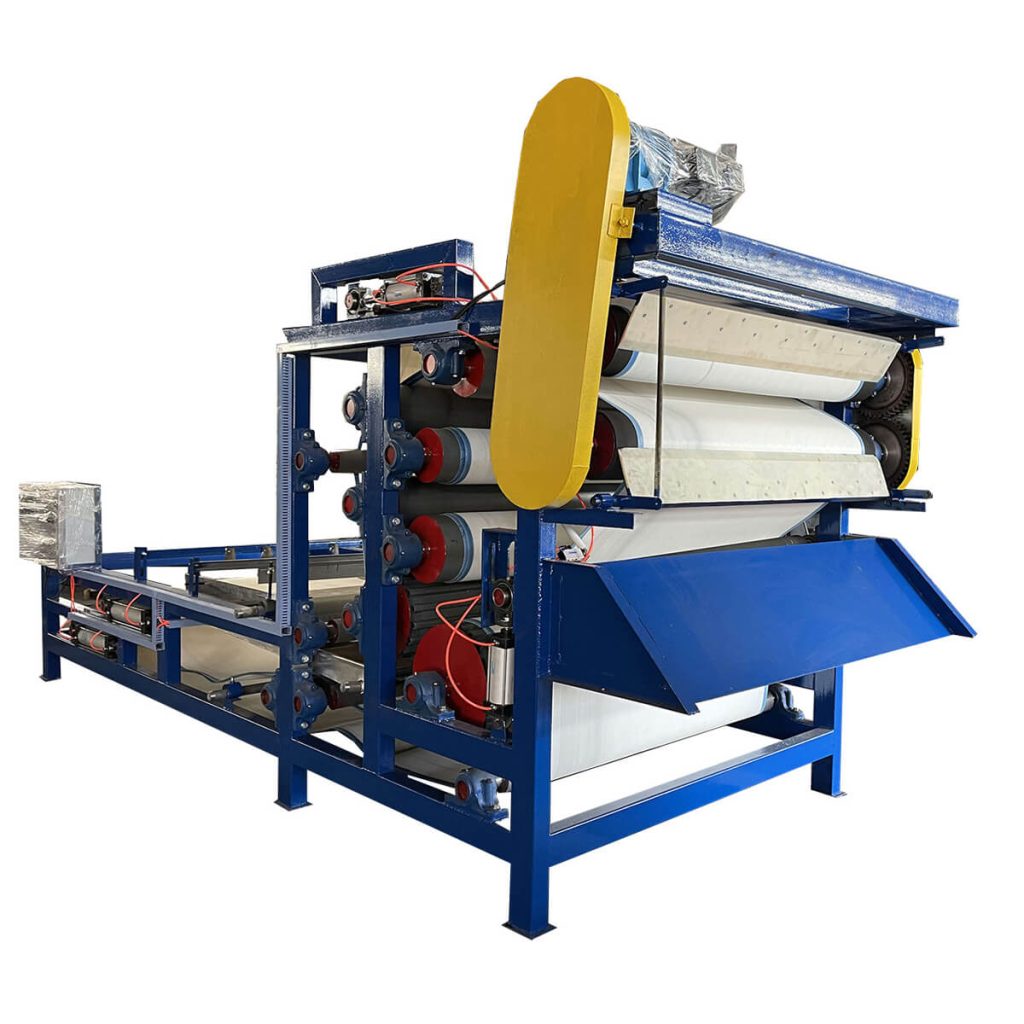
Belt Filter Press
Capacity: 0.5-30 t/h
Power: 0.75-7.5 kW
Concentration: Slurry feed concentration is 3-8%, and output concentration is 25-40%.
Application: Metallurgy, mining, chemical industry, paper making, printing and dyeing, leather, electroplating, brewing, coal, sugar making, etc.
