Tin ore is one of the important strategic mineral resources, and tin and tin alloys have been widely used in modern national defense, industry, cutting-edge science and technology and human life. At present, common tin ore beneficiation processes mainly include gravity separation, flotation and magnetic separation. The raw ore is washed and deslimed, crushed and screened, pre-separation, and then processed by one or more sorting equipment such as gravity separation equipment, flotation machine, and magnetic separator, the end result is a tin concentrate with ideal grade and recovery. The following mainly explains the different tin ore beneficiation processes and the required beneficiation equipment.
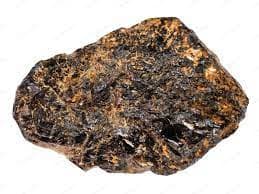
Tin ore has the characteristics of strong development, rust resistance and corrosion resistance. Tin can form various alloys with other metals and metals, and is easy to be plated on many metal surfaces. In particular, the surface of tin is corrosion-resistant and nontoxic.
I. Gravity separation
At present, the vast majority of tin concentrates come from cassiterite deposits, and the density of cassiterite is higher than that of co-existing minerals. Therefore, gravity separation has become one of the main beneficiation processes for tin ore, and is often used to separate tin sand ores. The gravity separation of cassiterite is generally the separation of ore sand. Generally, the multi-stage grinding and multi-stage separation process is adopted, which can realize the principle of early dissociation, early recovery and early tailing, and avoid excessive crushing caused by unevenly embedded cassiterite.
Since cassiterite will produce slime in the crushing and grinding stage, classification desliming is an important preparatory operation before cassiterite re-selection, which can control the selected size while removing the interference of ore slime. Generally, equipment such as washing machine, cross-flow belt chute, and small-diameter cyclone are used as cassiterite desliming equipment. The commonly used gravity separation equipment for tin ore mainly includes jig concentrator and shaking table.
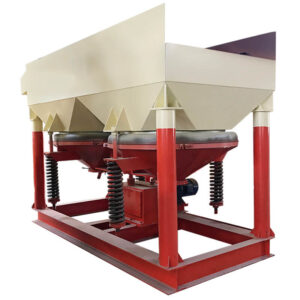
A. The jig Concentrator will mix mineral particles of different specific gravity, stratified by specific gravity in a vertically moving, variable-speed media stream. Minerals with low specific gravity are located in the upper layer, and minerals with large specific gravity are located in the lower layer. Using the action of machinery and water flow, the layered materials are discharged separately.
For sand tin ore with high monomer dissociation degree, it only needs to go through simple screening to screen out large pieces of tin-free waste rock, and then gravity separation by jigger to obtain good sand tin beneficiation index. The jig machine is especially suitable for sorting coarse mineral particles (mineral raw materials of any size except fine materials). For sand-tin beneficiation, under the premise that the specific gravity difference is ≥1.25 and the ore monomer is dissociated, the lower limit particle size can reach 0.04mm, the process operation is simple, the selected particle size is large, and the selected particle size is wide. The equipment has a large processing capacity, and it has a good effect in the sand tin mine with a high degree of monomer dissociation.
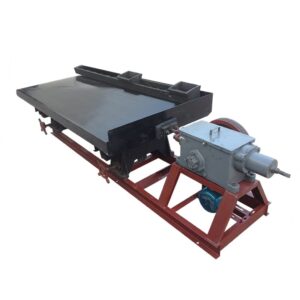
B. Shaking table is a kind of tin ore beneficiation equipment for beneficiation in horizontal medium flow. It mainly uses the transmission mechanism to drive the bed surface to do longitudinal reciprocating motion, and perform rush flow and bed surface differential motion. During the reciprocating motion, the ore particles undergo the layering action perpendicular to the bed surface and the separation action parallel to the bed surface, so that materials of different particle sizes are discharged from different sections of the bed surface to realize separation.
For sand tin ore with low monomer dissociation degree, it is difficult to obtain ideal concentrate grade and beneficiation recovery rate by simple screening-gravity separation process. Generally, a multi-stage grinding-multi-stage gravity separation process is required to improve the beneficiation index.First, the large waste rocks are screened out by screening, and then the coarse concentrate is obtained by gravity separation by jig, and then the coarse concentrate is rod-milled to break the conjoined structure, and then the jig is used for gravity separation. Since part of the over-ground tin ore cannot be completely recovered on the jig during the rod grinding process, the tailings of the second-stage jig need to be re-selected by shaking table. In the gravity separation equipment, the shaking table is particularly suitable for processing and sorting minerals with finer particle size, so it can be used to recover the fine-grained cassiterite present in the tailings, thereby improving the recovery rate.
