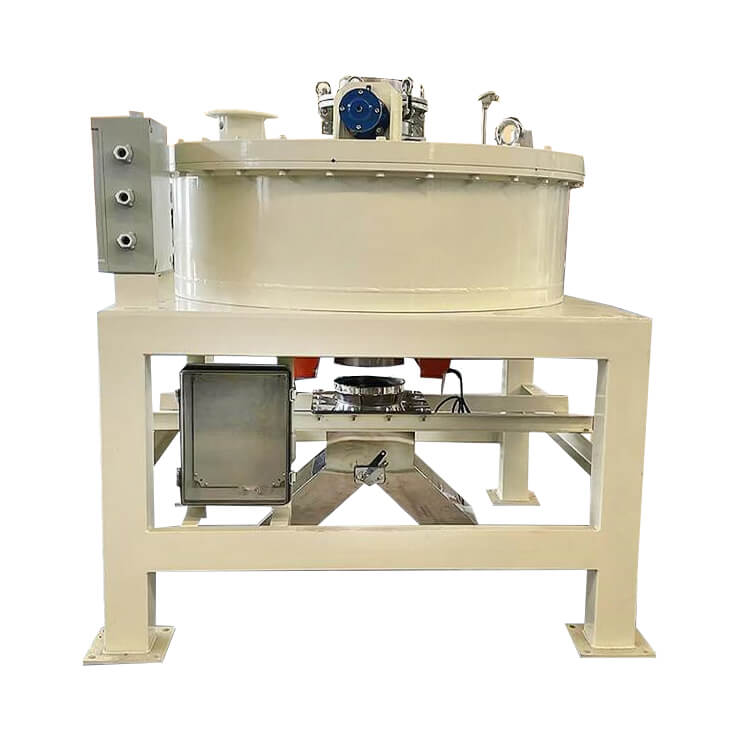
Slurry Magnetic Separator
Capacity: 10-100 m3/h
Feeding Material Density: 10-30%
Power: 90-178 kW
Application: Ceramics, mining, chemical industry, electronics, food and other industries.
Slurry Magnetic Separator Overview
The slurry magnetic separator is a kind of equipment widely used in mining, metallurgy, environmental protection, and other fields. It is mainly used to separate and extract magnetic substances. Its working principle is mainly based on the adsorption effect of magnetic fields on magnetic substances.
Application Range
The slurry magnetic separator is widely used in the removal and separation of iron impurities and magnetic substances in slurries. It glazes in ceramics, glass, chemicals, electronics, food, medicine, and other industries.
Features
- Unique material reverse pressure flow direction design, so the larger the specific gravity of iron, the easier to remove.
- The design of the pressure flow direction makes iron adsorbed and self-resistant, and it is easier to be left in the magnetic field.
- The back-flushing type automatic iron-unloading system is designed so that the iron can be more easily, quickly, and thoroughly discharged to the machine body.
- The equipment comes with an automatic water storage system, through the intelligent system’s accurate control, realizes the minimum water consumption, more energy saving, and environmental protection.
- In particular in the food and drug industry, the material contact part is made of food-grade stainless steel, so as to avoid secondary pollution.
- The equipment welding adopts high-tech non-filling cold welding technology and high-light treatment of the inner wall. Avoid material residue and wall hanging phenomenon.
Advantages
Slurry Magnetic Separator Advantages
- The magnetic field of the slurry machine is high, the magnetic field is evenly distributed, and the iron removal effect is obvious;
- The cooling system uses internal oil circulation, and external water-oil heat exchange is carried out through a heat exchanger. The heat dissipation coefficient is high, which can control the temperature rise at around 20C, extending the service life of the electromagnetic wire;
- The brake valve is made of imported materials, the valve body is strong and durable, and there is no residual slurry overflowing after closing;
- Iron removal uses high-pressure water spring flushing and air blowing to ensure thorough flushing and no residue;
- The mesh is made of special materials. After the power supply to the excitation coil is cut off, there is no residual magnetism, making it easy to remove iron;
- Fully automatic operation, no manual supervision is required, iron removal is convenient and fast, and there is no residue.
Structures & Working Principle
Slurry Magnetic Separator Structure
The slurry magnetic separator is mainly composed of a magnetic system, tank body, transmission device, ore feeding device, flushing device, and other parts. Among them, the magnetic system is the core part of the device and is responsible for generating the magnetic field. The tank is used to accommodate the slurry to be processed and achieve separation of magnetic substances through the action of a magnetic field.
