As a common gold extraction process from oxidized gold ores, the oxidized gold ore heap leaching process is widely used in gold extraction and recovery. People mainly use heap leaching to process low-grade ores that traditional methods can’t process. The heap leaching method of oxidized gold ore involves stacking gold-containing ores on an impermeable site and leaching them with cyanide solution. After the gold and silver in the ore are dissolved, they flow into the precious liquid storage pool along the pre-designed grooves on the site. These precious liquids containing gold and silver are adsorbed with activated carbon and then desorbed to recover gold and silver. The process of producing gold ingots from the precious liquid is the same as the cyanidation method. The heap leaching method has the advantages of a simple process, less equipment, less investment, quick results, low production cost, and strong adaptability of the ore.
Oxidation gold ore heap leaching method is an important technical means for gold extraction from gold mines. To achieve full contact between gold ore particles and Na2CN, it has become very important to use advanced technical means in dressing and smelting technology. In addition to looking for new efficient or non-toxic gold immersion solvents and pressurized oxidation processes, bacterial oxidation processes, chemical oxidation processes, chlorination methods, and sulfur-containing reagent oxidation methods, we should also improve gold immersion technical methods, such as: Use methods such as spraying and dripping to add cyanide through pipelines.
Oxidation Gold Ore Heap Leaching Process
The heap leaching method of oxidized gold mines mainly includes six stages: ore preparation, heap construction, leaching, gold recovery, solution recycling, and residue management.
1. Ore Preparation
Crushing and Grinding: The ore is crushed and ground to a suitable particle size to ensure adequate exposure of the gold particles.
Agglomeration (if necessary): Fine particles may be agglomerated to improve heap permeability and leach solution flow.
2. Heap Construction
Heap Formation: The prepared ore is stacked in heaps on a prepared pad with a liner system to prevent leach solution leakage.
Pad Design: The pad is designed to collect and channel the leachate solution to a recovery plant.
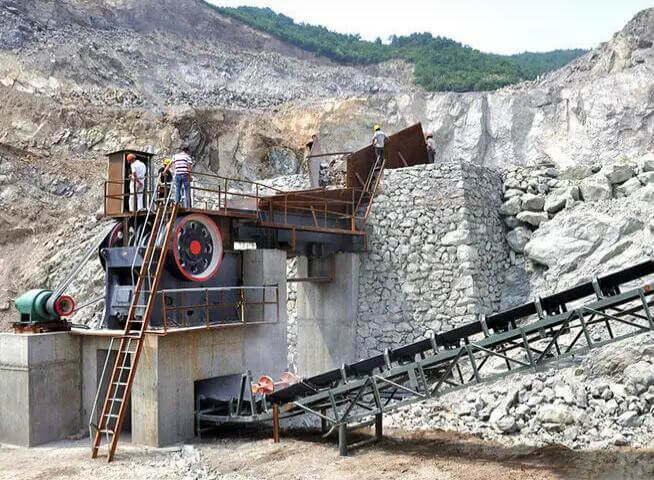
3. Leaching
Solution Application: A leaching solution, typically a dilute cyanide solution, is applied to the heap via drip emitters, sprinklers, or flooding.
Percolation: The solution percolates through the heap, dissolving the gold as it moves through the ore.
4. Gold Recovery
Pregnant Solution Collection: The gold-laden solution, known as the pregnant solution, is collected at the heap base.
Gold Extraction: The gold is extracted from the solution using carbon adsorption, zinc precipitation (Merrill-Crowe process), or electro-winning.
5. Solution Recycling
Barren Solution: The solution now depleted of gold (barren solution), is recycled back to the heap for further leaching.
6. Residual Management
Tailings Management: After leaching, the spent ore (tailings) is managed to minimize environmental impact. This may include rinsing the heap to remove residual cyanide and other chemicals.
The above are the six common stages of heap leaching of oxidized gold ores. Sometimes, the heap leaching process can be combined with the zinc replacement method, that is, high-grade gold ore is sent to the cyanide plant for treatment, while low-grade ore, off-surface ore, or waste rock is treated by heap leaching. In the actual production process, different gold ore properties require different heap leaching processes and parameters, which can only be determined through sufficient mineral processing tests.
Oxidation Gold Heap Leaching Considerations
In the process of extracting gold from oxidized gold ores by heap leaching, special attention needs to be paid to the following aspects:
Granulation
The lime dosage must reach a pH value between 9.5 and 10.5. Through experimentation, it has been determined that to achieve a certain alkalinity, a mixture can be made by adding 2 grams, 4 grams, or 6 grams of lime to 1000 grams of ore in a beaker, then adding water just enough to cover the surface of the ore. After 24 hours, the pH value is tested to ensure it falls within the range of 9.5 to 10.5. Cement dosage is determined based on the granules formed, which should not disperse or become muddy after soaking in water for 24 hours. Sodium cyanide dosage varies due to the high moisture content of the ore (often above 10%) and its impurities. During granulation, the concentration of sodium cyanide should be increased, typically ranging from 60 to 150 grams per ton of ore. The concentration of sodium cyanide added should be between 0.1% and 0.5%. By adjusting the quantity and concentration of sodium cyanide, the concentration for granulation can be determined, achieving a pH of around 11.5. The moisture content of the granules should be maintained between 15% and 20%, adding to the natural moisture content of the ore, which is approximately 10%. Total moisture content should generally not exceed 30%, as excessive moisture can cause the granules to disperse or become soft. The solidification time should be at least 72 hours. In case of rain during granulation, the ore should be covered to prevent gold loss, the heap can be sprayed with water while granulating, as gold is prone to leaching after granulation.
