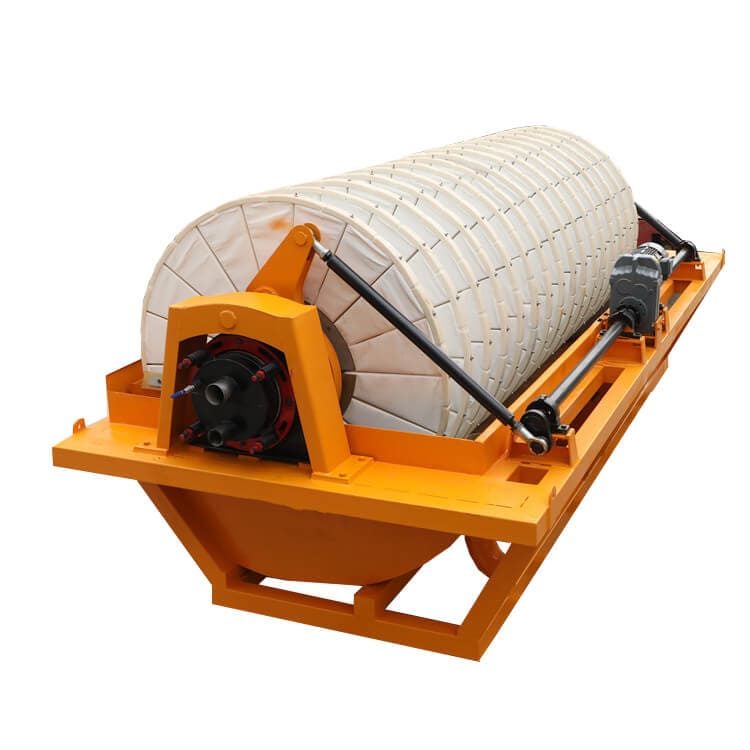
Disc Vacuum Filter
Filtering Area: 10-120 ㎡
Capacity: 0.85-1.2 t/h•m2
Application: Dehydration of non-ferrous metal concentrates, fine materials, coal washing plants, non-metallic minerals, chemical and environmental protection industries.
Disc Vacuum Filter Overview
Disc vacuum filter is a solid-liquid separation equipment, which uses vacuum as filtering power to separate solid and liquid in slurry, and is suitable for dehydration of non-ferrous metal concentrates, fine-grained materials, etc. The machine adopts advanced technologies such as filter disc guide frame guidance, variable speed stirring, back-blowing unloading, automatic centralized lubrication, etc. It is a dehydration equipment with excellent performance and reliable use. This machine is a new disc vacuum filter specially designed for ferrous ores (iron ore, ytterbium ore), precious metal ores (gold, silver and copper ore), non-ferrous metal ores (lead and zinc ore), non-metallic ores (feldspar ore, fluorite ore, andalusite ore, graphite ore, quartz sand ore), chemical industry, environmental protection, coal washing and ore dressing dehydration.
Disc Vacuum Filter Characteristics
Filter fan(disc)
- Smooth surface, evenly distributed dehydration holes, reasonable porosity, and rounded edges of filter fan and ribs not only improve the dehydration rate but also prolong the service life of filter cloth.
- The filter fan head has chamfers, high strength, and reinforced ribs at the bottom of the filter fan, which are not easy to damage or break during assembly and disassembly.
- The angle between the rib direction and the center line of the filter fan is more reasonable, and the fluid resistance is small. The filter fan’s large effective area improves the filter’s processing capacity.
- The wall thickness of the filter fan is 1/3 thicker than that of the ordinary one, and the weight of the filter fan is also increased by 1/3. It is a filter fan with reasonable structure and firmness in the current domestic market, and the average life is extended by 1.5 to 2 times.
Main shaft and filter tube
- The filter tube (including the shaft head) adopts high-strength wear-resistant ceramic composite steel pipe with a thick wall that is not easy to wear and prolongs the service life by more than two to three times.
