A Ball mill is very common grinding equipment in mineral processing applications. The grinding principle is to use the friction between the material and the steel ball or the steel column and the rotating form of the drum to promote the material to reach the ideal particle size standard. This standard is used to facilitate the classification and flotation operations in the subsequent beneficiation process. Then, the very important grinding equipment in the beneficiation equipment, the ball mill bears the heavy responsibility of grinding. If there is a slight error, the consequences will be great, so as the central link of the ball mill grinding operation, is there any operation that must be emphasized? method? As long as you master the nine-character secret of “uniform ore feeding, large sand return, and high concentration”, the most ideal grinding effect can be achieved.
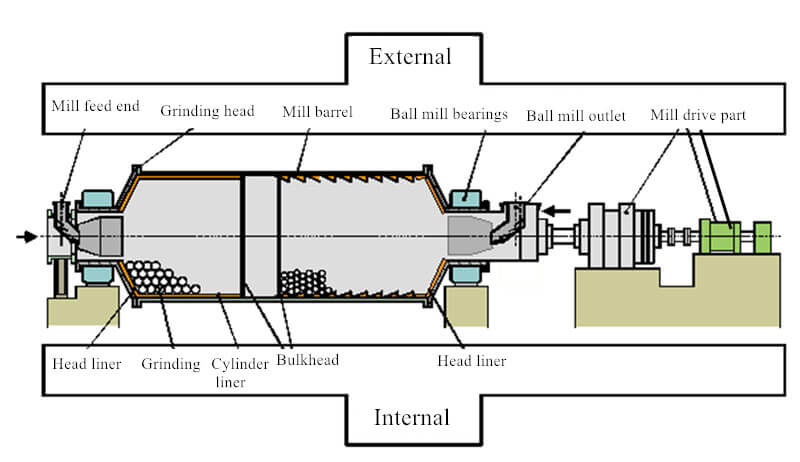
What is Uniform Ore Feeding?
In fact, there are two main meanings. First, the composition of the ore particle size is uniform. Second, the feeding speed (the amount of ore fed into the grinding machine per unit time) is constant. In order to improve the grinding efficiency, the amount of ore feeding should be continuous, uniform, and stable at a high level. More time and less time will make the mass fraction in the grinding machine fluctuate frequently, which is not conducive to the grinding process. Grinding feedstocks tend to have particle size segregation in the silo – fine in the middle, and coarse in the surrounding area, which can easily cause the uneven composition of the feedstock. Therefore, the silo should try to use multi-point discharge to feed the ore.
What is Large Sand Return?
Then the meaning of “large sand return” is also very simple. We require that a “large sand return” should be realized during the operation of the grid plate of the small ball mill. In order to explain such benefits, first of all, let’s talk about what is sand return. Sand return refers to the coarse-grained grade returned by the classifier to the grinding machine for regrinding during closed-circuit grinding. The amount of returned ore is often several times the original amount of ore supplied. The ratio of the amount of sand returned to the amount of raw ore feeding is called the sand return ratio.
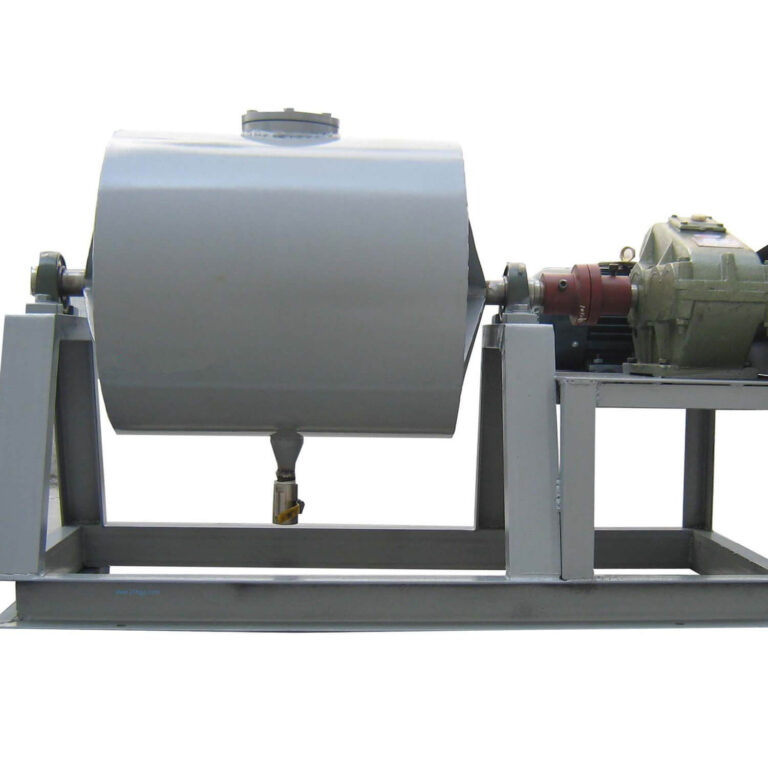
The practice has proved that the size of the sand return ratio will directly affect the productivity of the mill. The larger sand return ratio increases the total ore feeding volume of the mill, thereby increasing the discharge speed of the mill, shortening the residence time of materials in the mill, and accelerating the cycle. In addition, although the returned sand is coarse-grained ore, it is finer than the original ore after all, so the particle size composition of the whole feed of the mill becomes finer, and the comprehensive result is beneficial to improving the productivity of the small ball mill. By studying the relationship between the sand return ratio and the relative productivity of the mill. It can be known that within a certain range (such as between 100% and 500%) as the sand return ratio increases, the productivity of the mill increases with it. When it reaches a certain value, the productivity increase is very small, and the full feed of the mill is close to the maximum. Through the ability, it is easy to cause the ball to distend the belly. Therefore, the sand return ratio should be kept stable, close to a constant value.
What is High Concentration?
The so-called “high concentration“, the grinding mass fraction is an important factor affecting the productivity of the mill, which determines the friction between the grinding medium and the material to be ground, the fluidity of the pulp, and the effective density of the medium (the difference between the density of the medium and the pulp is different) ). At the same time, the amount of ore per unit volume in the ore discharge is large, so the amount of ore discharged is large. However, if the pulp mass fraction is too high, due to the increase in pulp density, the effective density and mobility of the grinding medium and the impact effect will be weakened by the loss of the steel balls of the dry ball mill. On the contrary, it will reduce the productivity of the grinding machine, and even prone to “bloating”.
Mainly refers to the mass fraction (mass fraction of pulp), which is the percentage of ore mass (dry weight) and pulp mass (ore + water) in the pulp, where mass fraction refers to the pulp mass fraction (grinding mass fraction) in the mill. In the operation of the grinding machine, a higher grinding mass fraction is generally used, so that a layer of the pulp can be attached to the surface of the medium, thereby enhancing the grinding effect favorable for grinding. Therefore, “high concentration” refers to appropriately increasing the grinding mass fraction within a certain range, which is conducive to improving the grinding effect.
As long as the above-mentioned ball mill operation specifications are mastered, or the predecessors have learned lessons through personal practice, the ball mill can continue to work in the best working condition. The core problem revealed by these nine-character secrets is the balance of input and output efficiency.