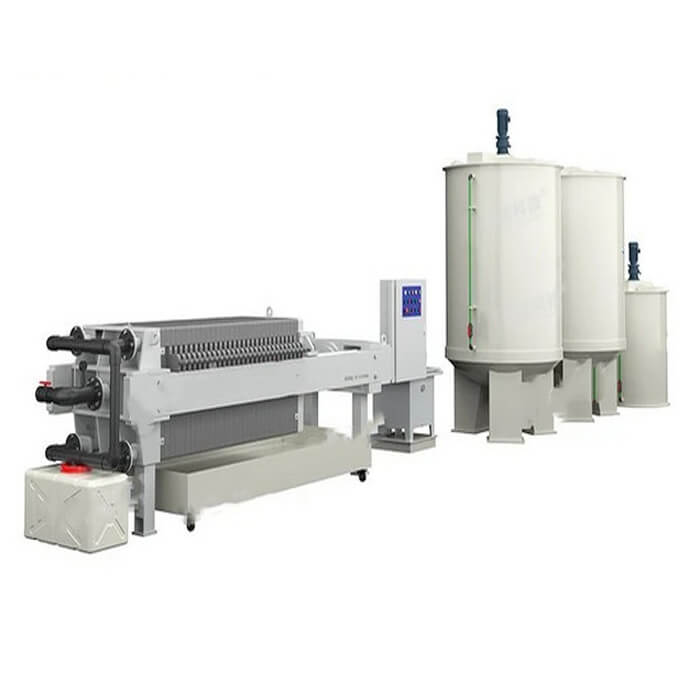
Tin Stripping Solution And Tin Recycling Equipment
Waste Liquid Treatment Capacity: 0-160 tons/month
Metal Production: 0-10 tons/month
Electricity Load: 15-50 kW
Tin Stripping Solution And Tin Recycling Equipment Overview
Tin stripping solution is commonly used for the removal of tin/lead and tin alloy layers from copper surfaces in the manufacturing process of electronic components (ICs) and printed circuit boards (PCBs), as well as for the removal of tin plating, tin-lead alloy plating, and tin solder joints. It is especially suitable for removing tin or lead-tin alloy layers on the copper surface of electronic components and discarded printed circuit boards. It can be operated by immersion or mechanical spraying.
The waste tin stripping solution usually contains metal ions(mainly tin (Sn) and other alloy components, such as copper (Cu), lead (Pb), etc.), acidic compounds(such as hydrofluoric acid (HF), nitric acid (HNO3), etc., used to dissolve the metal in the tin stripping process.), organic compounds(The tin stripping solution may contain some additives or auxiliaries.). These components make the waste solution need special treatment to be recycled and reused.
The tin stripping solution regeneration and tin recycling equipment are mainly concerned with the technology of recovering and recycling tin stripping solution. The equipment is designed to minimize resource waste, improve processing efficiency, and reduce environmental pollution. The equipment can regenerate the process through the following processes:
- Waste liquid filtration and purification
First, the waste liquid needs to go through coarse filtration to remove suspended matter and large particle impurities. Next, the liquid is further purified by ion exchange, activated carbon adsorption, or electrochemical methods. - Metal Separation and Recovery
Electrolysis or chemical precipitation is utilized to separate tin ions from the waste liquid. Electrolysis equipment allows tin to be deposited in solid form on the electrode surface, and the recovered tin can be used for reprocessing. The chemical precipitation method precipitates tin as a precipitate by adding a precipitating agent, which is then recovered by equipment such as filter presses. - Recycling
The treated waste liquid can be reused in production after neutralization, pH adjustment, and other steps to reduce the use of fresh acid.
![{"type":"elementor","siteurl":"https://www.jxscmineral.com/wp-json/","elements":[{"id":"3ffa5cf4","elType":"container","isInner":false,"isLocked":false,"settings":{"flex_direction":"column","container_type":"flex","content_width":"boxed","width":{"unit":"%","size":"","sizes":[]},"width_tablet":{"unit":"px","size":"","sizes":[]},"width_mobile":{"unit":"px","size":"","sizes":[]},"boxed_width":{"unit":"px","size":"","sizes":[]},"boxed_width_tablet":{"unit":"px","size":"","sizes":[]},"boxed_width_mobile":{"unit":"px","size":"","sizes":[]},"min_height":{"unit":"px","size":"","sizes":[]},"min_height_tablet":{"unit":"px","size":"","sizes":[]},"min_height_mobile":{"unit":"px","size":"","sizes":[]},"flex_direction_tablet":"","flex_direction_mobile":"","flex__is_row":"row","flex__is_column":"column","flex_justify_content":"","flex_justify_content_tablet":"","flex_justify_content_mobile":"","flex_align_items":"","flex_align_items_tablet":"","flex_align_items_mobile":"","flex_gap":{"column":"","row":"","isLinked":true,"unit":"px"},"flex_gap_tablet":{"column":"","row":"","isLinked":true,"unit":"px"},"flex_gap_mobile":{"column":"","row":"","isLinked":true,"unit":"px"},"flex_wrap":"","flex_wrap_tablet":"","flex_wrap_mobile":"","flex_align_content":"","flex_align_content_tablet":"","flex_align_content_mobile":"","grid_outline":"yes","grid_columns_grid":{"unit":"fr","size":3,"sizes":[]},"grid_columns_grid_tablet":{"unit":"fr","size":"","sizes":[]},"grid_columns_grid_mobile":{"unit":"fr","size":1,"sizes":[]},"grid_rows_grid":{"unit":"fr","size":2,"sizes":[]},"grid_rows_grid_tablet":{"unit":"fr","size":"","sizes":[]},"grid_rows_grid_mobile":{"unit":"fr","size":"","sizes":[]},"grid_gaps":{"column":"","row":"","isLinked":true,"unit":"px"},"grid_gaps_tablet":{"column":"","row":"","isLinked":true,"unit":"px"},"grid_gaps_mobile":{"column":"","row":"","isLinked":true,"unit":"px"},"grid_auto_flow":"row","grid_auto_flow_tablet":"row","grid_auto_flow_mobile":"row","grid_justify_items":"","grid_justify_items_tablet":"","grid_justify_items_mobile":"","grid_align_items":"","grid_align_items_tablet":"","grid_align_items_mobile":"","grid_justify_content":"","grid_justify_content_tablet":"","grid_justify_content_mobile":"","grid_align_content":"","grid_align_content_tablet":"","grid_align_content_mobile":"","grid__is_row":"row","grid__is_column":"column","overflow":"","html_tag":"","link":{"url":"","is_external":"","nofollow":"","custom_attributes":""},"background_background":"","background_color":"","background_color_stop":{"unit":"%","size":0,"sizes":[]},"background_color_stop_tablet":{"unit":"%"},"background_color_stop_mobile":{"unit":"%"},"background_color_b":"#f2295b","background_color_b_stop":{"unit":"%","size":100,"sizes":[]},"background_color_b_stop_tablet":{"unit":"%"},"background_color_b_stop_mobile":{"unit":"%"},"background_gradient_type":"linear","background_gradient_angle":{"unit":"deg","size":180,"sizes":[]},"background_gradient_angle_tablet":{"unit":"deg"},"background_gradient_angle_mobile":{"unit":"deg"},"background_gradient_position":"center center","background_gradient_position_tablet":"","background_gradient_position_mobile":"","background_image":{"url":"","id":"","size":""},"background_image_tablet":{"url":"","id":"","size":""},"background_image_mobile":{"url":"","id":"","size":""},"background_position":"","background_position_tablet":"","background_position_mobile":"","background_xpos":{"unit":"px","size":0,"sizes":[]},"background_xpos_tablet":{"unit":"px","size":0,"sizes":[]},"background_xpos_mobile":{"unit":"px","size":0,"sizes":[]},"background_ypos":{"unit":"px","size":0,"sizes":[]},"background_ypos_tablet":{"unit":"px","size":0,"sizes":[]},"background_ypos_mobile":{"unit":"px","size":0,"sizes":[]},"background_attachment":"","background_repeat":"","background_repeat_tablet":"","background_repeat_mobile":"","background_size":"","background_size_tablet":"","background_size_mobile":"","background_bg_width":{"unit":"%","size":100,"sizes":[]},"background_bg_width_tablet":{"unit":"px","size":"","sizes":[]},"background_bg_width_mobile":{"unit":"px","size":"","sizes":[]},"background_video_link":"","background_video_start":"","background_video_end":"","background_play_once":"","background_play_on_mobile":"","background_privacy_mode":"","background_video_fallback":{"url":"","id":"","size":""},"background_slideshow_gallery":[],"background_slideshow_loop":"yes","background_slideshow_slide_duration":5000,"background_slideshow_slide_transition":"fade","background_slideshow_transition_duration":500,"background_slideshow_background_size":"","background_slideshow_background_size_tablet":"","background_slideshow_background_size_mobile":"","background_slideshow_background_position":"","background_slideshow_background_position_tablet":"","background_slideshow_background_position_mobile":"","background_slideshow_lazyload":"","background_slideshow_ken_burns":"","background_slideshow_ken_burns_zoom_direction":"in","background_hover_background":"","background_hover_color":"","background_hover_color_stop":{"unit":"%","size":0,"sizes":[]},"background_hover_color_stop_tablet":{"unit":"%"},"background_hover_color_stop_mobile":{"unit":"%"},"background_hover_color_b":"#f2295b","background_hover_color_b_stop":{"unit":"%","size":100,"sizes":[]},"background_hover_color_b_stop_tablet":{"unit":"%"},"background_hover_color_b_stop_mobile":{"unit":"%"},"background_hover_gradient_type":"linear","background_hover_gradient_angle":{"unit":"deg","size":180,"sizes":[]},"background_hover_gradient_angle_tablet":{"unit":"deg"},"background_hover_gradient_angle_mobile":{"unit":"deg"},"background_hover_gradient_position":"center