
Stack High Frequency Fine Screen
Screening Size: 1.92-9.6 m2
Motor Power: 2.2 KW × 2
Screen Layer: 1-5
Screen Material: Polyurethane
Application: Sand washing and recycling, coal washing and dehydration, tailings dry discharge, mud dewatering
Stack High Frequency Fine Screen Overview
The stack high-frequency fine screen is a specialized vibrating screen designed to separate fine and ultra-fine particles from the feed material efficiently. These screens are commonly used in mineral processing, coal preparation, aggregate production, and industrial minerals processing.
5-deck Vibrating Stack Screen
JXSC Mineral is a reputable mining equipment manufacturer, and one of the products we offer is the 5-deck vibrating stack screen.
Here are some features of our 5-deck high-frequency screens:
- The stack vibrating screen adopts the structural design of superposed multi-layer screen boxes, with an effective screening area of 9.6m and five screen box layers. The effective screening width of the single-layer screen box is 1200mm, the effective screening length of the screen machine is 1600mm, and there are two sections of replaceable secondary slurry tanks between the two sections of the screen.
- It adopts high quality, high opening rate, anti-blocking, and wear-resistant polyurethane screen. It uses a special ore distributor to divert the flow and feed the ore feeder so that the material can be evenly spread on the screen surface while ensuring large output, thereby Reducing the impact of the slurry on the screen due to excessive flow speed and increasing the service life of the screen. The average life is not less than six months.
- Equipped with vibration motors with low energy consumption, high efficiency, stable and reliable performance. The motor installation uses patented thread anti-loosening technology to prevent loosening and ensure the reliability of the vibration source.
- Multiple channels are connected in parallel and occupy a small space. The five decks of the vibrating screen are superimposed layers, equivalent to merging the floor space of five screen machines into the floor space of one screen machine, making the entire vibrating screen more compact and increasing the flexibility of installation at the production site.
- All slurry-passing parts inside the screen box are lined with a high-wear-resistant particular rubber layer, which is highly bonded to the box’s surface and does not fall off, effectively avoiding wear and tear on the screen box from quicksand. The exterior of the screen box is all made of polyurethane spraying technology, with a spray thickness of 1.2-2mm, which greatly improves the wear and corrosion resistance of the screen box. The screen box plates are made of low-alloy, high-strength structural steel and produced using CNC cutting. The overall heat treatment of the screen box eliminates Stress, avoids secondary deformation of the screen box, and effectively extends the life of the equipment.
Advantages
Stack High Frequency Fine Screen Advantages
- High operating frequency
The operating frequency of high-frequency laminated vibrating screens is usually above thousands of times per minute (Hz), which means that its vibrations are faster and more efficient and can better separate fine particles. - High screening efficiency
Due to the effect of high-frequency vibration, the particles move quickly on the screen, thereby improving the screening efficiency. It is beneficial for handling fine granular and powdery materials. - High screening accuracy
High-frequency vibrations pass through the screen more efficiently, so higher screening accuracy is achieved, and a smaller particle size range is separated. - Multi-layer screening
Like traditional laminated vibrating screens, high-frequency laminated vibrating screens usually have multi-layer screens, allowing particles to be screened multiple times simultaneously, further improving screening efficiency and accuracy. - Wide applicability
High-frequency laminated vibrating screens can be used in various fields, including mining, metallurgy, building materials, food processing, medicine, etc., for screening, grading, impurity removal, and other applications.
Structures & Working Principle
Stack High Frequency Fine Screen Structure
The high-frequency sizing screen mainly consists of a linear vibrator, upper screen box, feeding box, fixed frame, lower screen basket, high-frequency vibration system, upper and lower screen material collection funnels, shear springs, etc.
Stack High Frequency Fine Screen Working Principle
The high-frequency vibrating sizer is driven by two electric vibrators with opposite movement directions to drive the screen frame in a straight line. The resultant force of the two electric vibrators acting on the screen frame passes through the center of gravity of the screen frame. Therefore, the exciting force at each point on the screen frame is the same. The slurry is fed from the upper or lower part of the ore separator and evenly divided into multiple channels through the ore separator. Then it enters multiple ore feeders through the ore feeding hose. The ore feeder sprinkles the slurry evenly on the upper end of the screen surface. Due to the continuous vibration of high frequency and small amplitude, the materials on the screen surface make a continuous jump on the inclined screen surface to disperse the materials. In the process of mixing, the fine-grained materials pass through the screen hole and are called the products under the screen, while the materials larger than the screen hole make a continuous forward jump on the inclined screen surface, and finally jump out of the screen to become the products on the screen. High frequency and small amplitude vibration can destroy the surface tension of pulp and the adhesion of fine particles to coarse particles, making materials loose and layered. The screen surface adopts a polyurethane screen, with a high opening rate and good screening permeability, which can reduce and prevent screen hole blockage and improve screening efficiency.
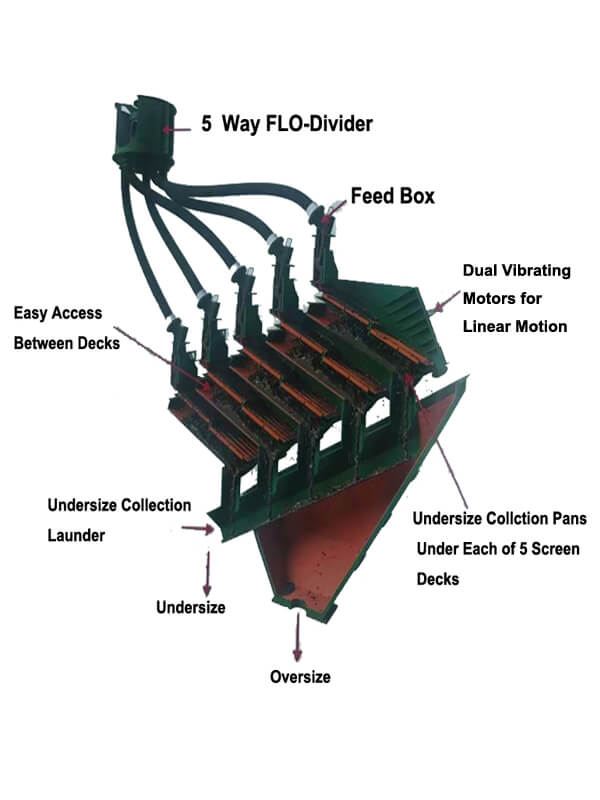
Technical Parameters
Model | Screening Size (m2) | Layer | Vibration Amplitude (mm) | Feeding Density (%) | Motor Power (kw) | Rotating Speed (r/m) | Lateral Slope (°) |
1216-1 | 1.92 | 1 | 1.33-2.61 | 30-40 | 2.2kw*2 | 1500 | 20 |
1216-2 | 3.84 | 2 | |||||
1216-3 | 5.76 | 3 | |||||
1216-5 | 9.6 | 5 |