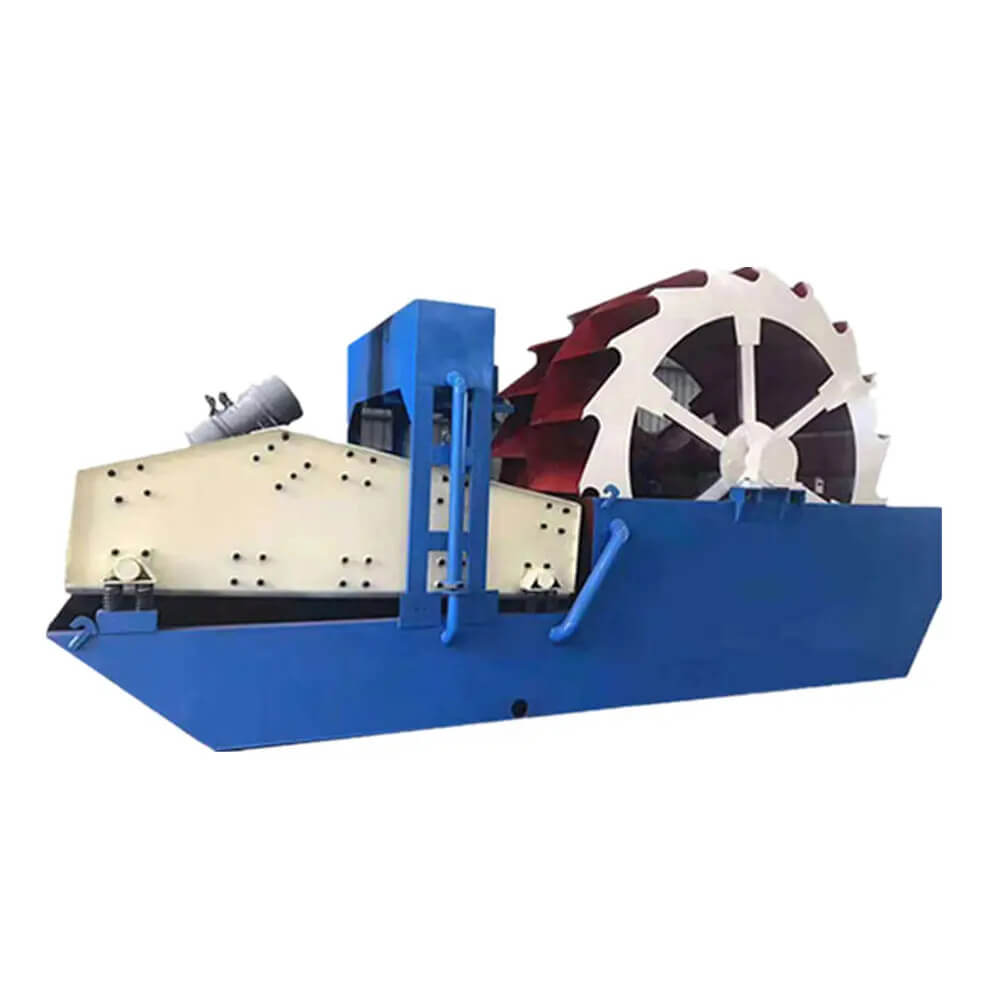
Sand Washing And Recycling Machine
Applicable Materials: River pebbles, granite, limestone, basalt, coal gangue, river sand, and other materials.
Application: Sandpits, mines, construction sites, highways, road and bridge construction, concrete mixing stations, water conservancy & hydropower, chemical industry, and other industries.
Applicable Production Line: River pebble sand making, granite splitting and crushing to make sand, limestone crushing and grinding, basalt crushing and sand-making, coal gangue crushing and sand-making, and other material production lines.