center","background_hover_gradient_position_tablet":"","background_hover_gradient_position_mobile":"","background_hover_image":{"url":"","id":"","size":""},"background_hover_image_tablet":{"url":"","id":"","size":""},"background_hover_image_mobile":{"url":"","id":"","size":""},"background_hover_position":"","background_hover_position_tablet":"","background_hover_position_mobile":"","background_hover_xpos":{"unit":"px","size":0,"sizes":[]},"background_hover_xpos_tablet":{"unit":"px","size":0,"sizes":[]},"background_hover_xpos_mobile":{"unit":"px","size":0,"sizes":[]},"background_hover_ypos":{"unit":"px","size":0,"sizes":[]},"background_hover_ypos_tablet":{"unit":"px","size":0,"sizes":[]},"background_hover_ypos_mobile":{"unit":"px","size":0,"sizes":[]},"background_hover_attachment":"","background_hover_repeat":"","background_hover_repeat_tablet":"","background_hover_repeat_mobile":"","background_hover_size":"","background_hover_size_tablet":"","background_hover_size_mobile":"","background_hover_bg_width":{"unit":"%","size":100,"sizes":[]},"background_hover_bg_width_tablet":{"unit":"px","size":"","sizes":[]},"background_hover_bg_width_mobile":{"unit":"px","size":"","sizes":[]},"background_hover_video_link":"","background_hover_video_start":"","background_hover_video_end":"","background_hover_play_once":"","background_hover_play_on_mobile":"","background_hover_privacy_mode":"","background_hover_video_fallback":{"url":"","id":"","size":""},"background_hover_slideshow_gallery":[],"background_hover_slideshow_loop":"yes","background_hover_slideshow_slide_duration":5000,"background_hover_slideshow_slide_transition":"fade","background_hover_slideshow_transition_duration":500,"background_hover_slideshow_background_size":"","background_hover_slideshow_background_size_tablet":"","background_hover_slideshow_background_size_mobile":"","background_hover_slideshow_background_position":"","background_hover_slideshow_background_position_tablet":"","background_hover_slideshow_background_position_mobile":"","background_hover_slideshow_lazyload":"","background_hover_slideshow_ken_burns":"","background_hover_slideshow_ken_burns_zoom_direction":"in","background_hover_transition":{"unit":"px","size":0.3,"sizes":[]},"background_motion_fx_motion_fx_scrolling":"","background_motion_fx_translateY_effect":"","background_motion_fx_translateY_direction":"","background_motion_fx_translateY_speed":{"unit":"px","size":4,"sizes":[]},"background_motion_fx_translateY_affectedRange":{"unit":"%","size":"","sizes":{"start":0,"end":100}},"background_motion_fx_translateX_effect":"","background_motion_fx_translateX_direction":"","background_motion_fx_translateX_speed":{"unit":"px","size":4,"sizes":[]},"background_motion_fx_translateX_affectedRange":{"unit":"%","size":"","sizes":{"start":0,"end":100}},"background_motion_fx_opacity_effect":"","background_motion_fx_opacity_direction":"out-in","background_motion_fx_opacity_level":{"unit":"px","size":10,"sizes":[]},"background_motion_fx_opacity_range":{"unit":"%","size":"","sizes":{"start":20,"end":80}},"background_motion_fx_blur_effect":"","background_motion_fx_blur_direction":"out-in","background_motion_fx_blur_level":{"unit":"px","size":7,"sizes":[]},"background_motion_fx_blur_range":{"unit":"%","size":"","sizes":{"start":20,"end":80}},"background_motion_fx_rotateZ_direction":"","background_motion_fx_rotateZ_speed":{"unit":"px","size":1,"sizes":[]},"background_motion_fx_rotateZ_affectedRange":{"unit":"%","size":"","sizes":{"start":0,"end":100}},"background_motion_fx_scale_effect":"","background_motion_fx_scale_direction":"out-in","background_motion_fx_scale_speed":{"unit":"px","size":4,"sizes":[]},"background_motion_fx_scale_range":{"unit":"%","size":"","sizes":{"start":20,"end":80}},"background_motion_fx_devices":["desktop","tablet","mobile"],"background_motion_fx_range":"","background_motion_fx_motion_fx_mouse":"","background_motion_fx_mouseTrack_effect":"","background_motion_fx_mouseTrack_direction":"","background_motion_fx_mouseTrack_speed":{"unit":"px","size":1,"sizes":[]},"background_motion_fx_tilt_direction":"","background_motion_fx_tilt_speed":{"unit":"px","size":4,"sizes":[]},"background_overlay_background":"","background_overlay_color":"","background_overlay_color_stop":{"unit":"%","size":0,"sizes":[]},"background_overlay_color_stop_tablet":{"unit":"%"},"background_overlay_color_stop_mobile":{"unit":"%"},"background_overlay_color_b":"#f2295b","background_overlay_color_b_stop":{"unit":"%","size":100,"sizes":[]},"background_overlay_color_b_stop_tablet":{"unit":"%"},"background_overlay_color_b_stop_mobile":{"unit":"%"},"background_overlay_gradient_type":"linear","background_overlay_gradient_angle":{"unit":"deg","size":180,"sizes":[]},"background_overlay_gradient_angle_tablet":{"unit":"deg"},"background_overlay_gradient_angle_mobile":{"unit":"deg"},"background_overlay_gradient_position":"center center","background_overlay_gradient_position_tablet":"","background_overlay_gradient_position_mobile":"","background_overlay_image":{"url":"","id":"","size":""},"background_overlay_image_tablet":{"url":"","id":"","size":""},"background_overlay_image_mobile":{"url":"","id":"","size":""},"background_overlay_position":"","background_overlay_position_tablet":"","background_overlay_position_mobile":"","background_overlay_xpos":{"unit":"px","size":0,"sizes":[]},"background_overlay_xpos_tablet":{"unit":"px","size":0,"sizes":[]},"background_overlay_xpos_mobile":{"unit":"px","size":0,"sizes":[]},"background_overlay_ypos":{"unit":"px","size":0,"sizes":[]},"background_overlay_ypos_tablet":{"unit":"px","size":0,"sizes":[]},"background_overlay_ypos_mobile":{"unit":"px","size":0,"sizes":[]},"background_overlay_attachment":"","background_overlay_repeat":"","background_overlay_repeat_tablet":"","background_overlay_repeat_mobile":"","background_overlay_size":"","background_overlay_size_tablet":"","background_overlay_size_mobile":"","background_overlay_bg_width":{"unit":"%","size":100,"sizes":[]},"background_overlay_bg_width_tablet":{"unit":"px","size":"","sizes":[]},"background_overlay_bg_width_mobile":{"unit":"px","size":"","sizes":[]},"background_overlay_video_link":"","background_overlay_video_start":"","background_overlay_video_end":"","background_overlay_play_once":"","background_overlay_play_on_mobile":"","background_overlay_privacy_mode":"","background_overlay_video_fallback":{"url":"","id":"","size":""},"background_overlay_slideshow_gallery":[],"background_overlay_slideshow_loop":"yes","background_overlay_slideshow_slide_duration":5000,"background_overlay_slideshow_slide_transition":"fade","background_overlay_slideshow_transition_duration":500,"background_overlay_slideshow_background_size":"","background