Lead and copper are non-ferrous metals, and their distribution and formation conditions vary. However, they often coexist in nature under certain specific geological circumstances. In copper ores, lead is usually present as an impurity. During metal processing and treatment, lead and copper can form alloys, such as lead-copper alloys, which are used to manufacture various industrial products, such as pipes and coins.
How to Remove Copper From Lead?
In the field of copper ore processing, effective separation of lead from copper is crucial. The following are some of the mainstream lead-copper separation methods.
Blow-refining
As a traditional method of removing copper from lead, the Blow Refining Method is particularly suitable for low-copper-content ores (less than 5% copper). It uses the difference in redox properties between copper and lead by heating the ore and blowing in oxygen or air so that copper oxidizes into copper oxide and is taken out by the gas, while the lead stays in the metal state in the furnace and finally realizes the separation.
Specific Steps of Blow-refining
- The copper ore is crushed into small particles and placed in the furnace to be heated.
- While the copper ore is burning, oxygen or air is continuously blown into the furnace so that the copper is oxidized into copper oxide (CuO).
- Lead, on the other hand, is not easily oxidized due to its poor oxidizing properties and remains in the furnace in a metallic state.
- Using the effect of gas flow, the copper oxide will be brought out of the furnace, and through the condenser cooling and precipitation to get pure copper.
- Lead, on the other hand, exists in the furnace in the form of lead oxide (PbO) and is eventually discharged as slag.
Reverse Extraction
For high copper-bearing ores, the counter-extraction method is particularly efficient. The principle is to utilize the selective extraction ability of a specific extractant for copper to extract the copper from the ore solution, leaving the lead unaffected. By adjusting the extraction conditions, the extracted copper can be further reduced to metallic copper to achieve the separation purpose.
Specific Steps of Reverse Extraction
- Crush the copper ore into small particles and add them to the solution.
- Add a specific extractant, such as petroleum ether, acid ester, etc., to the solution.
- The extractant may be chosen to extract copper and not lead. This means that the extractant can extract copper from the solution without affecting the presence of lead.
- By adjusting the pH of the extractant or other conditions, the extractant can be made to reduce the extracted copper to a metallic state, thus obtaining pure copper.
- Lead is present in the residual solution that has not been extracted, and can be separated from other metals by further treatment.
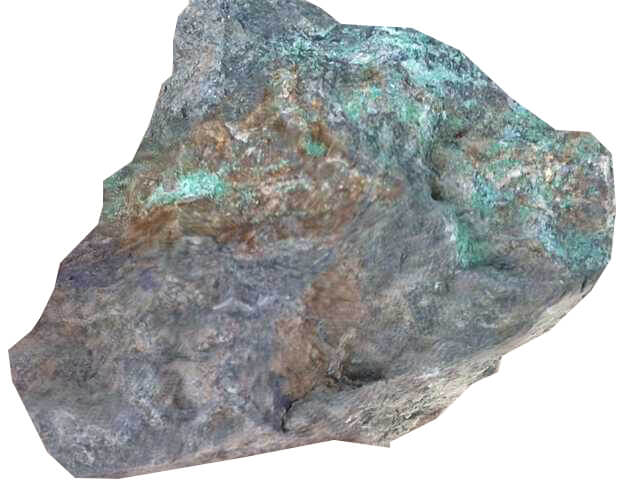
Electrolysis
Electrolysis, a modern technique, is widely used for the purification of copper ores. It realizes the complete separation of copper and lead by setting up a cathode and anode in an acidic solution and using electrochemical reactions to reduce copper ions to metallic copper at the cathode. Lead is oxidized to ions at the anode and taken out of the solution to be deposited on the anode.
Specific Steps of Electrolysis
- The copper ore is crushed into small particles and added to a certain concentration of acidic solution.
- Hang a copper plate or other conductor in the solution and use it as the cathode.
- another lead plate or other conductor is placed in the solution and used as the anode.
- By applying a voltage, the copper ions at the cathode are electrochemically reduced to form copper metal.
- At the same time, the lead on the anode is oxidized to ions, which are carried out of the solution and eventually deposited on the anode.
The primary advantage of using electrolysis to process high copper content ores is the ability to achieve extremely high purity levels of copper, making it ideal for applications requiring high electrical conductivity. Electrolysis effectively removes impurities by selectively depositing only copper ions onto the cathode, resulting in a refined copper product with minimal contamination, which is particularly valuable in the electronics industry. By electrolysis, complete separation of copper and lead can be achieved.
Key advantages of using electrolysis for copper processing
- High production efficiency
Electrolysis is a highly efficient smelting technology with much higher production efficiency than traditional smelting methods, which can significantly increase production capacity and shorten production cycles, thus reducing production costs. - High Purity
Electrolysis allows for the production of very high-purity copper (greater than 99.9%) by selectively depositing copper ions from the electrolyte solution onto the cathode, leaving behind impurities at the anode. - Controllable Process
The purity of the final copper product can be precisely controlled by adjusting parameters like current density, electrolyte composition, and electrode design. - Recovery of Valuable Impurities
Impurities that dissolve from the anode during electrolysis can be collected as “anode slime” which may contain valuable metals like gold, silver, and platinum, allowing for their potential recovery. - Environmentally Friendly
The electrolysis method uses fewer chemicals in the production process and consumes much less energy than the traditional smelting method. Compared to traditional smelting processes, electrolysis can generate fewer harmful emissions, potentially reducing environmental impact, and it can better protect the environment.
Lead copper removal is an important method for purifying copper, and blowing refinement, reverse extraction and electrolysis are the main technical means in the field of lead copper separation. Each of these methods has its unique applicable scenarios and advantages, and different methods can be selected for lead copper removal according to the different conditions of copper ores.