Zimbabwe 100 TPH Alluvial Chrome Processing
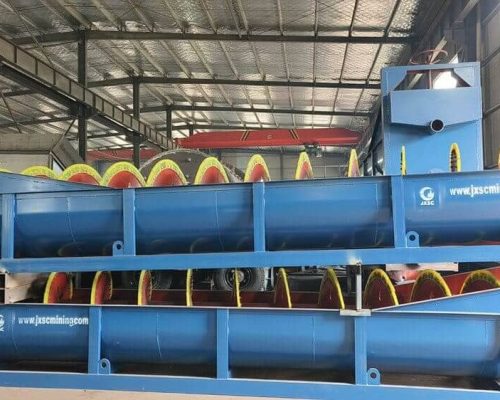
JXSC has provided two successful 100TPH alluvial chrome process plants in Zimbabwe. We design the separation process plant flowchart & plant layout drawing according to mineral ore’s conditions and offer a complete set of plant machines.
100 TPH Alluvial Chrome Processing Project Case
Introduction
Minerals: Alluvial Chrome( mostly soil and clay, mixed with some stones, gravels, and leaf branches.)
Raw Ore Information: Chrome concentrate size <2mm(40-50%); Chrome grade in the raw material is 17-23%; The required target grade after the beneficiation process should be 48-50%; There is some magnetite iron in raw materials, and need to reduce iron to increase Cr/Fe rate.
Capacity: 100 TPH * 2 lines
Process: Feeding -> Washing & Screening -> Gravity Separation -> Magnetic Separation -> Gravity Separation -> Dewatering
Solutions & Process
Alluvial Chrome Process Plant Flowchart
This setup is a 100 tons per hour alluvial chrome ore processing plant.
- Raw materials are unloaded to the raw material hopper by the excavator, then to a vibrating feeder to evenly feed raw material to the rotary scrubber. The vibrating feeder with the grizzly bar, has a gap of 70mm, in the case of big stone in raw materials, so above 70mm big stone can be removed from grizzly feeder.
- The rotary scrubber is used to wash raw materials and screen out waste material above 2mm. The raw materials are mostly soil and clay, so I need to go to the rotary scrubber for washing first. The rotary scrubber has a 2-layer PU screen, mesh size 2 mm and 20mm. 20mm PU screen for protecting 2mm mesh.
- After washing and screening by rotary scrubber, -2mm materials are pumped to rougher spiral chutes, a total of 18 sets. The middling of rougher spirals is pumped to cleaner spirals for further separation to improve the recovery rate. Cleaner spirals are 9 sets. So total spirals are 27 sets.
- All chrome concentrates from rougher spirals and cleaner spirals go on a magnetic separator to reduce some magnetite iron to increase the Cr/Fe rate.
- Chrome concentrate from the magnetic separator is pumped to shaking tables, a total use of 30 sets of shaking tables. Each 15 sets shaking table for one distribution tank. Use the slurry pump to send chrome concentrate to the distribution tank, then the distribution tank distributes slurry to each set shaking table. The shaking table is the final fine separation machine, it can effectively further improve chrome grade in concentrate to meet our customer’s requirement. The middling of all shaking tables is returned to cleaner spirals for separation again to increase the recovery rate. The tailings from shaking tables are sent to the settling pond.
- The chrome concentrate from all shaking tables is sent to a screw dewatering machine for removing mostly water. The underflow of the screw dewatering machine goes to the dewatering screen for further dehydration, so the dewatered concentrate can be transported to the finished product pile by belt conveyor. And the overflow of screw dewatering machines and under-screen slurry is returned to the hydrocyclone by pump, the overflow of the cyclone goes to the settling pond, and the overflow goes to the dewatering screen. That is the whole process for the dewatering system.
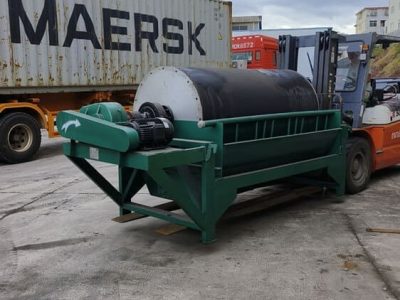
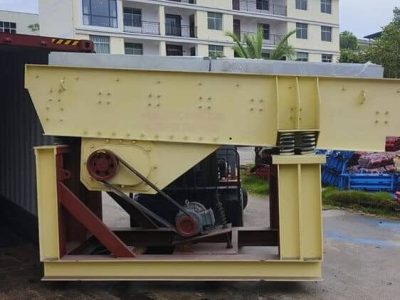
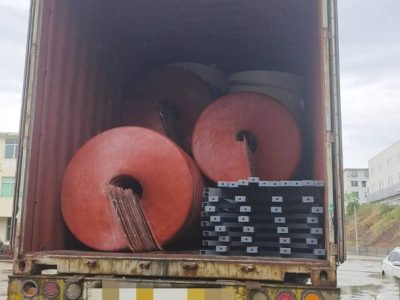
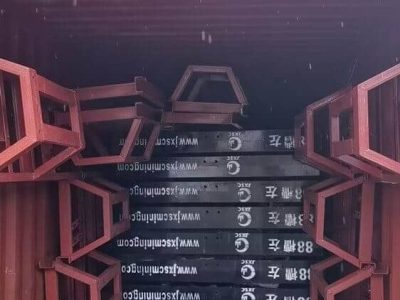