Copper Electrolytic Equipment/System
Copper electrolytic equipment is a device that reduces copper ions in the electrolyte into copper metal through electrolysis to form copper products such as copper plates or copper rods. It is widely used in copper smelters to produce high-purity cathode copper, also known as electrolytic copper. The copper electrolytic system is an industrial device that purifies metallic copper through electrochemical methods. It is mainly used to convert crude copper (containing impurities) or copper-containing solution into high-purity cathode copper.
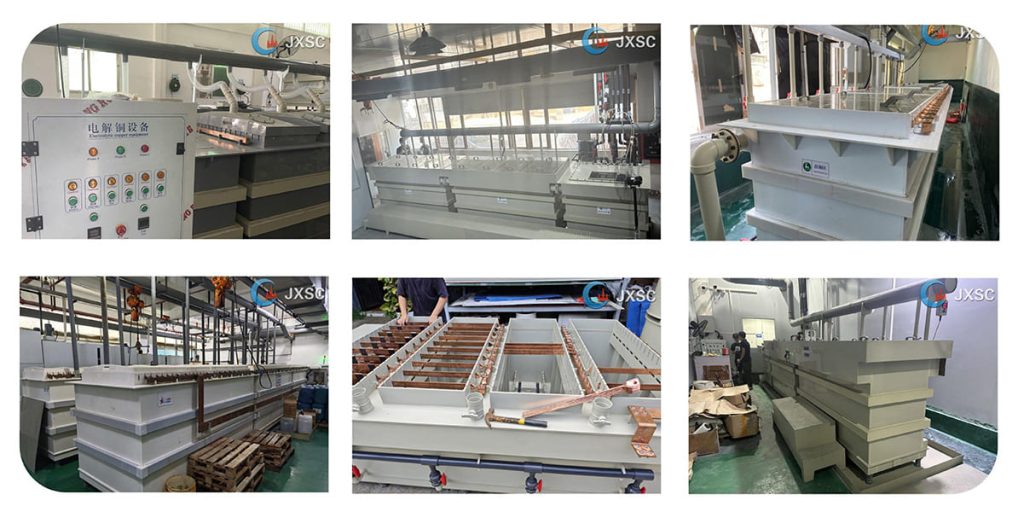
Copper Electrolytic (refining) Process
The copper electrolytic process, also known as electrorefining, is a method for purifying copper extracted from ores or recycled copper materials. This process uses electrolysis to separate impurities from copper, producing high-purity copper cathodes (typically 99.99% pure). It has the features of high-purity copper and selective removal of impurities.
Copper cathode & copper electrolytic
Copper Cathode: The copper cathode is a high-purity form of copper that is typically produced through a process called electrorefining. It is produced by applying an electric current to copper ore or scrap in an electrolytic cell, where copper ions from an anode plate migrate and settle on a cathode, forming pure copper. The copper cathode is a high-purity copper product(99.99% purity) that results from the electrorefining process, which is a key step in copper extraction.
Copper Electrolytic: Refers to the process of electrolysis used to refine copper or the copper that has undergone electrolytic refining but may be in a less refined or intermediate form before reaching the final product of copper cathodes.
Copper cathodes are the output of copper electrolytic systems used for refining and purifying copper, and are the final high-purity copper product. Copper electrolytic can either refer to the process of electrolytic refining or the intermediate products that arise from that process, such as the electrolytic copper used in further refinement or manufacturing.
Copper Electrolytic Equipment/System
Electrolytic copper production, also known as copper electrorefining, utilizes equipment like electrolytic cells, power supplies, and anode/cathode plates to purify copper and separate valuable impurities.
Copper Electrolytic Equipment/System refers to the set of machinery and components used to carry out the electrolytic refining process to produce high-purity copper. This process is essential in the copper industry to refine impure copper and produce copper cathodes with a high level of purity.
