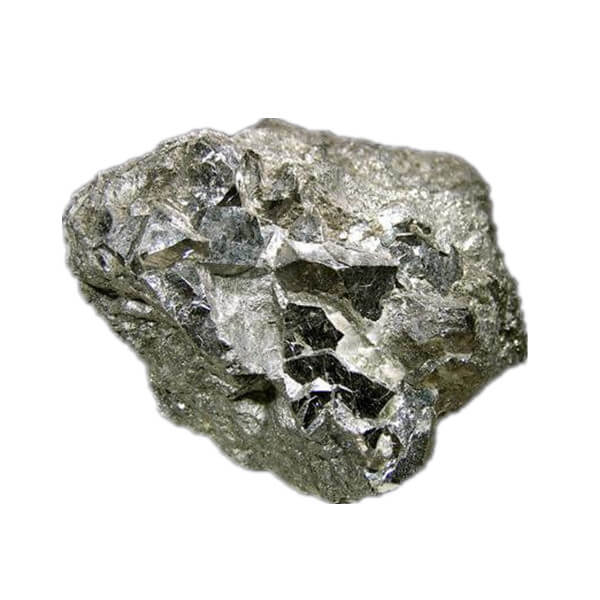
Cobalt is a silver-gray metal with the element symbol Co and atomic number 27. It belongs to Group VIII. It has a melting point of 1495°C and a boiling point of 2870°C. It is ductile and ferromagnetic. It is relatively stable in air at room temperature. When it is higher than 300°C, Cobalt begins to oxidize in the air. Cobalt is widely used in aerospace, machinery manufacturing, electrical and electronics, chemistry, ceramics, and other industrial fields because of its high-temperature resistance, corrosion resistance, and magnetic properties. It is one of the important raw materials for manufacturing superalloys, hard alloys, ceramic pigments, catalysts, and batteries.
Cobalt Ore Types
There are about 100 known cobalt-containing minerals.
The main cobalt minerals are: skutterudite (CoAs3), sulfur cobalt ore (Co3S4), fiber columnite (CuCo2S4), Cobaltite (CoAsS), smaltine (CoAs2), Erythrite (3CoO As2O5 8H2O, etc.,
There are four main types of cobalt ore in the world: ① copper-cobalt ore ② nickel-cobalt ore, including sulfide ore and oxide ore; ③ arsenic-cobalt ore; ④ cobalt-containing pyrite. These cobalt ores contain low Cobalt.
Skutterudite
The composition of skutterudite is CoAs3, containing Co20.77%, often containing a small amount of iron and nickel, equiaxed crystal system, and the crystal is in the shape of a cube, octahedron, or both. Aggregates are often dense granular, tin white to steel gray, sometimes with light gray or iridescent tint, gray-black streaks, metallic luster, opaque, Mohs hardness 5.5~6, density 6.5~6.8g/cm3. Produced in cobalt-nickel hydrothermal deposits, it is symbiotic with arsenic-cobalt ore, arsenic-nickel ore, red nickel ore, and other cobalt-nickel-arsenides. It is easily oxidized on the surface to form Erythrite, an essential mineral raw material for cobalt smelting.
Sulfurite cobalt ore
Sulfurite is a cobalt sulfide mineral composed of Co3S4, containing Co(58%), nickel, iron, equiaxed crystal system, and octahedral crystals, usually granular or dense massive aggregates. Light bright steel gray, gray-black streaks, metallic luster, Mohs hardness 5~5.5, density 4.85g/cm3.
Cobaltite
Cobaltite ore is also called arsenite cobalt, composition CoAsS, containing Co 35.4%, equiaxed or orthorhombic. The crystals are octahedron, cube, pentagonal dodecahedron, or their aggregation shapes; the aggregates are granular or dense blocks, tin white with a slight tinge of rose red. Black streaks, metallic luster, Mohs hardness 5~6, density 6.0~6.5g/cm3. It is a mineral of hydrothermal origin, produced in some contact meta-somatization deposits and cobalt-bearing hydrothermal veins. It is easily oxidized on the surface to become a rose-colored Erythrite. It is an essential mineral raw material for extracting cobalt.
Smaltine
Smaltine ore composition (Co, Ni, Fe) As3 ± x, cobalt, nickel, and iron content in a wide range of changes. When nickel and iron increase, Me(Co+Ni+Fe): As will significantly deviate from 1:3. For example, when rich in nickel, Me: As=1:3.273; when rich in iron, μe: As=1:2.3. Equiaxed crystal system, the crystals are in the form of cubes, octahedrons or both, usually in the form of granular and dense blocks. Tin white to steel gray, grayish black streaks. Metal luster, Mohs hardness 5.5~6, density 6.4~6.8g/cm3. It is mainly produced in cobalt-nickel-arsenide hydrothermal veins and symbiotic with arsenic-nickel ore, skutterudite, red nickel ore, etc. It is easily oxidized on the surface to become cobalt and nickel. It is an important mineral raw material for smelting cobalt and nickel.
