NdFeB magnets, also known as NdFeB magnets, are tetragonal crystals composed of neodymium, iron, and boron and have excellent magnetic properties. As a high-performance rare earth permanent magnet material, NdFeB has expanded the industrial chain to more emerging fields through its outstanding magnetic properties and significant energy-saving effects and has gradually been listed as a high-tech material that is encouraged and supported by the country for development. The scientific research and production of high-value-added products such as wind power generation, hybrid vehicles, consumer electronics, intelligent robot manufacturing, energy-saving elevators, and energy-saving petroleum pumping units are all inseparable from the support of NdFeB materials.
NdFeB Scrap
NdFeB scrap refers to the waste materials generated during the recycling and production process of NdFeB magnets. NdFeB magnet is a permanent magnet produced using rare earth elements such as NdFeB as the primary raw material. It has excellent characteristics such as high magnetic energy products and high stability.
During the processing and production of NdFeB magnets, some waste materials are often generated, such as chips, residual magnet materials, etc. After processing, these waste materials become NdFeB scrap.
NdFeB scrap mainly contains high concentrations of rare earth elements, such as neodymium, iron, boron, etc. The specific ingredients and causes are as follows:
- Chips: Powder, debris, etc., from the workpiece during processing. Its composition is mainly composed of neodymium iron boron magnets.
- Remaining magnet material: Comes from excess magnet material during the processing of permanent magnets. These materials also have relatively high magnetism. If reused, it can avoid repeated production processes and have a particular resource utilization value.
The impact of NdFeB scrap on the environment
The generation of NdFeB scrap exacerbates environmental problems. On the one hand, if the waste materials are not correctly processed, it will release rare earth elements and toxic elements and pollute the land and water sources. On the other hand, many rare earth elements and toxic elements are challenging to consume and have long-term environmental effects.
Although NdFeB scrap is difficult to process, it contains high amounts of rare earths and toxic elements. If reused, it has great potential value.
NdFeB scrap reprocessing
There are two main ways to reprocess NdFeB scrap:
One is to smelt the waste materials and extract the metal elements for reuse;
The other is to perform chemical reactions to convert waste materials into other chemicals.
Preliminary research shows that using NdFeB waste to produce metal alloys, composite materials, and other chemical compounds has high technical prospects. In addition, it is also technically feasible to use NdFeB waste to produce NdFeB magnets.
NdFeB Powder-making Process
1. Raw material conveying section
After the NdFeB scrap is calcined, it enters the transfer bin, and the raw materials fall into the belt feeder.
2. The grinding and powder selection section
NdFeB scrap enters the European version mill through the belt feeder for grinding. The ground materials are sorted by the powder selector under wind, and the finished powder that meets the requirements is selected and collected by the cyclone. The device performs collection and temporary storage.
3. Finished product storage and transportation section
The finished powder is sent downstream through pneumatic or other conveying equipment for the next step.