_overlay_slideshow_background_size_tablet":"","background_overlay_slideshow_background_size_mobile":"","background_overlay_slideshow_background_position":"","background_overlay_slideshow_background_position_tablet":"","background_overlay_slideshow_background_position_mobile":"","background_overlay_slideshow_lazyload":"","background_overlay_slideshow_ken_burns":"","background_overlay_slideshow_ken_burns_zoom_direction":"in","background_overlay_opacity":{"unit":"px","size":0.5,"sizes":[]},"background_overlay_opacity_tablet":{"unit":"px","size":"","sizes":[]},"background_overlay_opacity_mobile":{"unit":"px","size":"","sizes":[]},"css_filters_css_filter":"","css_filters_blur":{"unit":"px","size":0,"sizes":[]},"css_filters_brightness":{"unit":"px","size":100,"sizes":[]},"css_filters_contrast":{"unit":"px","size":100,"sizes":[]},"css_filters_saturate":{"unit":"px","size":100,"sizes":[]},"css_filters_hue":{"unit":"px","size":0,"sizes":[]},"overlay_blend_mode":"","background_overlay_hover_background":"","background_overlay_hover_color":"","background_overlay_hover_color_stop":{"unit":"%","size":0,"sizes":[]},"background_overlay_hover_color_stop_tablet":{"unit":"%"},"background_overlay_hover_color_stop_mobile":{"unit":"%"},"background_overlay_hover_color_b":"#f2295b","background_overlay_hover_color_b_stop":{"unit":"%","size":100,"sizes":[]},"background_overlay_hover_color_b_stop_tablet":{"unit":"%"},"background_overlay_hover_color_b_stop_mobile":{"unit":"%"},"background_overlay_hover_gradient_type":"linear","background_overlay_hover_gradient_angle":{"unit":"deg","size":180,"sizes":[]},"background_overlay_hover_gradient_angle_tablet":{"unit":"deg"},"background_overlay_hover_gradient_angle_mobile":{"unit":"deg"},"background_overlay_hover_gradient_position":"center center","background_overlay_hover_gradient_position_tablet":"","background_overlay_hover_gradient_position_mobile":"","background_overlay_hover_image":{"url":"","id":"","size":""},"background_overlay_hover_image_tablet":{"url":"","id":"","size":""},"background_overlay_hover_image_mobile":{"url":"","id":"","size":""},"background_overlay_hover_position":"","background_overlay_hover_position_tablet":"","background_overlay_hover_position_mobile":"","background_overlay_hover_xpos":{"unit":"px","size":0,"sizes":[]},"background_overlay_hover_xpos_tablet":{"unit":"px","size":0,"sizes":[]},"background_overlay_hover_xpos_mobile":{"unit":"px","size":0,"sizes":[]},"background_overlay_hover_ypos":{"unit":"px","size":0,"sizes":[]},"background_overlay_hover_ypos_tablet":{"unit":"px","size":0,"sizes":[]},"background_overlay_hover_ypos_mobile":{"unit":"px","size":0,"sizes":[]},"background_overlay_hover_attachment":"","background_overlay_hover_repeat":"","background_overlay_hover_repeat_tablet":"","background_overlay_hover_repeat_mobile":"","background_overlay_hover_size":"","background_overlay_hover_size_tablet":"","background_overlay_hover_size_mobile":"","background_overlay_hover_bg_width":{"unit":"%","size":100,"sizes":[]},"background_overlay_hover_bg_width_tablet":{"unit":"px","size":"","sizes":[]},"background_overlay_hover_bg_width_mobile":{"unit":"px","size":"","sizes":[]},"background_overlay_hover_video_link":"","background_overlay_hover_video_start":"","background_overlay_hover_video_end":"","background_overlay_hover_play_once":"","background_overlay_hover_play_on_mobile":"","background_overlay_hover_privacy_mode":"","background_overlay_hover_video_fallback":{"url":"","id":"","size":""},"background_overlay_hover_slideshow_gallery":[],"background_overlay_hover_slideshow_loop":"yes","background_overlay_hover_slideshow_slide_duration":5000,"background_overlay_hover_slideshow_slide_transition":"fade","background_overlay_hover_slideshow_transition_duration":500,"background_overlay_hover_slideshow_background_size":"","background_overlay_hover_slideshow_background_size_tablet":"","background_overlay_hover_slideshow_background_size_mobile":"","background_overlay_hover_slideshow_background_position":"","background_overlay_hover_slideshow_background_position_tablet":"","background_overlay_hover_slideshow_background_position_mobile":"","background_overlay_hover_slideshow_lazyload":"","background_overlay_hover_slideshow_ken_burns":"","background_overlay_hover_slideshow_ken_burns_zoom_direction":"in","background_overlay_hover_opacity":{"unit":"px","size":0.5,"sizes":[]},"background_overlay_hover_opacity_tablet":{"unit":"px","size":"","sizes":[]},"background_overlay_hover_opacity_mobile":{"unit":"px","size":"","sizes":[]},"css_filters_hover_css_filter":"","css_filters_hover_blur":{"unit":"px","size":0,"sizes":[]},"css_filters_hover_brightness":{"unit":"px","size":100,"sizes":[]},"css_filters_hover_contrast":{"unit":"px","size":100,"sizes":[]},"css_filters_hover_saturate":{"unit":"px","size":100,"sizes":[]},"css_filters_hover_hue":{"unit":"px","size":0,"sizes":[]},"background_overlay_hover_transition":{"unit":"px","size":"","sizes":[]},"border_border":"","border_width":{"unit":"px","top":"","right":"","bottom":"","left":"","isLinked":true},"border_width_tablet":{"unit":"px","top":"","right":"","bottom":"","left":"","isLinked":true},"border_width_mobile":{"unit":"px","top":"","right":"","bottom":"","left":"","isLinked":true},"border_color":"","border_radius":{"unit":"px","top":"","right":"","bottom":"","left":"","isLinked":true},"border_radius_tablet":{"unit":"px","top":"","right":"","bottom":"","left":"","isLinked":true},"border_radius_mobile":{"unit":"px","top":"","right":"","bottom":"","left":"","isLinked":true},"box_shadow_box_shadow_type":"","box_shadow_box_shadow":{"horizontal":0,"vertical":0,"blur":10,"spread":0,"color":"rgba(0,0,0,0.5)"},"box_shadow_box_shadow_position":" ","border_hover_border":"","border_hover_width":{"unit":"px","top":"","right":"","bottom":"","left":"","isLinked":true},"border_hover_width_tablet":{"unit":"px","top":"","right":"","bottom":"","left":"","isLinked":true},"border_hover_width_mobile":{"unit":"px","top":"","right":"","bottom":"","left":"","isLinked":true},"border_hover_color":"","border_radius_hover":{"unit":"px","top":"","right":"","bottom":"","left":"","isLinked":true},"border_radius_hover_tablet":{"unit":"px","top":"","right":"","bottom":"","left":"","isLinked":true},"border_radius_hover_mobile":{"unit":"px","top":"","right":"","bottom":"","left":"","isLinked":true},"box_shadow_hover_box_shadow_type":"","box_shadow_hover_box_shadow":{"horizontal":0,"vertical":0,"blur":10,"spread":0,"color":"rgba(0,0,0,0.5)"},"box_shadow_hover_box_shadow_position":" ","border_hover_transition":{"unit":"px","size":0.3,"sizes":[]},"shape_divider_top":"","shape_divider_top_color":"","shape_divider_top_width":{"unit":"%","size":"","sizes":[]},"shape_divider_top_width_tablet":{"unit":"%","size":"","sizes":[]},"shape_divider_top_width_mobile":{"unit":"%","size":"","sizes":[]},"shape_divider_top_height":{"unit":"px","size":"","sizes":[]},"shape_divider_top_height_tablet":{"unit":"px","size":"","sizes":[]},"shape_divider_top_height_mobile":{"unit":"px","size":"","sizes":[]},"shape_divider_top_flip":"","shape_divider_top_negative":"","shape_divider_top_above_content":"","shape_divider_bottom":"","shape_divider_bottom_color":"","shape_divider_bottom_width":{"unit":"%","size":"","sizes":[]},"shape_divider_bottom_width_tablet":{"unit":"%","size":"","sizes":[]},"shape_divider_bottom_width_mobile":{"unit":"%","size":"","sizes":[]},"shape_divider_