The ball mill is the key equipment for the material to be crushed and then crushed. The steel ball is used as the grinding medium to further grind the material to meet a certain fineness requirement and achieve a better grinding effect. It is widely used in cement, silicate products, new building materials, refractory materials, fertilizers, and non-ferrous metal beneficiation and glass ceramics and other production industries, dry or wet grinding of various ores and other grindable materials.
Special Steel Ball for Ball Mill
With the continuous use of ball mill equipment, the quality of ball mill steel balls has also become a key point. The varieties specified in the national standard include chemical composition, mechanical properties, Cast ball specifications, and inspection methods, etc.
Good quality grinding balls should have the following properties:
- High wear resistance, sufficient wear resistance for cutting wear, deformation wear and fatigue spalling wear
- High hardness for cutting wear
- High requirements for deformation wear and fatigue wear
- High strain fatigue, contact fatigue and impact fatigue life
- Good impact toughness, high impact resistance under repeated impact and wear conditions, no breakage
- High hardenability, to ensure that the overall wear of the ball is uniform without losing roundness
- Excellent metallurgical quality, produced according to the specified standard composition, without casting defects such as slag inclusion and sand inclusion.
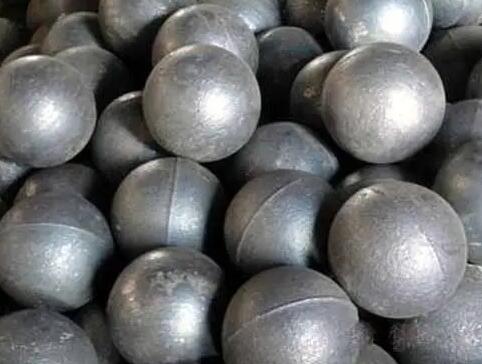
The steel ball is the medium used by the ball mill to grind the material. It impacts and grinds the material during the operation of the ball mill, and grinds the material into fine powder. The loading and matching of steel balls have a significant impact on the quality of the mill’s production-grade products, so ball matching is an important part of the daily process and technical management of ball mills. So what kind of steel balls are the most suitable for ball mills?
Ball Mill Steel Ball Requirements
- Impact force
When the impact energy generated by the steel ball exceeds the strength limit of the material, the material will be pulverized, but the excessive impact force applied to the ball mill lining plate and the simplified stress also increases, and the energy consumption is also large. Therefore, when choosing steel balls, theirimpact factor must be considered in the first place. - Grinding force
During the operation of the ball mill, the contact area between the material and the steel ball is mainly increased by the surface area of the steel ball, thereby improving the grinding efficiency, especially for the fine grinding bin. - Material storage capacity and extrusion force
Through the gradation of large and small balls, the gap between the steel balls is reduced, and the bulk density of the steel balls is increased, so that it has an appropriate material storage capacity. On the one hand, the flow rate of the material in the mill can be controlled, and the residence time can be extended to obtain sufficient grinding. - Impact times
More times is the main means to improve the grinding fineness and output. Increase the number of impacts by reducing the ball diameter and increasing the number of steel balls, which are necessary for impact and grinding. The impact force, impact times and material storage capacity of the steel ball depend on the ball diameter of the ball mill.
When the loading capacity is the same, the larger the average ball diameter, the stronger the impact force, the larger the porosity, and the faster the flow velocity, but the number of impacts decreases, and the material storage capacity becomes weaker. For hard-to-grind materials, steel slag grinding requires a strong impulse, as well as increasing the number of impacts and prolonging the grinding time of the materials in the silo. In actual production, it should be selected according to the actual situation of grinding.
As the most important part of the ball mill, the status of the steel ball is self-evident, so we must operate in strict accordance with the requirements when selecting and adding a ball mill to ensure the normal operation of the equipment.
4 Things Consider When Mixing Steel Balls
1. Equipment model: Such as cylinder diameter and length.
2. Production requirements: That is the user’s standard for the grinding fineness of materials.
3. Material properties: It refers to the initial particle size, hardness, and toughness of the material to be ground.
4. Steel ball size: It should pay attention to the steel ball size, don’t pursue the large size blindly.
Precautions for Grading of Steel Balls
- During the normal operation of the ball mill, the reasonable friction between the steel ball and the steel ball, the steel ball and the ore, and the steel ball and the ball mill lining plate will increase the wear and tear, making the large ball mill small and the medium ball mill into small balls. Therefore, under normal circumstances, there is no need to add a small ball.
- The steel balls in the ball mill are constantly worn out during the operation. To maintain a reasonable ratio of the ball charge filling rate and the balls, and to maintain the stable operation of the ball mill, it is necessary to reasonably supplement the balls to compensate for the wear and tear.
- The added weight of the steel ball is based on the quality of the steel ball, and the quality of the steel ball determines the amount of ore added per ton. Adopt a new wear-resistant steel ball. The addition of high-quality steel balls is calculated according to the amount of ore processed per ton (that is, 0.8kg per ton of ore). Generally, steel balls need to process one ton of ore (1kg—1.2kg).
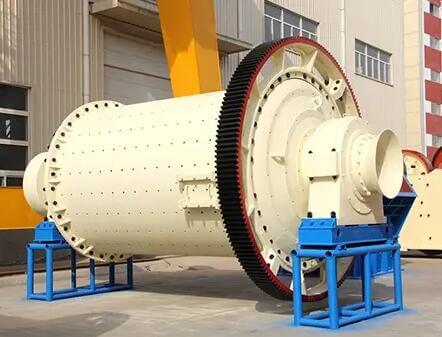
In the working process of the ball mill, whether the gradation of the steel balls of the grinding body is reasonable is related to the working efficiency of the equipment. Only by ensuring that the various balls have a certain proportion can they be adapted to the particle size composition of the material to be ground, and a good grinding effect can be achieved. Reasonable selection of the gradation of ball mill steel balls is an essential measure to improve the output and quality of ball mills.