Sand Washing And Recycling Machine Overview
The sand washing and recycling machine integrate sand washing, concentrated dehydration of coarse and fine sand, and fine sand recovery. So it is also called a sand washing and recycling integrated machine, fine sand recovery & dehydration machine, mud and sand washing and separation equipment. The equipment cleverly connects the fine sand recovery machine and the sand washing machine. It has a reasonable structure, occupies a small area, and the investment cost is lower than the price of the two pieces of equipment.
The integrated sand washing and recycling machine is usually used behind the circular vibrating screen or drum sieve. The sieved mixture of sand, water, and mud enters the feeding end of the integrated sand-washing and recycling machine through the chute. It cleans the sand, dehydration and desliming and output cleaning sand. The finished sand has a water content of 15% and a mud content of less than 3%. The sand product specification is medium sand.
The sand washing and recycling equipment is composed of a sand washing part and a fine sand recovery part.
- The sand washing part has the same function as the general wheel sand washing machine, and is used for sand washing, dehydration, and desliming;
- The recovery part can be combined arbitrarily according to customer needs. If fine sand recovery is required, it can be connected to a general fine sand recovery system. If fine sand dehydration recovery is required, it can be connected to a dewatering fine sand recovery machine. If different sand production effects are required, a multi-layer dewatering screen can also be configured.
Advantages
Sand Washing And Recycling Machine Advantages
- Combining the characteristics and advantages of the sand washing machine and the fine sand recovery machine, it has the functions of sand washing, fine sand dehydration and recovery.
