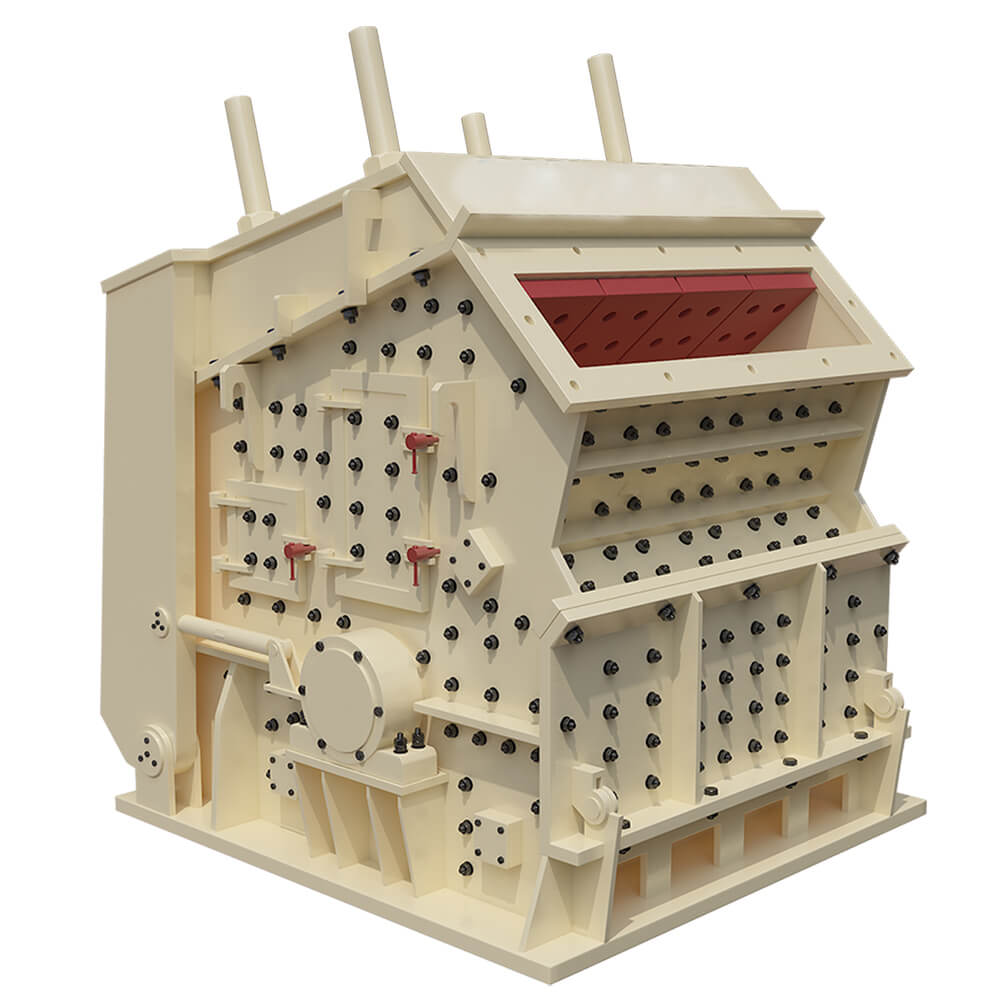
Impact Crusher
Capacity: 30-500 tph
Feeding Size: <700 mm
Process Material: A variety of medium hardness ores, such as limestone, feldspar, calcite, talc, barite, rare earth, clay, kaolin, dolomite, kaolin, gypsum, graphite, etc.7
Impact Crusher Overview
An impact crusher (impact break) is an ideal crushing machine for medium hardness materials, it can produce a more uniform particle shape (cubical) final product compared with the hammer crusher. Impact crushers are widely used in the aggregate industry (cement, asphalt, sand & gravel), owing to high reduction ratios and precisely shaped, cubical end products. Impact crushers can be set in any stage of the crushing circuit from primary crushing to the last step of the crushing process.
