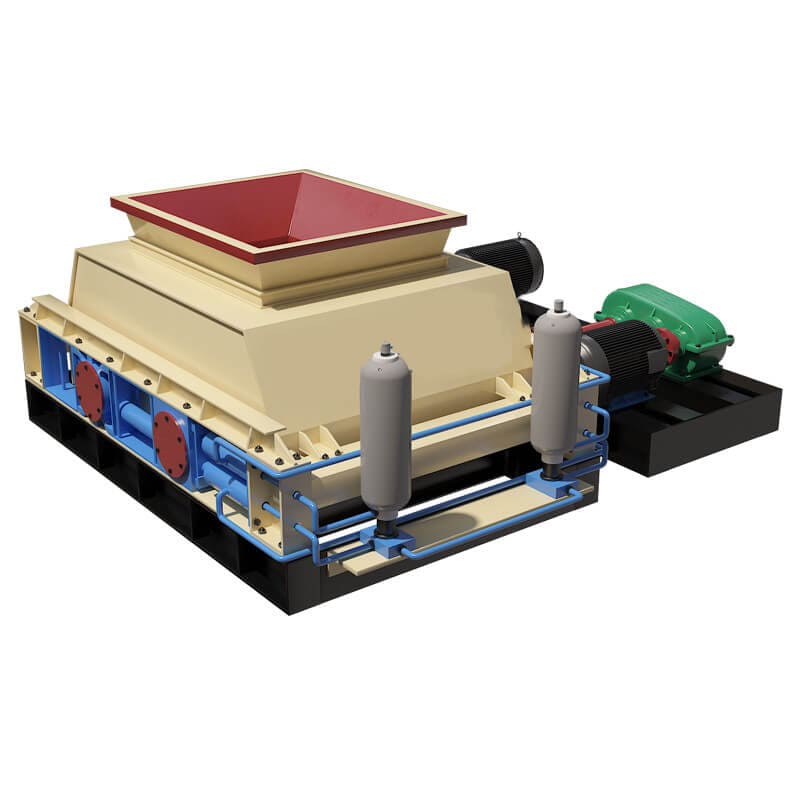
Hydraulic Roller Crusher
Capacity: 30-150 T/H
Max Feeding Size: 30 mm
Discharge Size: 5 mm
Application: It is suitable for medium and fine crushing of solid materials with compressive strength less than 250MPA and moisture less than 35%.
Hydraulic Roller Crusher Overview
The hydraulic roller crusher is a new type that combines various advanced technologies and is adjusted and controlled by the hydraulic system. It’s mainly used for crushing all kinds of medium hardness materials. It is widely used in fine crushing operations in cement clinker, sand making, building materials, mining, chemical industry, steel cement clinker, and other industries.
The unique feature of the hydraulic roll crusher is that it is equipped with a hydraulic system, which can automatically back off when it encounters unbreakable materials and increase the roll gap, thus discharging the materials and protecting the machine from damage. This electromechanical-hydraulic integration design enables the machine to run continuously and reliably, increasing production and reducing energy consumption.
The hydraulic roll crusher crushes materials by squeezing. This design skillfully utilizes the transmission of force and power to achieve precise control. Both hard rock and gravel can be crushed to the required size under gentle pressure, ensuring uniformity of crushing quality. In addition, this crusher is highly adjustable. Whether it is adjusting the crushing strength to suit different hardness materials or changing the discharge size to meet specific needs, it can be easily realized through the control system, which makes it surpass the traditional equipment in terms of flexibility.