bottom_height":{"unit":"px","size":"","sizes":[]},"shape_divider_bottom_height_tablet":{"unit":"px","size":"","sizes":[]},"shape_divider_bottom_height_mobile":{"unit":"px","size":"","sizes":[]},"shape_divider_bottom_flip":"","shape_divider_bottom_negative":"","shape_divider_bottom_above_content":"","margin":{"unit":"px","top":"","right":"","bottom":"","left":"","isLinked":true},"margin_tablet":{"unit":"px","top":"","right":"","bottom":"","left":"","isLinked":true},"margin_mobile":{"unit":"px","top":"","right":"","bottom":"","left":"","isLinked":true},"padding":{"unit":"px","top":"","right":"","bottom":"","left":"","isLinked":true},"padding_tablet":{"unit":"px","top":"","right":"","bottom":"","left":"","isLinked":true},"padding_mobile":{"unit":"px","top":"","right":"","bottom":"","left":"","isLinked":true},"_flex_align_self":"","_flex_align_self_tablet":"","_flex_align_self_mobile":"","_flex_order":"","_flex_order_tablet":"","_flex_order_mobile":"","_flex_order_custom":"","_flex_order_custom_tablet":"","_flex_order_custom_mobile":"","_flex_size":"","_flex_size_tablet":"","_flex_size_mobile":"","_flex_grow":1,"_flex_grow_tablet":"","_flex_grow_mobile":"","_flex_shrink":1,"_flex_shrink_tablet":"","_flex_shrink_mobile":"","position":"","_offset_orientation_h":"start","_offset_x":{"unit":"px","size":0,"sizes":[]},"_offset_x_tablet":{"unit":"px","size":"","sizes":[]},"_offset_x_mobile":{"unit":"px","size":"","sizes":[]},"_offset_x_end":{"unit":"px","size":0,"sizes":[]},"_offset_x_end_tablet":{"unit":"px","size":"","sizes":[]},"_offset_x_end_mobile":{"unit":"px","size":"","sizes":[]},"_offset_orientation_v":"start","_offset_y":{"unit":"px","size":0,"sizes":[]},"_offset_y_tablet":{"unit":"px","size":"","sizes":[]},"_offset_y_mobile":{"unit":"px","size":"","sizes":[]},"_offset_y_end":{"unit":"px","size":0,"sizes":[]},"_offset_y_end_tablet":{"unit":"px","size":"","sizes":[]},"_offset_y_end_mobile":{"unit":"px","size":"","sizes":[]},"z_index":"","z_index_tablet":"","z_index_mobile":"","_element_id":"","css_classes":"","e_display_conditions":"","motion_fx_motion_fx_scrolling":"","motion_fx_translateY_effect":"","motion_fx_translateY_direction":"","motion_fx_translateY_speed":{"unit":"px","size":4,"sizes":[]},"motion_fx_translateY_affectedRange":{"unit":"%","size":"","sizes":{"start":0,"end":100}},"motion_fx_translateX_effect":"","motion_fx_translateX_direction":"","motion_fx_translateX_speed":{"unit":"px","size":4,"sizes":[]},"motion_fx_translateX_affectedRange":{"unit":"%","size":"","sizes":{"start":0,"end":100}},"motion_fx_opacity_effect":"","motion_fx_opacity_direction":"out-in","motion_fx_opacity_level":{"unit":"px","size":10,"sizes":[]},"motion_fx_opacity_range":{"unit":"%","size":"","sizes":{"start":20,"end":80}},"motion_fx_blur_effect":"","motion_fx_blur_direction":"out-in","motion_fx_blur_level":{"unit":"px","size":7,"sizes":[]},"motion_fx_blur_range":{"unit":"%","size":"","sizes":{"start":20,"end":80}},"motion_fx_rotateZ_effect":"","motion_fx_rotateZ_direction":"","motion_fx_rotateZ_speed":{"unit":"px","size":1,"sizes":[]},"motion_fx_rotateZ_affectedRange":{"unit":"%","size":"","sizes":{"start":0,"end":100}},"motion_fx_scale_effect":"","motion_fx_scale_direction":"out-in","motion_fx_scale_speed":{"unit":"px","size":4,"sizes":[]},"motion_fx_scale_range":{"unit":"%","size":"","sizes":{"start":20,"end":80}},"motion_fx_transform_origin_x":"center","motion_fx_transform_origin_y":"center","motion_fx_devices":["desktop","tablet","mobile"],"motion_fx_range":"","motion_fx_motion_fx_mouse":"","motion_fx_mouseTrack_effect":"","motion_fx_mouseTrack_direction":"","motion_fx_mouseTrack_speed":{"unit":"px","size":1,"sizes":[]},"motion_fx_tilt_effect":"","motion_fx_tilt_direction":"","motion_fx_tilt_speed":{"unit":"px","size":4,"sizes":[]},"sticky":"","sticky_on":["desktop","tablet","mobile"],"sticky_offset":0,"sticky_offset_tablet":"","sticky_offset_mobile":"","sticky_effects_offset":0,"sticky_effects_offset_tablet":"","sticky_effects_offset_mobile":"","sticky_parent":"","animation":"","animation_tablet":"","animation_mobile":"","animation_duration":"","animation_delay":"","_transform_rotate_popover":"","_transform_rotateZ_effect":{"unit":"px","size":"","sizes":[]},"_transform_rotateZ_effect_tablet":{"unit":"deg","size":"","sizes":[]},"_transform_rotateZ_effect_mobile":{"unit":"deg","size":"","sizes":[]},"_transform_rotate_3d":"","_transform_rotateX_effect":{"unit":"px","size":"","sizes":[]},"_transform_rotateX_effect_tablet":{"unit":"deg","size":"","sizes":[]},"_transform_rotateX_effect_mobile":{"unit":"deg","size":"","sizes":[]},"_transform_rotateY_effect":{"unit":"px","size":"","sizes":[]},"_transform_rotateY_effect_tablet":{"unit":"deg","size":"","sizes":[]},"_transform_rotateY_effect_mobile":{"unit":"deg","size":"","sizes":[]},"_transform_perspective_effect":{"unit":"px","size":"","sizes":[]},"_transform_perspective_effect_tablet":{"unit":"px","size":"","sizes":[]},"_transform_perspective_effect_mobile":{"unit":"px","size":"","sizes":[]},"_transform_translate_popover":"","_transform_translateX_effect":{"unit":"px","size":"","sizes":[]},"_transform_translateX_effect_tablet":{"unit":"px","size":"","sizes":[]},"_transform_translateX_effect_mobile":{"unit":"px","size":"","sizes":[]},"_transform_translateY_effect":{"unit":"px","size":"","sizes":[]},"_transform_translateY_effect_tablet":{"unit":"px","size":"","sizes":[]},"_transform_translateY_effect_mobile":{"unit":"px","size":"","sizes":[]},"_transform_scale_popover":"","_transform_keep_proportions":"yes","_transform_scale_effect":{"unit":"px","size":"","sizes":[]},"_transform_scale_effect_tablet":{"unit":"px","size":"","sizes":[]},"_transform_scale_effect_mobile":{"unit":"px","size":"","sizes":[]},"_transform_scaleX_effect":{"unit":"px","size":"","sizes":[]},"_transform_scaleX_effect_tablet":{"unit":"px","size":"","sizes":[]},"_transform_scaleX_effect_mobile":{"unit":"px","size":"","sizes":[]},"_transform_scaleY_effect":{"unit":"px","size":"","sizes":[]},"_transform_scaleY_effect_tablet":{"unit":"px","size":"","sizes":[]},"_transform_scaleY_effect_mobile":{"unit":"px","size":"","sizes":[]},"_transform_skew_popover":"","_transform_skewX_effect":{"unit":"px","size":"","sizes":[]},"_transform_skewX_effect_tablet":{"unit":"deg","size":"","sizes":[]},"_transform_skewX_effect_mobile":{"unit":"deg","size":"","sizes":[]},"_transform_skewY_effect":{"unit":"px","size":"","sizes":[]},"_transform_skewY_effect_tablet":{"unit":"deg","size":"","sizes":[]},"_transform_skewY_effect_mobile":{"unit":"deg","size":"","sizes":[]},"_transform_flipX_effect":"","_transform_flipY_effect":"","_transform_rotate_popover_hover":"","_transform_rotateZ_effect_hover":{"unit":"px","size":"","sizes":[]},"_transform_rotateZ_effect_hover_tablet":{"unit":"deg","size":"","sizes":[]},"_transform_rotateZ_effect_hover_mobile":{"unit":"deg","size":"","sizes":[]},"_transform_rotate_3d_hover":"","_transform_rotateX_effect_hover":{"unit":"px","size":"","sizes":[]},"_transform_rotateX_effect_hover_tablet":{"unit":"deg","size":"","sizes":[]},"_transform_rotateX_effect_hover_mobile":{"unit":"deg","size":"","sizes":[]},"_transform_rotateY_effect_hover":{"unit":"px","size":"","sizes":[]},"_transform_rotateY_effect_hover_tablet":{"unit":"deg","size":"","sizes":[]},"_transform_rotateY_effect_hover_mobile":{"unit":"deg","size":"","sizes":[]},"_transform_perspective_effect_hover":{"unit":"px","size":