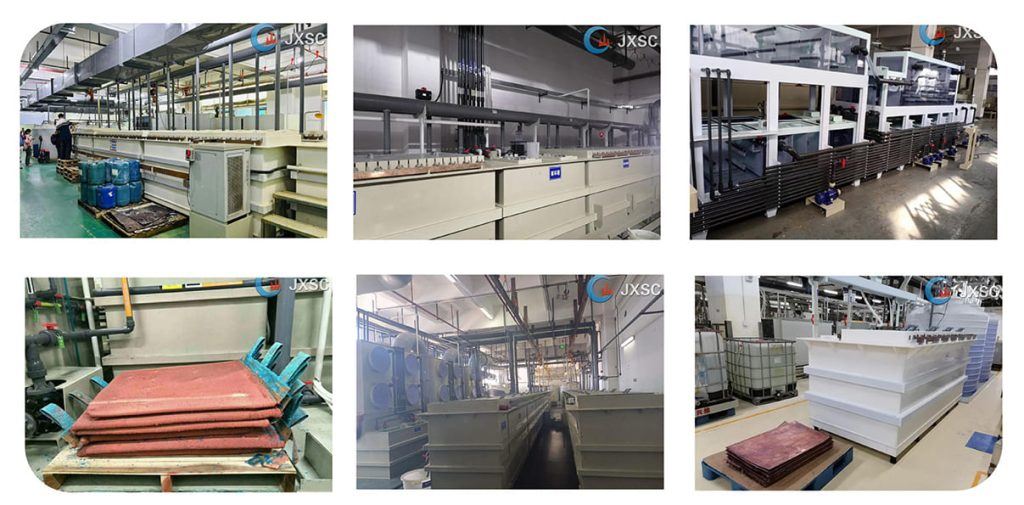
Refining Principle of Copper Electrolysis Machine
Electrolytic copper production equipment uses electrolysis to reduce the copper ions in the electrolyte to the copper metal on the electrode. The specific process is to pass the current through the electrolyte solution. The cations get electrons at the cathode. They are reduced, and the anions lose electrons at the anode and are oxidized so that pure copper is deposited on the cathode. Electrolytic copper is one of the core processes in the modern copper smelting industry.
Copper Electrolysis System Production Process
- Preparation stage
Make the crude copper into a thick plate as the anode, the pure copper sheet as the cathode, and prepare the electrolyte solution. - Electrolysis process
After power is turned on, the copper on the anode loses electrons and enters the electrolyte solution, and the copper ions on the cathode get electrons and are reduced to pure copper. - Impurity treatment
Impurities less active than copper, such as gold and silver, are deposited at the bottom of the electrolytic cell, and active impurities remain in the electrolyte for subsequent treatment.
Advantages
- High-purity output
The purity of cathode copper can reach more than 99.99%, meeting the high-precision requirements of power (cables), electronics (circuit boards), etc. - High efficiency and energy-saving
1. Titanium-based composite anode and low-voltage electrolytic cells are used, and the current efficiency is ≥95%.
2. The waste heat recovery system uses the flue gas of the anode furnace to heat the electrolyte, reducing steam consumption by 30%. - Environmental protection and low-carbon
1. The fully enclosed residual anode washing unit achieves zero wastewater discharge.
2. The exhaust gas is sprayed with alkali solution + adsorbed by activated carbon, and the SO₂ emission concentration is ≤100mg/Nm³.
Applications
- Pyrometallurgical smelting and purification: processing crude copper anode plates (traditional copper mines).
- Hydrometallurgy: leaching copper ions from low-grade oxide ores, scrap copper, or electronic waste, and direct electrolytic purification.
- Renewable resources: recycling waste copper wire, copper slag, etc. to achieve resource recycling.
Electrolytic Copper Equipment Processing Materials
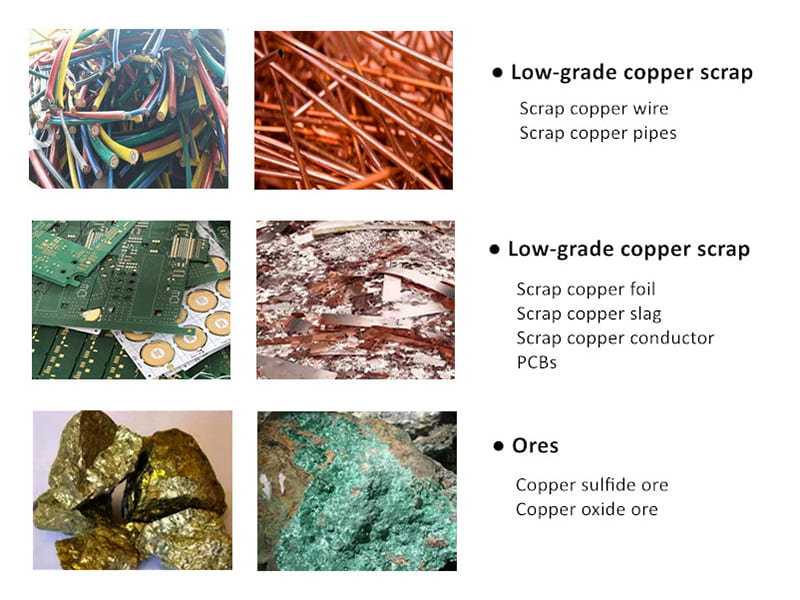
The copper electrolysis machine can process materials like scrap copper wire, scrap copper pipes, scrap copper foil, scrap copper slag, scrap copper conductor, PCBs, copper shavings, sulfide & oxide ores, etc.,
Copper Electrolytic Equipment/System for Sale
JXSC Electrolytic Copper Solutions
—— Technological Innovation Empowers Green Metallurgy
Under the global trend of efficient development of copper resources and green smelting, we provide mining companies with full-process solutions from ore processing to high-purity cathode copper production with its independently developed electrolytic copper equipment and leaching-extraction-electrolysis integrated system, helping customers achieve the three goals of efficient production, energy conservation and emission reduction, and intelligent upgrading.
