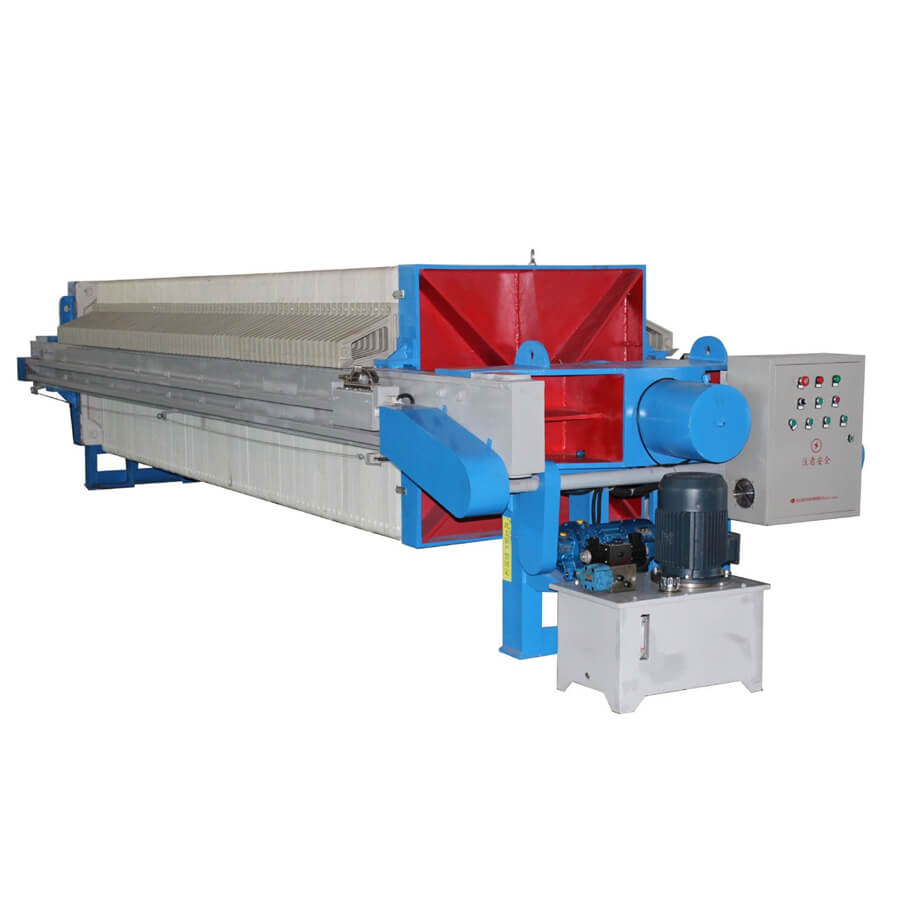
Plate And Frame Filter Press
Filter Chamber Volume: 0.24-7.96 m3
Filter Areas: 20-500 m2
Filter Plates: 20-128 pcs
Power: 2.2-5.5 kw
Application: Widely used in chemical, pharmaceutical, metallurgy, dyestuff, food, brewing, ceramics, and environmental protection industries.
Plate And Frame Filter Press Overview
The plate and frame filter press is a common solid-liquid separation equipment that can handle different suspensions, such as wastewater treatment in chemical, food, and pharmaceutical industries, filtration of solid particles, etc.
The plate and frame filter press is a relatively traditional filter press with a simple structure and easy operation and is suitable for various types of sludge dehydration. The advantage of the plate and frame filter press is that it has a large filtering area and can adapt to large-flow sewage treatment needs. In addition, due to its simple structure, it is also easier to maintain. However, the disadvantage of the plate and frame filter press is that its filtration effect is greatly affected by the plate and frame material and process parameters, and it requires manual loading, unloading, and cleaning, which is highly labor-intensive.
The main part of the plate and frame filter press is a set of filter chambers consisting of filter plates and filter frames in alternating order. When working, the slurry will be transferred by the feeding pump from the feeding hole on the thrust plate to all chambers, under the pressure of the feeding pump, solid particles in the slurry will be trapped in the filter chambers and form into filter cakes slowly, liquid throughout the filter clothes and come out of outlet holes. Solid and liquid will finally be separated after one filtration cycle.