Belt Filter Press Overview
Belt filter press is a kind of equipment widely used in the field of solid-liquid separation, especially for the dehydration of activated sludge, metallurgical sludge, flotation concentrate, and tailings (coal). It is widely used in metallurgy, mining, chemical industry, papermaking, printing and dyeing, leather, electroplating, brewing, coal, sugar making, and other industries. A belt filter press is a kind of equipment that separates solid and liquid under a certain pressure through one or more continuously running filter belts. The belt filter press has become a commonly used solid-liquid separation equipment in many industries due to its simple structure, large processing capacity, convenient operation, and high degree of automation.
A belt filter press is built so that it occupies very little space. The entire equipment occupies very little space due to its unique build. Although it performs the same function and gives the same effective results as other filter machines, it occupies ½ of the space compared to all other filter machines.
Features
- The concentrated belt filter press has a compact structure, novel style, convenient operation and management, large processing capacity, low filter cake moisture content, and good effect.
- The gravity dewatering section is inclined, and the sludge liquid surface is 30mm above the filter cloth. The gravity dewatering section is long, and the total length of the first and second gravity dewatering sections is more than 5m, so the sludge is fully dehydrated and loses fluidity before squeezing.
- The dewatering roller adopts a “T”-shaped drain trough to discharge the water quickly after squeezing. Thereby improving the dewatering effect. The filter belt deviation is equipped with an automatic control device, and the filter belt tension and filter belt moving speed can be freely adjusted, which is convenient for operation and management.
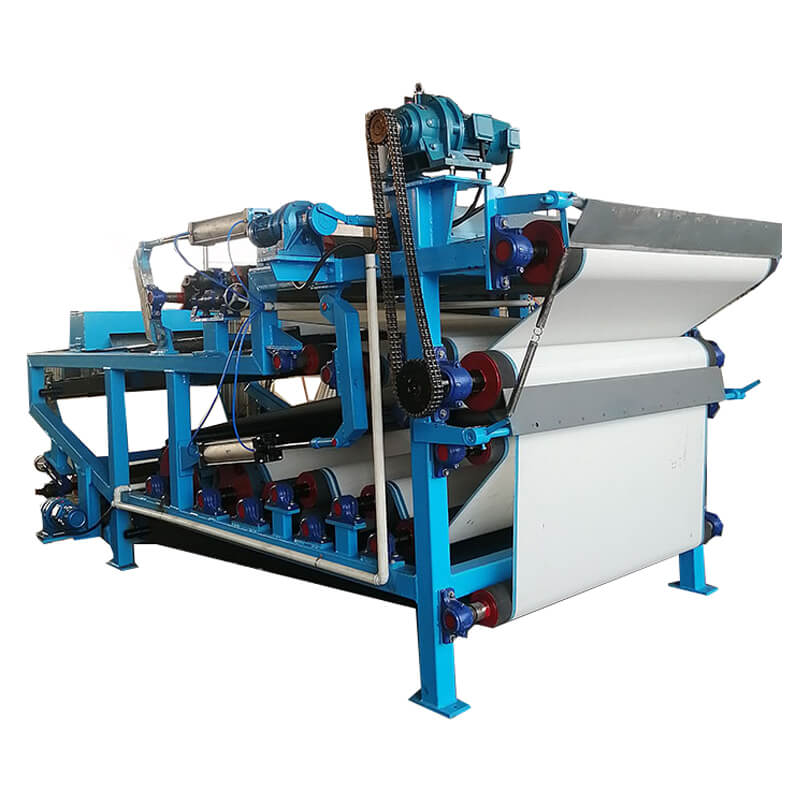
The belt filter press is easy to handle. It has an uncomplicated and straightforward design. The easy and simple design makes a belt filter very easy to use and operate. No special training is required to learn the operation of a belt press machine. It can be used even by ordinary workers without any special instructions. The machine is not only simple in its design but also gives very accurate results.
