The mining jig separator is also called a large particle jig. It is a mineral processing jig used to process coarse-grained ore. The machine uses the upper and lower screens to discharge materials at the same time. It can handle 0-30mm particle size. Materials are pre-selected and selected. It is mainly used for processing hematite, limonite, mirroring, pyrite, manganese ore, garnet ore, celestite ore, barite ore, fluorite ore, and other metal and non-metallic minerals, and for chromite slag, the treatment of industrial smelting waste residues such as silicomanganese slag also has excellent results.
Optimum feed particle size for jig machine
The jig is mineral processing equipment. Like other mineral processing equipment, it has a specific feed particle size. Choosing the appropriate jig equipment and the optimal feed particle size will significantly impact the jig mineral processing indicators.
The feed size of the jig machine is 0-30mm, enabling jig selection of coarse, medium, and fine-grained minerals. However, in actual production, the crushing or grinding of the ore needs to be determined based on the embedding characteristics and properties. Fineness, and then choose the corresponding jig selection based on these factors rather than deciding the crushing particle size of the ore based on the selected particle size of the jig.
Using coarse-grained jig machines for coarse-grained iron minerals, manganese ore, barite, celestite, etc., Using trapezoidal jigs and down-moving jigs for medium & fine-grained ore beneficiation. For mineral beneficiation with finer particle size, it is best to use a sawtooth wave jig to improve the recovery effect of fine-grained heavy minerals.
Therefore, the optimal selection particle size of the jig is determined by its structure. In order to achieve the best jig mineral processing effect, it is necessary to consider not only the optimal selection particle size of the jig but also the embedded characteristics of the ore. As well as the properties of the ore, the corresponding jig selection is determined after determining the degree of monomer dissociation of the ore to achieve better mineral processing indicators.
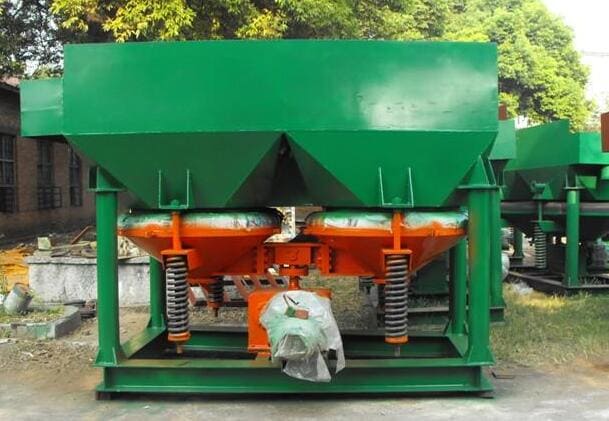
Advantages of mining jig
- Energy saving, high efficiency, and environmental protection.
- The selected particle size range is wide, and 0-30mm particle size minerals can be selected without classification.
- The upper and lower parts are discharged simultaneously, and the concentrate can be discharged in stages.
- Stable continuous working performance, using high wear-resistant technology, and long equipment service life.
Recycling Effect of Sawtooth Wave Jig Mineral Processing
The pulsation curve generated by the jig is a sawtooth waveform, which has the characteristics of uniform rising water flow and rapid falling water flow. The water flow fluctuation curve generated during regular operation is a sawtooth waveform, which enhances the suction effect during the jig dressing process and is highly effective. It benefits the recovery of fine-grained minerals, has water-saving characteristics, and continuously operates. The sawtooth wave pulsation cycle curve of the sawtooth wave jig has a pronounced effect on the beneficiation of fine-grained heavy mineral deposits, and the recovery rate reaches a high level. It occupies a critical position in many mineral processing fields. It is also widely used in the selection and sorting of tailings recovery. Because of its low price, large processing capacity, energy saving, and environmental protection, more and more customers choose it.
It mainly uses the sawtooth wave jig for the beneficiation of tungsten, tin, gold, iron, manganese, titanium, chromium, sulfur, other minerals, manganese slag, chromium slag, stainless steel slag and other smelting slag recovery alloy particles, metal recovery in mine beneficiation tailings, tailings treatment, etc. Because of its large particle size, wide particle size, and high mineral processing efficiency, it is sought after by many customers.
