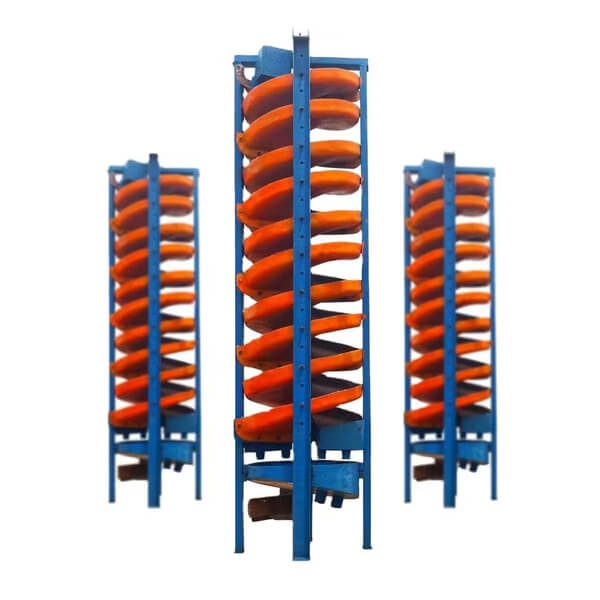
Polyurethane(PU) Spiral Chute Separator
Capacity: 0.8-4 tph
Feeding Size: 0.02-0.5 mm
Feeding Density: 25% – 55%
PU Spiral Chute Separator Overview
PU spiral chute separator is a type of equipment commonly used in gravity separation. It utilizes the spiral shape of the chute and the density difference of the material to sort the ore under the effect of gravity.
Polyurethane spiral chute separators are made of fiberglass lined with wear-resistant resin and an emery cover; then, paint Polyurethane is added. The abrasion resistance and chemical stability of PU materials make them highly desirable for gravity beneficiation processes. They excel especially with highly abrasive or corrosive ores, eg. they offer significant advantages in the silica sand beneficiation.
Features
- Superior abrasion resistance:PU material has very high abrasion resistance, suitable for processing sand, high-hardness minerals, and other abrasive materials; prolong the service life of the equipment, and reduces the frequency of replacement.
- Chemical stability:PU is resistant to acid and alkali corrosion, can be used in complex chemical environments, adapted to corrosive media in ore processing.
- Lightweight design: lighter than metal, easy to carry and install, reduces transportation and installation costs.
- High separation efficiency: Smooth surface and low friction, good material flow, can improve the efficiency and precision of sorting.
- Modularized structure: The height, inclination, and diameter of the chute can be adjusted according to the characteristics of the ore, processing capacity, and beneficiation requirements.
Scope of application
The application of PU spiral chute separator in gravity beneficiation includes but is not limited to the following minerals:
- Iron ore:for separating iron minerals from veinstone.
- Gold and tungsten ores: to separate high-density precious metal minerals.
- Tin and chrome ores:efficient extraction of heavy minerals.
- Rare earth ores: efficient sorting of rare metals.
- Coal washing: removing high-density impurities in coal and improving the purity of coal.
Due to its wear-resistant, corrosion-resistant, and lightweight characteristics, the PU spiral chute has become an important piece of equipment in gravity beneficiation, and it is especially suitable for handling mineral sorting in highly abrasive and complex environments. Its efficient sorting performance enhances the mineral recovery rate and reduces the cost of mineral processing, which is a high-quality choice in modern mineral processing technology.
Advantages
PU Spiral Chute Separator Advantages
- Cost saving:PU spiral chutes are light, moisture-proof, anti-rust, wear-proof, anti-corrosion, and noise-free. They have long service life and low maintenance cost, which reduce the overall operating cost of the equipment.
- Environmentally friendly:No need for complex mechanical structure and power equipment, only the use of gravity for beneficiation, energy saving, and environmental protection; does not produce harmful chemicals or additional pollutants.
- Good separation effect:Highly efficient material flow and separation capacity can significantly improve the recovery rate and mineral grade.
Structures & Working Principle
PU Spiral Chute Separator Structure
The main parts of a spiral chute are feeder chute, trough pillar, product collection funnel, product intercepted slot, spiral chute, tripod, etc.,
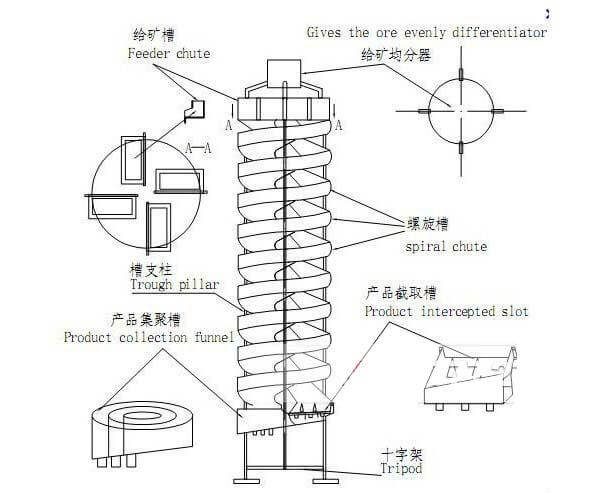
PU Spiral Chute Separator Working Principle
In the beneficiation process, the pulp of the polyurethane spiral chute is subjected to the joint action of inertial centrifugal force and gravity when flowing in the spiral chute. The slurry in the rotary movement generates inertial centrifugal force, prompting light and heavy minerals in the groove surface banding, which are discharged continuously. This sorting principle utilizes the inertial centrifugal force generated in the rotary motion of the slurry, prompting the light and heavy minerals to be separated on the trough surface.
Technical Parameters
Model | JXSC-600 | JXSC-1200 |
Outer Diameter | 600mm | 1200mm |
Spiral Pitch | 320-430mm | 600-630mm |
Starts Number | 2 | 2 |
Feeding Size | 0.02-0.3mm | 0.03-0.5mm |
Feeding Density | 25%-50% | 25%-55% |
Capacity | 0.8-1.2tph | 2-4tph |
Dimension | 600*600*2650mm | 1200*1200*3500mm |
Weight | 70 kg | 132 kg |