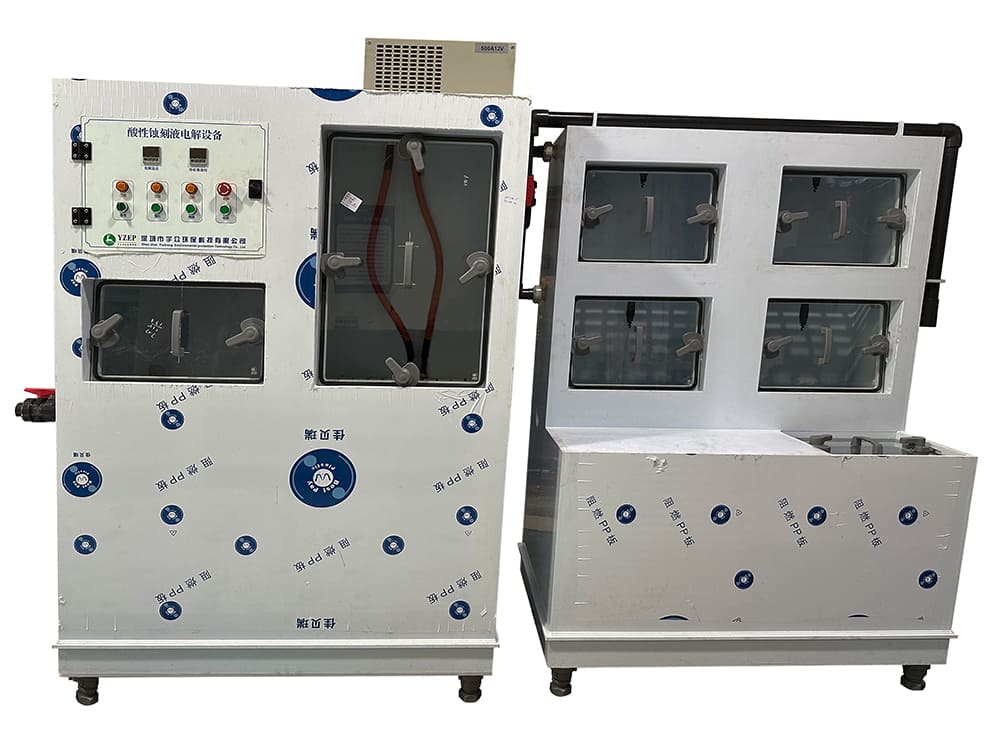
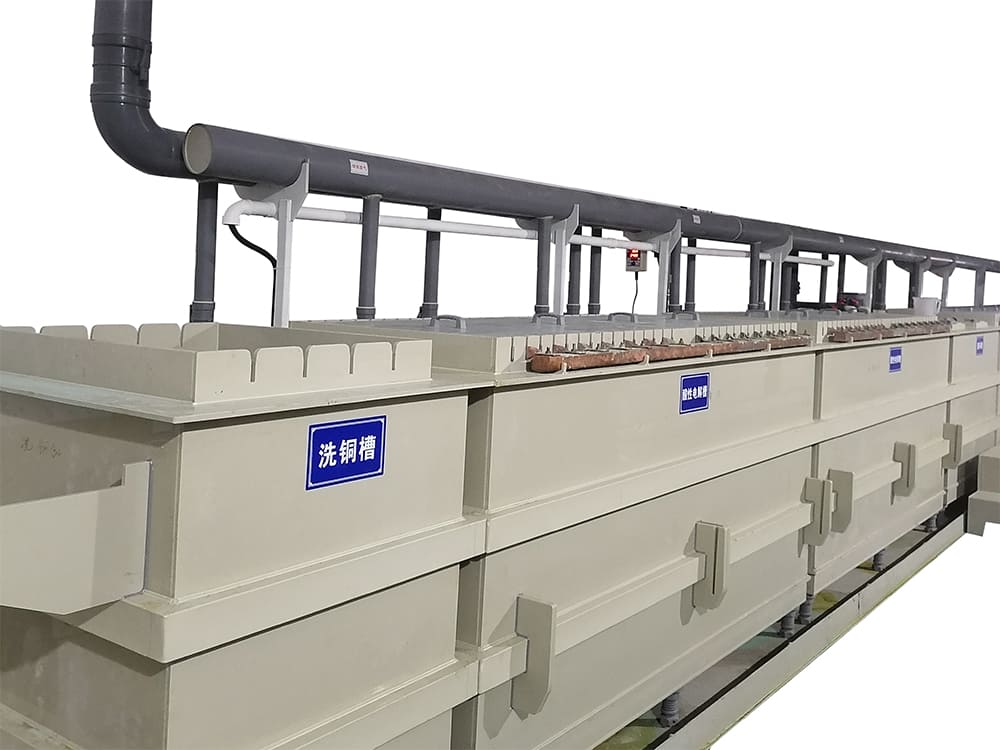
Acid Etching Fluid Recycling And Copper Extraction Equipment
Waste Liquid Treatment Capacity: 0-100 Tons/Month
Copper Production Capacity: 0-10 Tons/Month
Electricity Load: 30-90 kW
The acid etching fluid recycling and copper extraction equipment(system) uses a composite diaphragm electrolysis method to treat waste acid etching fluid with high copper content.
