The existing artificial sand or natural sand in the market is cleaned by traditional sand washing equipment. The sand washing equipment is too traditional and outdated, and the quality of the washed sand is poor, which greatly reduces the quality and price of the sand. The sand washing and recycling machine successfully solved the problem of poor sand quality.
Sand Washing And Recycling Machine Features
- Environmental Protection: Rational use of sand washing sludge and wastewater to reduce environmental pollution and waste of water resources.
- Operation: The all-in-one sand washing and recycling machine is easy to operate, simplifies the operating personnel, and is convenient for maintenance.
- Energy: Less sand washing loss, rational use, and resource-saving.
Sand Washing And Recycling Machine Application Range
The integrated sand washing and recycling machine is widely used to wash and select materials in sand and gravel fields, mines, building materials, transportation, chemical industry, water conservancy and hydropower, concrete mixing stations, and other industries.
Sand Washing And Recycling Machine Performance
- The mud content of the finished sand is less than 3%, which meets the mud content requirements of sand and gravel aggregates for concrete.
- After dehydration, the moisture content of the finished sand is 17-24%, and there is no open water so that it can be directly loaded and transported abroad.
- The recovery rate of 100to +200 mesh fine sand reaches 70-90%, which can effectively improve resource utilization.
Accessories Performance
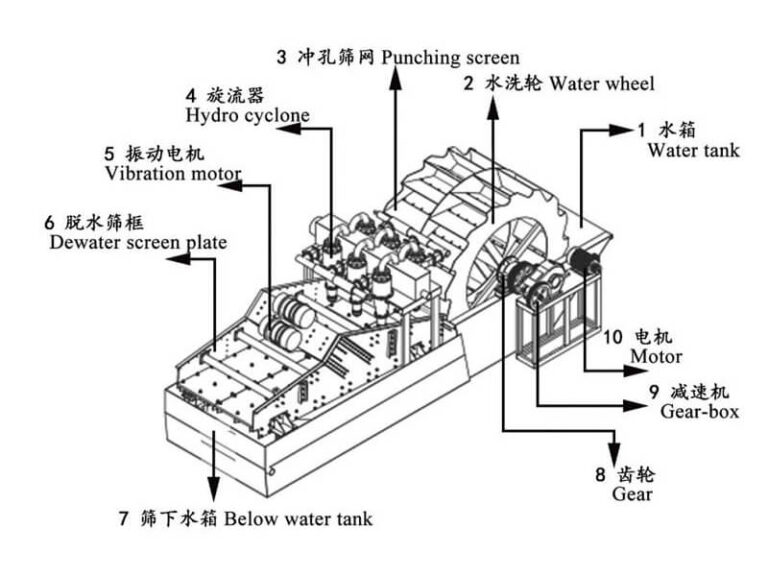
The integrated sand washing and recovery machine is composed of a high-pressure separator, dewatering screen, impeller separator, reducer, high-pressure vacuum pump, cleaning tank, high-level return water tank, motor, vibration motor, and other components.
- Impeller separator: high cleaning degree, large processing capacity, low power consumption, and long service life.
The impeller drive bearing device is isolated from water and water-receiving materials to avoid damage to the bearing due to water immersion, sand, and pollutants, significantly reducing the failure rate.
- Vacuum high-pressure pump: power step-down, tightly sealed, and the slurry is not easy to leak.
The high-pressure vacuum pump is wear-resistant and energy-saving. It adopts advanced design theory and is designed according to the principle of slight loss so that the shape of the flow-passing parts and the flow state of the slurry have achieved ideal results.
- Dehydration screen: The screen surface has self-cleaning performance, no hole blocking, high screening efficiency, and long service life.
Since the polyurethane elastic screen uses steel as the skeleton material, polyurethane has a very high elastic modulus, high strength to absorb impact force and high wear resistance, high tensile strength, and its carrying capacity is that of rubber screen. It is more than 2.5 times that of the mesh, and its service life is 8-10 times higher than that of ordinary metal screens, three times that of stainless steel screens, and 3.9 times that of natural rubber. It is currently a relatively wear-resistant screen material.