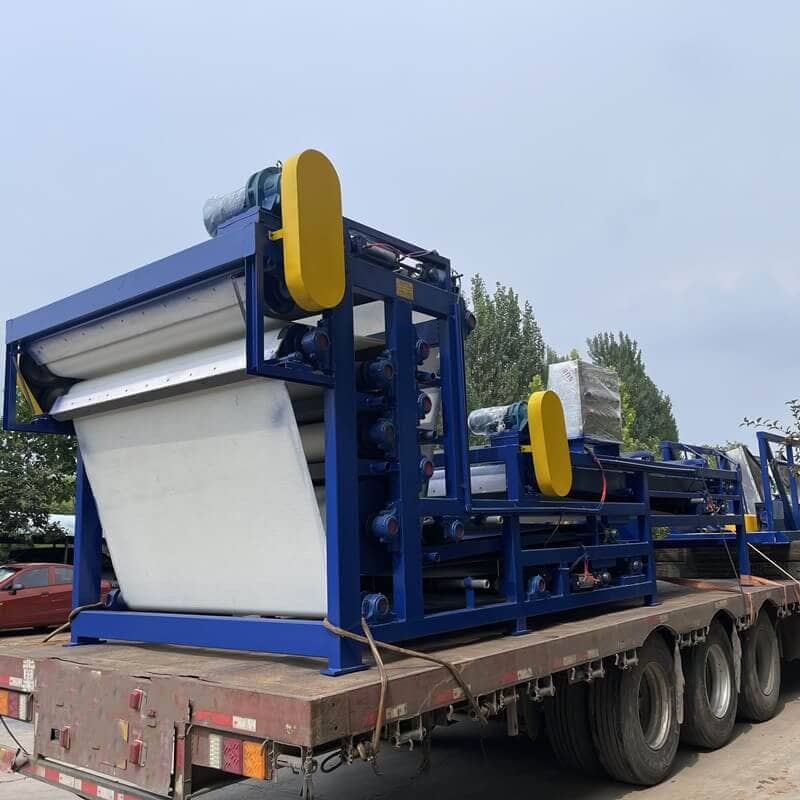
Advantages
Belt Filter Press Advantages
- Automatic control & continuous operation
The belt press filter can function for 24 hours. It does not have to be stopped like other presses. The continued operation helps to save cost in energy. A lot of time also gets saved since it can function continuously. This continuous operation feature makes a belt press the most promising choice in filter machines. - Stable operation and long service life
The belt press filter is made of high-strength stainless steel bearings in place of conventional carbon steel bearings. Stainless steel bearings provide the machine with a long operational life. The high-strength stainless steel bearings protect the belt press machine from rust or corrosion. Resistance from rust or corrosion increases the life of the belt press machine by ten years. The belt filter has a particular adjustment structure that protects the machine from damage. - Less Energy
Among all filter machines, the belt press filter consumes less energy. Less consumption of energy automatically lessens the energy cost of the industries. A belt press and other filter machines have identical treatment effects. However, a belt press under the same treatment effect will consume and need less power. You can say that a belt press filter needs 1/3rd less water and power than all other filter machines. - High dehydration efficiency and high solid content of mud cake
Scientific design and reasonable layout ensure the filter press has high dehydration performance. The main dehydration roller adopts a perforated design, it increases the processing capacity and allows the sludge to be dehydrated on both sides. The two sides of the filter belt are quickly dehydrated during the filtration process, shortening the dehydration time. The arrangement of the smaller rollers at the back and the change of the contact angle of the filter belt ensure the combination of pressure and shear force, thereby greatly improving the solid content and dehydration efficiency of the mud cake. - Easy to manage and maintain
The tension of the filter belt is achieved by an inflated cylinder, so that the entire filter belt maintains a constant tension, and the tension will not change due to changes in the feed amount, which is convenient for operation and management. - Automatic deviation correction, automatic feeding
The filter press has an air pressure control system that automatically detects the position of the filter belt on the roller and automatically corrects the deviation. For wide filter belt filter presses, there is also an automatic sludge feeding device to ensure that the sludge enters the filter belt evenly, thereby improving the filtration efficiency and extending the life of the filter belt.
Structures & Working Principle
Belt Filter Press Structures
The general mechanical components of a belt filter press include dewatering belts, rollers, and bearings, a belt tracking and tensioning system, controls and drives, and a belt washing system.
