Quartz sand beneficiation separates and purifies high-purity sand from raw quartz ore to meet various industrial requirements. Quartz sand is a common raw material used in glassmaking, ceramics, electronics, and construction industries.
Impurity Minerals in Quartz Sand
Trash minerals in common quartz sand vary by geographic location and deposit characteristics, but the following are some common trash minerals that may be present in quartz sand:
Feldspar: Feldspar is a kind of aluminum-containing mineral, and the common ones are albite and potassium feldspar. They are usually white, pink, or gray. Feldspar is a common impurity in quartz sand, which can affect the purity and transparency of quartz sand.
Mica: Mica is a flaky mineral; the common ones are muscovite and biotite. They may exist in the quartz sand as fine flake particles, affecting the texture and transparency of the sand body.
Iron oxide minerals: Such as hematite and magnetite, give quartz sand a different color, which may affect its use in areas such as glass manufacturing.
Clay Minerals: Quartz sand may contain clay particles that can affect the fluidity and processing properties of the sand body.
Carbonate minerals: Such as calcite or dolomite, usually exist in the form of fine particles. These minerals’ presence may affect the quartz sand’s chemical stability.
Other metal oxides: Such as zircon (zircon) and so on. These minerals can affect the chemical composition of the quartz sand.
Organic matter: Organic matter residues may also be present in quartz sand, mainly if formed in a natural environment.
Zero electric point of impurity minerals in quartz sand
The zero electric point of impurity minerals in quartz sand refers to the pH value in solution when the mineral surface has a specific charge, that is, the pH value at which the surface charge is neutralized. At this pH value, the charge on the mineral surface will become neutral, affecting the interaction between the mineral and other substances, such as adsorption, precipitation, etc.
The following are the zero-electric point ranges of impurity minerals in some typical quartz sands. Note that these values may vary due to deposit origin, experimental conditions, etc.
- Feldspar: The zero charge point of feldspar is usually between pH 2-3.
- Mica: The zero charge point of mica is in the pH 2-4 range.
- Iron Oxide Minerals: Hematite has a zero charge point around pH 9, and magnetite has a zero charge point in the pH 6-7 range.
- Carbonate Minerals: Calcite has a zero charge point between pH 8-9, and dolomite has a zero charge point in the pH 9-10 range.
- Zircon: Zircon has a zero charge point around pH 6-7.
Mineral Name | Zero Point (PZC) |
Potassium feldspar K(AISi3O8) | 1.4-1.7 |
Albite NA(AISi3O8), Anorthite Ca(AI2Si2O8) | 1.9-3.6 |
Muscovite KAI2[Si3AIO10] (OH, F)2 | 1.0 |
Quartz SiO2 | 2.0 |
Apatite Ca5(PO4)3(OH,F,CI) | 4.0-7.0 |
Magnet Mine Fe3O4 | 6.3-6.7 |
Hematite Fe2O3 | 5.2-8.7 |
Ilmenite FeTiO3 | 5.6 |
Goethite FeOOH | 5.9-6.9 |
These zero electric point values are approximate and can be determined by measuring properties such as charge in a laboratory setting. Knowing the point of zero electricity of impurity minerals can help optimize the beneficiation and processing of quartz sand for more efficient separation and purification. In different industrial applications, this information also helps predict and control impurities’ behavior to obtain quartz sand products of desired purity.
Quartz Sand Beneficiation Methods
Purification by chemical method
The chemical method of purifying quartz sand is mainly acid leaching, which is also the most commonly used because of its high leaching efficiency. Compared with physical processes, the cost of chemical methods is higher, but the purification effect is better, especially in the case of high purity requirements for quartz sand; chemical purification is more effective. The acids commonly used in pickling are sulfuric acid, hydrochloric acid, nitric acid, hydrofluoric acid, oxalic acid, etc. Dilute acid has a good effect on removing impurities such as iron, aluminum, and magnesium. In contrast, concentrated sulfuric acid and hydrofluoric acid have an excellent impact in removing impurities such as titanium and chromium. Therefore, in actual beneficiation, the purification effect of mixed acid on quartz sand is the best. Oxalic acid is a weak acid with little environmental pollution, less corrosion on equipment, and an obvious iron removal effect. The reaction mechanism is that oxalic acid reacts with impurities such as iron on the surface of quartz sand particles to form several complexes separated from the particle surface to achieve the purpose of separation and purification. In addition, high-temperature chlorination calcination is usually used to remove inclusion impurities in quartz. The principle is to heat the quartz to 1000-1300°C and inject a mixed gas of chlorine and hydrogen chloride to remove the alkali metal. For impurities such as alkaline earth metals and transition metals, the purity of quartz sand after high-temperature chlorination can reach more than 99.99%.