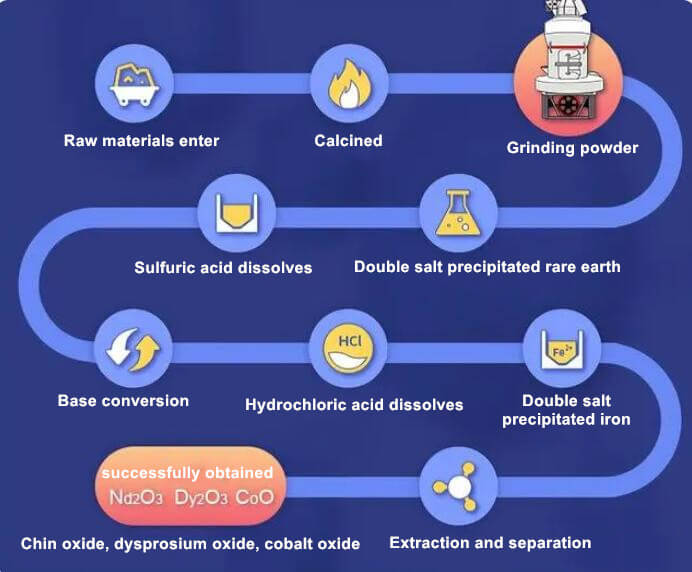
40000 Tons/Year NdFeB Grinding Plant
Material: NdFeB scrap
Capacity: 40,000 tons/year
Finished product particle size: 300 mesh
Finished product use: rare earth materials
Main equipment: MTW European version mill
NdFeB Grinding Production Line Production Process
The on-site raw materials are transported to the European version of the primary mill via a belt conveyor for grinding and processing. The fan airflow sends the ground materials to the powder separator for classification. Materials that do not meet the fineness requirements fall into the grinding chamber for re-grinding, and qualified materials are the air that flows through the pipe and enters the cyclone powder collector for separation and collection. Finally, the finished product is transported to the elevator by the screw conveyor and reaches the finished product warehouse. The entire production line has a smooth flow and high work efficiency, which increases the grinding output.
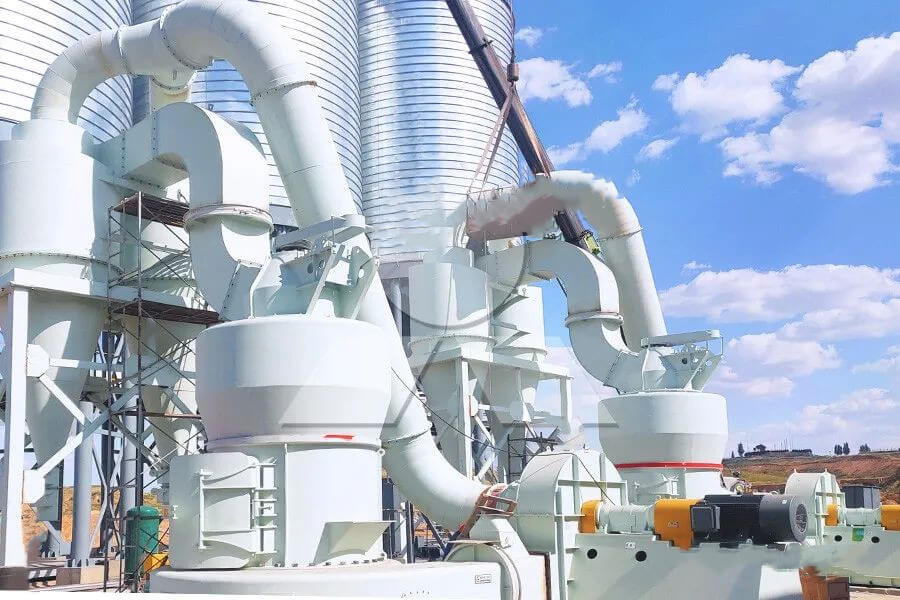
NdFeB Grinding Production Line Advantages
- Reasonable layout and small footprint
The MTW European version of the mill has a vertical structure, a small footprint, substantial completeness, and a self-contained production system, saving land area and better meeting customer needs. - Intelligent system, more stable operation
The intelligent control system controls the equipment’s operating status, saving labor costs and improving production efficiency. - Simple operation and maintenance
The structural design is more compact, and essential components are made of high-quality steel, making the machine durable and reliable. It has superior performance, stable air volume and pressure, low failure rate, and more convenient installation and adjustment. - Green and environmentally friendly, no dust spillage
It adopts a negative pressure system; there is no dust pollution. The feeding, grinding, and finished product conveying systems are all equipped with efficient dust removal devices to achieve dust-free operation.
The 40,000 tons per year NdFeB grinding production line has been optimally configured regarding production technology and equipment selection. The finished products are of high quality, and the production process is environmentally friendly. You can contact us anytime if you want to know more about the relevant equipment and Craftsmanship.