The sawtooth wave jig feeds the materials to be sorted into the container space, which rotates around a straight centerline at high speed. This space is equipped with a device with adjustable stroke and frequency of incited water flow in the radial direction. The horizontally layered mineral deposits and gangue are discharged from the upper hole of the device under the effect of incited water flow, and the light mineral deposits are discharged along the device. The walls are discharged upward, performing a helpful sorting process on the mineral deposits.
The sawtooth wave jig machine stratifies fine-grained light and heavy mineral deposits laterally according to density and adds a device to incite water flow in the direction of mineral deposit stratification so that the jigging process also proceeds perpendicular to gravity. The mineral deposits after centrifugation are stratified very evenly, and coupled with the jig flow of large and small strokes; the fine-grained mineral deposits are effectively recovered. After sorting and recycling by the sawtooth wave jig machine, the tailings can be reused, effectively reducing the waste of resources.
Jig Separator for Tin Solution
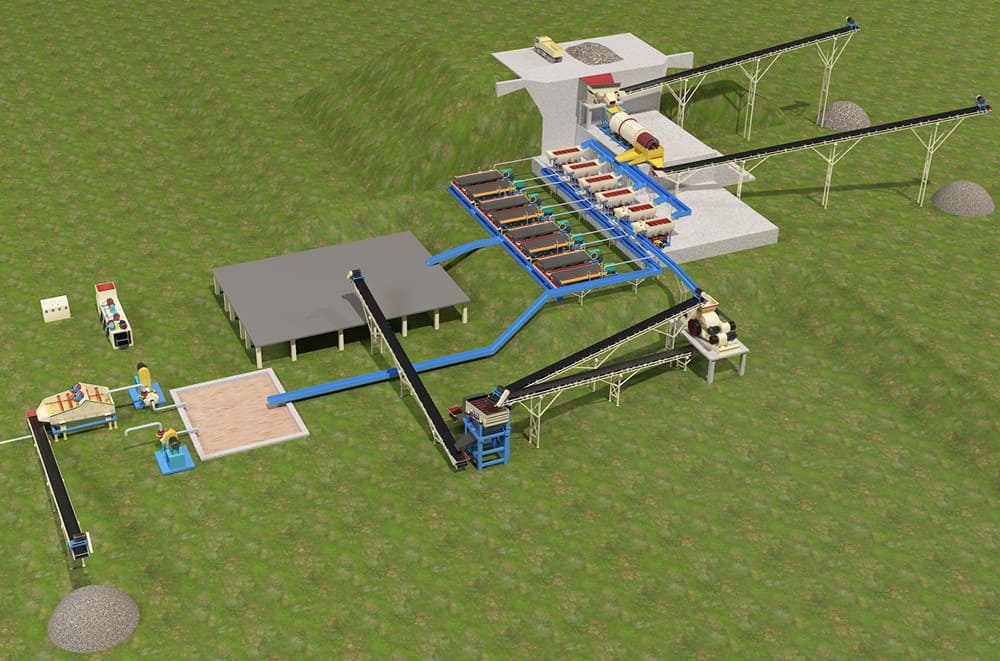
This complete setup is Coltan(Ta-Nb), Tin, Tungsten Washing & Concentration Plant.
It is configured with a Vibrating Feeder to feed raw material and remove oversized rocks.
Trommel Scrubber to wash off the sticky mud from raw ores, and screen out three size ranges, the Ta-Nb, Tin grains will be released more easily from the cleaned ores.
Jig Separator is a gravity roughing concentration machinery, the over-screen big-grained concentrate of Jig will be crushed & sieved by Double Roller Crusher & Vibrating Screen, to get -2mm fine concentrate and transport to shed for drying in the sun. The under-screen concentrate of the Jig will feed to the Shaking Table for further concentration.
JXSC Shaking Table enjoys a very high recovery ratio for processing Coltan and Cassiterite, its concentrate will also convey to the shed for drying.
The final concentration equipment is the Three-Disc Dry Magnetic Separator, widely used for Tin, Cassiterite, and Coltan enrichment. Using this separator can separate 4 different minerals at one time, and the concentrate grade can reach 60%-70%.
The capacity for this processing plant can be customized as per request such as 30tph, 50tph,100tph, etc.