The fiery new energy vehicle market has led to a rapid increase in the demand for power batteries. The demand for lithium resources, which is a key raw material for power batteries, is also growing. The explosive demand makes lithium resources in an urgent situation of short supply, and the price of lithium mines is also increasing. It is imperative to increase the development of lithium mines.
Uses of Lithium Metal
- Used as a coolant in nuclear fusion or nuclear fission reactors. Because metallic lithium has large heat capacity, wide liquidus temperature range, high thermal conductivity, low viscosity, and low density.
- Lithium and its compounds have the characteristics of high combustion, fast speed, wide flame, and large calorific value. They are often used as high-energy fuels for rockets, aircraft, or submarines.
- The lens made of lithium fluoride crystal is installed on the astronomical telescope. Because lithium fluoride has the highest transparency to ultraviolet rays, astronomers can use it to gain insight into the mysteries hidden in the deepest part of the Milky Way.
- Lithium is also an essential raw material for high-energy manufacturing batteries. Lithium power batteries have the characteristics of high energy density, high working voltage, and low self-discharge rate, and are ideal materials for power batteries.
Lithium ore is a lithium resource that is naturally formed and can be mined economically. It is the lightest metal in the world. The primary raw materials for lithium ore beneficiation come from three categories: spodumene, lepidolite, and lepidolite. The Uyuni Salt Flats in Bolivia, South America, Chile, China, and Argentina have the largest lithium mine production capacity.
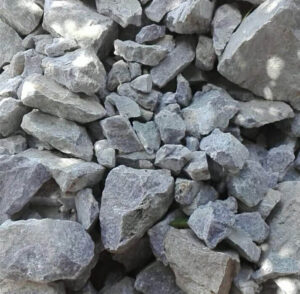
Lithium Ore Beneficiation Process
The mineral properties of lithium ore determine that lithium ore beneficiation can be separated by hand separation, flotation, chemical-flotation combined method, radioactive separation method, etc. Flotation is currently the most widely used lithium ore separation method in lithium ore concentrators. The leading equipment is the crusher, ball mill, jig separator, flotation machine, etc.
Manual selection
The preferred method is suitable for raw ore types such as spodumene and beryl, which have large crystals and are easily selected by hand. It is currently the primary lithium ore beneficiation process in developing countries, but it will gradually be replaced by machinery as society progresses.
Flotation method
Lithium ore separation by flotation is the progress of mechanized separation. Different flotation methods are set according to the different types of lithium ore. For example, spodumene can be used in positive flotation or reverse flotation. Lepidolite is easy to float, and positive flotation is commonly used. Lithium ore flotation agent selection: three alkalis: Na2CO3, Na2S, and NaOH.
The primary method of lithium ore positive flotation is: Add sodium hydroxide to the pulp at the beginning for stirring and scrubbing to remove surface pollutants. After desliming and ore washing, subsequent treatments are divided into three categories:
1. First pumice mica, then pumice spodumene, and finally pumice feldspar.
The steps are:
- In a weakly acidic medium, use cationic pumice.
- Concentrate the flotation tailings to 50% solids, mix with oleic acid collectors and alcohol foaming agents, dilute to 17% solids, and use pumice spodumene.
- After the spodumene-floated tailings are treated with hydrofluoric acid, a cationic collector is added to float the feldspar.
2. First pumice spodumene, then pumice mica, and then pumice feldspar.
The steps are:
- Concentrate the pulp to 64% solids, stir with oleic acid, sulfuric acid, and foaming agent, then dilute to 21% pumice spodumene.
- Mica in spodumene flotation tailings is floated out with a cationic collector.
- Mica flotation tailings are added with hydrofluoric acid to activate feldspar, and cationic collector pumice feldspar is added.
3. Spodumene and mica are mixed for flotation, and finally pumice feldspar.
The steps are:
- Add sulfuric acid to the thick slurry to adjust, then add an anion collector to float mica and spodumene.
