes a jaw crusher, vibrating screen, ball mill, classifier, stirring tank, flotation machine, magnetic separator (used to remove iron impurities) ), concentrator, dryer, etc.
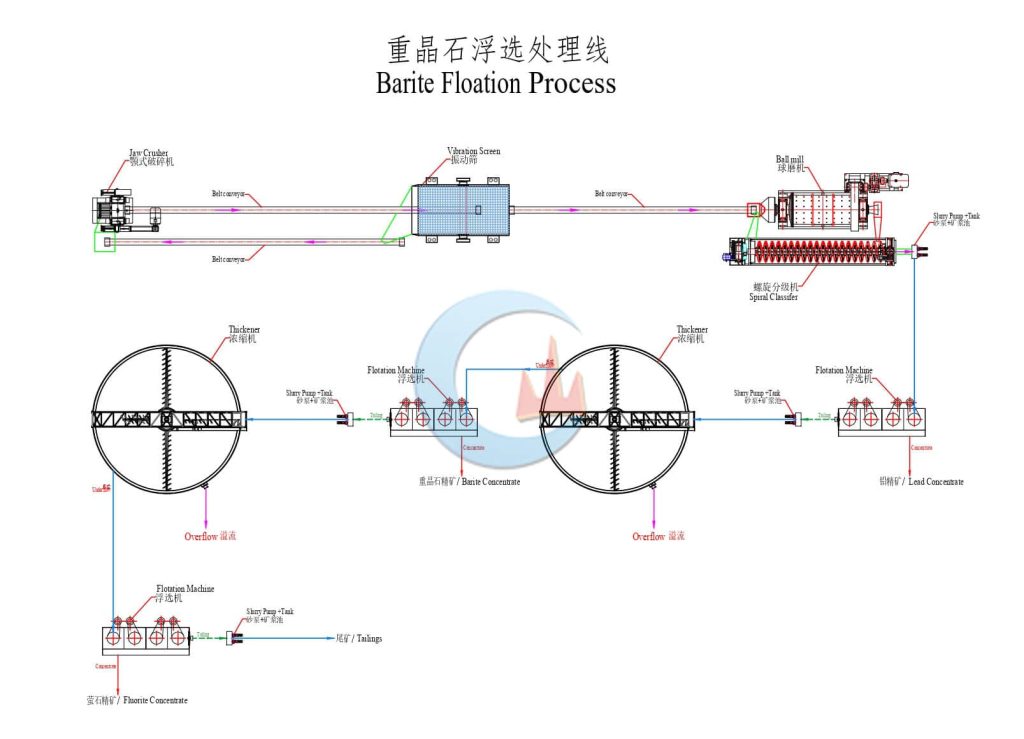
Barite Beneficiation Process
Crushing and Screening
The crushing process uses a jaw crusher, and a two-stage crushing process is used to crush the large pieces of barite mined; the screening process uses a simple and practical circular vibrating screen with a large processing capacity, high screening efficiency, and a failure rate of this type of vibrating screen Low, large processing capacity, high screening efficiency, easy to operate, it is an ideal equipment for barite ore screening; the jig sorting process uses two types of jigs to separate the coarse and fine-grained barite materials after crushing. Perform jig sorting.
Gravity Separation
The usual methods for barite gravity beneficiation are crushing, screening, and jigging beneficiation processes to obtain higher-grade concentrates, and the product grade can reach more than 80%. The jig separator is the leading equipment for sorting and purifying barite ore. It has the characteristics of energy saving, high efficiency, environmental protection, etc., and has high economic benefits.
Magnetic Separation
Wet magnetic separators are usually used to select some iron-containing minerals, such as siderite, which are used as barite raw materials for barium-based medicines that require very low iron content.
Flotation
Flotation is often used to sort barite ores with fine particle sizes and gravity separation tailings. Depending on the adsorption method, anionic collectors(such as fatty acid alkyl sulfates and alkyl sulfonates) or cationic amine collectors are used to flotate barite ores.
Barite Processing Plant 3D Flowchart
This setup is a barite processing plant, it is configured with a vibrating grizzly feeder, jaw crusher, log washer, spiral sand washer, vibrating screen, and belt conveyors.
- The materials under the grizzly bar of the vibrating feeder are conveyed to 3 spiral sand washers through the material guide chute.
- The material above the grizzly bar is fed to the jaw crusher. The discharged material of the jaw crusher enters the 2 log washers.
- The spiral-out materials from the log washers are fed into the spiral sand washer. The overflow of the log washer is guided to the vibrating screen.
- The discharging materials of the 3 spiral sand washers are all fed into the vibrating screen.
- The vibrating screen sieves 2 kinds of finished products with different particle sizes, 0-20mm and materials over 20mm.