Rock Copper Ore Flotation & Electrolysis System
This 3D flowchart design is for a complete processing plant from raw copper ore to copper concentrate and then to cathode copper plate finished products, which consists of two major systems: flotation beneficiation system and copper electrolysis system.
1. The flotation beneficiation system mainly includes feeding, crushing and screening, grinding and classification, copper ore flotation, copper concentrate filtration, tailings dehydration, and finally copper concentrate.
2. The copper concentrate enters the copper electrolysis system, which mainly includes leaching and filtration, extraction system, washing system, back extraction system, electrolysis system, transfer and regeneration system. The purity of cathode copper obtained by electrolysis can reach more than 99%.
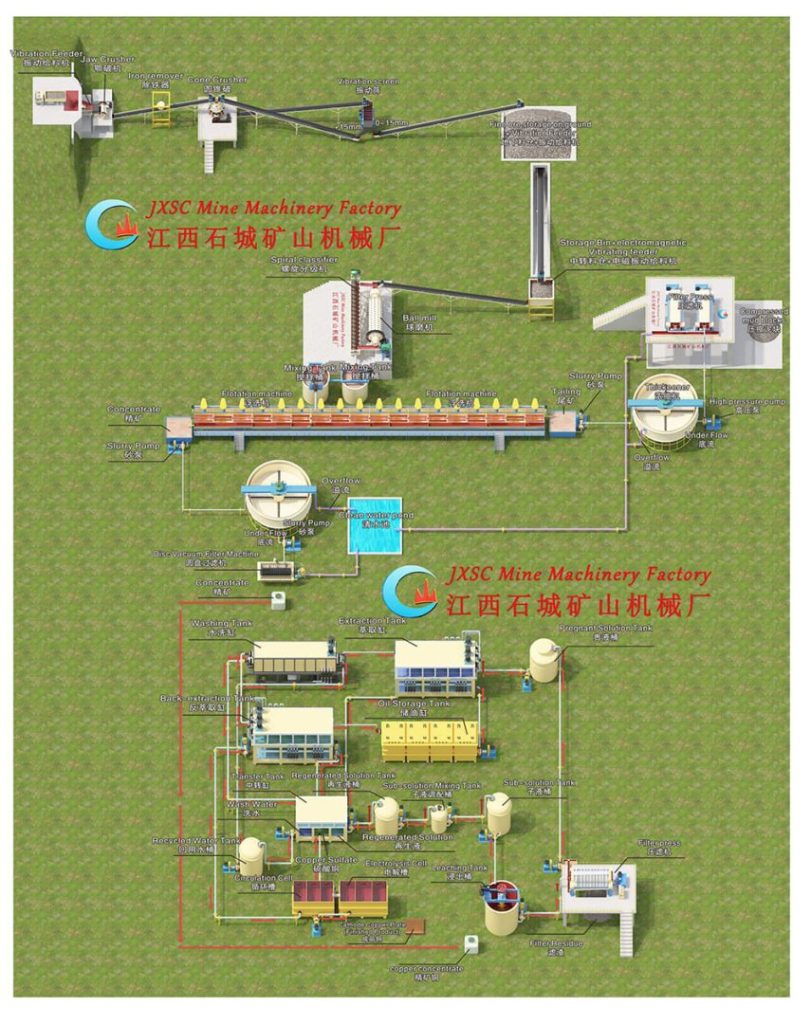
Rock Copper Ore Gravity Separation & Electrolysis System
This 3D flowchart design is for a complete processing plant from raw copper ore to copper concentrate and then to cathode copper plate finished products, which consists of two major systems: gravity beneficiation system and copper electrolysis system.