II. Flotation separation
Due to the low separation efficiency of cassiterite gravity separation for tin minerals with a particle size below 19 μm, flotation has become one of the important ways to recover fine-grained tin minerals. However, the fine particle flotation of cassiterite also has problems such as large surface area of ore particles and large consumption of chemicals. At present, there are two methods to improve the effect of fine-grained cassiterite flotation: one is to pretreat fine-grained tin minerals before flotation; the other is to use effective flotation reagents and equipment combinations.
It is worth noting that the fine particle flotation of tin ore has problems such as large surface area of ore particles and large consumption of chemicals. Currently, we can pre-treat fine-grained tin minerals prior to flotation, or use an effective combination of flotation reagents and equipment to improve cassiterite fine-grained flotation.
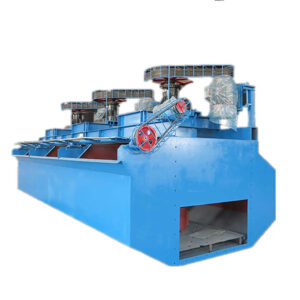
III. Magnetic separation
Since some tin ores often contain various iron oxide minerals (such as magnetite, hematite and limonite, etc.), tungsten ore and other symbiotic minerals, these minerals cannot be very good with cassiterite by flotation and gravity separation to separate. Therefore, magnetic separation is often used in the washing process to realize the separation of tin and iron. The magnetic separation of tin ore is mainly wet strong magnetic separation, which is used for raw ore, secondary concentrate and concentrate before entering the gravity separation operation. However, a dry magnetic separation process is often used to separate tungsten and tin minerals. Commonly used magnetic separation equipment includes wet magnetic separator and dry magnetic separator.
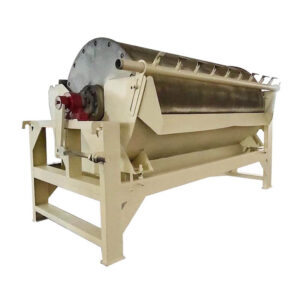
A. The wet magnetic separator is a wet permanent magnetic separator widely used in the separation of strong magnetic minerals. According to different uses and sorting conditions, each series of wet magnetic separators have different magnetic system designs and tank structures. The large wrap angle magnetic system of the wet magnetic separator can increase the length of the separation belt and the number of magnetic inversions, and realize the efficient separation of magnetic minerals and non-(weak) magnetic minerals.
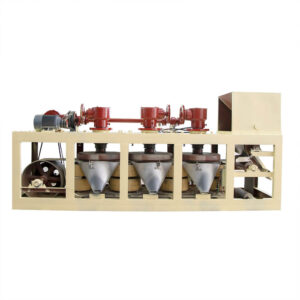
B. Dry magnetic separators are often used to separate tungsten ore coexisting with tin ore. The main minerals of tungsten and tin are relatively dense, and wolframite, scheelite and cassiterite are generally accumulated in the rough concentrate. Among them, the coarse-grained materials can be operated by a dry strong magnetic separator to separate wolframite from cassiterite and scheelite, and then separate cassiterite and scheelite by electric separation.
Generally speaking, in the actual beneficiation process, the selection of tin ore beneficiation process and equipment is often determined according to various factors such as the nature of tin ore, dressing plant conditions, and investment budget. If you want to separate tin ore more economically and environmentally, you should first conduct a beneficiation test, comprehensively analyze the properties of the ore, and obtain a scientific beneficiation test report. In order to judge which tin ore beneficiation process and the specific type and model of tin ore beneficiation equipment to use, in order to achieve an ideal return on investment.
Relation case
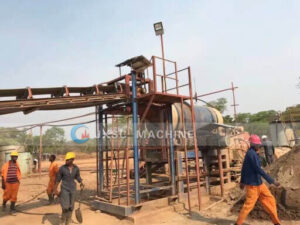
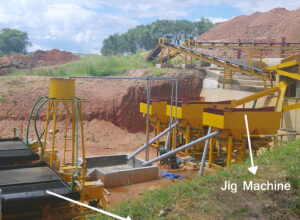