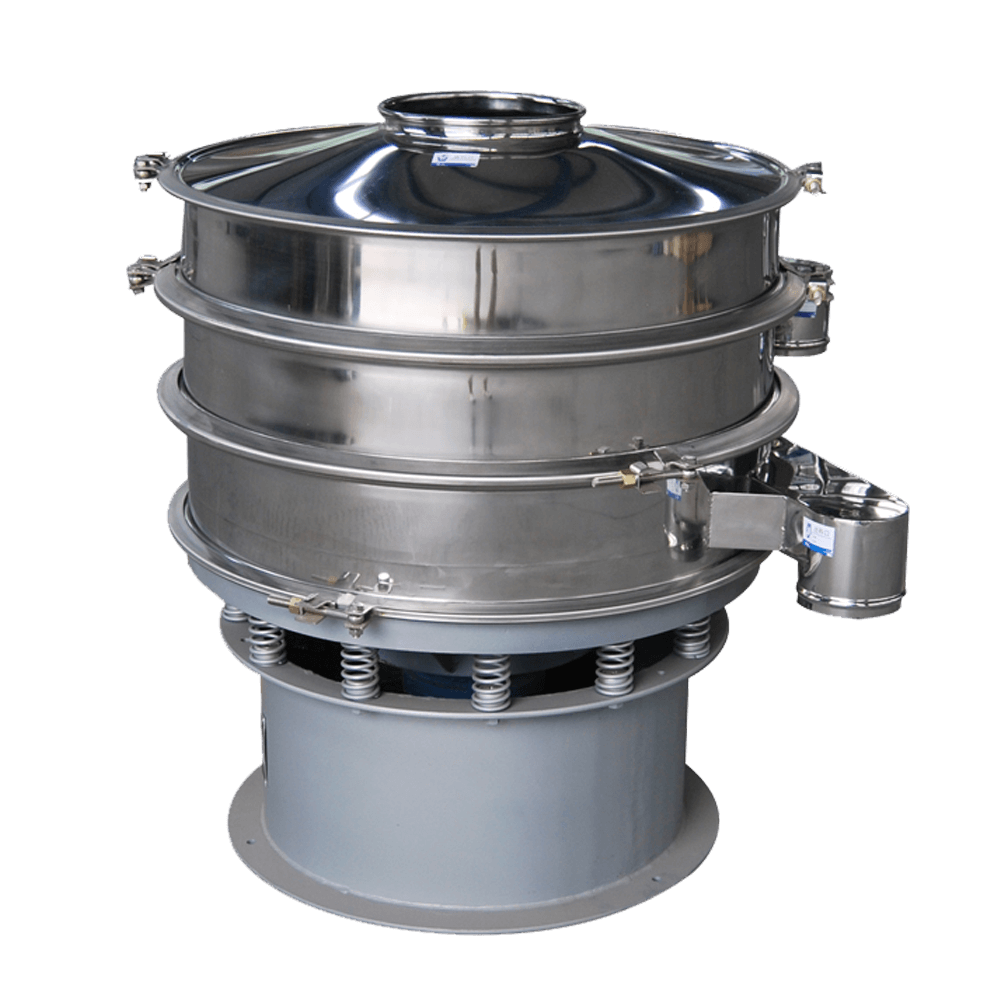
Rotary Vibration Screen
Screening Size: 0.2281-2.7922 m2
Motor Power: 0.55kW-3.7kW
Screen Layer: 1-5 available
Screen Mesh: 2-500 mesh
Applications: Food, ceramic, chemical, pharmaceutical industry, metallurgy, pollution abatement, etc.,
Rotary Vibrating Screen Overview
The rotary vibrating screen is a vibrating screening equipment with high screening fineness and large processing capacity. It can achieve satisfactory screening results for particles, fine powders, and liquids.
Application Range
1. Abrasive & Ceramics: alumina, quartz sand, mud, spray soil particles.
2. Chemical: resin sand, pigment, washing powder, micro powder, paint, soda ash, lemon powder, rubber, and plastics.
3. Food: sugar, salt, soda, MSG (monosodium glutamate), milk powder, soybean milk, yeast, juice, soy sauce, vinegar, etc.
4. Paper Making: coating, coated slurry, black-and-white liquid, waste liquor, papermaking liquid, wastewater recycling.
5. Metallurgy: titanium oxide, zinc oxide, electromagnetic materials, metal powder, welding rod powder, titanium oxide, etc.
6. Pharmaceutical: TCM (traditional Chinese medicine) powder, TCM liquid, western medical powder, western medical liquid, TCM & western medical particles, etc.