"","sizes":[]},"_transform_perspective_effect_hover_tablet":{"unit":"px","size":"","sizes":[]},"_transform_perspective_effect_hover_mobile":{"unit":"px","size":"","sizes":[]},"_transform_translate_popover_hover":"","_transform_translateX_effect_hover":{"unit":"px","size":"","sizes":[]},"_transform_translateX_effect_hover_tablet":{"unit":"px","size":"","sizes":[]},"_transform_translateX_effect_hover_mobile":{"unit":"px","size":"","sizes":[]},"_transform_translateY_effect_hover":{"unit":"px","size":"","sizes":[]},"_transform_translateY_effect_hover_tablet":{"unit":"px","size":"","sizes":[]},"_transform_translateY_effect_hover_mobile":{"unit":"px","size":"","sizes":[]},"_transform_scale_popover_hover":"","_transform_keep_proportions_hover":"yes","_transform_scale_effect_hover":{"unit":"px","size":"","sizes":[]},"_transform_scale_effect_hover_tablet":{"unit":"px","size":"","sizes":[]},"_transform_scale_effect_hover_mobile":{"unit":"px","size":"","sizes":[]},"_transform_scaleX_effect_hover":{"unit":"px","size":"","sizes":[]},"_transform_scaleX_effect_hover_tablet":{"unit":"px","size":"","sizes":[]},"_transform_scaleX_effect_hover_mobile":{"unit":"px","size":"","sizes":[]},"_transform_scaleY_effect_hover":{"unit":"px","size":"","sizes":[]},"_transform_scaleY_effect_hover_tablet":{"unit":"px","size":"","sizes":[]},"_transform_scaleY_effect_hover_mobile":{"unit":"px","size":"","sizes":[]},"_transform_skew_popover_hover":"","_transform_skewX_effect_hover":{"unit":"px","size":"","sizes":[]},"_transform_skewX_effect_hover_tablet":{"unit":"deg","size":"","sizes":[]},"_transform_skewX_effect_hover_mobile":{"unit":"deg","size":"","sizes":[]},"_transform_skewY_effect_hover":{"unit":"px","size":"","sizes":[]},"_transform_skewY_effect_hover_tablet":{"unit":"deg","size":"","sizes":[]},"_transform_skewY_effect_hover_mobile":{"unit":"deg","size":"","sizes":[]},"_transform_flipX_effect_hover":"","_transform_flipY_effect_hover":"","_transform_transition_hover":{"unit":"px","size":"","sizes":[]},"motion_fx_transform_x_anchor_point":"","motion_fx_transform_x_anchor_point_tablet":"","motion_fx_transform_x_anchor_point_mobile":"","motion_fx_transform_y_anchor_point":"","motion_fx_transform_y_anchor_point_tablet":"","motion_fx_transform_y_anchor_point_mobile":"","hide_desktop":"","hide_tablet":"","hide_mobile":"","_attributes":"","custom_css":""},"defaultEditSettings":{"defaultEditRoute":"content"},"elements":[{"id":"aa93750","elType":"widget","isInner":false,"isLocked":false,"settings":{"slides":[{"image":{"url":"https://www.jxscmineral.com/wp-content/uploads/2022/05/rotary-scrubber-5.jpg","id":2709,"alt":"rotary scrubber","source":"library"},"_id":"7f9b70e","type":"image","image_link_to_type":"","image_link_to":{"url":"","is_external":"","nofollow":"","custom_attributes":""},"video":{"url":"","is_external":"","nofollow":"","custom_attributes":""}},{"image":{"url":"https://www.jxscmineral.com/wp-content/uploads/2022/05/rotary-scrubber-2.jpg","id":2706,"alt":"rotary scrubber","source":"library"},"_id":"17f0074","type":"image","image_link_to_type":"","image_link_to":{"url":"","is_external":"","nofollow":"","custom_attributes":""},"video":{"url":"","is_external":"","nofollow":"","custom_attributes":""}},{"image":{"url":"https://www.jxscmineral.com/wp-content/uploads/2022/05/rotary-scrubber-1.jpg","id":2705,"alt":"rotary scrubber","source":"library"},"_id":"357038b","type":"image","image_link_to_type":"","image_link_to":{"url":"","is_external":"","nofollow":"","custom_attributes":""},"video":{"url":"","is_external":"","nofollow":"","custom_attributes":""}},{"_id":"d50274e","image":{"url":"https://www.jxscmineral.com/wp-content/uploads/2022/05/rotary-scrubber-3.jpg","id":2707,"alt":"rotary scrubber","source":"library","size":""},"type":"image","image_link_to_type":"","image_link_to":{"url":"","is_external":"","nofollow":"","custom_attributes":""},"video":{"url":"","is_external":"","nofollow":"","custom_attributes":""}}],"height":{"unit":"px","size":300,"sizes":[]},"content_width":"full","skin":"carousel","effect":"slide","slideshow_height":{"unit":"px","size":"","sizes":[]},"slideshow_height_tablet":{"unit":"px","size":"","sizes":[]},"slideshow_height_mobile":{"unit":"px","size":"","sizes":[]},"slides_per_view":"","slideshow_slides_per_view":"","slideshow_slides_per_view_tablet":"","slideshow_slides_per_view_mobile":"","thumbs_ratio":"219","centered_slides":"","slides_per_view_tablet":"","slides_per_view_mobile":"","slides_to_scroll":"","slides_to_scroll_tablet":"","slides_to_scroll_mobile":"","height_tablet":{"unit":"px","size":"","sizes":[]},"height_mobile":{"unit":"px","size":"","sizes":[]},"width":{"unit":"%","size":"","sizes":[]},"width_tablet":{"unit":"px","size":"","sizes":[]},"width_mobile":{"unit":"px","size":"","sizes":[]},"show_arrows":"yes","pagination":"bullets","speed":500,"autoplay":"yes","autoplay_speed":5000,"loop":"yes","pause_on_hover":"yes","pause_on_interaction":"yes","overlay":"","caption":"title","icon":"search-plus","overlay_animation":"fade","image_size_size":"full","image_size_custom_dimension":{"width":"","height":""},"image_fit":"","lazyload":"","space_between":{"unit":"px","size":10,"sizes":[]},"space_between_tablet":{"unit":"px","size":10,"sizes":[]},"space_between_mobile":{"unit":"px","size":10,"sizes":[]},"slide_background_color":"","slide_border_size":{"unit":"px","top":"","right":"","bottom":"","left":"","isLinked":true},"slide_border_radius":{"unit":"px","size":"","sizes":[]},"slide_border_color":"","slide_padding":{"unit":"px","top":"","right":"","bottom":"","left":"","isLinked":true},"arrows_size":{"unit":"px","size":20,"sizes":[]},"arrows_size_tablet":{"unit":"px","size":"","sizes":[]},"arrows_size_mobile":{"unit":"px","size":"","sizes":[]},"arrows_color":"","pagination_position":"outside","pagination_size":{"unit":"px","size":"","sizes":[]},"pagination_size_tablet":{"unit":"px","size":"","sizes":[]},"pagination_size_mobile":{"unit":"px","size":"","sizes":[]},"pagination_color_inactive":"","pagination_color":"","play_icon_color":"","play_icon_size":{"unit":"px","size":"","sizes":[]},"play_icon_size_tablet":{"unit":"px","size":"","sizes":[]},"play_icon_size_mobile":{"unit":"px","size":"","sizes":[]},"play_icon_text_shadow_text_shadow_type":"","play_icon_text_shadow_text_shadow":{"horizontal":0,"vertical":0,"blur":10,"color":"rgba(0,0,0,0.3)"},"overlay_background_color":"","overlay_color":"","caption_typography_typography":"","caption_typography_font_family":"","caption_typography_font_size":{"unit":"px","size":"","sizes":[]},"caption_typography_font_size_tablet":{"unit":"px","size":"","sizes":[]},"caption_typography_font_size_mobile":{"unit":"px","size":"","sizes":[]},"caption_typography_font_weight":"","caption_typography_text_transform":"","caption_typography_font_style":"","caption_typography_text_decoration":"","caption_typography_line_height":{"unit":"px","size":"","sizes":[]},"caption_typography_line_height_tablet":{"unit":"em","size":"","sizes":[]},"caption_typography_line_height_mobile":{"unit":"em","size":"","sizes":[]},"caption_typography_letter_spacing":{"unit":"px","size":"","sizes":[]},"caption_typography_letter_spacing_tablet":{"unit":"px","size":"","sizes":[]},"caption_typography_letter_spacing_mobile":{"unit":"px","size":"","sizes":[]},"caption_typography_word_spacing":{"unit":"px","size":"","sizes":[]},"caption_typography_word_spacing_tablet":{"unit":"em","