With the acceleration of urbanization, the increase in the amount of waste has become a common concern. In order to solve the problem of waste disposal, thermal waste-to-energy plants have come into being. However, waste-to-energy plants generate metal wastes in the process of waste treatment, and these metal wastes, if not handled properly, can cause serious harm to the environment and human health. This post will discuss metal wastes from waste-to-energy plants and how to recycle them.
Metal Wastes From Wast-to-energy Plant
What Metals Are Contained in The Slag of a Waste-to-energy Plant?
Slag from waste-to-energy plants contains metals such as iron, zinc, copper, chromium, manganese, aluminum, and silicon.
The slag from waste-to-energy incineration plants consists of two main components: the metal contained in the waste itself and the metal oxides generated during the incineration process. These metals are oxidized, decomposed, and passivated at high temperatures during the waste incineration process, and eventually remain in the form of slag. The metal components in the slag include but are not limited to, iron, zinc, copper, chromium, manganese, aluminum, etc. These metals exist in the slag mostly in the form of oxides, hydroxides, and carbonates. In addition, the slag may contain a small amount of unburned organic matter and other impurities, which are not completely burned during the incineration process and therefore remain in the slag.
The amount and types of metals in the slag are affected by the composition of the waste and the treatment process. For example, some metals may be recycled during the incineration process, while others may be present in different forms in the slag depending on the incineration conditions. Therefore, the composition and content of metals in the slag have a certain range of variability, but common metal compositions mainly include the ones mentioned above.
What Are The Sources of Metals in Waste-to-energy Plant Slag?
The main sources of metals in the slag of waste-to-energy plants include metal products such as cans, nails and tin cans, as well as residues from the incineration process of plastics, wood and bamboo, food waste, paper and other waste.
- Iron
Iron is the most common metal in the slag of waste-to-energy plants and the most abundant metallic element in the slag. The iron in the slag mainly comes from metal items in the waste, such as cans and steel bars, and the iron content can usually reach about 10%. - Aluminum
Aluminum in the slag of waste-to-energy plants mainly comes from food packaging, aluminum foil, etc. in the waste, and the content is generally around 3%. Aluminum in slag can be recycled due to its high recovery rate. - Copper
Copper is an important industrial metal and one of the important metal elements in the slag of waste-to-energy plants. The copper in the slag mainly comes from wires and cables in the waste, and the content is usually around 1%. - Zinc
Zinc in the slag of waste-to-energy plants mainly comes from batteries, galvanized iron, etc. in the waste, and the content is generally around 0.5%. Zinc is an important metallurgical metal that can be recycled.
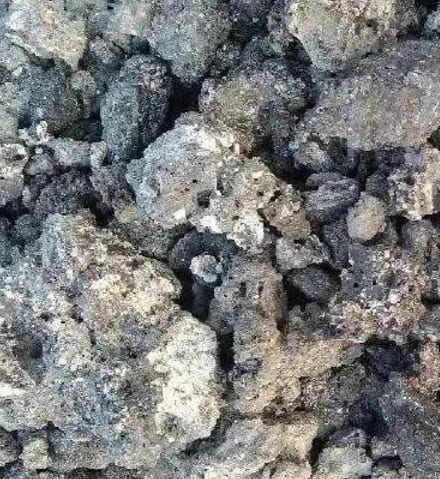
Hazards of Metal Waste From Waste-to-energy Plants
The hazards of metal waste are mainly reflected in the following aspects:
- Environmental pollution: metal waste can pollute soil and water sources if discharged directly into the environment without proper treatment. These metal elements may enter the human body through the food chain, posing a threat to human health.
- Hazard to human health: Certain metal elements such as lead and mercury are toxic and can cause damage to the human nervous system, kidneys, liver, etc., and may even lead to serious diseases such as cancer.
- Waste of resources: The recycling value of metal wastes is neglected, leading to a waste of resources. If these metal wastes can be effectively recycled and reused, it will not only reduce environmental pollution but also save natural resources.
How to Recover Metals From Waste-to-energy Plants?
Metal waste generated in the process of waste treatment in waste incineration power plants poses a threat to the environment and human health, and its harm needs to be reduced through effective management and technical means. In order to reduce the harm of metal waste to the environment and human body, the following measures should be taken:
- Improve the efficiency and accuracy of waste classification and reduce the waste containing metal into incinerators.