Plate And Frame Filter Press Features
- High-quality Materials
The main beam of the filter press is made of selected high-quality steel with a high safety factor, and the surface has been treated with anti-rust and anti-corrosion treatment.
- Easy to Use
The control system adopts PLC control, and the operating parameters of each stage can be input on the touch screen. They can realize fault self-diagnosis, display the fault location, and have alarm sound and light signal output.
- Reasonable Design
It has low power consumption, large processing capacity, good separation performance, high dehydration efficiency, a high solid content rate of mud cake, and a wide application range.
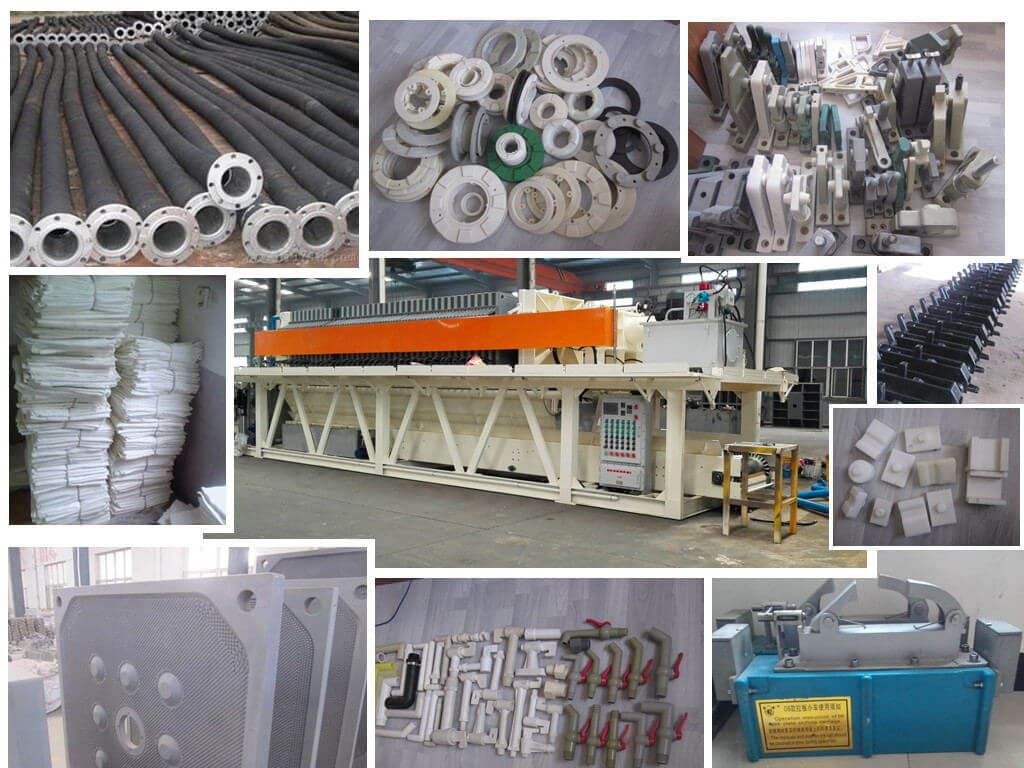
Applications of Plate And Frame Filter Press
- Mining and Mineral Processing
Plate and frame filter presses are used in the mining and mineral processing to filter out solids from slurries, such as coal, iron ore, and precious metals.
- Wastewater Treatment
Plate and frame filter presses are commonly used in wastewater treatment plants to remove solids and impurities before they are discharged into the environment.
- Chemical Processing
Plate and frame filter presses are used in the chemical industry to separate solids from liquids in various chemical processing applications.
- Food and Beverage Processing
The food and beverage industry uses plate and frame filter presses to clarify liquids, remove impurities, and separate solids from liquids in products such as juices, beer, and wine.
- Pharmaceuticals
Plate and frame filter presses are used in the pharmaceutical industry for the filtration of APIs, as well as other intermediate and final products.
