Graphite is an allotrope of the element carbon with a unique crystal structure and physical properties that make it widely used in multiple industrial and scientific fields.
Graphite Main Applications
Graphite has many applications in the refractory industry, mainly due to its unique properties, such as high-temperature stability, thermal conductivity, and corrosion resistance. The following are the main applications of graphite in the refractory industry.
- Graphite electrode: Graphite electrode is one of the most common applications in the refractory industry. They are used in metallurgical processes in electric arc furnaces, such as steel and aluminum production. Graphite electrodes have excellent electrical conductivity and high-temperature stability, allowing them to withstand extreme furnace temperatures and chemical environments.
- Graphite heat exchanger: Graphite heat exchanger transfers heat in high-temperature and corrosive environments. They are commonly used in the chemical industry to help control and regulate temperature.
- Graphite seals: Due to the corrosion resistance and high-temperature resistance of graphite, it is often used to make seals, such as graphite gaskets and graphite washers, to ensure the sealing of containers and pipes.
- Graphite bricks and blocks: Graphite bricks and blocks are commonly used for lining high-temperature kilns, crucibles, and other heat treatment equipment. They resist high temperatures and corrosion and can withstand extreme thermal stresses.
- Graphite thermally conductive material: Graphite thermally conductive material is used to manufacture high-temperature thermocouple protection sleeves and thermal conductive parts to ensure the accuracy and long life of the temperature sensor.
- Graphite ceramic composites: Graphite and ceramic composites combine the conductivity of graphite with the wear resistance of ceramics and are used to make high-performance bearings, seals, and other wear-resistant parts.
Flake graphite is widely used in the metallurgical industry to produce graphite crucibles and magnesia carbon bricks.
1. Magnesia carbon bricks
The quality index requirements for graphite of magnesia carbon bricks generally include particle size (mesh), fixed carbon, ash, volatile matter, and moisture. High-quality refractory bricks use flake graphite with high carbon content and better performance than earthy graphite, medium carbon, and high carbon products with a 90% to 97% carbon content and particle sizes of -80 to +200 mesh. The trend is towards using finer particle size grades and flake graphite with high carbon content. Increasing the amount of graphite added to magnesia carbon bricks can enhance the strength and oxidation resistance by improving the purity of graphite.
2. Graphite crucible
Graphite crucible has a long history of application in the metallurgical industry. It is made of natural large flake graphite, high-quality silicon carbide as raw materials, and clay or carbon as a binding agent. The proportion of graphite in the crucible raw material formula accounts for Between 40% and 50%.

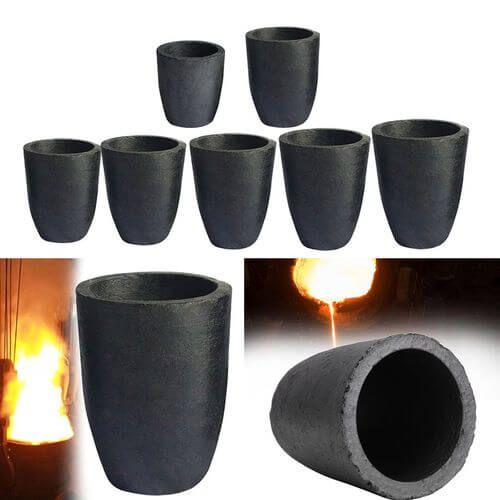
3. High purity graphite
Compared with natural graphite materials, the carbon content in high-purity graphite is greater than 99.9%. In some particular fields, such as those used in high-tech industries such as nuclear energy and semiconductors, the rate is 99.99% or even higher.
4. Flexible graphite
Flexible graphite has been widely used in petroleum, the Chemical industry, metallurgy, and other fields.
5. Expandable graphite
- Small particles of expandable graphite are used to produce flame-retardant coatings;
- Graphite with a high initial expansion temperature is used for flame-retardant engineering plastics and rubber;
- Graphite with a low initial expansion temperature is used to produce fireproof sealing strips;
- Micro-expanded graphite is used as a high-energy battery Material.
6. Colloidal graphite
Colloidal graphite is widely used in electrical conductivity, electromagnetic shielding, antistatic, forging, casting, wire drawing, lubrication, sealing, screen printing circuits, color display manufacturing, and other fields.