Erythrite
Erythrite is an arsenate mineral. Its crystals are extremely rare. The crystals are needle-shaped or plate-shaped, transparent to translucent, pink to bright red, pearl gray, monoclinic, and glassy. Generally, it appears as an aggregate soil or leather shell. When cobalt is heated, it will change color to blue. Chemical formula Co3(AsO4)2·8H2O, density 2.91~2.95g/cm3, hardness 1.5~2.5, used for extracting cobalt, also used for coloring of glass and ceramics.
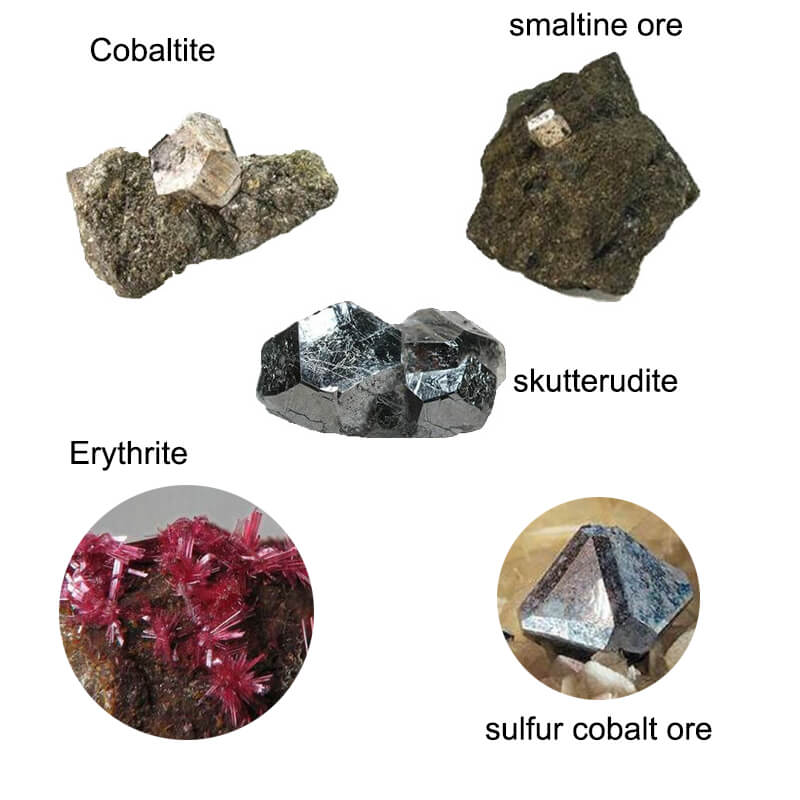
Copper-cobalt ore beneficiation process
The processes of crushing, screening, and grinding are similar in the beneficiation process of copper-cobalt ore. Still, in beneficiation, flotation, magnetic separation, and mixed separation may be used. So what are the beneficiation methods of copper-cobalt ore?
(1) Flotation
The flotation process is easy to operate and highly controllable, and not only can recover low-grade and complex fine-grained copper and cobalt minerals, reduce the separation difficulty of copper and cobalt minerals, and improve the quality and recovery rate of copper and cobalt concentrates.
Flotation process:
First, the copper-cobalt raw ore is ground, and a certain amount of regulator is added during the grinding process to adjust the pH value of the pulp to within the range of 9-10. After grinding treatment, add collector and foaming agent to the ore pulp, then carry out copper-cobalt mixed flotation roughing. After two times of sweeping, we can obtain tailings. Add inhibitors to the mixed flotation foam, and after three times of beneficiation, we can get the copper-cobalt mixed Concentrate. In turn, add inhibitors and collectors and carry out copper-cobalt separation flotation. After one roughing and one sweeping, we get cobalt Concentrate. For the foam after separation and flotation of copper and cobalt, separate twice to obtain copper concentrate.
(2) Combined process of flotation and magnetic separation
Cobalt has weak magnetic properties. In most cases, flotation cannot recover all cobalt. It can recover with a magnetic separation process.
Process flow:
First, grind the copper-cobalt oxide ore flotation tailings with a mill to -0.074mm, accounting for 70-90%, make a slurry with a concentration of 10-40%, and use a high-gradient magnetic separator with a background field strength of 0.8-1.2T. Strong magnetic roughing to obtain strong magnetic roughing concentrate and strong magnetic roughing tailings and strong magnetic roughing tailings are the final magnetic tailings.
(3) Leaching process
For complex copper-cobalt oxide ores, leaching and other methods are usually used for treatment. Oxidized ores are generally severely weathered and have poor permeability, so they are unsuitable for all heap leaching. The combination of heap leaching and stirring leaching can obtain high recovery rates of copper and cobalt metals.
Process flow:
Crush and grind the copper oxide cobalt raw ore, and classify the crushed ore according to the particle size. Heap leaching is adopted for products with a size of +5mm, using staged heap leaching, first spraying and leaching copper, control the pH value at 1.5, the spraying intensity is 10~15L/m2.min, and the leaching time is 60~120 days; Grade product leaching stirring leaching, stirring leaching carried out under normal pressure, and the reaction temperature is 20-80 ℃, and pH value controlled at 1.5, and leaching liquid-solid ratio is 4:1, and grinding fineness-200 order accounts for 60%~ 90%, the leaching time is less than 4 hours.
The above three methods are the three commonly used beneficiation processes for copper-cobalt ore. Which one is suitable depends on our production conditions.