Acid Etching Fluid And Copper Recycling Equipment Overview
The acid etching fluid recycling and copper extraction equipment(system) uses a composite diaphragm electrolysis method to treat waste acid etching solution with high copper content. Through electrolysis, a strong oxidizing gas – chlorine gas is generated in the anode area, which replaces the oxidant and is reused in the etching production line. At the same time, copper ions are reduced to high-purity copper plates through electrodeposition at the cathode. The solution after copper reduction retains the hydrochloric acid and etching salt in the original components of the etching solution. It is adjusted to become a regenerated sub-liquid with stable etching properties and returned to the etching line for recycling.
The acid etching fluid copper recycling system includes:
- Filtration: Removing particulate matter from the used etching solution.
- Chemical Treatment: Adding chemicals to precipitate out impurities and recover copper.
- Separation: Using methods like centrifugation or settling to separate the copper from the solution.
- Purification: Further treatment is needed to ensure the recovered copper meets the required quality standards.
- Recycling: Reusing the cleaned etching fluid or treating it for disposal.
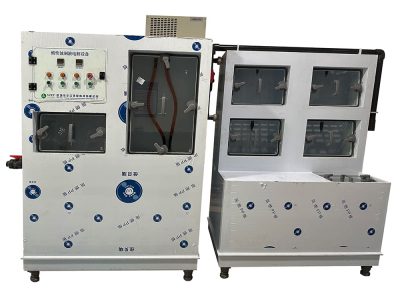

Product/System Features
- The etching liquid regeneration liquid has stable composition parameters, and the etching rate and etching factor after reuse are equivalent to those of the purchased sub-liquid;
- The electrolysis workshop and etching production line have multiple chlorine alarms linked to PLC control. Once there is a chlorine leak, the fire cow will be cut off immediately, the chlorine source will be cut off, and the standby fan will be turned on at the same time;
- The exhaust tower is set with an automatic addition control device, and the sensor probe is calibrated and repaired regularly to prevent the exhaust gas from being discharged substandard;
- The storage containers are all set with double high liquid level sensor alarms to prevent the leakage of the solution;
- The system is set with a five-level exhaust gas absorption treatment to ensure that chlorine and other exhaust gases are completely treated.
Working Principle
Ionic Membrane Electrolytic Copper(IEM) Working Principle
The process of “ionic membrane electrolytic copper” is adopted. In this process, the anode and cathode of the electrolytic cell are separated into two independent regions by the ionic membrane. The anode zone is the waste etching solution regeneration zone, which can generate bivalent copper ions in the waste etching solution after copper reduction through an electrochemical reaction, to regenerate the waste etching solution. The cathode zone is the copper recovery zone. Through the ion diaphragm, the ions in the solution can be selectively migrated, so that the copper ions in the solution can be reduced to copper by electrons.
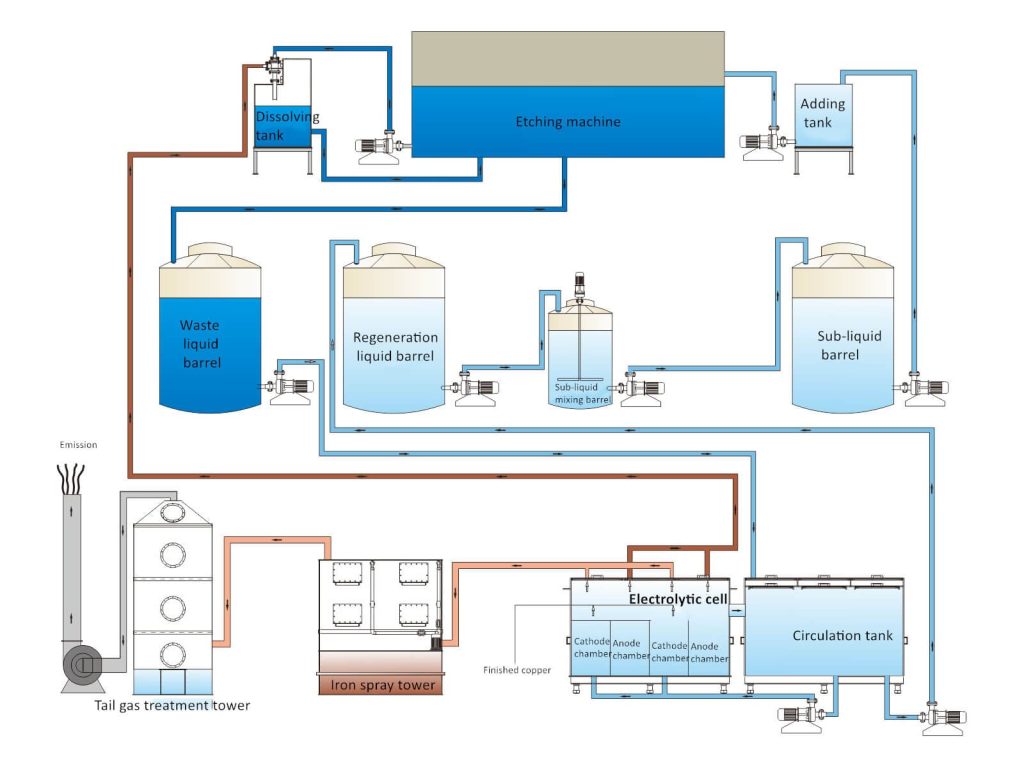
Technical Parameters
Model | Waste Liquid Treatment Capacity (Tons/Month) | Electricity Load (kW) | Copper Production Capacity (Tons/Month) | Occupied Area(m2) |
YZ-SXDJ-10 | 10-50 | 30 | 3 | 30 |
YZ-SXDJ-50 | 50-100 | 60 | 5 | 50 |
YZ-SXDJ-100 | 100 | 90 | 10 | 100 |