7. Lithium-ion battery anode materials
The currently mature and used negative electrode materials for lithium-ion batteries are mainly carbon graphite. To be used as the negative electrode material for lithium-ion batteries, natural flake graphite must undergo particle spheroidization and surface coating. Spheroidization technology primarily uses special crushing and shaping equipment to make irregular graphite particles collide with each other under the impact of airflow, causing curling and wrapping so that the particles become spherical or nearly spherical, which is commonly known as spherical graphite. Spherical graphite has a small specific surface area and can easily achieve uniform orientation when stacked, improving material performance. Surface coating technology mainly aims at the shortcomings of natural graphite particles having many active points on the surface and being prone to side reactions with the electrolyte. The surface of the graphite particles is covered with a thin layer of amorphous carbon with a stable structure to improve stability.
8. Isotropic graphite materials
Isotropic graphite material (nuclear graphite) products refer to fine-structured and ultra-fine-structured graphite formed by isostatic pressing using natural graphite and petroleum coke as the primary raw materials. The products are bulk artificial graphite products. Its main products are:
- Graphite reflection blocks for high-temperature gas-cooled reactors.
- Graphite balls for high-temperature gas-cooled reactor spherical reactors.
- Nuclear-grade graphite gaskets.
- Electrode graphite powder for high-temperature gas-cooled reactors.
9. High thermal conductivity graphite material
The gradual miniaturization, compact structure, and high power density of high-power-density electronic devices and high-end electronic industrial devices have caused heat dissipation problems, posing severe challenges to the working stability and reliability of the devices, thereby increasing the heat generated during their operation. Strengthening exports and dispersion puts forward higher requirements. Currently, the heat sink base materials used in general heat dissipation (such as high-end civilian electronic devices, chip materials for LEDs, heat exchangers for industrial machines, etc.) are almost all aluminum alloys. Due to their thermal conductivity (237W/m·K), It is challenging to meet the requirements due to its limitations, and this type of material is heavier and has a larger thermal expansion coefficient, which greatly limits its widespread use as a heat dissipation material for electronic device packaging. Because of this, research and development of new materials with high thermal conductivity, lightweight, and good thermal stability are significant in achieving miniaturization of components, lightweight devices, and efficient operation.
The successful development of high thermal conductivity graphite materials provides the most effective way to solve the heat dissipation problem of high-power electronic devices. Since this type of material is light in weight (only 1/2 to 1/5 of traditional metal thermal conductive materials), has high thermal conductivity, is corrosion-resistant, and has a small thermal expansion coefficient, it is not only beneficial to electronics to replace traditional metal materials in the aforementioned devices that require heat dissipation. The miniaturization and high power density of the device can effectively reduce the weight of the device and increase the payload; at the same time, it is used in my country’s high-end electronic devices and equipment, and can also efficiently dissipate heat, be safe to use, and have a long life (mainly its Strong resistance to corrosion and oxidation).
10. Graphite for the foundry industry
Use graphite as casting mold coating to increase the smoothness of castings and reduce cracks and pores in castings. The requirements for graphite raw materials generally have a particle size of 74 μm and a carbon content of 70% to 80%.
11. Graphite for the electrical industry
Use graphite to make electrodes, brushes, carbon rods, carbon tubes, anode plates, graphite gaskets, lithium-ion power batteries, etc. Graphite raw materials require a particle size of 43 μm and a 94% to 97% carbon content.
12. Fluorinated graphite
Fluorinated graphite is a 10μm-12μm ultra-fine powder material of (C2F)n and (CF)n. The main producing and consuming countries are developed countries, such as Japan, the United States, Russia, France, and Germany. Main uses: solid lubricants, fluorinated glass release agents, high-energy battery materials, fluorine graphite fiber materials, computer, and integrated circuit memory materials.
Graphite’s various properties make it a key material in many fields, helping improve equipment performance, reduce energy consumption, extend equipment life, and support scientific research and technological innovation. People’s use of graphite determines its mining value. If you are a mineral owner or investor and want to know how graphite is beneficial, please get in touch with our technical team.