Microbiological purification
Microbial leaching is a new purification method that uses the physiological functions of microorganisms and their metabolites to separate the impurity components on the surface of quartz sand from the quartz matrix through oxidation, dissolution, and decomposition. Foreign studies have found that using microorganisms such as Aspergillus niger, Mycobacterium phlei, Penicillium, and Bacillus polymyxin to extract quartz sand has a good purification effect. Although microbial leaching is more environmentally friendly and energy-saving in removing impurities, its disadvantages, such as long leaching time and low leaching efficiency, restrict its industrial application.
Combined purification
Due to the different properties of quartz ore in other regions, the impurities contained and particle sizes of embedded parts are also different. Therefore, when the pretreated quartz sand is further purified and prepared, it is necessary to adopt other joint processes according to the ore properties of the quartz sand to remove impurities in a targeted manner and obtain high-purity quartz sand.
Surface modification
Natural quartz powder has a poor affinity with polymer materials. When used as a filler, it is often dispersed unevenly or even agglomerated, significantly impacting the product’s quality. Therefore, it is necessary to modify the surface of the quartz powder to make it reactive. The commonly used modifiers for the surface chemical modification of quartz sand include silane coupling agents (amino, epoxy, methacryl, trimethyl, methyl, and vinyl), aluminate coupling agents, titanate coupling agents, etc. Coupling agent, stearic acid compounding agent, etc., among which silane coupling agent is mainly used.
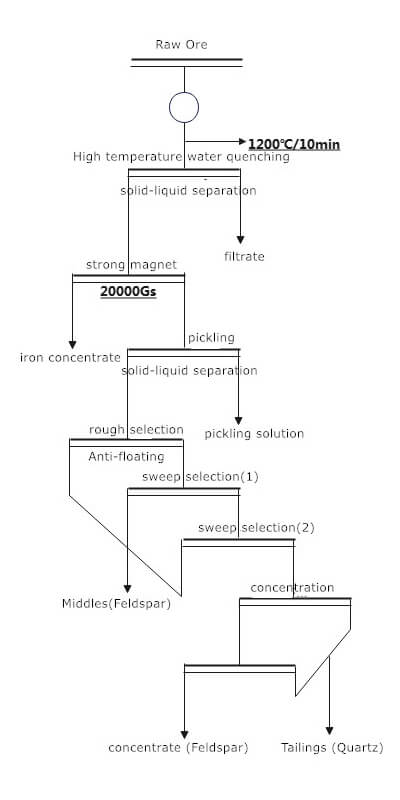
Quartz Sand Beneficiation Process
The beneficiation process involves several steps to remove impurities and obtain high-purity quartz sand:
- Mining and Crushing: Raw quartz ore is extracted from mines and undergoes coarse crushing to reduce particle size.
- Grinding: The crushed quartz ore is further ground to achieve the desired particle size. Grinding can be done using equipment like ball mills.
- Classification: After grinding, the finely ground quartz ore is mixed with water to form a slurry. The slurry is then classified to separate the quartz particles from impurities based on particle size.
- Flotation: Flotation is commonly used to separate quartz particles from impurities. In the flotation process, specific reagents and modifiers are added to the slurry to selectively render the quartz particles hydrophobic, allowing them to attach to air bubbles and float to the surface. At the same time, the impurities remain in the aqueous phase.
- Dewatering: The resulting flotation concentrate contains quartz particles, water, and reagents. Dewatering processes, such as filtration or centrifugation, remove excess water from the concentrate.
- Drying: The dewatered concentrate is dried to reduce moisture content further and stabilize the quartz sand.
- Purification: Additional purification steps may be needed depending on the application requirements. High-purity quartz sand is often required for applications like electronics. Additional treatments involve acid leaching or other chemical processes to remove remaining impurities.
- Final Grading and Packaging: The purified and dried quartz sand is graded based on particle size and quality. The final product is then packaged and prepared for distribution or further processing.
It’s important to note that the beneficiation process can vary based on factors such as the raw ore’s characteristics and the final product’s desired purity. The goal of quartz sand beneficiation is to produce a high-purity product suitable for specific industrial applications while minimizing the content of impurities that could affect the end-use performance of the material.