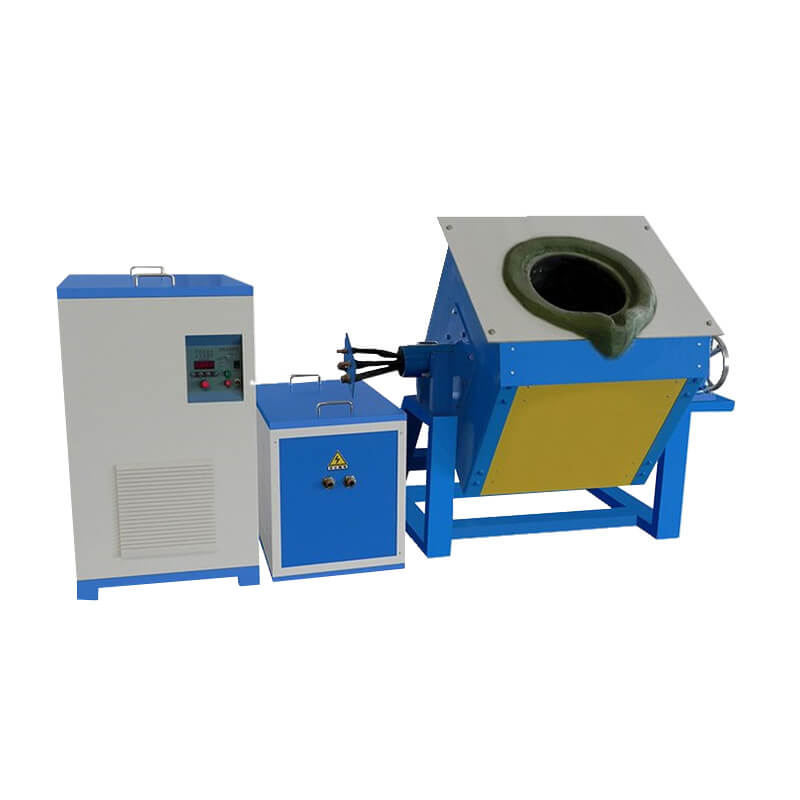
Small Tilt Melting Furnace
Frequency Range: 1-20KHz
Voltage: 3-Phase 380V±20%
Procession Material: Gold, copper, silver, aluminum, aluminum alloy, steel, stainless steel, etc.,
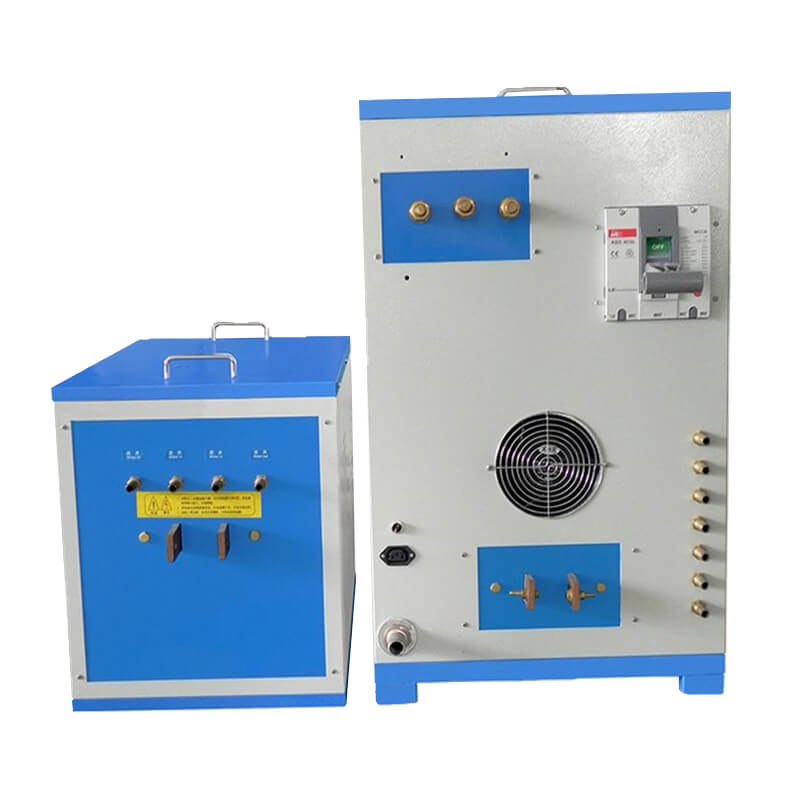
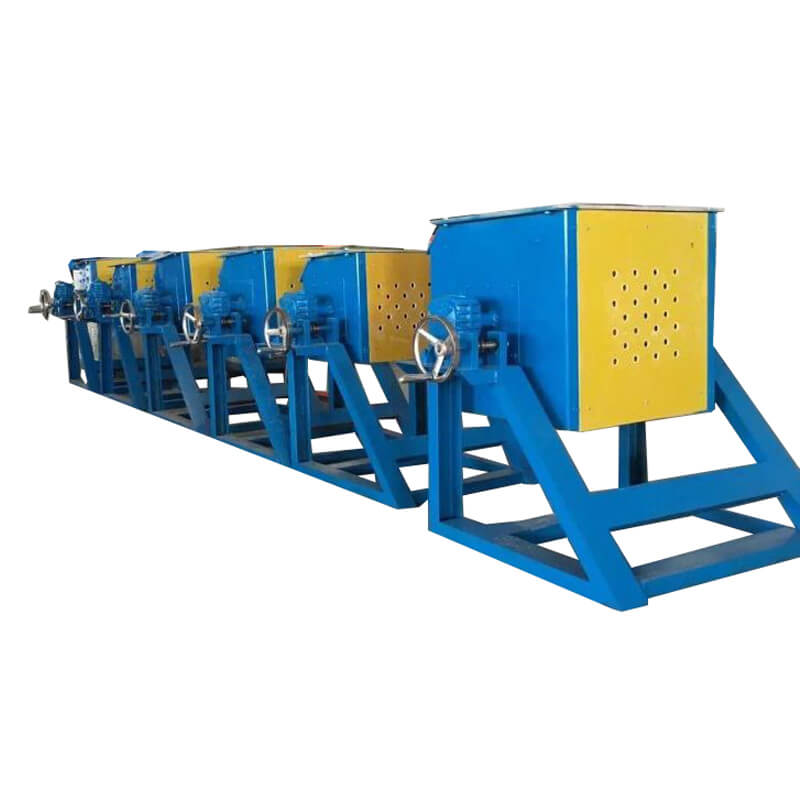
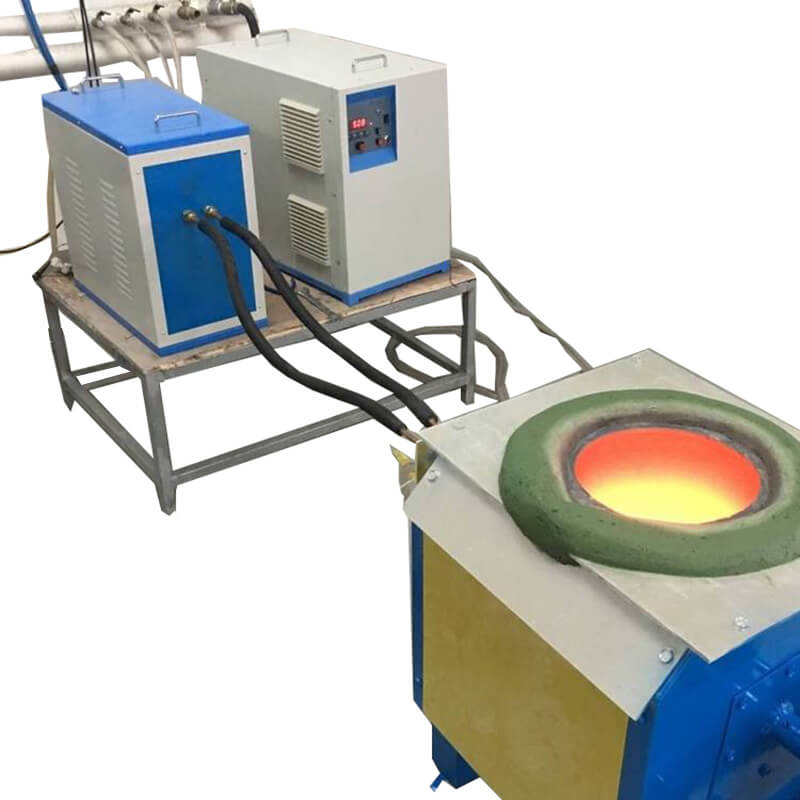
Small Tilt Melting Furnace Overview
A tilting melting furnace is an intermediate frequency induction melting furnace for metal melting and casting. Its main feature is that it can be tilted or poured to facilitate feeding, unloading, and control of the melting process. The melting furnace is usually constructed of refractory materials to resist high temperatures and chemical attacks.
The tilting mechanism can be operated manually or automatically, depending on the requirements of the melting process.
