With the rapid development of modern industry, human demand for natural mineral resources is increasing daily. The mineral dressing process refers to the process of continuous processing of ore. The mineral dressing is a constant production process consisting of ongoing operations. Mineral raw materials enter the sorting operation after crushing to separate valuable minerals from gangue or various beneficial minerals from each other.
The separation operation is the critical operation (or main operation) of the beneficiation process. It adopts different beneficiation methods according to the other properties of minerals. Separation operations include gravity separation, flotation, magnetic separation, electric separation, picking selection, and chemical beneficiation.
1. Gravity Separation
Gravity beneficiation is referred to as gravity separation. It is a beneficiation method for separating minerals according to their specific gravity and settling velocities in the medium.
The gravity separation process uses water, air, heavy liquid, and suspension as separation media. A heavy liquid is a liquid whose specific gravity is greater than water, and a suspension is a two-phase liquid composed of water and solid particles suspended in it. The gravity separation process is carried out in the medium.
Features
- In the medium (mainly water) flow, the different proportions of mineral raw material particles are used for separation, including heavy medium separation, jig separation, shaker separation, chute separation, etc.
- Gravity separation is the primary beneficiation method for wolframite, cassiterite, placer gold, coarse-grained iron, and manganese ore.
- Gravity separation is widely used in sorting rare metal placers.
- Gravity is suitable for a wide range of particle sizes, from several hundred millimeters to less than one millimeter.
- Mineral processing cost is low, less environmental pollution.
If the particle size of the mineral is within the above range and the specific gravity of the components differs significantly, gravity selection is the most suitable method. Sometimes, gravity separation (mainly heavy medium separation, jigging separation, etc.) can be used to pre-select part of the waste rock and then use other methods to reduce the cost of mineral processing. With the increase of lean ore and fine mineral raw materials, gravity separation equipment tends to be large-scale and multi-layered, and compound motion equipment, such as centrifugal concentrators, shaking beds, vibrating chutes, etc., are used to improve the gravity separation of fine-grained materials efficiency. At present, gravity separation has been able to select 20μm materials effectively. Gravity selection is the essential coal preparation method.
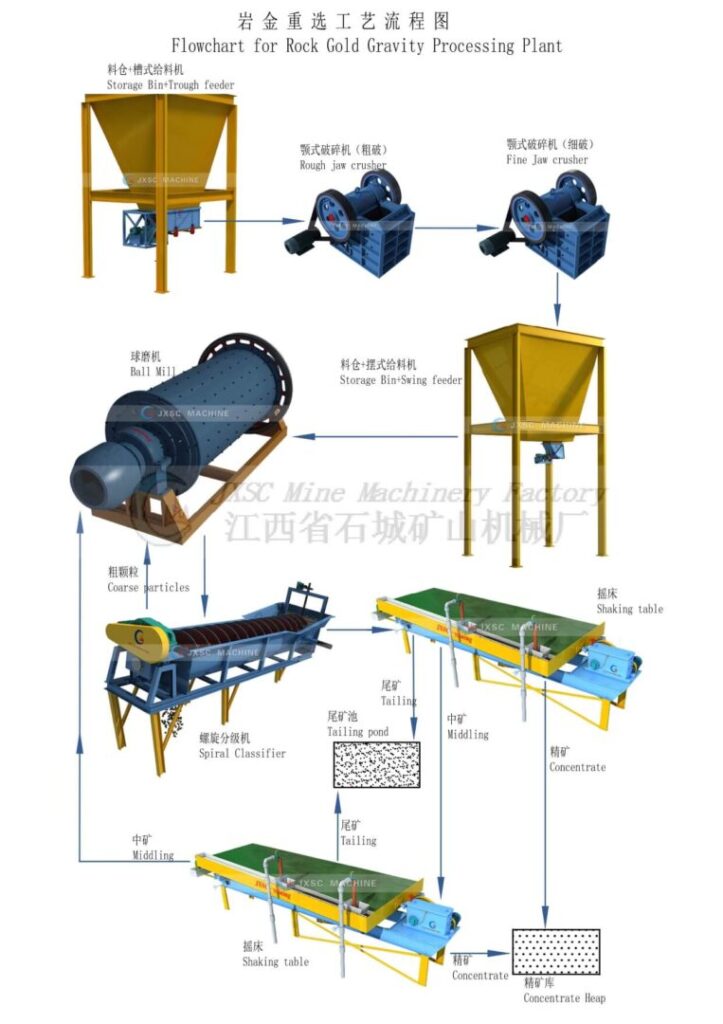
2. Flotation
Flotation uses the difference in wettability (hydrophobicity or hydrophilicity) of the surface of various mineral raw material particles to water to selection. It usually refers to froth flotation. Few natural hydrophobic minerals often add collectors to the pulp to enhance the hydrophobicity of the minerals to be floated. Add various regulators to improve selectivity. Add a foaming agent and inflate to generate air bubbles, so that hydrophobic mineral particles are attached to the air bubbles, float, and separate. Flotation can process materials smaller than 0.2-0.3mm. In principle, it can sort various mineral raw materials, which is the most widely used method. Flotation can also be used to sort intermediate smelting products and ions in solution (see ion flotation) and treat wastewater. In recent years, some new methods for recovering fine materials (less than 5-10 μm) have emerged in addition to large-scale flotation machines. For example, selective flocculation-flotation, using a flocculant to make certain fine-grained materials form larger flocs selectively and then separate them by flotation (or desliming); shear flocculation-flotation, plus collection Stir with high intensity after adding the agent, etc., so that the fine-grained minerals form flocs and then flotation, and carrier flotation, oil agglomeration flotation, etc.