7. Environment Protection: rubbish, excrement, waste oil, food effluent, wastewater processing, etc.
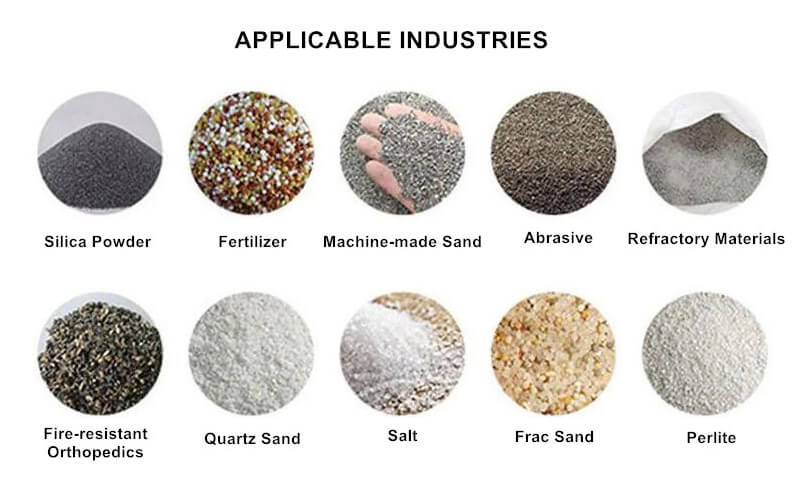
The rotary vibration screen vibrates in a circular motion, with adjustable amplitude, long material screening flow line, multi-layer screening, clear screening of each specification, and high screening efficiency. It is suitable for screening in the mining and sand and gravel industries.
Benefits
- Fine filter In the rotary vibrating screen, the sieve cloth is a stainless steel wire woven mesh, and the smallest can reach 600 mesh (0.02mm). The counterweight rapid adjustment system can control and adjust the material movement on the sieve cloth, and maintain a long screening time to complete the fine screen.
- High throughput Horizontal, inclined, vertical 3D vibratory motion for higher vibrations and 3 times higher throughput through precise screening allows throughputs from 100 to 5,000 kg/h depending on the product, mesh size, and machine feed flow.
- No dust pollution The rotary vibrating screen can be used with a hose to fully seal without dust, floating powder, and liquid splashing. It is very suitable for sanitary production lines and dust-free workshops, and it is also very helpful to protect the health of your employees.
- Good adaptability The height of the machine can be specially customized according to customer requirements. The discharge port can be placed 360 degrees, which is convenient for other equipment in the production line.
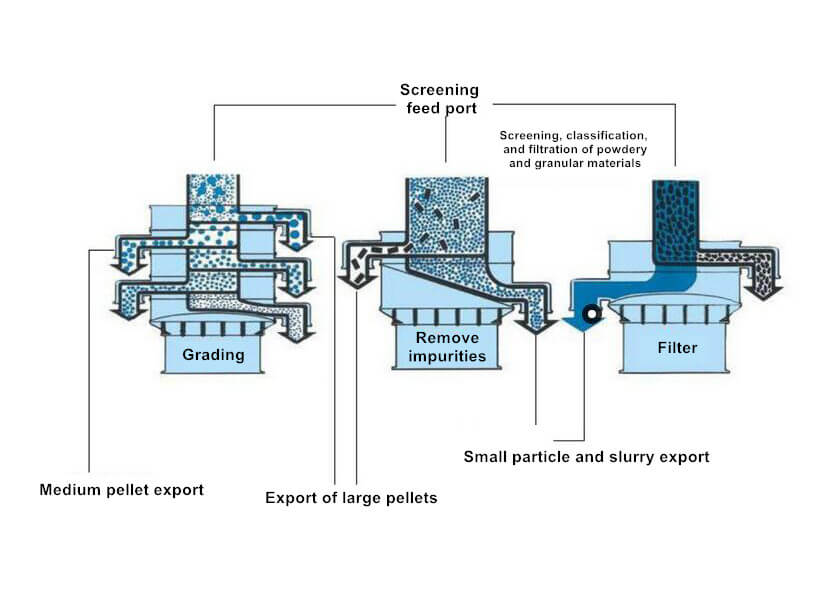
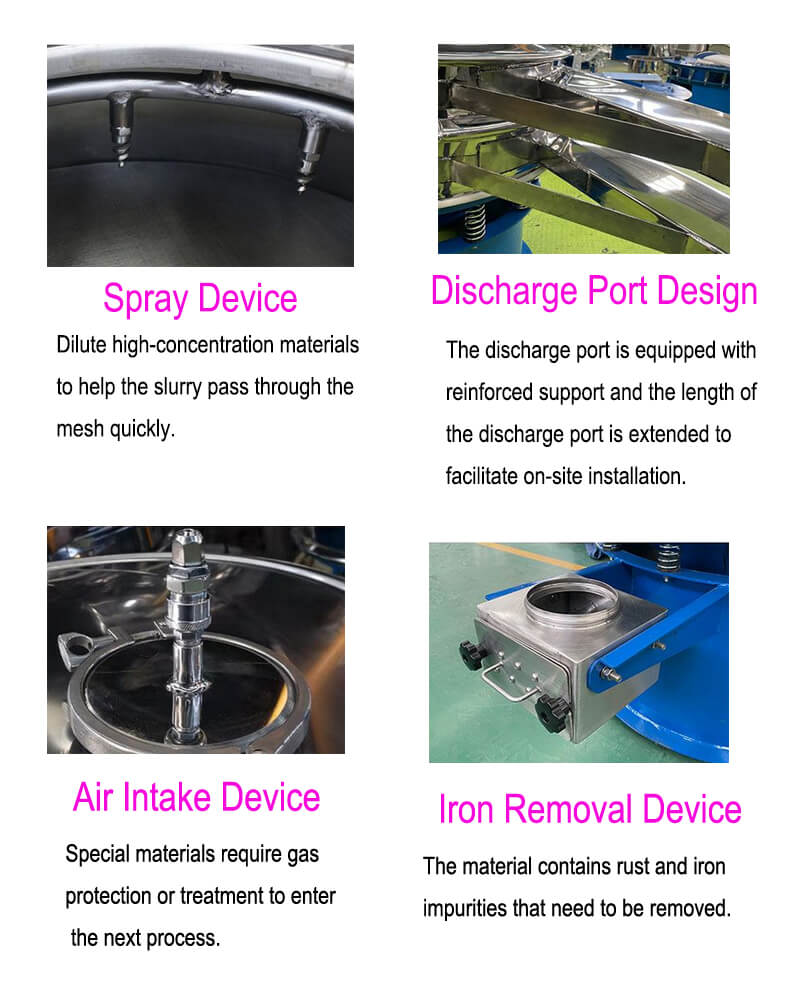
Rotary Vibration Screen Details
- Spray Device Dilute high-concentration materials to help the slurry pass through the mesh quickly.
- Discharge Port Design The discharge port is equipped with reinforced support, and the length of the discharge port is extended to facilitate on-site installation.