- Vibration motor: reasonable design, excellent material selection, high efficiency, low-temperature rise, and long service life.
The excitation force and output of the vibration motor are properly matched, the body is light in weight, the starting torque is large, and the volume is small. Because it uses smooth rotation to generate vibration, the noise is low. The fully enclosed structure can work in any dust without explosion-proof requirements. We are adjusting the angle of the eccentric block to adjust the excitation force. According to the vibration motor’s installation method to change the exciting force’s direction. Multiple units can synthesize various vibration forms to meet different job requirements.
- High-pressure separator: wear-resistant material, high elasticity, and high strength
The separation principle of the high-pressure separator is centrifugal sedimentation. When the slurry to be separated enters the high-pressure separator from the periphery of the high-pressure separator at static pressure, it is forced to make a rotary motion. Due to the different centrifugal force, centripetal buoyancy, fluid drag, etc., the solid coarse particles in the slurry overcome the hydraulic resistance and move to the wall of the vessel, and under the joint action of their gravity, move downward along the wall of the vessel in a spiral. In contrast, the fine and small particles and most of the water is subjected to the small centrifugal force, it will make a rotary motion with the slurry before it gets close to the wall.
- High return water tank
The wastewater discharged from the high-pressure separator plays a buffer role, which is convenient for free drainage in all directions on the site. In addition, the water source in the lower cleaning tank is insufficient, resulting in a poor water supply of the high-pressure vacuum pump, inadequate pressure of the high-pressure separator, and a decrease in centrifugal force. , providing hydration.
- Other widgets
Bottom flow port: It is made of high wear-resistant material. This machine comes with three bottom flow ports of different specifications, which are used by the material content to adjust the material concentration.
Spring: rubber-metal helical composite spring composed of a layer of rubber wrapped around a coiled metal spring. It has the characteristics of non-linearity and structural damping of rubber springs and features of large deformation and large bearing capacity of helical metal springs. , its stability and bearing capacity are superior to those of rubber springs.
The integrated sand washing and recycling machine adopt many advanced structures inside and a beautiful arc-shaped structure design on the outside, making the whole machine more humanized and reducing the damage caused by manual operation.
Common Faults and Solutions of Sand Washing and Recycling Machine
1. The power of the sand suction pump shaft is too large
Possible reasons
- The packing gland is too tight.
- The packing heats up.
- Friction occurs in the pump.
- The bearing is damaged.
- The belt of the driving device is too tight.
- The pump flow rate is too large.
- The speed is too high.
- The specific gravity is large.
- The motor shaft and the pump shaft are not aligned or not parallel.
Treatment methods: loose packing gland bolts, eliminate friction, replace bearings, adjust belts, adjust pump operation, adjust speed, adjust motor shaft, and sand suction pump shaft.
2. The sand suction pump cannot supply water
Possible reasons: air leakage at the suction pipe or filler, incorrect steering, damage to the impeller, blockage of the suction pipe, etc.
Treatment method
- Seal the leaking part.
- Check the steering, and replace the new impeller if necessary.
- Remove the blockage.
3. The bearing life of the sand suction pump is short
Possible reasons: the motor shaft and the pump shaft are not aligned or parallel, the shaft is bent, there is friction in the pump, or the impeller is out of balance, foreign matter enters the bearing, or the amount of lubricating oil is improper, and the bearing assembly is unreasonable.
Treatment method: adjust the motor shaft and pump shaft; change the oil to eliminate friction, replace the impeller with a new one, clean the bearing, change the bearing or reassemble the bearing.
4. Abnormal vibration and loud noise of the sand suction pump
Possible reasons: The bearing damage causes an unbalanced impeller, air intake in the suction pipe, uneven flow due to clogging, and pump evacuation.
Treatment method: Replace new bearings and impellers if necessary; avoid air intake, clean up blockages, and improve the feeding situation of the pump.