- It is cleaner than traditional sand washing machines, and the price of sand is better.
- Reasonable structure, small footprint, and simple installation
- Lower investment cost than the price of two pieces of equipment.
- The all-in-one machine has higher working efficiency and low energy consumption.
- Energy saving and environmental protection.
- Long service life and low maintenance cost.
- Special models can be tailored according to different needs.
Structures & Working Principle
Sand Washing And Recycling Machine Structure
The sand washing and recycling machine is composed of a high-pressure separator, dehydration screen, impeller separator, reducer, high-pressure vacuum pump, cleaning tank, high-level return water tank, motor, vibration motor, and other components.
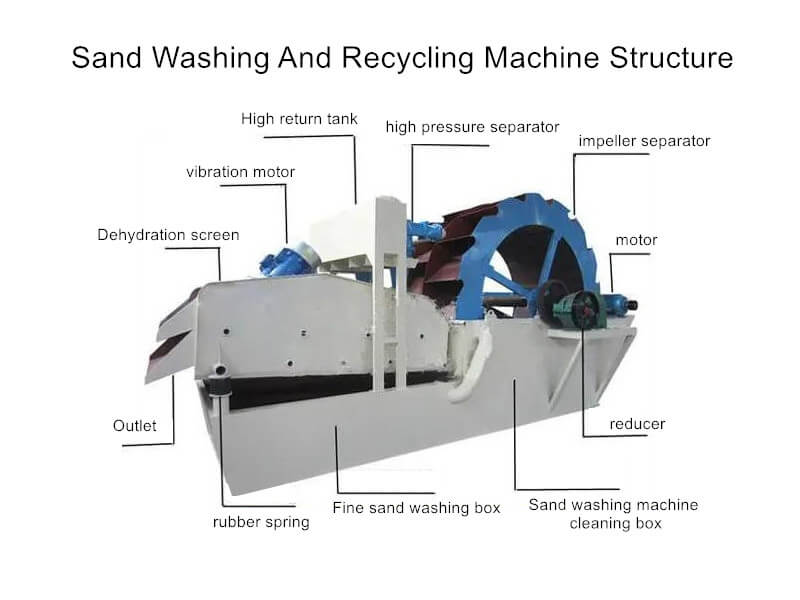
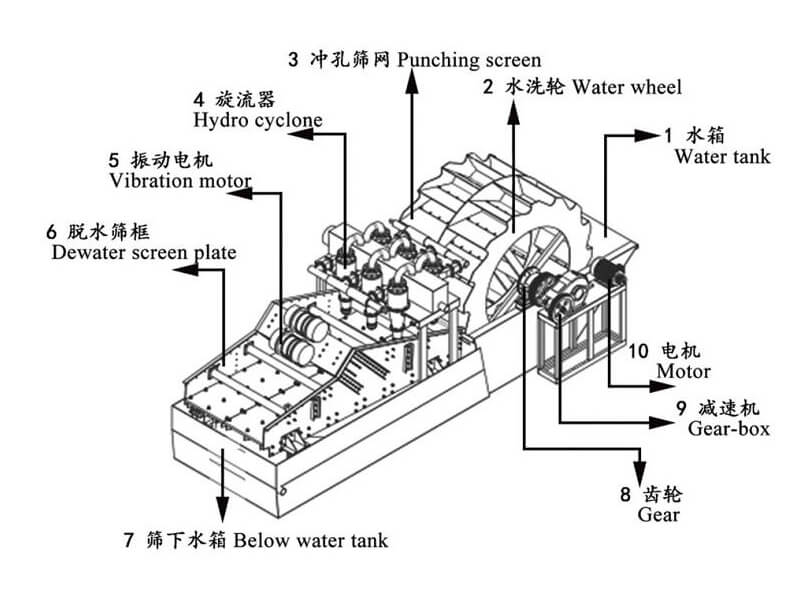
Sand Washing And Recycling Machine Working Principle
The mixture of sand and water enters the cleaning tank and is cleaned by the impeller separator, separating the sand and mud. It is transported to the high-pressure separator by a high-pressure vacuum pump. The fine sand concentrated by centrifugal classification is discharged into the upper layer of the dewatering screen through the sand settling nozzle for dehydration treatment. The remaining waste water, mud, dust, and other impurities are passed through the overflow port of the high-pressure separator, discharged into the high-return tank, and then removed. Coarse sand is produced from the upper layer, and fine sand is produced from the lower layer or mixed with coarse and fine sand (can be adjusted according to requirements).
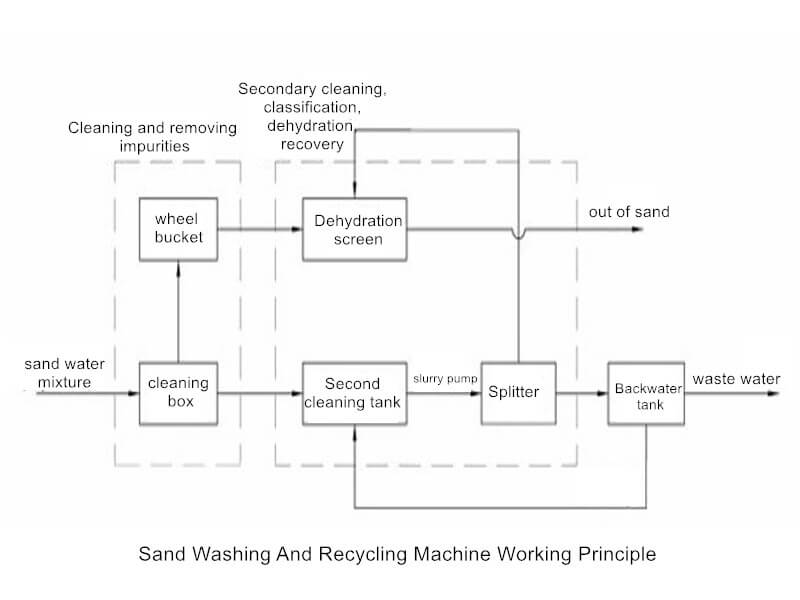
Technical Parameters
Model | Capacity(T/H) | Motor Power(Kw) |
2208 | 15-40 | 8P 4Kw |
2611 | 20-54 | 8P 5.5Kw |
2914 | 50-100 | 8P 7.5Kw |
3020 | 80-200 | 8P 11Kw |
3121 | 90-260 | 8P 11Kw |