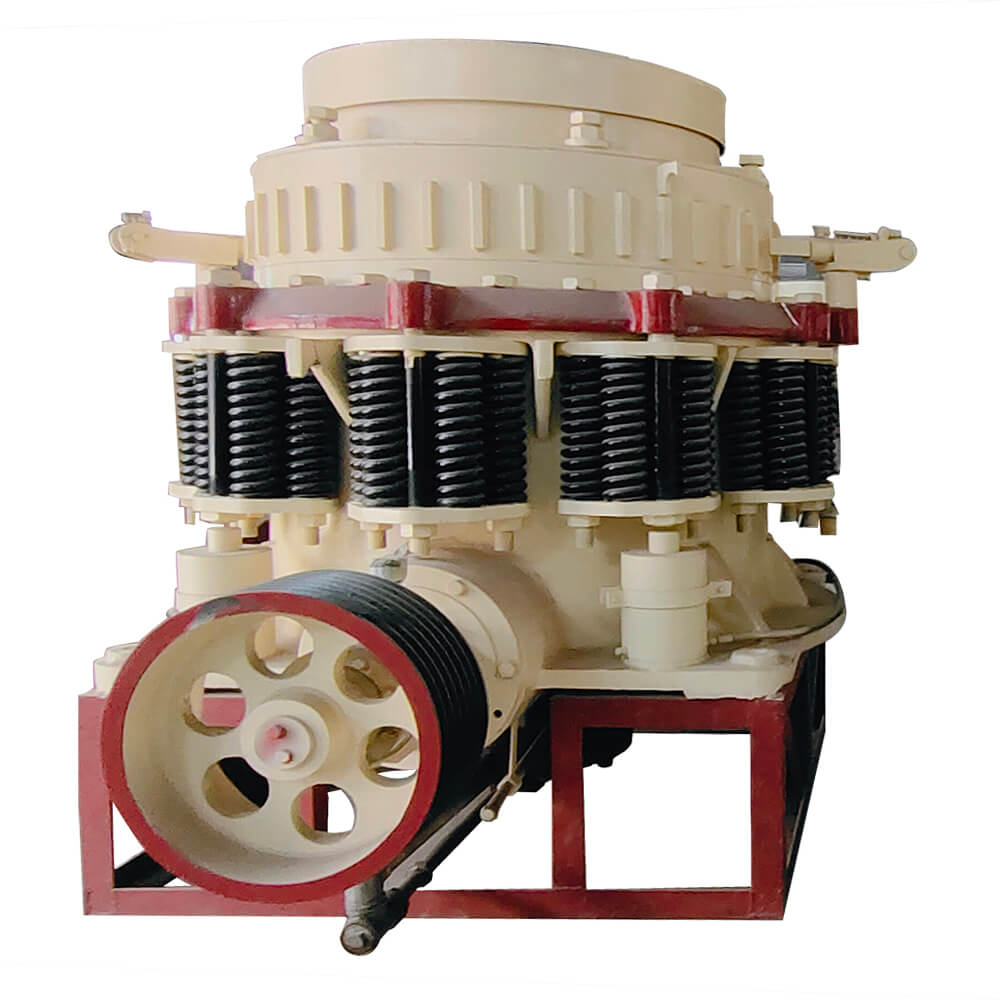
Cone Crusher
Capacity: 10-1450 tph
Feeding Size: 50-425 mm
Discharge Size: 6-64 mm
Process Material: Hard rock, ore, slag, refractory, etc. Such as granite, basalt, pebbles, copper ore, iron ore, limestone, quartz, and diabase.
Cone Crusher Overview
Cone crushers are popularly used in the aggregate, mining, concrete, and coal industries, suit for the secondary, tertiary crushing stages to do material size reduction and shaping. Be different from than jaw crusher, impact crusher, the cone crusher is a type of compression crusher, innovative designed with a cone-shaped inlet from where the object material is put in for crushing, reduces material by squeezing or compressing it until it gets smaller discharges at the bottom.
Cone Crusher Types
Cone crushers are mainly divided into Spring Cone Crushers and Hydraulic Cone Crushers, but the hydraulic cone crusher has more advantages, such as the hydraulic overload relief system, which can automatically clear the obstruction and prevent overload. Hydraulic Cone Crushers divide into single cylinder hydraulic cone crushers and multi-cylinder cone crushers.
Advantages
Spring Cone Crusher Advantages
- Continuous rotation of the operated cone body and high productivity.
- Easy to press, impact and crush and low power consumption.
- Even particle size of products and uniform surface wear of movable cone.
- Simple structure: frame, horizontal axis, movable cone, balance wheel, eccentric bushing, upper crushing wall (fixed cone), down crushing wall (movable cone), fluid coupling, lubrication system, hydraulic system, control system, etc.
- The movable cone swings close to discharge opening of crushing cavity, which intersects an equal parallel strip between them to make end products granularity. The feed opening is not large, which can deal with the primary crushed materials.
- This kind of cone crusher adopts dry oil and water sealing avoiding dust entering and keeping clean.
Hydraulic Cone Crusher Advantages
- Highly reliable with high crushing efficiency and good shape of product size.