Impact Crusher Types
Common types have horizontal shaft impact crusher (HSI) and vertical shaft impact crusher (VSI). Besides, designed stationary and mobile impact crushers (track, wheel) for different applications.
Advantages
Impact Crusher Advantages
- Broken than large, generally for 30 to 40, the largest up to 150.
- High grinding efficiency, and low power consumption.
- Product granularity and less crushing phenomenon.
- Can selective crushing.
- Adaptability can be hard brittle broken, fibrous, and the following material, especially suitable for brittle material breakage.
- Equipment, small volume, light quality, simple structure, easy maintenance.
Structures & Working Principle
Impact Crusher Structure
The main parts of a impact crusher are hopper body, cascade cylinders, feed tubes, crushing chamber, crusher base; often replaced wear parts are worn plates, blow bars, breaker plates, etc.
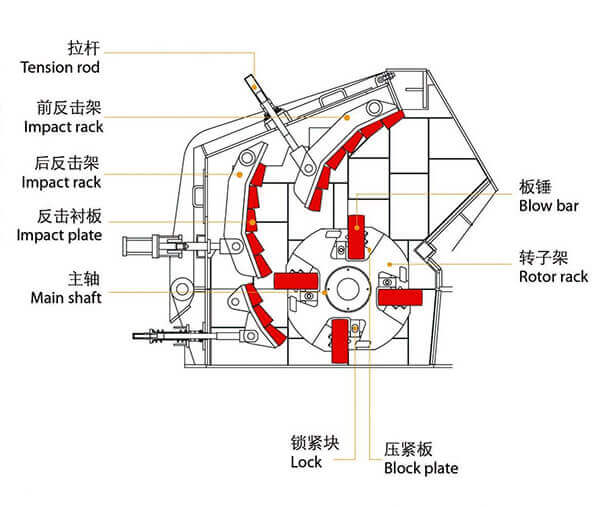
Impact Crusher Working Principle
Impact crusher is a machine that breaks materials using the impact of energy. The rotor rotates of our impact crusher with a high speed driven by a motor. When the materials get into the hammer effect area, they are impacting to break with the hammer on the rotor and then threw to the impacting position to take another crushing. After that, they spring back to the hammer impacting area from the impact wrist plate to take crushing again. This procedure repeats itself. The materials get into 1, 2, 3 impact cavities from big to small to take repeated crushing. When the material is crushed to the required size, it’s discharged from the outlet. The material’s discharging size and shape can be changed by adjusting the gap between the impact frame and rotator.
Technical Parameters
Model | Rotor Spec (mm) | Feed Opening Size (mm) | Max Feed Edge(mm) | Capacity (t/h) | Motor Power(kW) | Weight(t) | Overall Dimension (L*W*H)mm |
PF1007 | 1000*700 | 400*730 | 300 | 30-50 | 37-55 | 9.5 | 2400*1558*2660 |
PF1010 | 1000*1050 | 400*1080 | 350 | 50-80 | 55-75 | 12.2 | 2400*2250*2620 |
PF1210 | 1250*1050 | 400*1080 | 350 | 70-120 | 110-132 | 14.9 | 2690*2338*2890 |
PF1214 | 1250*1400 | 400*1430 | 350 | 130-180 | 132-160 | 18.6 | 2690*2688*2890 |
PF1310 | 1300*1050 | 490*1170 | 400 | 80-140 | 110-160 | 16.2 | 2780*2478*2855 |
PF1315 | 1320*1500 | 860*1520 | 500 | 160-250 | 180-260 | 19.3 | 3096*3273*2667 |
PF-1320 | 1320*2000 | 860*2030 | 500 | 160-350 | 300-375 | 28 | 3096×3560×3185 |
PF-1520 | 1500*2000 | 1315*2040 | 700 | 300-500 | 400-450 | 42.8 | 3890×3560×3220 |