Tilt Melting Furnace Types
- Motor drive tilting melting furnace
- Manual tiltingmelting furnace
- Hydraulictilting melting furnace
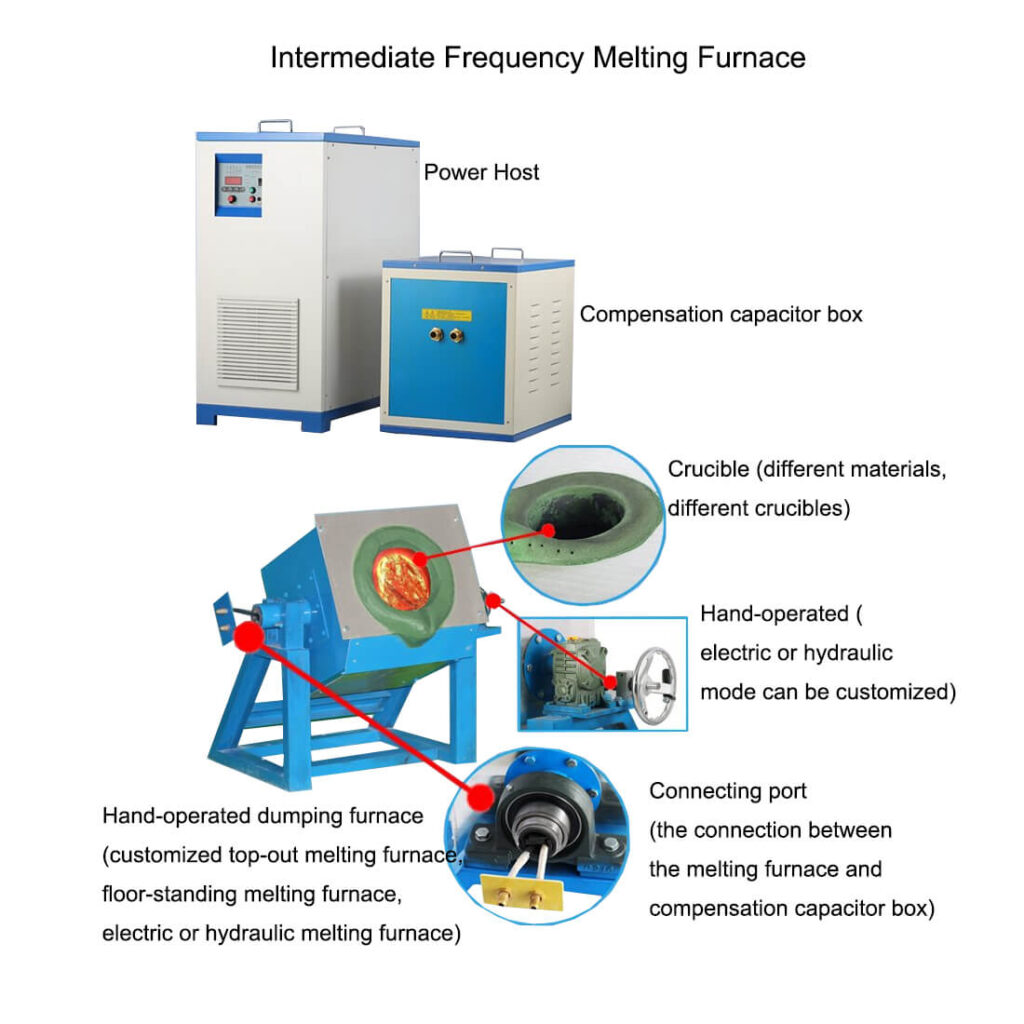
Our Small Melting Furnace Features
- Power range:The power range of the intermediate frequency melting furnace is 15kw-160kW.
- Heating method: The magnetic field induction heating method is adopted, and the metal purification has a very good effect.
- Objects of action: Metal:gold, silver, copper, iron, aluminum, zinc, tin, antimony, nickel, and various alloys; Non-metallic: silicon, polysilicon, graphite molds, etc.,
- Heating furnace body: Graphite crucible, quartz sand crucible, magnesia casting crucible, ceramic crucible, cast iron crucible, etc. (Different crucibles are equipped according to the melting of different metals).
- Heating speed: The heating speed is fast, suitable for 10-30 minutes for smelting with a low melting point, and 40-50 minutes for a large amount of smelting with a high melting point.
- Furnace temperature: More than 1200-1600 degrees, which can melt polysilicon.
Advantages
Small Tilt Melting Furnace Advantages
- The intermediate frequency melting furnace is used for melting steel, stainless steel, copper, gold, silver, and other materials.
- The intermediate frequency melting furnace has a good electromagnetic stirring effect, which is beneficial to the uniform temperature and structure of the smelted metal, is beneficial to scum, and reduces impurities.
- The frequency range is wide, from 1KHZ-20KHZ. The induction coil and matching compensation capacitor can be designed by comprehensively considering the melting amount, electromagnetic stirring effect, heating efficiency, noise during work, etc., to determine the size of the output frequency.
- Compared with SCR intermediate frequency, energy saving is at least 20%.
- The equipment is small in size and light in weight. The melting capacity ranges from a few kilograms to hundreds of kilograms. There is a wide range of options. It suits factory production and small-scale smelting for schools and research institutes.