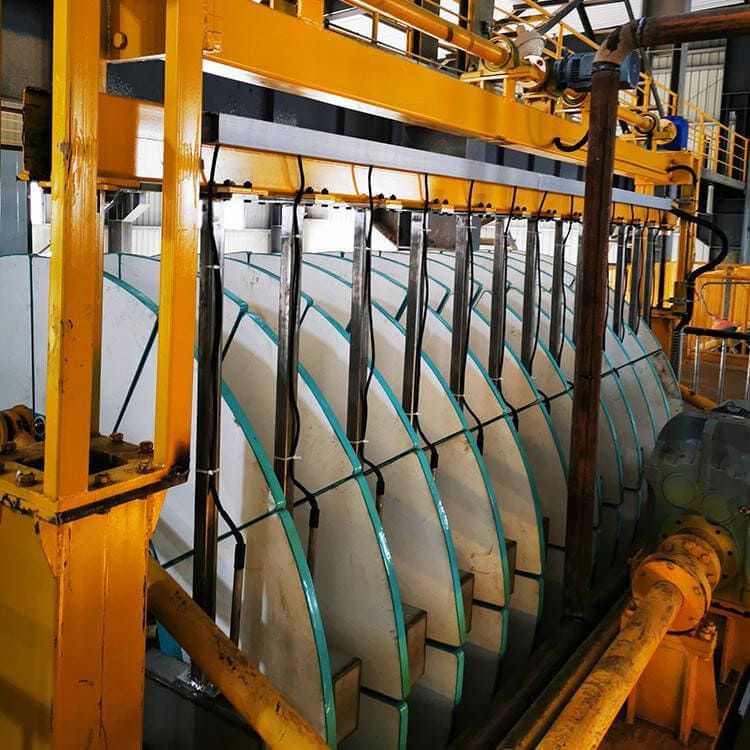
2. The flange connection is canceled at the interface between the filtrate pipe and the filter fan, and mold positioning and direct welding are adopted, which eliminates the aging factor of the leak-proof rubber gasket at the original flange connection and eliminates possible leakage points.
3. The pressure plate of each filter fan block is tightened with stainless steel screws and nuts at both ends, which is not easy to rust, makes it easy to replace the filter cloth, and greatly reduces labor intensity.
Stirring
- Add permanent magnets to prevent mineral powder from entering the stirring sleeve;
- Use water seal;
- Use packing seal;
- Add a skeleton seal ring to seal the shaft;
- The shaft surface is plated to prevent rust;
Tank body
The tank body below the stirring shaft adopts a corundum polymer wear-resistant coating to prevent the tank body steel plate from being worn.
Lubrication and cleaning
The dry oil pump is used for centralized multi-point automatic lubrication to ensure the normal operation of the equipment. The filter cloth is cleaned with an automatic cleaning device to maintain a good dehydration effect.
Electric control
The frequency conversion condensation is used to adjust the concentration and flow of the material to achieve the ideal working effect.
Disc vacuum filter is a highly efficient, energy-saving, and highly automated solid-liquid separation equipment, widely used in mining, metallurgy, the chemical industry, environmental protection, and other fields. Its main advantage is that it can continuously and efficiently filter and dehydrate, but it also needs to consider the initial investment and maintenance costs. It can greatly improve production efficiency and economic benefits through reasonable selection and use.
Advantages
Disc Vacuum Filter Advantages
- High-efficiency filtration
The disc vacuum filter can quickly and accurately remove impurities from the liquid and improve the quality and purity of the product. The filter fan is made of high-strength engineering plastics, with a smooth surface, uniform distribution of dehydration holes, and reasonable porosity. - Long service life
The filtrate tube can be made of high-strength wear-resistant ceramic composite steel pipe, which can increase the service life by more than 2 to 3 times. The gas distribution plate and friction plate are made of wear-resistant cast iron and equipped with a dry oil pump for automatic lubrication, with a good sealing effect and long service life. - Easy to maintain
The disc vacuum filter has a simple structure, convenient operation, a small daily maintenance workload, and saves labor costs. It adopts a new type of rake stirring, and the drive system is above the tank body. No sealing measures are required, and there is no slurry leakage. - Energy saving and environmental protection
Compared with traditional filtering equipment, the disc vacuum filter has lower energy consumption and higher environmental protection performance. - High safety
The disc vacuum filter is equipped with a safety protection device, which can automatically shut down under abnormal conditions to ensure the personal safety of the operator. - Environmentally friendly materials
The disc vacuum filter is made of environmentally friendly materials, which are harmless to the environment and conform to the green development concept of today’s society.
Structures & Working Principle
Disc Vacuum Filter Structure
The disc vacuum filter composes a tank body, a main shaft, a filter disc, a distribution valve, a stripping device, a flushing device, a screen washing device, a transmission device, a discharging device, and other parts.