Advantages
Plate And Frame Filter Press Advantages
- High Efficiency
Plate and frame filter press can complete the filtration and solid-liquid separation process in a relatively short time, thereby improving production efficiency. - Easy Operation
Operating the plate and frame filter press is relatively simple, requiring only basic settings and controls to achieve automated filtration operations. - Wide Applicability
Plate and frame filter press is suitable for various solid-liquid separation processes and can handle different types of suspensions, such as wastewater treatment in chemical, food, pharmaceutical industries, and filtration of solid particles, etc. - Good Filtration Effect
Plate and frame filter press uses multiple layers of filter plates and filter cloths for filtration, resulting in a good filtration effect and achieving high solid-liquid separation efficiency. - Energy Saving and Environmental Protection
Compared to other solid-liquid separation equipment, plate and frame filter press consumes less energy during operation, reducing energy costs, and also reducing waste and pollutant emissions, meeting energy-saving and environmental protection requirements. - Low Maintenance Cost
Plate and frame filter press has relatively low maintenance costs, usually only requiring regular cleaning and replacement of consumable parts such as filter cloths, making maintenance relatively simple. - High Operational Flexibility
Plate and frame filter press can be adjusted and optimized according to different process requirements, with high operational flexibility to meet the needs of different production scenarios.
Structures & Working Principle
Plate and Frame Filter Press Structure
The plate and frame filter press is a kind of separation equipment widely used in industrial production. Its main structure and components are as follows:
- Filter Plates: These are the main components of the filter press. They are flat, rectangular plates with a central hole, often with filter cloths attached.
- Filter Frames: Frames surround the filter plates and provide support. They also have a central hole that aligns with the hole in the filter plates.
- Hydraulic System: Many modern plate and frame filter presses use a hydraulic system to apply pressure to the plates, squeezing the filter cake between them for better filtration.
- Feed Inlet: The slurry or suspension to be filtered is pumped into the filter press through a feed inlet.
- Filtrate Outlet: The liquid filtrate passes through the filter cloth and filter plates and exits the press through a filtrate outlet.
- Cake Discharge: Once the filtration process is complete, the solid cake formed between the plates is removed manually or using automated cake discharge systems.
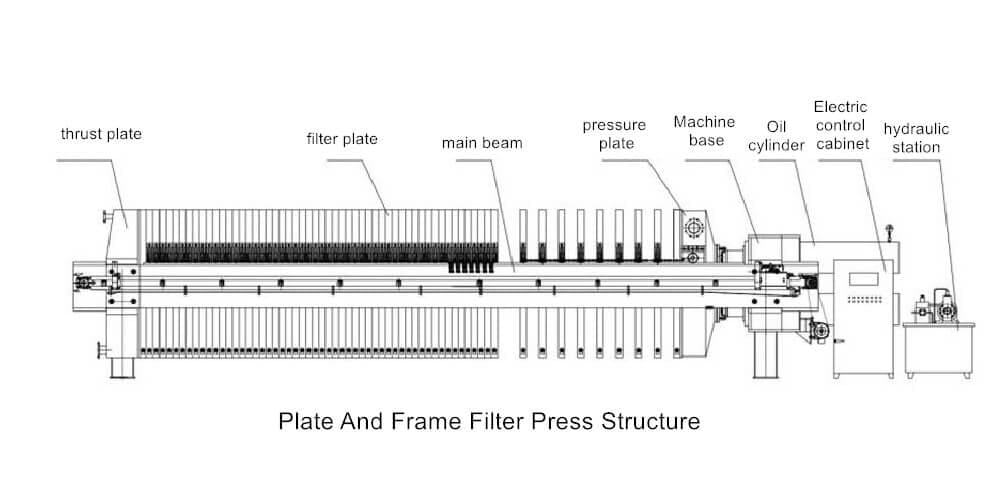
Plate and Frame Filter Press Working Principle
The working principle of plate and frame filter press mainly includes the following steps:
- Filling: The slurry or suspension is pumped into the filter press through the feed inlet. The filter press is initially open, allowing the slurry to flow into the space between the filter plates.