size":"","sizes":[]},"caption_typography_word_spacing_mobile":{"unit":"em","size":"","sizes":[]},"icon_size":{"unit":"px","size":"","sizes":[]},"lightbox_color":"","lightbox_ui_color":"","lightbox_ui_hover_color":"","lightbox_video_width":{"unit":"%","size":"","sizes":[]},"_title":"","_margin":{"unit":"px","top":"","right":"","bottom":"","left":"","isLinked":true},"_margin_tablet":{"unit":"px","top":"","right":"","bottom":"","left":"","isLinked":true},"_margin_mobile":{"unit":"px","top":"","right":"","bottom":"","left":"","isLinked":true},"_padding":{"unit":"px","top":"","right":"","bottom":"","left":"","isLinked":true},"_padding_tablet":{"unit":"px","top":"","right":"","bottom":"","left":"","isLinked":true},"_padding_mobile":{"unit":"px","top":"","right":"","bottom":"","left":"","isLinked":true},"_element_width":"","_element_width_tablet":"","_element_width_mobile":"","_element_custom_width":{"unit":"%","size":"","sizes":[]},"_element_custom_width_tablet":{"unit":"px","size":"","sizes":[]},"_element_custom_width_mobile":{"unit":"px","size":"","sizes":[]},"_flex_align_self":"","_flex_align_self_tablet":"","_flex_align_self_mobile":"","_flex_order":"","_flex_order_tablet":"","_flex_order_mobile":"","_flex_order_custom":"","_flex_order_custom_tablet":"","_flex_order_custom_mobile":"","_flex_size":"","_flex_size_tablet":"","_flex_size_mobile":"","_flex_grow":1,"_flex_grow_tablet":"","_flex_grow_mobile":"","_flex_shrink":1,"_flex_shrink_tablet":"","_flex_shrink_mobile":"","_element_vertical_align":"","_element_vertical_align_tablet":"","_element_vertical_align_mobile":"","_position":"","_offset_orientation_h":"start","_offset_x":{"unit":"px","size":0,"sizes":[]},"_offset_x_tablet":{"unit":"px","size":"","sizes":[]},"_offset_x_mobile":{"unit":"px","size":"","sizes":[]},"_offset_x_end":{"unit":"px","size":0,"sizes":[]},"_offset_x_end_tablet":{"unit":"px","size":"","sizes":[]},"_offset_x_end_mobile":{"unit":"px","size":"","sizes":[]},"_offset_orientation_v":"start","_offset_y":{"unit":"px","size":0,"sizes":[]},"_offset_y_tablet":{"unit":"px","size":"","sizes":[]},"_offset_y_mobile":{"unit":"px","size":"","sizes":[]},"_offset_y_end":{"unit":"px","size":0,"sizes":[]},"_offset_y_end_tablet":{"unit":"px","size":"","sizes":[]},"_offset_y_end_mobile":{"unit":"px","size":"","sizes":[]},"_z_index":"","_z_index_tablet":"","_z_index_mobile":"","_element_id":"","_css_classes":"","e_display_conditions":"","motion_fx_motion_fx_scrolling":"","motion_fx_translateY_effect":"","motion_fx_translateY_direction":"","motion_fx_translateY_speed":{"unit":"px","size":4,"sizes":[]},"motion_fx_translateY_affectedRange":{"unit":"%","size":"","sizes":{"start":0,"end":100}},"motion_fx_translateX_effect":"","motion_fx_translateX_direction":"","motion_fx_translateX_speed":{"unit":"px","size":4,"sizes":[]},"motion_fx_translateX_affectedRange":{"unit":"%","size":"","sizes":{"start":0,"end":100}},"motion_fx_opacity_effect":"","motion_fx_opacity_direction":"out-in","motion_fx_opacity_level":{"unit":"px","size":10,"sizes":[]},"motion_fx_opacity_range":{"unit":"%","size":"","sizes":{"start":20,"end":80}},"motion_fx_blur_effect":"","motion_fx_blur_direction":"out-in","motion_fx_blur_level":{"unit":"px","size":7,"sizes":[]},"motion_fx_blur_range":{"unit":"%","size":"","sizes":{"start":20,"end":80}},"motion_fx_rotateZ_effect":"","motion_fx_rotateZ_direction":"","motion_fx_rotateZ_speed":{"unit":"px","size":1,"sizes":[]},"motion_fx_rotateZ_affectedRange":{"unit":"%","size":"","sizes":{"start":0,"end":100}},"motion_fx_scale_effect":"","motion_fx_scale_direction":"out-in","motion_fx_scale_speed":{"unit":"px","size":4,"sizes":[]},"motion_fx_scale_range":{"unit":"%","size":"","sizes":{"start":20,"end":80}},"motion_fx_transform_origin_x":"center","motion_fx_transform_origin_y":"center","motion_fx_devices":["desktop","tablet","mobile"],"motion_fx_range":"","motion_fx_motion_fx_mouse":"","motion_fx_mouseTrack_effect":"","motion_fx_mouseTrack_direction":"","motion_fx_mouseTrack_speed":{"unit":"px","size":1,"sizes":[]},"motion_fx_tilt_effect":"","motion_fx_tilt_direction":"","motion_fx_tilt_speed":{"unit":"px","size":4,"sizes":[]},"sticky":"","sticky_on":["desktop","tablet","mobile"],"sticky_offset":0,"sticky_offset_tablet":"","sticky_offset_mobile":"","sticky_effects_offset":0,"sticky_effects_offset_tablet":"","sticky_effects_offset_mobile":"","sticky_parent":"","_animation":"","_animation_tablet":"","_animation_mobile":"","animation_duration":"","_animation_delay":"","_transform_rotate_popover":"","_transform_rotateZ_effect":{"unit":"px","size":"","sizes":[]},"_transform_rotateZ_effect_tablet":{"unit":"deg","size":"","sizes":[]},"_transform_rotateZ_effect_mobile":{"unit":"deg","size":"","sizes":[]},"_transform_rotate_3d":"","_transform_rotateX_effect":{"unit":"px","size":"","sizes":[]},"_transform_rotateX_effect_tablet":{"unit":"deg","size":"","sizes":[]},"_transform_rotateX_effect_mobile":{"unit":"deg","size":"","sizes":[]},"_transform_rotateY_effect":{"unit":"px","size":"","sizes":[]},"_transform_rotateY_effect_tablet":{"unit":"deg","size":"","sizes":[]},"_transform_rotateY_effect_mobile":{"unit":"deg","size":"","sizes":[]},"_transform_perspective_effect":{"unit":"px","size":"","sizes":[]},"_transform_perspective_effect_tablet":{"unit":"px","size":"","sizes":[]},"_transform_perspective_effect_mobile":{"unit":"px","size":"","sizes":[]},"_transform_translate_popover":"","_transform_translateX_effect":{"unit":"px","size":"","sizes":[]},"_transform_translateX_effect_tablet":{"unit":"px","size":"","sizes":[]},"_transform_translateX_effect_mobile":{"unit":"px","size":"","sizes":[]},"_transform_translateY_effect":{"unit":"px","size":"","sizes":[]},"_transform_translateY_effect_tablet":{"unit":"px","size":"","sizes":[]},"_transform_translateY_effect_mobile":{"unit":"px","size":"","sizes":[]},"_transform_scale_popover":"","_transform_keep_proportions":"yes","_transform_scale_effect":{"unit":"px","size":"","sizes":[]},"_transform_scale_effect_tablet":{"unit":"px","size":"","sizes":[]},"_transform_scale_effect_mobile":{"unit":"px","size":"","sizes":[]},"_transform_scaleX_effect":{"unit":"px","size":"","sizes":[]},"_transform_scaleX_effect_tablet":{"unit":"px","size":"","sizes":[]},"_transform_scaleX_effect_mobile":{"unit":"px","size":"","sizes":[]},"_transform_scaleY_effect":{"unit":"px","size":"","sizes":[]},"_transform_scaleY_effect_tablet":{"unit":"px","size":"","sizes":[]},"_transform_scaleY_effect_mobile":{"unit":"px","size":"","sizes":[]},"_transform_skew_popover":"","_transform_skewX_effect":{"unit":"px","size":"","sizes":[]},"_transform_skewX_effect_tablet":{"unit":"deg","size":"","sizes":[]},"_transform_skewX_effect_mobile":{"unit":"deg","size":"","sizes":[]},"_transform_skewY_effect":{"unit":"px","size":"","sizes":[]},"_transform_skewY_effect_tablet":{"unit":"deg","size":"","sizes":[]},"_transform_skewY_effect_mobile":{"unit":"deg","size":"","sizes":[]},"_transform_flipX_effect":"","_transform_flipY_effect":"","_transform_rotate_popover_hover":"","_transform_rotateZ_effect_hover":{"unit":"px","size":"","sizes":[]},"_transform_rotateZ_effect_hover_tablet":{"unit":"deg","size":"","sizes":[]},"_transform_rotateZ_effect_hover_mobile":{"unit":"deg","size":"","sizes":[]},"_transform_rotate_3d_hover":"","_transform_rotateX_effect_hover":{"unit":"px","size":"","sizes":[]},"_transform_rotateX_effect_hover_tablet":{"unit":"deg","size":"","sizes":[]},"_transform_rotateX_effect_hover_mobile":{"unit":"deg","size":"","sizes":[]},"_transform_rotateY_effect_hover":{"unit":"px","size":"","sizes":[]},"_transform_rotateY_effect_hover_tablet":{"unit":"deg","size":"","sizes":[]},"_transform_rotateY_effect_hover_mobile":{"unit":"deg","size":"","sizes":[]},"_transform_perspective_effect_hover":{"unit":"px","size":"","sizes":[]},"_transform_perspective_effect_hover_tablet":{"unit":"px","size":"","sizes":[]},"_transform_perspective_effect_hover_mobile":{"unit":"px","size":"","sizes":[]},"_transform_translate_popover_hover":"","_transform_translateX_effect_hover":{"unit":"px","size":"","sizes":[]},"_transform_translateX_effect_hover_tablet":{"unit":"px","size":"","sizes":[]},"_transform_translateX_effect_hover_mobile":{"unit":"px","size":"","sizes":[]},"_transform_translateY_effect_hover":{"unit":"px","size":"","sizes":[]},"_transform_translateY_effect_hover_tablet":{"unit":"px","size":"","sizes":[]},"_transform_translateY_effect_hover_mobile":{"unit":"px","size":"","sizes":[]},"_transform_scale_popover_hover":"","_transform_keep_proportions_hover":"yes","_transform_scale_effect_hover":{"unit":"px","size":"","sizes":[]},"_transform_scale_effect_hover_tablet":{"unit":"px","size":"","sizes":[]},"_transform_scale_effect_hover_mobile":{"unit":"px","size":"","sizes":[]},"_transform_scaleX_effect_hover":{"unit":"px","size":"","sizes":[]},"_transform_scaleX_effect_hover_tablet":{"unit":"px","size":"","sizes":[]},"_transform_scaleX_effect_hover_mobile":{"unit":"px","size":"","sizes":[]},"_transform_scaleY_effect_hover":{"unit":"px","size":"","sizes":[]},"_transform_scaleY_effect_hover_tablet":{"unit":"px","size":"","sizes":[]},"_transform_scaleY_effect_hover_mobile":{"unit":"px","size":"","sizes":[]},"_transform_skew_popover_hover":"","_transform_skewX_effect_hover":{"unit":"px","size":"","sizes":[]},"_transform_skewX_effect_hover_tablet":{"unit":"deg","size":"","sizes":[]},"_transform_skewX_effect_hover_mobile":{"unit":"deg","size":"","sizes":[]},"_transform_skewY_effect_hover":{"unit":"px","size":"","sizes":[]},"_transform_skewY_effect_hover_tablet":{"unit":"deg","size":"","sizes":[]},"_transform_skewY_effect_hover_mobile":{"unit":"deg","size":"","sizes":[]},"_transform_flipX_effect_hover":"","_transform_flipY_effect_hover":"","_transform_transition_hover":{"unit":"px","size":"","sizes":[]},"motion_fx_transform_x_anchor_point":"","motion_fx_transform_x_anchor_point_tablet":"","motion_fx_transform_x_anchor_point_mobile":"","motion_fx_transform_y_anchor_point":"","motion_fx_transform_y_anchor_point_tablet":"","motion_fx_transform_y_anchor_point_mobile":"","_background_background":"","_background_color":"","_background_color_stop":{"unit":"%","size":0,"sizes":[]},"_background_color_stop_tablet":{"unit":"%","size":"","sizes":[]},"_background_color_stop_mobile":{"unit":"%","size":"","sizes":[]},"_background_color_b":"#f2295b","_background_color_b_stop":{"unit":"%","size":100,"sizes":[]},"_background_color_b_stop_tablet":{"unit":"%","size":"","sizes":[]},"_background_color_b_stop_mobile":{"unit":"%","size":"","sizes":[]},"_background_gradient_type":"linear","_background_gradient_angle":{"unit":"deg","size":180,"sizes":[]},"_background_gradient_angle_tablet":{"unit":"deg","size":"","sizes":[]},"_background_gradient_angle_mobile":{"unit":"deg","size":"","sizes":[]},"_background_gradient_position":"center center","_background_gradient_position_tablet":"","_background_gradient_position_mobile":"","_background_image":{"url":"","id":"","size":""},"_background_image_tablet":{"url":"","id":"","size":""},"_background_image_mobile":{"url":"","id":"","size":""},"_background_position":"","_background_position_tablet":"","_background_position_mobile":"","_background_xpos":{"unit":"px","size":0,"sizes":[]},"_background_xpos_tablet":{"unit":"px","size":0,"sizes":[]},"_background_xpos_mobile":{"unit":"px","size":0,"sizes":[]},"_background_ypos":{"unit":"px","size":0,"sizes":[]},"_background_ypos_tablet":{"unit":"px","size":0,"sizes":[]},"_background_ypos_mobile":{"unit":"px","size":0,"sizes":[]},"_background_attachment":"","_background_repeat":"","_background_repeat_tablet":"","_background_repeat_mobile":"","_background_size":"","_background_size_tablet":"","_background_size_mobile":"","_background_bg_width":{"unit":"%","size":100,"sizes":[]},"_background_bg_width_tablet":{"unit":"px","size":"","sizes":[]},"_background_bg_width_mobile":{"unit":"px","size":"","sizes":[]},"_background_video_link":"","_background_video_start":"","_background_video_end":"","_background_play_once":"","_background_play_on_mobile":"","_background_privacy_mode":"","_background_video_fallback":{"url":"","id":"","size":""},"_background_slideshow_gallery":[],"_background_slideshow_loop":"yes","_background_slideshow_slide_duration":5000,"_background_slideshow_slide_transition":"fade","_background_slideshow_transition_duration":500,"_background_slideshow_background_size":"","_background_slideshow_background_size_tablet":"","_background_slideshow_background_size_mobile":"","_background_slideshow_background_position":"","_background_slideshow_background_position_tablet":"","_background_slideshow_background_position_mobile":"","_background_slideshow_lazyload":"","_background_slideshow_ken_burns":"","_background_slideshow_ken_burns_zoom_direction":"in","_background_hover_background":"","_background_hover_color":"","_background_hover_color_stop":{"unit":"%","size":0,"sizes":[]},"_background_hover_color_stop_tablet":{"unit":"%","size":"","sizes":[]},"_background_hover_color_stop_mobile":{"unit":"%","size":"","sizes":[]},"_background_hover_color_b":"#f2295b","_background_hover_color_b_stop":{"unit":"%","size":100,"sizes":[]},"_background_hover_color_b_stop_tablet":{"unit":"%","size":"","sizes":[]},"_background_hover_color_b_stop_mobile":{"unit":"%","size":"","sizes":[]},"_background_hover_gradient_type":"linear","_background_hover_gradient_angle":{"unit":"deg","size":180,"sizes":[]},"_background_hover_gradient_angle_tablet":{"unit":"deg","size":"","sizes":[]},"_background_hover_gradient_angle_mobile":{"unit":"deg","size":"","sizes":[]},"_background_hover_gradient_position":"center center","_background_hover_gradient_position_tablet":"","_background_hover_gradient_position_mobile":"","_background_hover_image":{"url":"","id":"","size":""},"_background_hover_image_tablet":{"url":"","id":"","size":""},"_background_hover_image_mobile":{"url":"","id":"","size":""},"_background_hover_position":"","_background_hover_position_tablet":"","_background_hover_position_mobile":"","_background_hover_xpos":{"unit":"px","size":0,"sizes":[]},"_background_hover_xpos_tablet":{"unit":"px","size":0,"sizes":[]},"_background_hover_xpos_mobile":{"unit":"px","size":0,"sizes":[]},"_background_hover_ypos":{"unit":"px","size":0,"sizes":[]},"_background_hover_ypos_tablet":{"unit":"px","size":0,"sizes":[]},"_background_hover_ypos_mobile":{"unit":"px","size":0,"sizes":[]},"_background_hover_attachment":"","_background_hover_repeat":"","_background_hover_repeat_tablet":"","_background_hover_repeat_mobile":"","_background_hover_size":"","_background_hover_size_tablet":"","_background_hover_size_mobile":"","_background_hover_bg_width":{"unit":"%","size":100,"sizes":[]},"_background_hover_bg_width_tablet":{"unit":"px","size":"","sizes":[]},"_background_hover_bg_width_mobile":{"unit":"px","size":"","sizes":[]},"_background_hover_video