- 24-hour uninterrupted melting capacity.
- It is convenient to replace the furnace bodies of different weights, materials, and methods to meet the requirements of various smelting furnaces.
Structures & Working Principle
Small Tilt Melting Furnace Structure
The small intermediate frequency tilt melting furnace comprises an intermediate frequency power supply, compensation capacitor box, and melting furnace.
Intermediate Frequency Induction Melting Furnace Working Principle
The working principle of the intermediate frequency induction melting furnace is to use the strong magnetic field-induced current generated by the intermediate frequency induction to form an eddy current in the furnace, so that the workpiece generates a local high temperature, thereby realizing the melting of the metal and the heat preservation of the molten pool. Specifically, when the medium-frequency induction melting furnace is working, the molten metal is first placed in the furnace, and then the coil in the furnace is connected. When the current passes through the coil, a strong magnetic field will be generated, and the magnetic field will form an eddy current in the molten metal. The heat generated by the eddy current makes the molten metal rapidly heat up to the melting point, forming a molten pool. At this time, the metal in the molten pool is in a high-temperature and high-energy state, and the insulation material in the furnace will maintain the temperature in the furnace to keep the metal in a molten state. After reaching the required temperature and time, disconnect the power supply, and the molten metal pool will cool and solidify to produce the required workpiece.
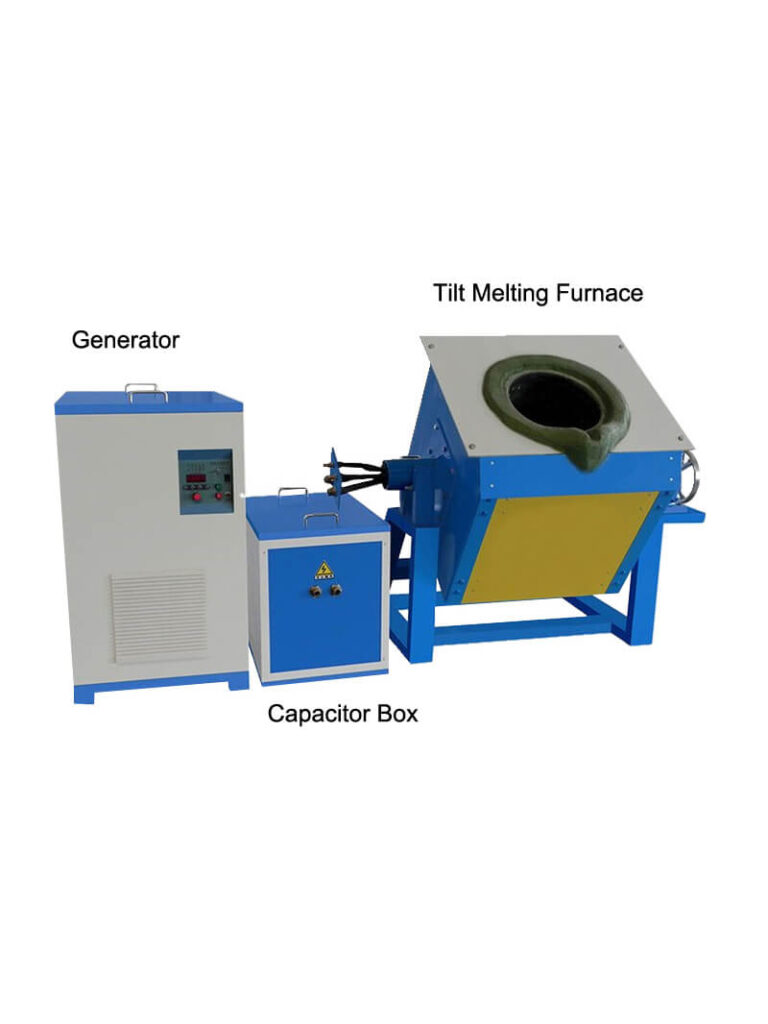
Technical Parameters
Model | Maximum Input Power(Kw) | Voltage | Melting Capacity(Kg) | ||
Steel, Stainless Steel | Copper, Gold, Silver | Aluminum, Aluminum Alloy | |||
JXSC-ZP15 | 15 | 3-phase 380V±20%, 50/60 Hz | 3 | 10 | 3 |
JXSC-ZP25 | 25 | 5 | 20 | 5 | |
JXSC-ZP35 | 35 | 10 | 30 | 10 | |
JXSC-ZP45 | 45 | 20 | 50 | 20 | |
JXSC-ZP70 | 70 | 25 | 100 | 25 | |
JXSC-ZP90 | 90 | 40 | 120 | 40 | |
JXSC-ZP110 | 110 | 50 | 150 | 50 | |
JXSC-ZP160 | 160 | 100 | 250 | 100 |