- Filtration: Once the filter press is filled, it is closed by applying hydraulic pressure. This pressure pushes the filter plates and frames together, compressing the slurry and forcing the liquid component to pass through the filter cloth while retaining the solid particles as a cake.
- Dewatering: As the filtrate passes through the filter cloth, the solid particles accumulate on the surface, forming a cake. The hydraulic pressure is maintained for a certain period to ensure thorough dewatering.
- Cake Discharge: After dewatering, the filter press is opened, and the solid cake is removed from between the filter plates. This can be done manually or using automated systems, depending on the design of the filter press.
- Rinse and Repeat: The process is repeated for the next slurry batch, with the filter press being cleaned if necessary between cycles.
Overall, the plate and frame filter press applies pressure to a slurry or suspension to separate the solid particles from the liquid component, resulting in a dewatered solid cake and a clarified liquid filtrate.
Technical Parameters
Model | Filter Area (m2) | Filter Plates Number (pcs) | Dimensions of The Filter Plate (mm) | Cake Thickness (mm) | Filter Chamber Volume (m3) | Filter Pressure (Mpa) | Foundation Center (mm) | Dimensions (L x W x H) (mm) | Motor Power (kw) | Overall Weight (kg) |
XMAZ800U | 20 | 20 | 800 x 800 x 55 | 25 | 0.24 | 0.5 | 2265 | 3215 x 1320 x 1160 | 2.2 | 2073 |
30 | 30 | 0.37 | 0.8 | 2815 | 3765 x 1320 x 1160 | 3090 | ||||
40 | 40 | 0.49 | 0.8 | 3365 | 4315 x 1320 x 1160 | 3380 | ||||
50 | 50 | 0.62 | 1 | 3915 | 4865 x 1320 x 1160 | 3090 | ||||
60 | 60 | 0.74 | 4465 | 5415 x 1320 x 1160 | 4070 | |||||
70 | 70 | 0.87 | 1.6 | 5015 | 5965 x 1320 x 1160 | 4360 | ||||
80 | 80 | 1 | 5565 | 6515 x 1320 x 1160 | 4700 | |||||
XMAZ1000U | 100 | 62 | 1000 x 1000 x 60 | 30 | 1.48 | 0.5-1.6 | 5020 | 6110 x 1460 x 1360 | 3 | 6200 |
120 | 75 | 1.8 | 5800 | 6890 x 1460 x 1360 | 6710 | |||||
XMAZ1250U | 150 | 58 | 1250 x 1250 x 65 | 2.26 | 5390 | 6920 x 1850 x 1620 | 11800 | |||
180 | 69 | 2.7 | 6100 | 7630 x 1850 x 1620 | 12700 | |||||
200 | 79 | 3.02 | 6620 | 8150 x 1850 x 1620 | 13300 | |||||
220 | 84 | 3.29 | 7080 | 8610 x 1850 x 1620 | 13900 | |||||
250 | 95 | 3.73 | 7290 | 9320 x 1850 x 1620 | 14800 | |||||
XMAZ1500U | 300 | 77 | 1500 x 1500 x 70 | 32 | 4.76 | 0.7-1.6 | 7450 | 9100 x 1960 x 1780 | 5.5 | 27000 |
320 | 83 | 5.14 | 7870 | 9520 x 1960 x 1780 | 27690 | |||||
340 | 88 | 5.45 | 8220 | 9870 x 1960 x 1780 | 28380 | |||||
350 | 90 | 5.58 | 8360 | 10010 x 1960 x 1780 | 28730 | |||||
380 | 98 | 6.08 | 8920 | 10570 x 1960 x 1780 | 29760 | |||||
400 | 103 | 6.39 | 9270 | 10920 x 1960 x 1780 | 30450 | |||||
150 | 116 | 7.21 | 10180 | 11830 x 1960 x 1780 | 32170 | |||||
500 | 128 | 7.96 | 11020 | 12670 x 1960 x 1780 | 33890 |