Trinidad 100 TPH Granite Crushing Plant
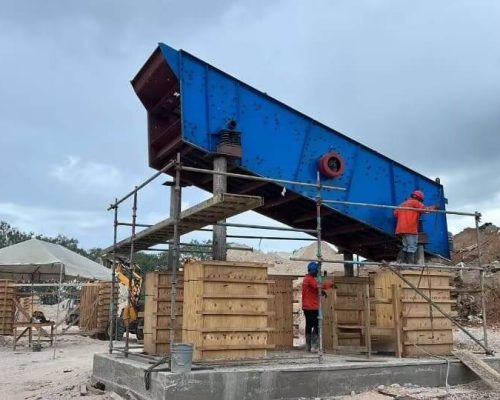
JXSC has provided a successful 100TPH granite crushing plant in Trinidad. We design the crushing process plant flowchart & plant layout drawing according to stone conditions and offer a complete set of plant machines.
100 TPH Granite Crushing Plant Project Case
Introduction
Minerals: Granite
Capacity: 100 TPH
Process: Feeding -> Crushing -> Secondary Crushing -> Screening
Final Product Size Requirements: 0-5 mm, 5-10mm, and 10-20mm.
Solutions & Process
Granite Crushing Plant
This setup is a granite-crushing plant.
The raw material will be sent to a feeding hopper. Raw material sizes can be around 0-500mm. Then the materials go to a vibrating feeder which can work with a 500mm grizzly bar to screen the more than 500mm raw ores. The material less than 500mm will be sent to the jaw crusher to crush to be smaller, around 60-150mm.
Then the materials crushed by the jaw crusher will be sent to a cone crusher crushed to 0-40mm by one belt conveyor. (We generally suggest matching one iron remover above this belt conveyor to remove any iron in the raw material.) We recommend using a cone crusher for a big-capacity plant as the secondary crushing part, like in a situation of more than 50 tons. The crushed materials from the cone crusher will be sent to a vibrating screen with three layers of screen, the mesh size is 5mm, 10mm, and 20mm.
The sizes of more than 20mm will be sent back to the primary jaw crusher to crush again. A vibrating screen will screen out 3 final products and convey them to different stockpiles.
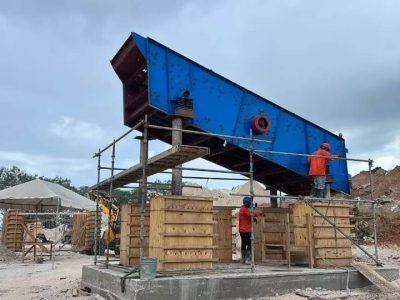
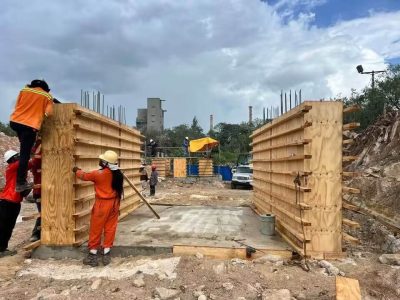
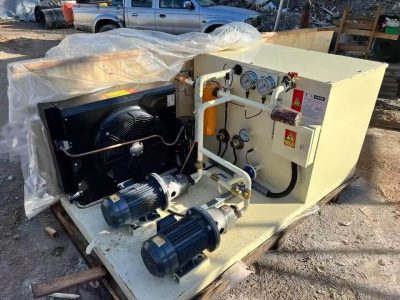