South Africa 100TPH Diamond Washing Plant
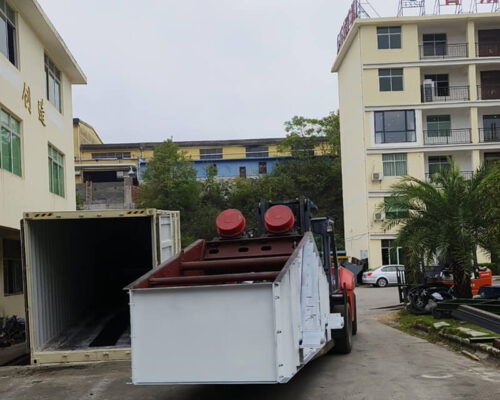
JXSC has provided a successful 100TPH diamond washing plant in South Africa. We design the ore process plant flowchart & plant layout drawing according to ore conditions and provide a complete set of plant machines.
100TPH Diamond Washing Plant Project Case
Introduction
Minerals: Diamond
Capacity: 100 TPH
Ore Condition: Contains a lot of slime
Process: Feeding ->Washing -> Screening
Solutions & Process
Diamond Washing Plant
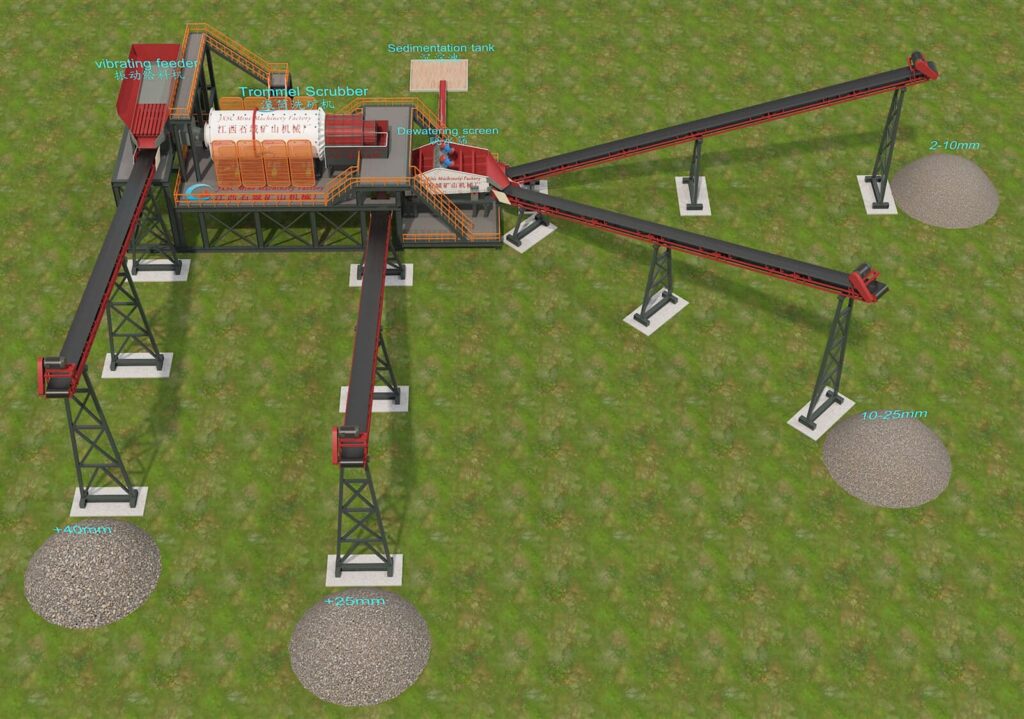
This setup is a 100tph diamond wash plant consisting of a grizzly vibrating feeder, trommel scrubber, high frequency vibrating screen, belt conveyor, and storage bin.
The whole setup is a fully steel structure frame, designed with three operation platforms, each platform comes with an aisle and stairs. Each platform has an Integral modular design, which makes installation work very easy after customers receive the plant.
The customer’s diamond ore conditions are as follows:
- Raw ore contains much sticky clay and needs strong washing.
- Diamond particle size range is 2-25mm.
- The processing capacity required is 100tph.
- The maximum feeding size of raw ore is 150mm, which requires a vibrating feeder with a 40mm grizzly bar to remove above 40mm big waste stone.
- The diamond minerals must be sieved 2-10mm and 10-25mm after washing.
- Final products 2-10mm, 10-25mm, and 25-40mm need to go to a storage bin by belt conveyor.
We designed this setup according to these ore conditions to meet customer requirements. The whole processing flow is as follows:
Firstly, the vibrating feeder comes with a 40mm grizzly bar, to remove over 40mm of big waste stone. Use a loader or excavator to feed raw ore into a grizzly feeder, below 40mm go into a trommel scrubber for strongly washing clay.
Secondly, a Trommel scrubber with two decks PU screen 2mm&25mm, after washing clay, it sieves out 0-2 mm slurry going to settling pond, 2-25mm going to high frequency vibrating screen, 25-40mm going to the storage bin by belt conveyor.
Thirdly, 2-25mm from the trommel scrubber goes to a high-frequency vibrating screen for further washing and screening out 2-10mm and 10-25mm products. The HFV screen has two decks PU screens 2 mm and 10mm. The two products 2-10mm and 10-25mm are sent to a storage bin by belt conveyors.
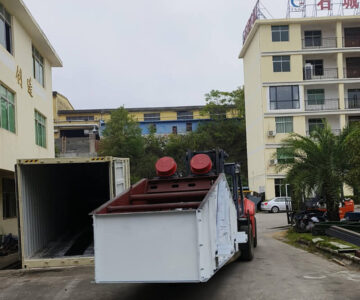
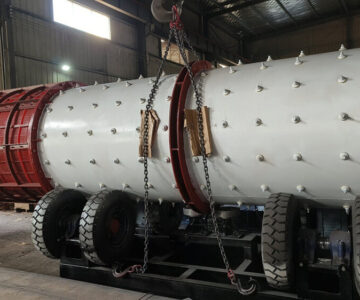
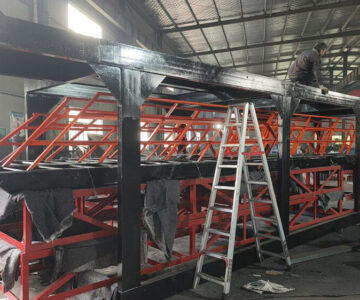