- Air Intake Device Special materials require gas protection or treatment to enter the next process.
- Iron Removal Device The material contains rust and iron impurities that need to be removed.
Advantages
Rotary Vibrating Screen Advantages
- Fully sealed design, the working environment is clean and pollution-free;
- Automatic screening, automatic discharge, high efficiency;
- The body is modular in design and can be used in one or more layers;
- The screen can be replaced at will according to the requirements, and the screening granularity can be easily changed;
- The discharge port can be rotated 360° to facilitate production layout.
Structures & Working Principle
Rotary Vibration Screen Structure
Rotary vibrating screen mainly includes mesh cleaning systems, damping spring, beam ring, vibration motor, seal, etc.
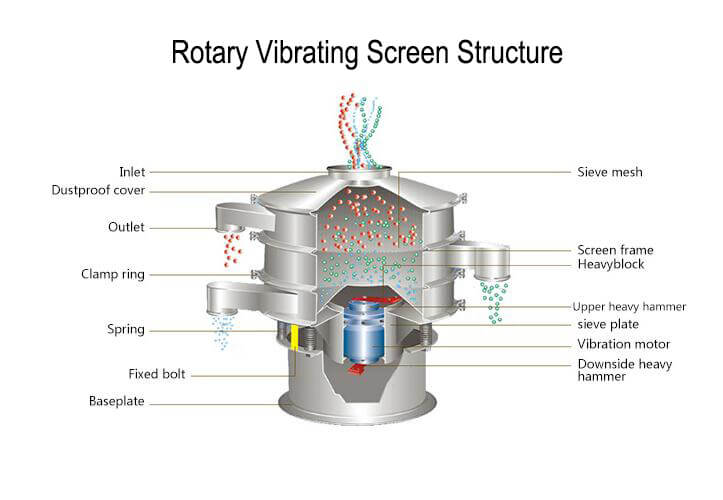
Rotary Vibration Screen Working Principle
The rotary vibrating screen uses a vertical vibration motor as the exciter. The upper and lower ends of the vibration motor are equipped with eccentric weights, which convert the rotational motion of the vibration motor into horizontal, vertical, and tilted three-dimensional motion and then transfer this motion to the Screen surface. Adjusting the phase angles of the upper and lower ends can change the movement trajectory of the material on the screen surface.
Technical Parameters
Model | Screen Size(m2) | Layer | Screen Diameter(mm) | Screen Mesh (mesh) | Motor Power(kw) | |
Vibration Motor | Ordinary Motor | |||||
600 | 0.2281 | 1-5 | 1-25 | Ⴔ540 | 0.55 | 0.75 |
800 | 0.4183 | 1-5 | 1-25 | Ⴔ730 | 0.75 | 1.1 |
1000 | 0.6359 | 1-5 | 1-25 | Ⴔ900 | 1.1 | 1.5 |
1200 | 0.9499 | 1-5 | 1-25 | Ⴔ1100 | 1.5 | 1.5 |
1500 | 1.5386 | 1-5 | 5-40 | Ⴔ1400 | 2.2 | 2.2 |
1800 | 2.2687 | 1-3 | 5-40 | Ⴔ1700 | 3.0 | 2.2 |
2000 | 2.7922 | 1-3 | 1-40 | Ⴔ1886 | 3.7 | 3.0 |