_link":"","_background_hover_video_start":"","_background_hover_video_end":"","_background_hover_play_once":"","_background_hover_play_on_mobile":"","_background_hover_privacy_mode":"","_background_hover_video_fallback":{"url":"","id":"","size":""},"_background_hover_slideshow_gallery":[],"_background_hover_slideshow_loop":"yes","_background_hover_slideshow_slide_duration":5000,"_background_hover_slideshow_slide_transition":"fade","_background_hover_slideshow_transition_duration":500,"_background_hover_slideshow_background_size":"","_background_hover_slideshow_background_size_tablet":"","_background_hover_slideshow_background_size_mobile":"","_background_hover_slideshow_background_position":"","_background_hover_slideshow_background_position_tablet":"","_background_hover_slideshow_background_position_mobile":"","_background_hover_slideshow_lazyload":"","_background_hover_slideshow_ken_burns":"","_background_hover_slideshow_ken_burns_zoom_direction":"in","_background_hover_transition":{"unit":"px","size":"","sizes":[]},"_border_border":"","_border_width":{"unit":"px","top":"","right":"","bottom":"","left":"","isLinked":true},"_border_width_tablet":{"unit":"px","top":"","right":"","bottom":"","left":"","isLinked":true},"_border_width_mobile":{"unit":"px","top":"","right":"","bottom":"","left":"","isLinked":true},"_border_color":"","_border_radius":{"unit":"px","top":"","right":"","bottom":"","left":"","isLinked":true},"_border_radius_tablet":{"unit":"px","top":"","right":"","bottom":"","left":"","isLinked":true},"_border_radius_mobile":{"unit":"px","top":"","right":"","bottom":"","left":"","isLinked":true},"_box_shadow_box_shadow_type":"","_box_shadow_box_shadow":{"horizontal":0,"vertical":0,"blur":10,"spread":0,"color":"rgba(0,0,0,0.5)"},"_box_shadow_box_shadow_position":" ","_border_hover_border":"","_border_hover_width":{"unit":"px","top":"","right":"","bottom":"","left":"","isLinked":true},"_border_hover_width_tablet":{"unit":"px","top":"","right":"","bottom":"","left":"","isLinked":true},"_border_hover_width_mobile":{"unit":"px","top":"","right":"","bottom":"","left":"","isLinked":true},"_border_hover_color":"","_border_radius_hover":{"unit":"px","top":"","right":"","bottom":"","left":"","isLinked":true},"_border_radius_hover_tablet":{"unit":"px","top":"","right":"","bottom":"","left":"","isLinked":true},"_border_radius_hover_mobile":{"unit":"px","top":"","right":"","bottom":"","left":"","isLinked":true},"_box_shadow_hover_box_shadow_type":"","_box_shadow_hover_box_shadow":{"horizontal":0,"vertical":0,"blur":10,"spread":0,"color":"rgba(0,0,0,0.5)"},"_box_shadow_hover_box_shadow_position":" ","_border_hover_transition":{"unit":"px","size":"","sizes":[]},"_mask_switch":"","_mask_shape":"circle","_mask_image":{"url":"","id":"","size":""},"_mask_notice":"","_mask_size":"contain","_mask_size_tablet":"","_mask_size_mobile":"","_mask_size_scale":{"unit":"%","size":100,"sizes":[]},"_mask_size_scale_tablet":{"unit":"px","size":"","sizes":[]},"_mask_size_scale_mobile":{"unit":"px","size":"","sizes":[]},"_mask_position":"center center","_mask_position_tablet":"","_mask_position_mobile":"","_mask_position_x":{"unit":"%","size":0,"sizes":[]},"_mask_position_x_tablet":{"unit":"px","size":"","sizes":[]},"_mask_position_x_mobile":{"unit":"px","size":"","sizes":[]},"_mask_position_y":{"unit":"%","size":0,"sizes":[]},"_mask_position_y_tablet":{"unit":"px","size":"","sizes":[]},"_mask_position_y_mobile":{"unit":"px","size":"","sizes":[]},"_mask_repeat":"no-repeat","_mask_repeat_tablet":"","_mask_repeat_mobile":"","hide_desktop":"","hide_tablet":"","hide_mobile":"","_attributes":"","custom_css":""},"defaultEditSettings":{"defaultEditRoute":"content"},"elements":[],"widgetType":"media-carousel","htmlCache":"\t\t\n\t\t\t\t\t\n\t\t\t\n\t\t\t\t\n\t\t\t\t\t\t\t\t\t\t\t\n\t\t\t\t\t\t\t\t\t\n\n\t\t\t\n\t\t\t\t\t\n\t\t\t\t\t\t\t\t\n\t\t\t\t\t\t\t\t\t\t\t\n\t\t\t\t\t\t\t\t\t\n\n\t\t\t\n\t\t\t\t\t\n\t\t\t\t\t\t\t\t\n\t\t\t\t\t\t\t\t\t\t\t\n\t\t\t\t\t\t\t\t\t\n\n\t\t\t\n\t\t\t\t\t\n\t\t\t\t\t\t\t\t\n\t\t\t\t\t\t\t\t\t\t\t\n\t\t\t\t\t\t\t\t\t\n\n\t\t\t\n\t\t\t\t\t\n\t\t\t\t\t\t\t\t\n\t\t\t\t\t\t\t\t\t\n\t\t\t\t\t\t\t\t\t\t\t\t\t\t\t\n\t\t\t\t\t\t\t\t\t\t\t\t\t\t\t\t\n\t\t\t\t\t\t\t\t\t\t\t\t\t\tPrevious\n\t\t\t\t\t\t\n\t\t\t\t\t\t\n\t\t\t\t\t\t\t\t\t\t\t\t\t\tNext\n\t\t\t\t\t\t\n\t\t\t\t\t\t\t\t\t\t\t\t\n\t\t\n\t\t\t\t\n\t\t","editSettings":{"defaultEditRoute":"content","panel":{"activeTab":"content","activeSection":"section_slides"},"activeItemIndex":1}}],"editSettings":{"defaultEditRoute":"layout","panel":{"activeTab":"layout","activeSection":"section_layout_container"}},"htmlCache":null}]}](https://www.jxscmineral.com/wp-content/uploads/2024/09/Tin-Stripping-Solution-And-Tin-Recycling-Equipment-Application-5.jpg)
Our Product/System Features
Our tin stripping solution and tin recycling equipment have a lot of technological advantages that meet the needs of the market.
- The composition parameters of the tin-returning regeneration liquid are stable, and the tin stripping rate and copper bite amount after reuse are similar to that of the purchased sub-liquid phase.
- The exhaust gas tower is set with an automatic adding control device, and the calibration and overhaul of the induction probe at regular intervals, which can effectively prevent the emission of waste gas;
- The storage containers are set with double-layer high-level induction alarms to prevent solution leakage, safe and without hidden danger;
- The regeneration liquid can realize 100% reuse;
- The equipment covers a small area and has a low investment cost.
Working Principle/Process
Tin Recycling Equipment Structures
A typical tin recycling plant consists of the following modules
- Filter unit: For initial removal of impurities.
- Electrolysis tanks: For recovery of tin by deposition using electrolysis.
- Precipitation tank: Recovery of tin by chemical precipitation.
- Recycling system: Recycling of the treated liquid back into the process.
- Wastewater treatment system: To treat the remaining wastewater harmlessly to meet the discharge standards.
Waste Tin Stripping Solution & Tin Recycling Equipmet Working Principle
The main process of the waste tin stripping solution regenerating and tin recycling equipment is to add special precipitants and precipitation aids to the tin waste liquid, and selectively precipitate the metal tin and copper ions in the retreated tin waste liquid. The solid-liquid separation device separates the metal precipitation and the upper layer of the clear liquid, and then obtains the tin sludge and clarified filtrate with a tin content of 30%. The filtrate is adjusted for the composition of the filtrate and its indexes reach the requirements required for retreated tin production and then returned to the tin production line through the automatic control of the addition system. After the filtrate is adjusted to meet the requirements of the tin production line, it is returned to the tin production line through the automatic control adding system, thus realizing the recycling of resources and zero discharge of waste liquid, energy saving, and environmental protection.
Technical Parameters
Model | Waste Liquid Treatment Capacity (tons/month) | Metal Production (tons/month) | Electricity Load (kW) | Occupied Area (m2) |
SN20TB | 5-20 | 0.3-1.2 | 15 | 45 |
SN80TB | 25-80 | 1.5-5 | 30 | 120 |
SN160TB | 80-160 | 5-10 | 50 | 200 |