Heap Stability
Because cars roll back and forth on the ore pile, it is easy to compact and crush the ore particles. Once the weather is hot, they will become large cakes. If conditions permit, it is best to pile them on a conveyor belt. The height of the ore pile should not be too high at present. It is suitable to be 3 to 4 meters. After the leaching rate stabilizes, it will increase again.

Spraying
The pellets that have been granulated into agglomerates must not be washed or washed to adjust the PH value. The PH value should be adjusted during granulation. It is not allowed to pre-spray the ore. After washing, mud will be formed and lumps will form. After the pellets are muddy, they will no longer be granulated. The consequences will be serious. The sodium cyanide solution cannot penetrate downward during spraying, and it is easy to accumulate liquid on the surface.
Sodium cyanide concentration during spraying
Since the ore is complex and the weather is cold, the sodium cyanide concentration during initial spraying can be appropriately increased and can be controlled between 0.1% and 0.08% until the peak period (i.e. gold leaching) After the highest concentration), it can be reduced to 0.08% ~ 0.06%, and in the later stage it can be reduced to 0.04% ~ 0.02%. The concentration of precious liquid gold can be adjusted at any time to adjust the sodium cyanide concentration.
Spray cycle
The spray time is generally 7 to 8 hours a day, and cannot exceed 10 hours at most (but the amount should be reduced). Generally, spray 1 and stop 1 or spray 1 and stop 2. During the day, because the temperature is high, gold is easy to leach, so you can spray 1 and stop. 1. At night, because the weather is cold and not freezing, you can spray for 30 minutes and stop for 1 hour, or spray for 1 and then stop for 2, or do not spray at night. The spraying time should not be too long so that the ore pile can absorb oxygen when not sprayed. If the spraying time is long and the number of times is high, the volume of the solution will be increased. In this way, the concentration of the expensive solution will be reduced and sodium cyanide will be wasted. At the same time, it will also increase the volume of noble liquid and affect the adsorption capacity of gold-loaded carbon.
Spray intensity
Spray intensity is related to spray time and liquid volume. Generally, it is more appropriate to control the spray intensity at 6 to 20 L/m2.h (6 to 20 liters/square meter × hour). The maximum cannot exceed 25~30L/m2.h (calculated using the yard area, daily spray volume, and time). If the spray intensity is high, the volume of the noble liquid will increase and the gold concentration will be diluted, which will affect the adsorption capacity of activated carbon (generally the adsorption capacity of activated carbon is 8-10kg/t). If the volume of noble liquid is large, the same adsorption time will be reduced due to the low gold concentration. , the adsorption amount is reduced and the adsorption time is prolonged, which also affects the workload and cost of desorption electrolysis. It also increases the capacity of your liquid pool. The most important thing is to reduce the concentration of gold and extend the spray time, so the spray volume cannot be too large. Large, the spray cycle should not be too many per day.
Leaching of gold concentration
Generally, according to the theoretical spray gold concentration leaching, the gold grade of the precious liquid during the peak period is 5 times or more than that of the original ore, that is, the raw ore grade is 3g/t. According to normal and successful heap leaching, the highest noble liquid gold grade should be 15g/m3, due to various conditions in actual production, it is less than 5 times, but at least 2 to 3 times, especially for granulation and heap leaching, adding appropriate sodium cyanide solution for granulation and appropriate loading (not suitable for heap leaching) Compacted ore particles), appropriate spray volume, the gold grade of your liquid should reach its peak between the 1st and 3rd day, reaching more than 6g/m3, and then gradually decrease, so that the spraying time does not need to be delayed for a long time. long, reaching the end below 1g/m3. If the gold concentration does not reach the expected concentration there is no obvious peak period, or the peak period is delayed or extended, it means that the heap leaching has failed and the leaching rate will not be too high and cannot meet the laboratory test indicators. This is all related to the spray intensity or sodium cyanide concentration, pH value, etc. It should be checked and analyzed immediately, otherwise, it will extend the leaching time, reduce the leaching rate, waste sodium cyanide, and be detrimental to the next step of activated carbon adsorption. It will not only increase the amount of adsorbed carbon, Impurities will be adsorbed on the carbon, reducing the amount of gold adsorbed and increasing the cost of electrolysis.
The gap between the gold leaching rate and the laboratory leaching rate
Generally, if the leaching rate in the laboratory column leaching test is 70%, it is understandable that the on-site leaching rate should be 60-70% because the laboratory conducts column leaching simulation under ideal conditions. Experimental, but the difference cannot be huge on-site, otherwise the cause should be found.
The oxidation gold ore heap leaching process offers a cost-effective and efficient method for extracting gold from low-grade ores. However, it requires careful planning, stringent management, and adherence to environmental and safety regulations to ensure successful and sustainable operation.