1. The gravity beneficiation system mainly includes feeding, crushing and screening, grinding and classification, gravity separation (spiral chute for primary separation and shaking table for final separation), and finally get copper concentrate.
2. The copper concentrate enters the copper electrolysis system, which mainly includes leaching and filtration, extraction system, washing system, back-extraction system, electrolysis system, transfer and regeneration system. The purity of cathode copper obtained by
Electrolysis can reach more than 99%.
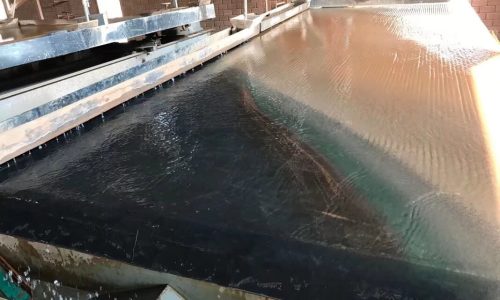
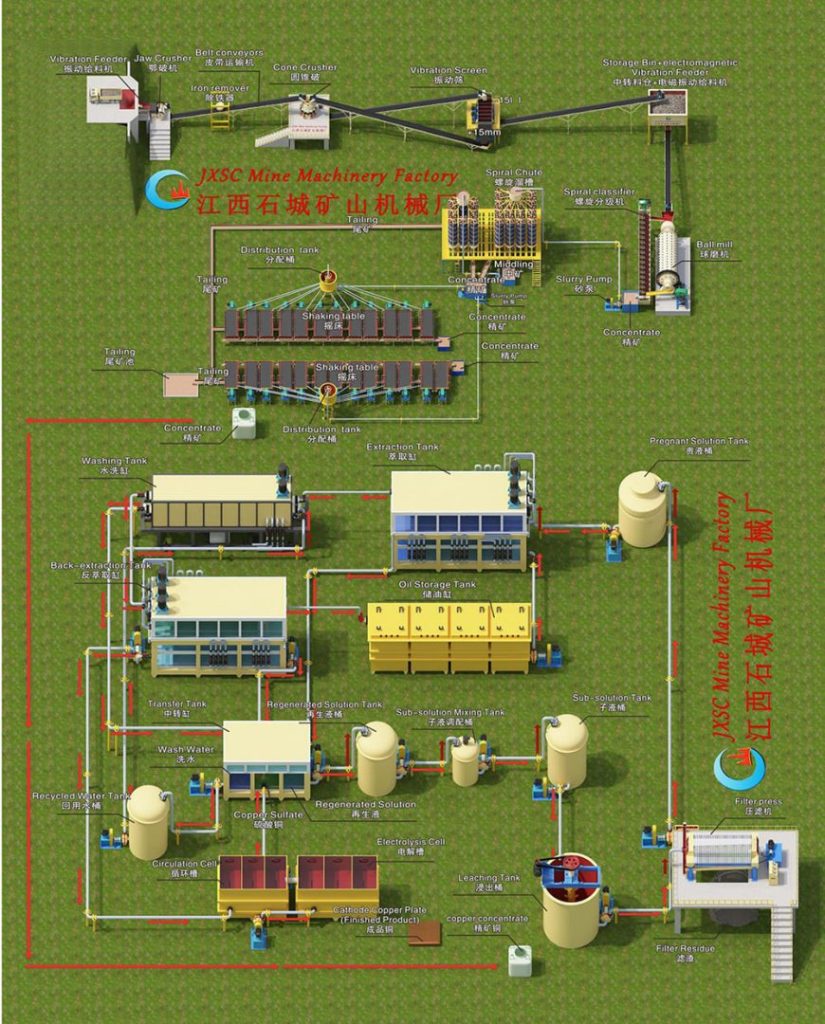
As the copper smelting industry moves towards intelligence and greening, JXSC Mineral is becoming a strong partner for the transformation and upgrading of global copper enterprises with its leading electrolytic equipment and system solutions. Our technology is centered on high precision, high efficiency, and high reliability, covering the entire process from electrolytic cell design to cathode copper output, helping customers achieve production capacity breakthroughs and cost optimization.