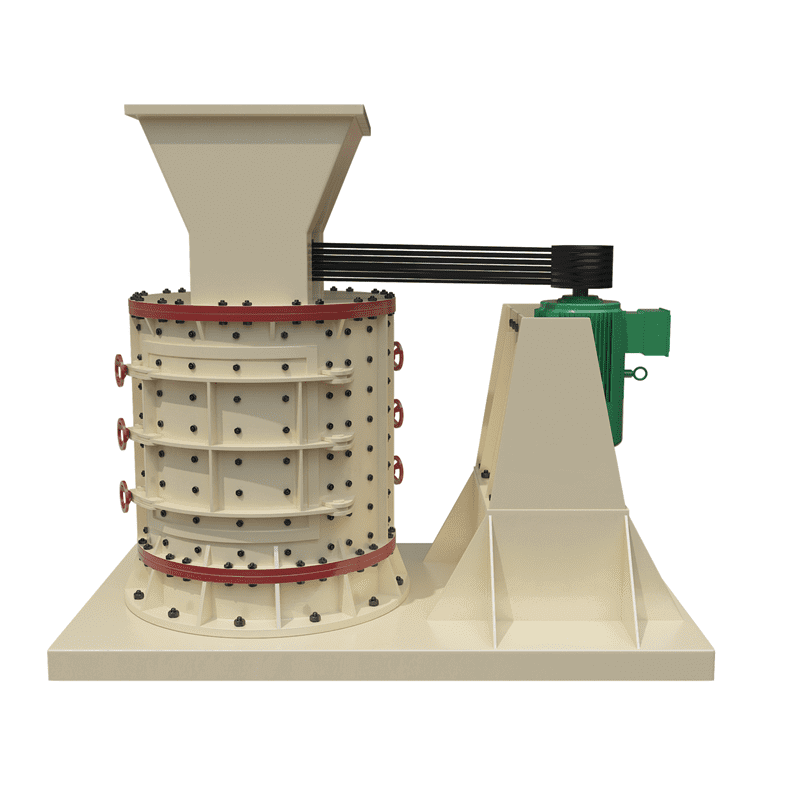
Vertical Shaft Compound Crusher
Capacity: 5-200 TPH
Feeding Size: ≤100 mm
Discharge Size: 0-5 mm
Power: 30-250 kW
Application: Mineral processing plants, coal plants, chemical plants, cement, glass, ceramics, electric power, etc.
Vertical Shaft Compound Crusher Overview
A vertical shaft compound crusher is a special type of crushing equipment that combines the characteristics of vertical crushers and impact crushers. It usually consists of the rotor and impact plate of a vertical crusher, which can perform impact and squeeze crushing simultaneously to achieve a more efficient crushing effect.
The compound vertical crusher is widely used in mining, construction, metallurgy, the chemical industry, and other industries. It is suitable for crushing ore, slag, construction waste, and other materials of various hardness and strength. It is one of the necessary crushing equipment.
The vertical shaft compound crusher is a new type of crushing equipment developed and designed based on the technology of similar crushers at home and abroad. It can perform fine crushing and coarse grinding of many types of materials. It has a large crushing ratio, low energy consumption, energy saving and environmental protection, stable operation, and easy operation and maintenance. It can crush blast furnace slag, coal gangue, lump coal, sandstone, gypsum, and other materials. The vertical shaft compound crusher is vertical crushing equipment that is more convenient to move and operate. It is small in size and relatively cheap. It is more affordable than other crushing equipment, has high-cost performance, and has strong production capacity.
Features
- Not easy to clog There is no screen bar setting, so it is difficult to block when crushing materials with high moisture and large mud content.
- Device protection mechanism The elastic adjustment mechanism automatically discharges unbreakable objects into the system without damaging the equipment.
- Low noise and less pollution The working noise is less than 75 decibels (db level); the advanced sealing device can prevent dust from floating in the air during crushing, improving the environment of the work site.
- High productivity It has the functions of fine crushing and coarse grinding, and it is suitable for medium-hard and extra-hard materials.
- Consumable parts have a long service life The wearing parts adopt the current domestic new high-strength, wear-resistant materials.
Advantages
Vertical Shaft Compound Crusher Advantages
- High efficiency, good product particle size, and fine crushing and coarse grinding functions.
- It has a wide range of applications and can crush materials with a compressive strength not exceeding 350 MPa.
- High safety performance. When encountering unbreakable materials, the insurance system provides insurance and protects the equipment.
- It is energy-saving and easy to use, and the product is in the shape of a cube and has a high packing density.
- Advanced wear-resistant material, small self-lining wear, and easy maintenance.
- The bearings are arranged horizontally, the life is long, and it can crush materials at high temperatures.
Structures & Working Principle
Vertical Shaft Compound Crusher Structure
Vertical shaft compound crusher, also called vertical shaft sand-making machine, consists of a transmission device, bearing, upper machine cover, liner, hammer head, hammer plate, main shaft, belt, feed port, discharge port, support, motor, and access door, cylinder, upper cover, and base, etc., the internal structure is simple and reasonable, the operating cost is low, and the principle of stone against stone is used to reduce wear and tear.
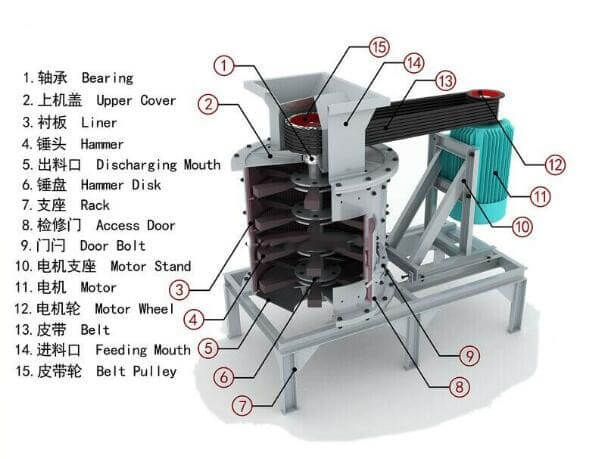
Vertical Shaft Compound Crusher Working Principle
The stone falls vertically into the machine body from the upper part of the vertical shaft compound crusher and falls onto the equipment’s throwing plate. Under centrifugal force, the material is thrown to the inner wall of the cylinder and violently collides with the counterattack plate installed on the inner wall. Violent impact also occurs, and the material is broken or cracked. After the material enters the conical rotor cavity, it is broken by stamping, extrusion, etc., during the falling process. The material is further broken into small particles, and the qualified finished product is discharged from the discharge port.
Technical Parameters
Model | Rotor Diameter (mm) | Speed of Mainshaft (r/min) | Feeding Size (mm) | Discharge Size (mm) | Capacity (t/h) | Power (kW) |
800 | 650 | 1350 | 50 | 0-5 | 5-15 | 30 |
1000 | 800 | 970 | 70 | 0-5 | 10-30 | 55 |
1250 | 1000 | 940 | 100 | 0-5 | 20-60 | 75 |
1500 | 1250 | 650 | 100 | 0-5 | 30-80 | 110 |
1750 | 1560 | 600 | 100 | 0-5 | 40-100 | 185-200 |
2000 | 1740 | 500 | 100 | 0-5 | 80-200 | 220-250 |