3. Magnetic Separation
Magnetic separation uses the difference in magnetic properties of mineral particles to sort in an inhomogeneous magnetic field.
The weak magnetic field separator separates strong magnetic minerals (magnetite, pyrrhotite, etc.)
The high magnetic field magnetic separator separates weak magnetic minerals (hematite, siderite, ilmenite, wolframite, etc.)
The weak magnetic field magnetic separator is mainly an open-circuit magnetic system composed of permanent magnets. The high-field magnetic separator is a closed-circuit magnetic system that primarily uses an electromagnetic magnetic system. Weak magnetic iron minerals can also be turned into strong magnetic minerals through magnetization roasting and then separated by a weak magnetic field magnetic separator. The structure of the magnetic separator is drum type, belt type, rotary ring type, disc type, induction roll type, and so on. The magnetic pulley is used for pre-selecting massive strong magnetic ore. The primary development trend of magnetic separation is to solve the recovery problem of fine-grained weak magnetic minerals.
4. Electric Separation
Electric separation uses the difference in the electrical properties of mineral particles to separate in a high-voltage electric field. It mainly uses to sort conductors, semiconductors, and non-conductor minerals.
Electric Separators Classification
- Accord electric field: Electrostatic separators, corona separators, and composite electric field separators.
- Accord the charging method of ore particles: Contact electrification separators, corona electrification separators, and friction electrification separators.
Features
- The electric separator has a narrow particle size range and low processing capacity, and raw materials need to be dried, so the application is limited.
- The cost is not high, the separation effect is good, and the pollution is less.
- The electric separation mainly uses for the selection of coarse concentrates, such as the separation of white Tungsten ore, cassiterite, zircon, rutile, ilmenite, tantalum-niobium ore, monazite, etc.
- Electric separation is also used for grading and dust removal of mineral raw materials. The development trend of electric separation is to develop equipment with large processing capacity and high efficiency in separating fine-grained materials.
5. Picking Selection
Picking includes the manual and mechanical selection. It is mainly used for pre-selecting and discarding waste rocks.
Hand selection is based on the external characteristics of minerals, with manual selection. This ancient beneficiation method is still used in some mines.
Mechanical sorting includes
- Optical sorting, using the differences in the optical properties of minerals;
- X-ray sorting, using the characteristics of fluorescence under X-ray irradiation;
- Radiation sorting, using the natural radioactivity of uranium, thorium, and other minerals. In the 1970s, electric and magnetic sorting using mineral conductivity or magnetism began to appear.
6. Chemical Beneficiation
Chemical beneficiation uses the difference in the chemical properties of minerals to separate and recover valuable components by chemical methods or a combination of chemical and physical processes to obtain chemical concentrates. This method is more adaptable than the usual physical beneficiation method and has a better separation effect, but the cost is higher. It is often used to deal with mineral raw materials, intermediate products, or tailings that are difficult or impossible to process with physical beneficiation methods. With the increasing number of complex, refractory, and fine-grained mineral raw materials, combining physical and chemical beneficiation processes has attracted more and more attention. Examples of successful applications of chemical separation include cyanidation gold extraction, acid leaching-precipitation-flotation, separation-flotation treatment of copper oxide ore, etc. Applying techniques such as solvent extraction, ion exchange, and bacterial leaching has further promoted the development of chemical separation. Its trend is: to develop more effective leaching agents and extractants, develop biochemical methods, reduce energy consumption and costs, and prevent environmental pollution.
In addition, mineral raw materials use the difference in friction coefficient and collision recovery coefficient to separate friction and bounce when they are moving or colliding on an inclined plane.