- The mixed concentrate is stirred in the acidic medium to float mica and iron-containing minerals, and the product in the tank is spodumene.
- After mixing the tailings after flotation, add hydrofluoric acid to treat them, and then use cationic collector pumice feldspar.
The above processing process of lithium ore requires grinding machines, such as ball mills and other grinders. Our company is a manufacturer of grinding equipment. Our equipment is mainly used in the grinding and processing hard rock lithium in lithium ore resources. At present, lithium resources in salt lake brine have been depleted day by day. Extracting lithium from pegmatite ores has become essential for obtaining lithium resources. There are many ways to extract lithium minerals from this type of ore, such as sulfuric acid roasting, sulfate, chlorination, etc. However, ore grinding is the critical link that cannot be lost before extraction. Our company’s vertical, European, and ball mills can be applied to the grinding process of lithium ore, and each has its own advantages.
Lithium Ore Grinders
European Mill
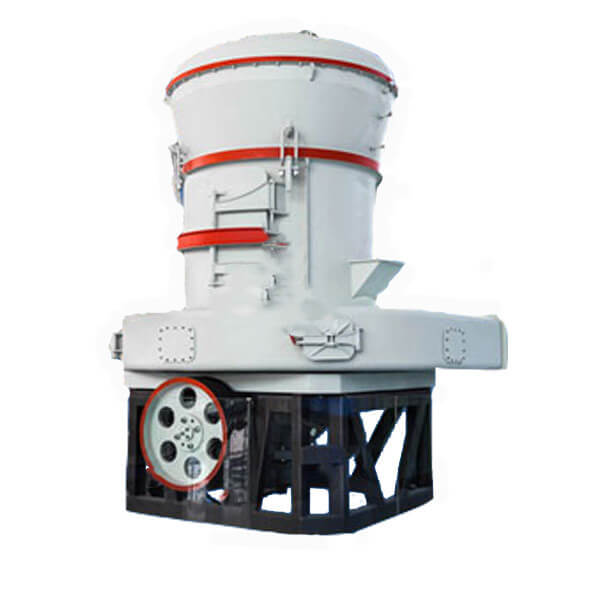
- Novel design and reasonable structure
- Small footprint and low power consumption
- long operating life
- Low cost of wearing parts
Vertical Mill
- Integrates crushing, drying, grinding, grading, and conveying.
- Compact layout, small footprint.
- The whole machine works under sealed and negative pressure, no dust spillage.
- Increase the size of the grinding force through hydraulic boosting, increase the output and improve the grinding efficiency.
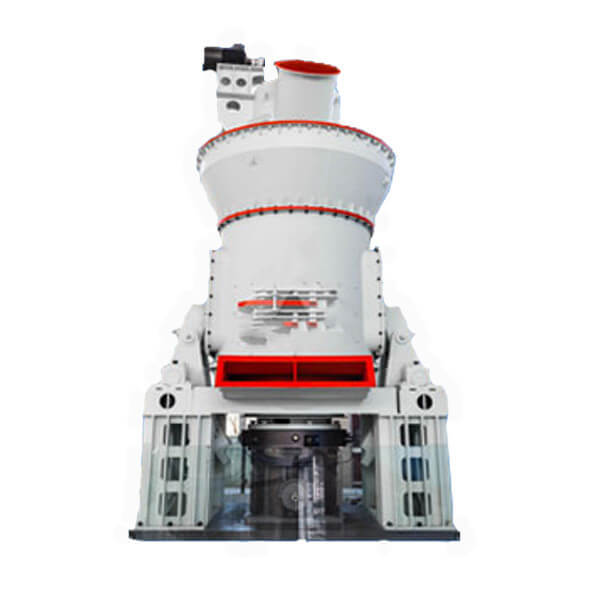
If you are finding mining grinders or mills, please contact us. We will give you the best grinding mill machine journey.