- Enhance the recycling and treatment technology of metal waste to increase the recovery rate of metals.
- Properly dispose of metal wastes generated in the incineration process to avoid their harm to the environment and human body.
Technical Methods for Metal Recycling From Power Plant Slag
1. Physical sorting method
The use of metal and cinder physical property differences, such as density, magnetism, etc., through the sieve, magnetic separation, and other methods to separate metal and cinder. This method is simple and easy to implement, suitable for high metal content and a single type of ash.
2. Chemical leaching method
The use of chemical reagents and the metal in the ash reaction, which will be converted into soluble compounds, and then through precipitation, filtration, and other steps to separate the metal. This method is suitable for ash with low metal content or complex types.
3. Bioleaching method
Using the metabolism of microorganisms, the metal in the ash is transformed into soluble compounds, thus realizing the recovery of metal. This method has the advantages of environmental protection and low energy consumption and is a future research hotspot in the field of metal recycling.
Recovery Process of Metals in Waste Power Plant Slag
Magnetic separation + flotation: Firstly, iron and other magnetic metals are separated by a magnetic separator, and then non-magnetic metals are extracted by flotation or chemical leaching, etc. to realize the separation and recovery of metals.
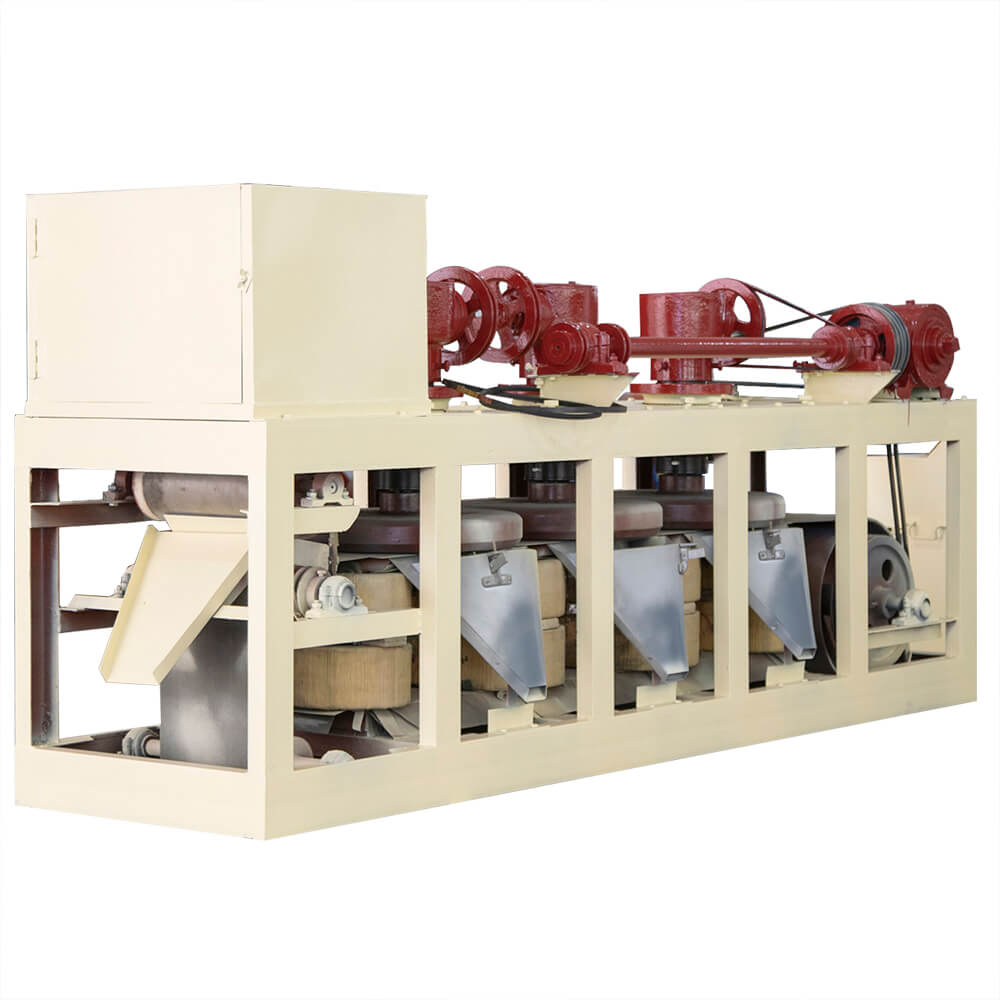
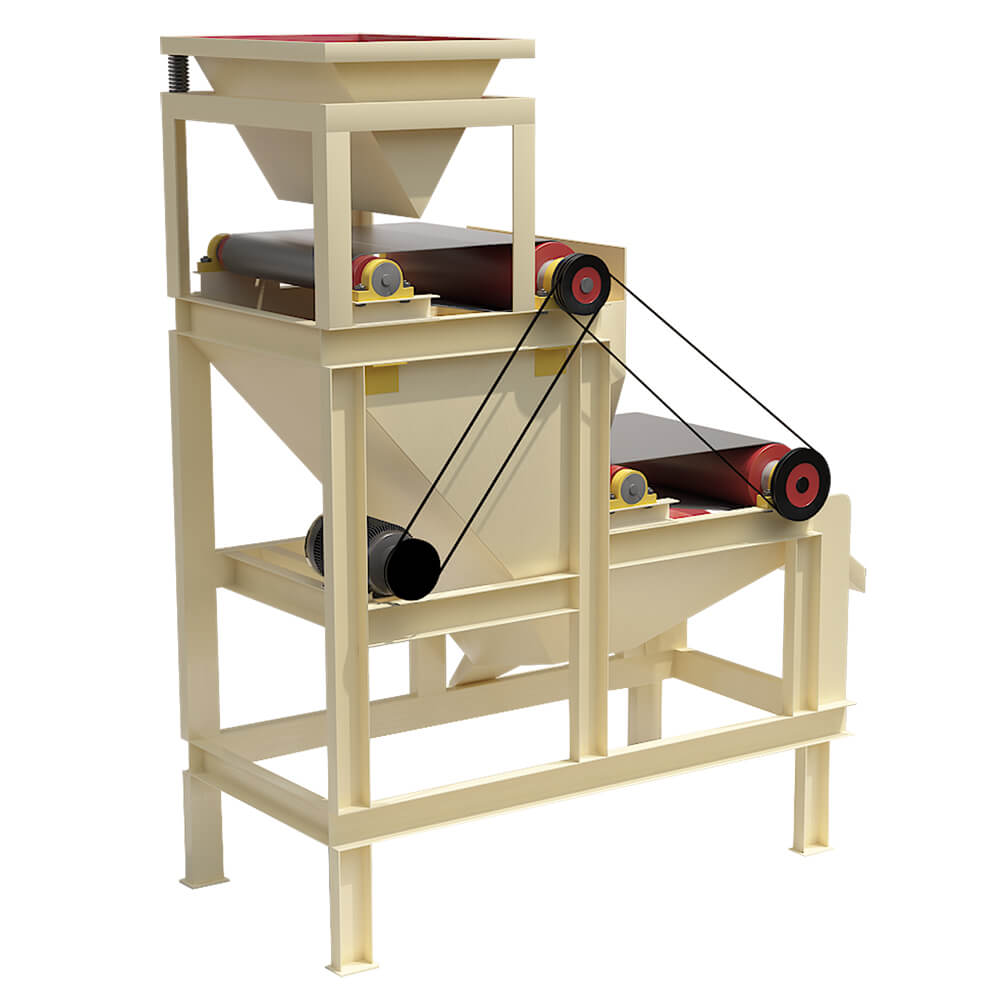
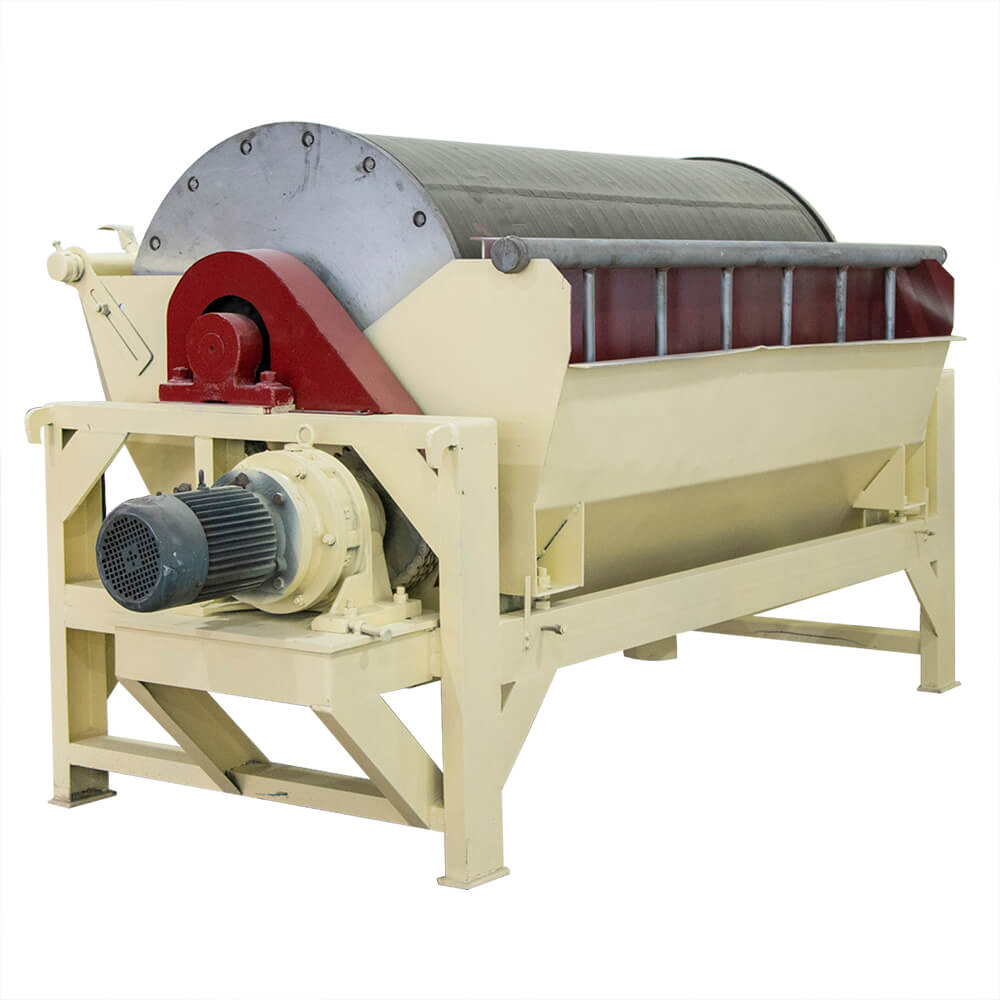
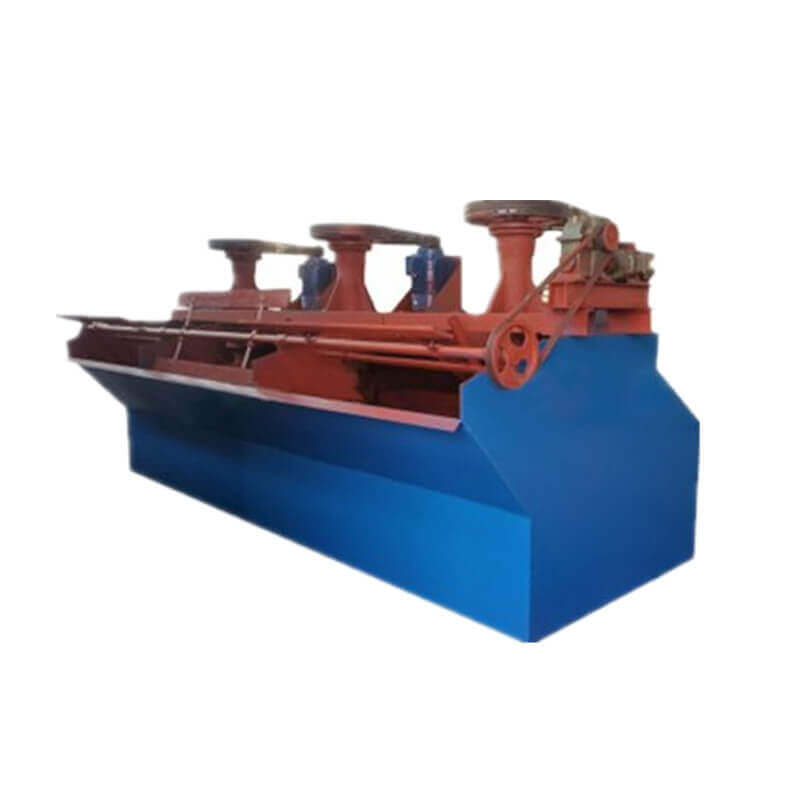
Magnetic separation + gravity separation: first of all, it is necessary to go through magnetic separation to recover the magnetic ferrous materials therein, then use a jigger to recover the remaining metals, and finally use eddy current to recover the aluminum in the tailings of jigger, while the metals recovered by jigger are mainly copper, tin, lead, zinc, gold, silver, these metals with larger specific gravity, manually select the gold, silver and other precious metals, and then the rest of the metal mixture into the shaking table sorting can be done.