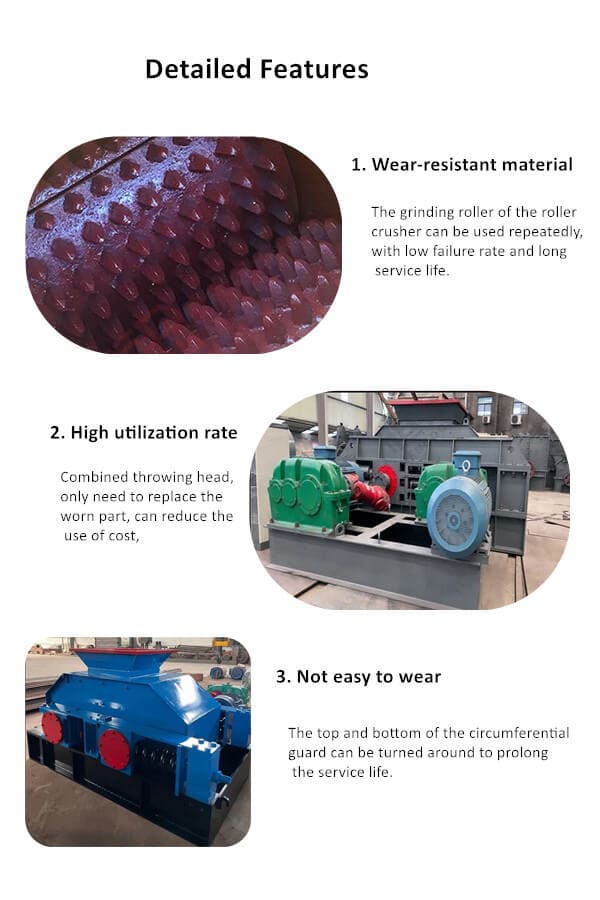
Advantages
Hydraulic Roller Crusher Advantages
- Energy saving and environmental protection
Compared with the traditional crusher, the hydraulic roll crusher consumes much less energy during operation, and its low carbon design and optimized control system significantly reduce energy consumption during operation. - Automation
The hydraulic roll crusher utilizes an automated control system that automatically adjusts the gap between the rolls and self-adjusts according to the material size and discharge specifications, reducing the need for manual intervention and lowering operational risk. - Durability
Heavy thickened roller skin is adopted, with advanced materials, reasonable structure, wear resistance, and impact resistance. The service life of parts is greatly extended with an automatic lubrication device. - Strong adaptability
Whether it is hard ore, soft rock, or special specifications of materials, the hydraulic roller crusher can easily cope with to meet diverse production requirements. - Most improved maintenance
With the standardized design of the equipment, wearing parts such as the wear-resistant layer on the surface of the crushing rolls can be replaced quickly, which reduces the time needed for maintenance and improves the overall operating efficiency of the equipment.
Structures & Working Principle
Hydraulic Roller Crusher Structure
- Upper feeding hopper: Used to input materials into the crusher.
- Frame part: The frame structure to support the whole equipment.
- Fixed Roller Section: The fixed roller cooperates with the movable roller for material crushing.
- Movable Roller Section: Movable rollers that move relative to the fixed rollers to crush the materials.
- Hydraulic support section: Provides the pressure required by the movable roller to ensure it is in close contact with the fixed roller.
- Transmission section: It includes a reducer, motor, and electric control device, responsible for driving the movable roller rotation.
These parts work together to ensure that the high-pressure roller crusher can work efficiently and stably to realize the crushing of materials.
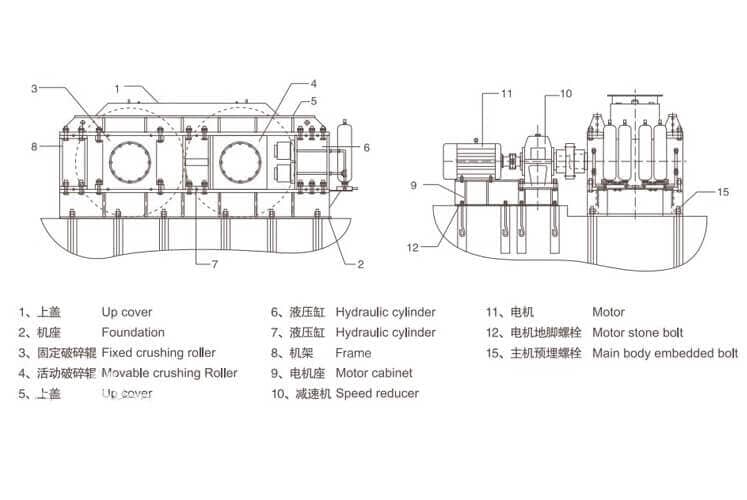
Hydraulic Roller Crusher Working Principle
The working principle of the hydraulic roller crusher is to squeeze and crush the material with two symmetrically arranged rollers. The rollers usually consist of a fixed roller and a movable roller, and the adjustment of the roller spacing is realized through the hydraulic system, to control the granularity of the output materials. The hydraulic roller crusher usually consists of the motor, hydraulic system, rollers, base, feeding port, discharge port, and other components. When working, the material enters into the crushing area from the inlet and is squeezed and sheared by the two rollers to be crushed into the required particles. The hydraulic system can realize the precise adjustment of the roller spacing, to control the granularity and shape of the output material.
Technical Parameters
Model | 2PGY-1000*800 | 2PGY-1200*1000 | 2PGY-1500*1000 |
Grinding Roller Diameter (mm) | 1000 | 1200 | 1500 |
Grinding Roller Length (mm) | 800 | 1000 | 1000 |
Max Feeding Size (mm) | <25 | <30 | <30 |
Max Throughput (mm) | <25mm 120t/h | <30mm 230t/h | <30mm 300t/h |
Discharge Size (mm) | <5 | <5 | <5 |
Final Product Capacity (T/H) | 30-60 | 60-100 | 100-150 |
Power (Kw) | 45kw-90kw*2 | 90kw-110kw*2 | 160kw*2 |
Total Weight (kg) | 18000 | 28000 | 31000 |