- Multiple types of crushing cavities can be chosen. With suitable crushing cavity type and eccentricity, it can meet the production requirement and realize high production.
- Hydraulic adjustment of the discharge port, which can expediently and timely adjust the discharge port. The crusher can operate under a full feed state, reducing quick-wear part consumption and operation costs.
- Advanced hydraulic pressure technology is applied to realize overload protection effectively. It simplifies the structure of the crusher and reduces weight. All the maintenance and examination can be finished on the crusher, which makes maintenance more convenient.
- Double insurance of hydraulic pressure and lubrication systems protects the hydraulic cone crusher with good bearing lubrication during overload.
- Reasonable price and low operation cost;
Structures & Working Principle
Cone Crusher Structure
The main parts of a cone crusher are Rack, horizontal axis, moving cone, balance wheel, eccentric sleeve, upper broken wall (fixed cone), lower broken wall (moving cone), fluid coupling, lubrication system, hydraulic system, etc. Cone crusher wear parts, the most often replaced parts are the frame liners, mantle liners, bowl liners.
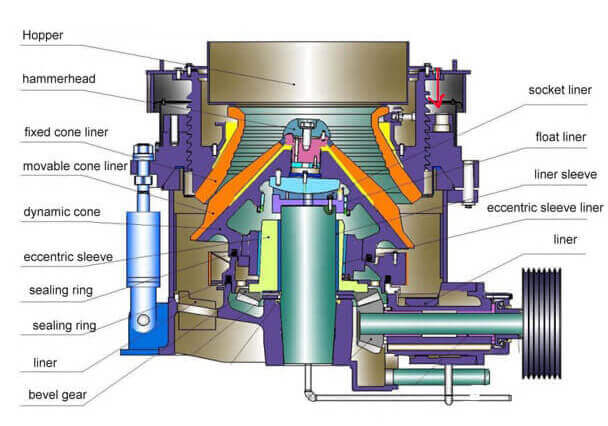
Cone Crusher Working Principle
While the eccentric shaft rotating, the materials are continuously squeezed and compressed between the moving and fixed steel, thus the materials gradually become smaller and pass down through the discharge port. The required final size is adjustable and determined by the gap between the two crushing steel at the lowest point. Hydraulic cone crushers have a hydraulic setting adjustment system, which gives more advantages than a normal spring cone crusher.
Technical Parameters
Model | Feeding Size (mm) | Discharging Size (mm) | Power (KW) | Capacity (T/H) |
HP200 | 50-185 | 5-19 | 132-200 | 90-250 |
HP300 | 50-230 | 6-25 | 180-250 | 110-440 |
HP400 | 50-295 | 6-30 | 280-355 | 140-630 |
HP500 | 55-330 | 6-30 | 355-450 | 175-790 |
HP800 | 90-353 | 6-32 | 550-630 | 260-1200 |
Model | Chamber | Feeding Opening(mm) | Max Feeding Size(mm) | Minimum Discharge(mm) | Maximum Discharge(mm) | Motor Power | Machine Weight | Capacity | ||||
Stroke | Stroke | Stroke | Stroke | Stroke | Stroke | KW | KG | T/H | ||||
DNGP100 | A | 150 | 120 | 12 | 15 | 30 | 39 | 37 | 40 | 90 | 5800 | 35-135 |
B | 130 | 105 | 10 | 11 | 26 | 33 | 31 | 38 | ||||
C | 100 | 85 | 7 | 9 | 16 | 33 | 30 | 30 | ||||
DNGP200 | A | 220 | 180 | 18 | 22 | 30 | 35 | 30 | 30 | 160-220 | 12300 | 85-350 |
B | 150 | 120 | 15 | 19 | 26 | 35 | 30 | 30 | ||||
C | 80 | 60 | 9 | 12 | 35 | 30 | ||||||
DNGP300 | A | 230 | 190 | 20 | 25 | 45 | 40 | 250-280 | 16500 | 115-400 | ||
B | 150 | 125 | 17 | 20 | 45 | 40 | ||||||
C | 80 | 60 | 10 | 13 | 40 | 35 | ||||||
DNGP500 | A | 230 | 180 | 22 | 26 | 50 | 45 | 315 | 25800 | 245-500 | ||
B | 150 | 125 | 19 | 22 | 48 | 43 | ||||||
C | 100 | 80 | 12 | 14 | 40 | 35 | ||||||
DNGP600 | A | 280 | 220 | 22 | 26 | 45 | 35 | 355 | 26700 | 280-715 | ||
B | 150 | 125 | 19 | 22 |
Model | Crushing Cone Dia(Feet) | Max Feeding Size(mm) | Discharge Size Range(mm) | Main Machine Power(KW) | Process Capacity(T/H) |
DN900 | 3′(914) | 50-163 | 10-38 | 75 | 27-140 |
DN1200 | 4′ | 80-180 | 16-50 | 132 | 80-250 |
DN1300 | 4.25′(1295) | 70-238 | 10-51 | 155 | 50-360 |
DN1600 | 5.5′(1676) | 90-331 | 10-64 | 240 | 100-630 |
DN2100 | 7′(2134) | 120-425 | 13-64 | 315-400 | 300-1450 |