Tanzania 200 TPH Magnesite Process Plant
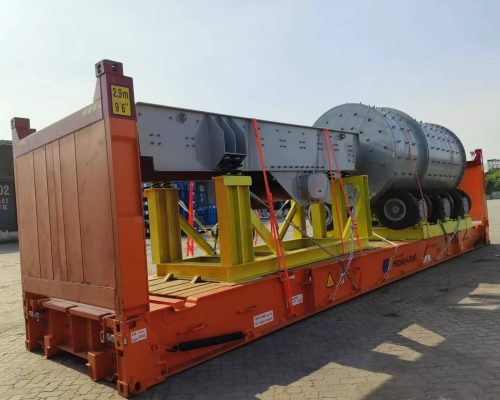
JXSC has provided a successful 200 TPH magnesite washing and screening in Tanzania. We design the separation process plant flowchart and plant layout drawing according to the mineral ore’s conditions and offer a complete set of plant machines.
Magnesite Process Plant Project Case
Introduction
Minerals: Magnesite ore with sticky clay
Feeding Size: 0-300 mm
Capacity: 200 TPH
Final Product Requirement: 4-50mm, 50-100mm, 100-150mm
Process: Feeding -> Washing -> Screening -> Washing
Solutions & Process
Magnesite Washing And Screening Process Plant Flowchart
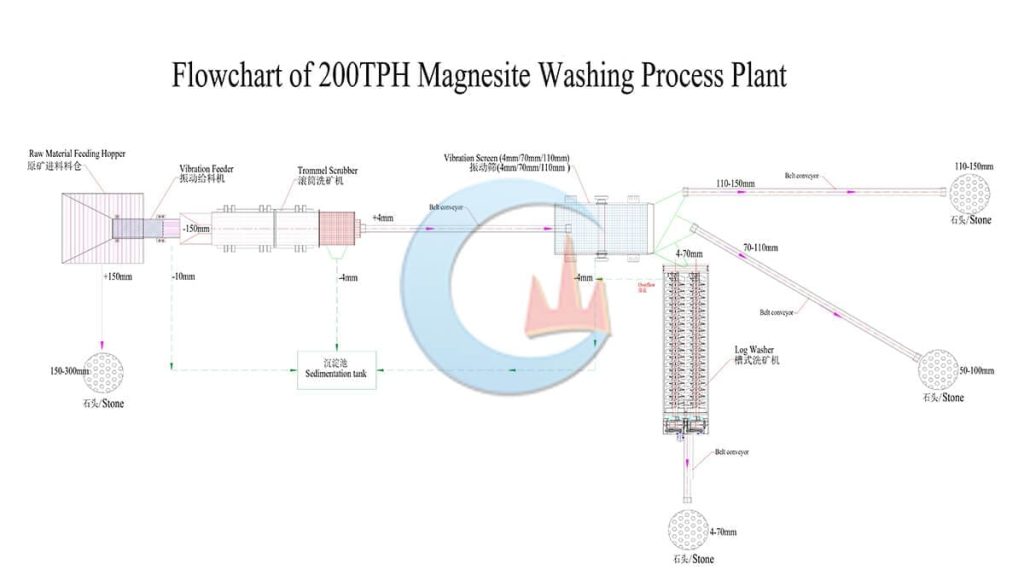
This setup is a 200-ton-per-hour magnesite ore-washing process plant. It is configured with a vibration feeder, trommel scrubber, vibration screen, log washer, etc. The process is as follows:
The raw material is fed by a tipper truck or excavator into a grizzly hopper with a grizzly bear with a gap of 150 mm. Over-grizzled material larger than 150 mm is stacked nearby and under-grizzled material smaller than 150 mm enters the vibratory feeder.
The vibratory feeder also has a grizzly bear with a clearance of 10 mm. 10-150 mm of material enters the rotary grit screen for scrubbing, while debris smaller than 10 mm flows to the settling tank for water recycling.
This rotary scrubber‘s washing efficiency is very high. Its screening section has two layers of polyurethane with screen sizes of 4 mm and 20 mm (the 20 mm screen protects the 4 mm screen). The under-screen material (less than 4 mm) goes into the same settling tank, and the top-screen material (4-150 mm) is conveyed to the vibrating screen.
The vibrating screen is used for further accurate screening and is divided into 3 decks of 4 mm, 50 mm, and 100 mm. The under-screened material of 4-50 mm goes to the log washer, while the intermediate sizes of 50-100 mm and the oversized material of 100-150 mm are conveyed to a separate yard.
The log washer is used to re-wash the 4-50 mm material for a cleaner end product.
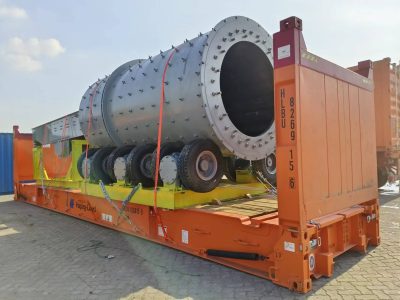
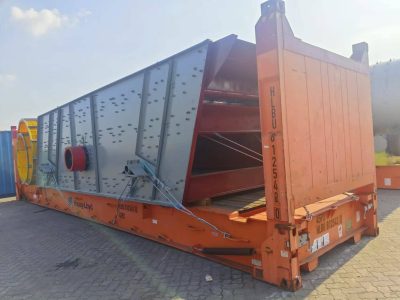
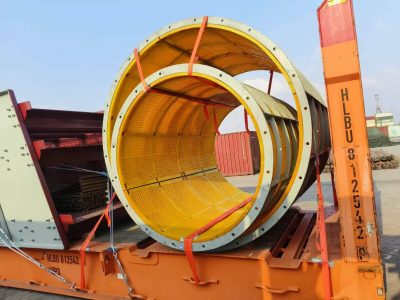
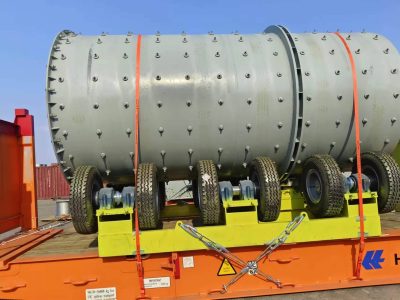