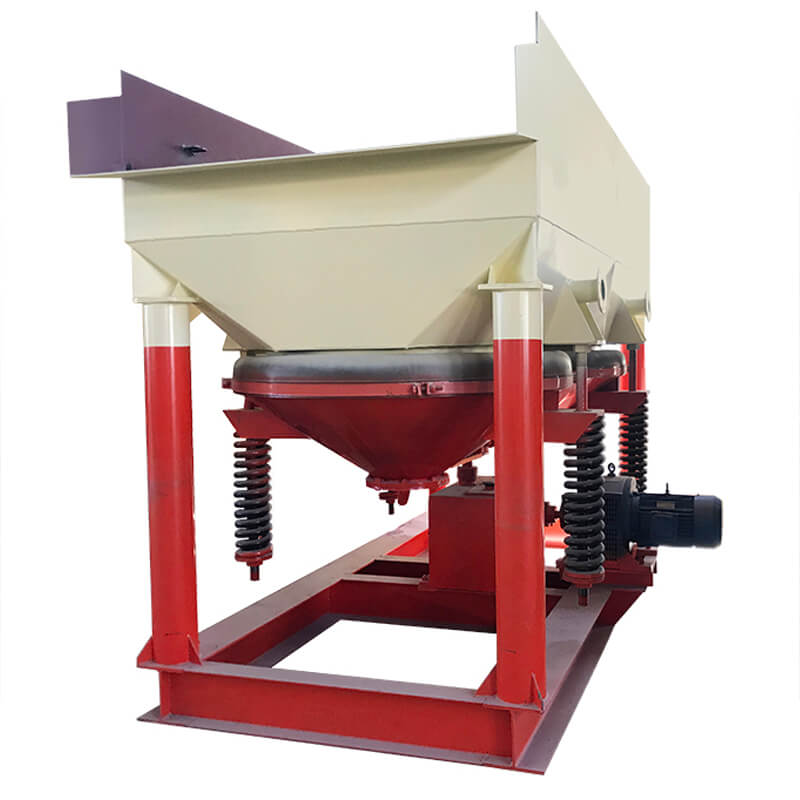
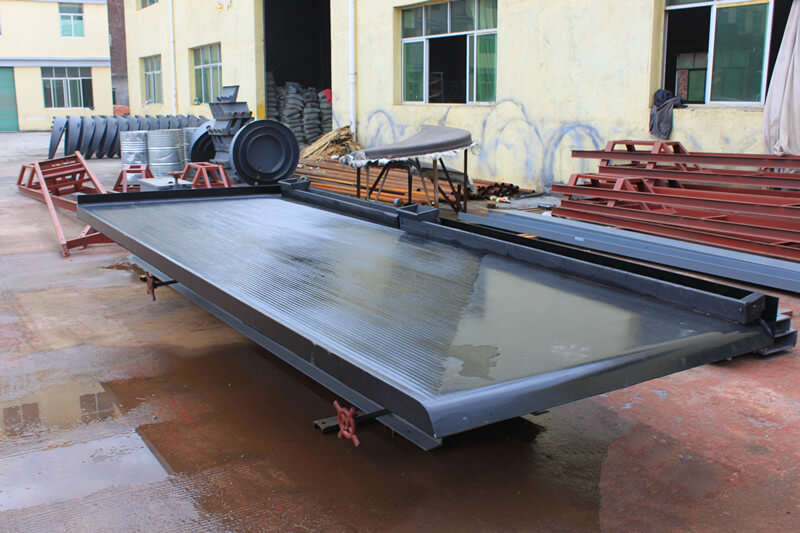
This is only two of the many metal recovery process, there are other different processes used to recover the metal in the waste incineration residue, as to which process and equipment, the key is still to decide according to the actual situation.