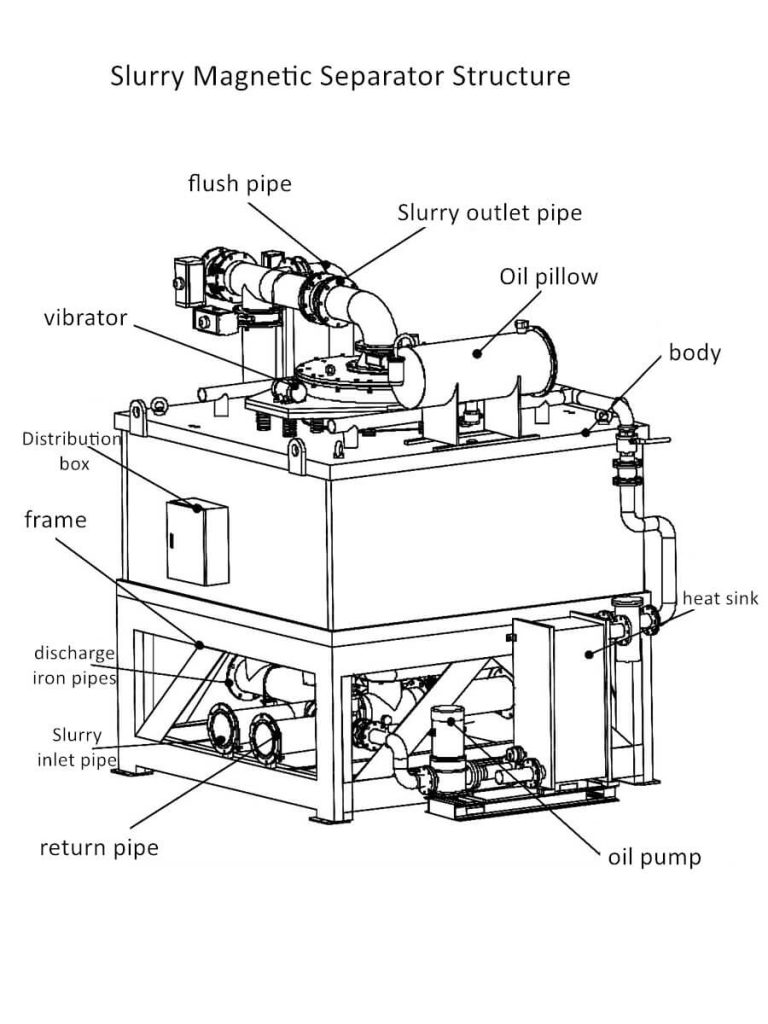
Slurry Magnetic Separator Working Principle
During the working process, the electromagnetic slurry magnetic separator will form a stable magnetic field. When the slurry containing magnetic substances enters the magnetic field area, it is affected by the force of the magnetic field, and the magnetic substances are adsorbed on the surface of the magnetic system. Non-magnetic materials, on the other hand, will continue to flow along the tank because they are not affected by the magnetic field force, thereby achieving the separation of magnetic materials and non-magnetic materials.
The magnetic system usually consists of electromagnets and magnetic poles. Electromagnets generate magnetic fields through electric current, and the magnetic poles determine the distribution and intensity of the magnetic field. By adjusting the size and direction of the current, the strength and distribution of the magnetic field can be controlled to meet different separation needs.
Technical Parameters
Model | ZT-YL600-Q | ZT-YL800-Q | ZT-YL1000-Q | ZT-YL1000-T | ZT-YL1000L-Q | ZT-YL1200-Q | ZT-YL1200L-Q |
Input Voltage (ACV) | 380 | 380 | 380 | 380 | 380 | 380 | 380 |
Power (kW) | 90 | 120 | 150 | 140 | 150 | 178 | 178 |
Magnetic Field Strength (GS) | 18000 | 18000 | 18000 | 15000 | 18000 | 15000 | 15000 |
Capacity (m3/h) | 10-40 | 15-50 | 20-75 | 20-75 | 20-75 | 25-100 | 25-100 |
Kaolin Feed Concentration | 10-20% | 10-20% | 10-20% | 10-20% | 10-20% | 10-20% | 10-20% |
Potassium, Albite Ore Concentration | 20-30% | 20-30% | 20-30% | 20-30% | 20-30% | 20-30% | 20-30% |
Weight (T) | 15 | 23 | 32 | 28 | 43 | 45 | 53 |
Output Voltage (DCV) | 0-530 | 0-530 | 0-530 | 0-530 | 0-530 | 0-530 | 0-530 |
Output Current (DCA) | 0-160 | 0-210 | 0-285 | 0-285 | 0-285 | 0-330 | 0-330 |
Cooling Method | Oil and Water Double Cooling | Oil and Water Double Cooling | Oil and Water Double Cooling | Oil and Water Double Cooling | Oil and Water Double Cooling | Oil and Water Double Cooling | Oil and Water Double Cooling |
Coil Power (kW) | 80 | 110 | 132 | 120 | 130 | 160 | 160 |
Cavity Height (mm) | 700 | 700 | 700 | 800 | 600 | 800 | 700 |
Coil Material | Copper | Copper | Copper | Copper | Aluminum | Copper | Aluminum |
Installation Size (mm) | 1550*1550*3200 | 1980*1980*3200 | 2300*2300*3200 | 2130*2130*3300 | 2600*2600*3800 | 2600*2600*3300 | 2800*2800*3800 |