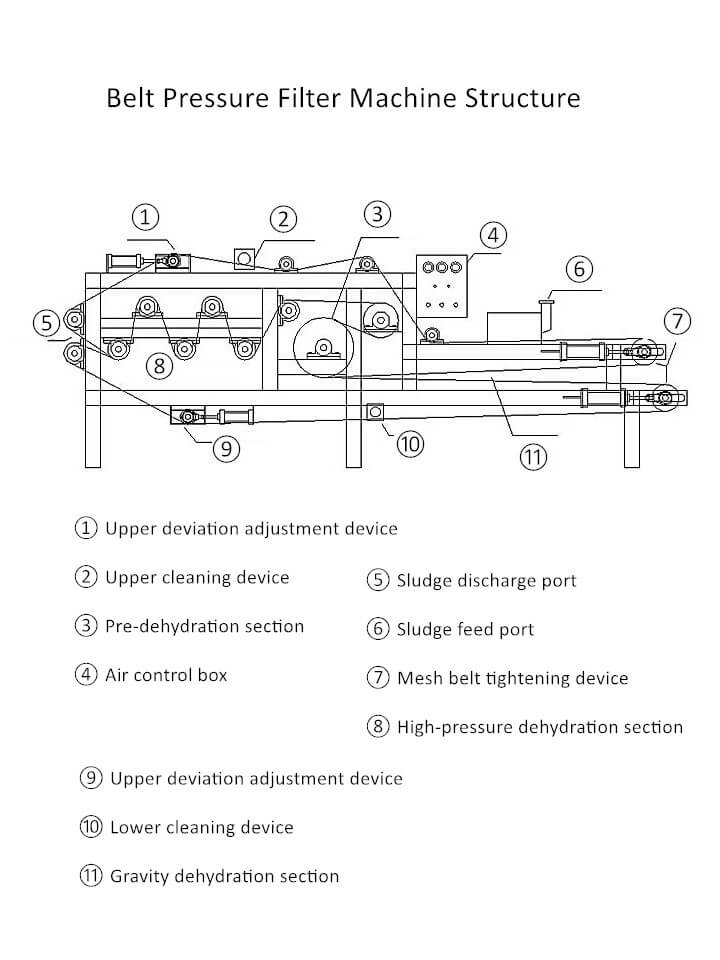
Belt Filter Press Working Principle
To improve the dehydration of sludge, improve the properties of filter cakes, and increase the permeability of materials, the sludge needs to be chemically treated. This machine uses a unique “water flocculation mixer” device to achieve the effect of chemical dosing flocculation. Through the wedge-shaped pre-pressing, low-pressure, and high-pressure areas, the extrusion and shearing force from small to large gradually squeezes the sludge to achieve the greatest degree of mud and water separation, forming a filter cake for discharge.
Technical Parameters
Model | Capacity (T/H) | Motor Power (kW) | Air Compressor Power (kW) | Belt Width (mm) | Slurry Feed Concentration (%) | Output Concentration (%) | L*W*H (mm) |
TXYL500 | 0.5-4 | 0.75 | 1.1 | 500 | 3-8 | 25-40 | 4290*900*1840 |
TXYL1000 | 3-6.5 | 1.5 | 2.2 | 1000 | 3-8 | 25-40 | 4790*1400*2040 |
TXYL1500 | 4-9.5 | 1.5 | 3 | 1500 | 3-8 | 25-40 | 4790*1900*2040 |
TXYL2000 | 5-13 | 2.2 | 4 | 2000 | 3-8 | 25-40 | 4790*2400*2040 |
TXYL2500 | 7-15 | 4 | 5.5 | 2500 | 3-8 | 25-40 | 5300*2900*2250 |
TXYL3000 | 8-20 | 5.5 | 5.5 | 3000 | 3-8 | 25-40 | 5300*3400*2250 |
TXYL4000 | 12-30 | 7.5 | 7.5 | 4000 | 3-8 | 25-40 | 5300*4400*2250 |