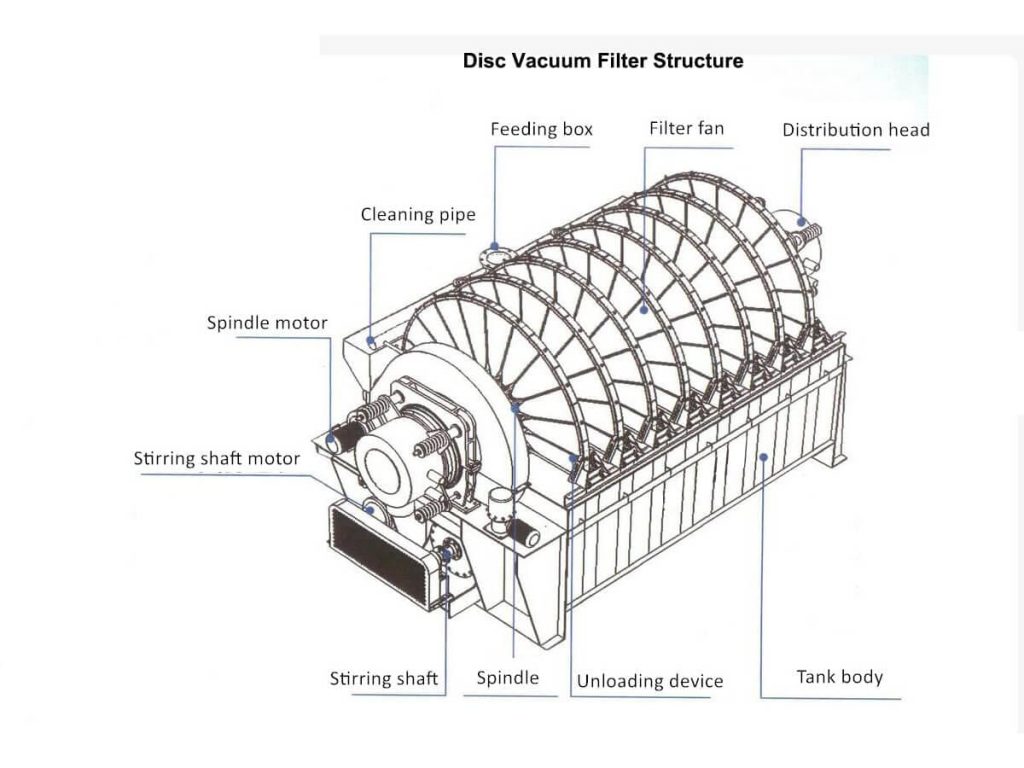
Disc Vacuum Filter Working Principle
A disc vacuum filter is a solid-liquid separation equipment. The filter disc is driven by a speed-regulating motor through a reducer and an open-gear transmission so that it rotates at a certain speed in a tank filled with slurry. When a filter fan of the filter disc is in the filter adsorption area, a pressure difference is formed on both sides of the filter medium with the help of the vacuum pump, so that the solid material is adsorbed on the filter medium (filter cloth) and forms a filter cake, and the filtrate is discharged through the filtrate pipe and the distribution head. When this filter fan is separated from the slurry level and enters the dehydration area, the filter cake is continuously separated from the water under the suction force of the vacuum, and further discharged from the filtrate pipe and the distribution head, so the filter cake is dried. After entering the unloading area, the filter cake is unloaded from the filter disc with back blowing and scraper, falls into the discharge trough, and is transported away by the ore collection belt conveyor. The whole operation process is carried out continuously.
Technical Parameters
Filter Tray Diameter (mm) | Ⴔ 2100 | Ⴔ 3100 | ||||||||||||||
Filtration Area (m2) | 10 | 15 | 20 | 25 | 30 | 35 | 40 | 45 | 50 | 60 | 60 | 72 | 84 | 96 | 108 | 120 |
Filter Tray Quantity (PCs) | 2 | 3 | 4 | 5 | 6 | 7 | 8 | 9 | 10 | 12 | 5 | 6 | 7 | 8 | 9 | 10 |
Power of Main SpindleMotor (kW) | 2.2 | 3 | 4 | 5.5 | 5.5 | 7.5 | 11 | |||||||||
Power of Stirring Motor (kW) | 3 | 4 | 5.5 | 7.5 | 7.5 | 11 | 15 | |||||||||
Discharge Method | Blowback | |||||||||||||||
Length (mm) | 2535 | 2925 | 3315 | 3705 | 4095 | 4485 | 4875 | 5265 | 5655 | 6435 | 4735 | 5235 | 5735 | 6235 | 6735 | 7235 |
Width (mm) | 2480 | 4280 | ||||||||||||||
Height (mm) | 2690 | 3740 | ||||||||||||||
Processing Capacity (t/h•m2) | 0.85-1.2 |