Ore screening(mineral screening or ore sieving) is a process in mineral processing and mining operations where raw or crushed ore is separated into different size fractions or grades based on particle size.
Ore Screening Purpose
Ore screening primarily aims to classify the ore into various size ranges to facilitate further processing, improve ore quality, and ensure that only the desired size fractions are subjected to subsequent beneficiation processes.
Key Aspects of Ore Screening
Particle Size Classification
Ore screening involves separating the ore particles into different categories or size classes. This is typically done by passing the ore through a vibrating screen or sieve with various-sized openings or mesh. The mesh size or screen openings are chosen based on the final product’s desired size distribution and the downstream processes’ specific requirements.
Types of Screens
Various screens can be used in ore screening, including vibrating, trommel, and grizzly screens. Each type has its advantages and is chosen based on the characteristics of the ore and the screening requirements.
Importance in Ore Processing
Proper ore screening is essential in ore processing as it helps to:
- Separate oversized or undersized particles that may cause processing issues or inefficiencies.
- Prepare the ore for subsequent processing steps, such as crushing, grinding, and beneficiation.
- Optimize the yield of valuable minerals by ensuring that the desired size fractions are targeted for further treatment.
Efficiency and Product Quality
Effective ore screening can improve the overall efficiency of ore processing plants and result in a higher-quality final product. It helps maximize the recovery of valuable minerals while minimizing the processing of unwanted material (gangue).
The choice of screening equipment and the specific screening process depends on factors such as the ore’s characteristics (particle size distribution, moisture content, and mineral composition), the required product specifications, and the overall ore processing flow. Proper ore screening is critical in mineral processing operations to ensure efficient and cost-effective ore beneficiation.
Ore Screening Machines
Ore screening machines, also known as mineral screening equipment or ore sieving machinery, are specialized machines used in the mineral processing and mining industry to separate raw or crushed ore into different size fractions based on particle size. These machines are crucial in classifying and preparing ore for further processing. There are several types of ore screening machines commonly used:
Vibrating Screens
Vibrating screens are the most widely used ore screening machines. They consist of a vibrating deck with screens or mesh of various sizes. The vibration of the screen deck helps separate ore particles based on size. Vibrating screens are versatile and can be used for dry and wet screening.
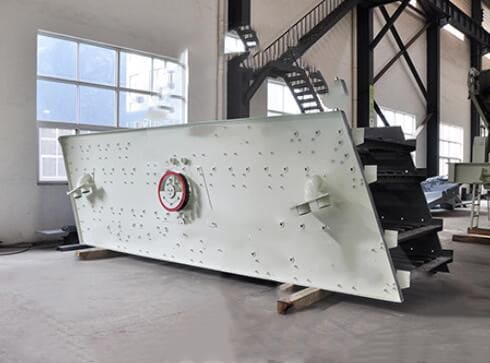
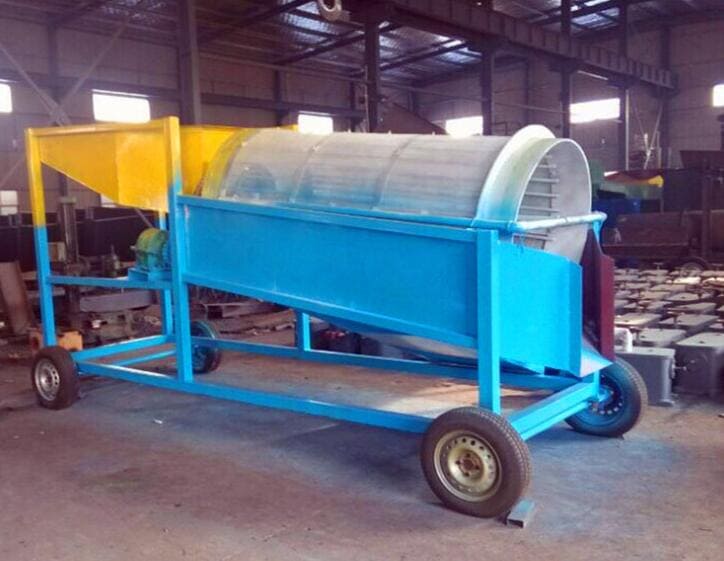
Trommel Screens
Trommel screens are cylindrical, rotating screens with holes or slots of varying sizes along the length of the drum. They are often used for preliminary ore screening and are effective for separating material, mainly when dealing with sticky or clay-rich ores.
Grizzly Screens
Grizzly screens consist of parallel bars or rails at the feed end of a conveyor or vibrating feeder. They are primarily used to remove oversized particles or rocks from the ore stream before they enter the primary processing equipment.
High-Frequency Screens
High-frequency screens are specialized vibrating screens designed to operate at higher frequencies, providing better control over particle separation. They are used for fine screening and can improve overall screening efficiency.
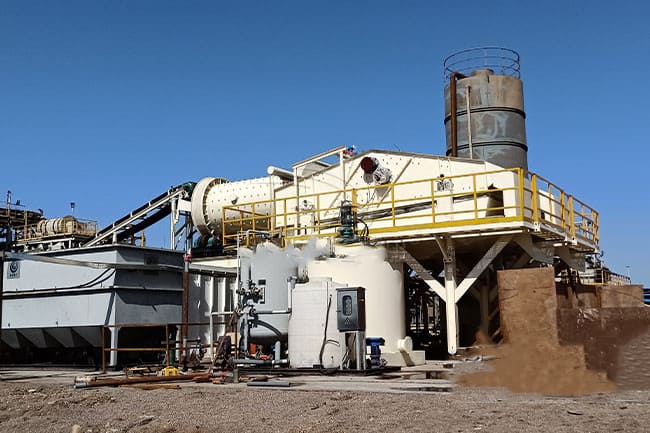
Flip-Flop Screens
Flip-flop screens can handle difficult-to-screen materials like moist, exemplary, or sticky ores. They employ alternating motion to prevent clogging of the screen openings.
Inclined Screens
Inclined screens have a sloped deck that helps to improve screening efficiency and material flow. They are often used for screening in various stages of the ore processing circuit.
Multi-Deck Screens
Multi-deck screens consist of multiple screen decks stacked on each other. They are used to separate the ore into several size fractions simultaneously.
Static Screens
Static screens are simple, stationary screens with fixed openings. They are used for basic sizing and scalping operations.
The choice of the appropriate ore screening machine depends on various factors, including the ore’s characteristics (particle size distribution, moisture content, and mineral composition), the desired product specifications, and the specific requirements of the ore processing circuit. Additionally, throughput capacity, efficiency, and maintenance requirements play a role in selecting the correct screening equipment for a particular mining or mineral processing application.
Ore screening machines play a crucial role in mining by efficiently separating valuable minerals from waste material. These machines have evolved to become more advanced and effective, with various types available to suit different mining operations. They provide numerous benefits such as increased productivity, reduced operating costs, and improved product quality. However, mining companies must choose the right screening machine for their needs and ensure proper maintenance to maximize its performance and longevity. By investing in high-quality ore screening machines and implementing best practices, mining companies can optimize their operations and achieve greater success in extracting valuable minerals from ore.