Progress in ilmenite flotation research
Ilmenite (FeTiO3) has a theoretical TiO2 content of 52.63% and is the main mineral for extracting titanium and titanium dioxide. The ilmenite beneficiation process depends on factors such as deposit type, ore properties, and mineral composition. Since the properties of primary titanium ores are relatively similar and the target minerals are relatively simple, the ore beneficiation methods and process flows used have common characteristics.
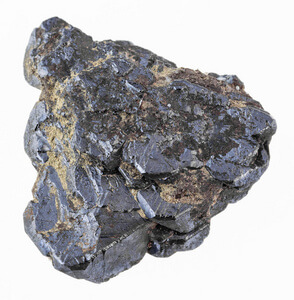
Single Flotation or Magnetic Separation Process
The primary ilmenite developed industrially is a composite deposit containing iron and titanium. The ore dressing process is divided into two parts: iron beneficiation and titanium beneficiation. The raw material of the titanium dressing plant is tailings from iron dressing. Titanium separation methods include gravity separation, magnetic separation, electric separation, and flotation. The industrial processes for selecting titanium include the following:
For ilmenite ore with fine particle size, titanium concentrate can be obtained directly by flotation after grinding and beneficiation or a wet strong magnetic separator can be used as roughing equipment, and the magnetic separation concentrate can be recovered by flotation( Single flotation method or magnetic separation). The flotation process is relatively simple and easy to operate and manage, but the use of flotation reagents will increase the cost of mineral processing.
Flotation process
Flotation is an effective method for recovering fine-grained ilmenite. Flotation is used for primary titanium-containing ores separation, especially for fine-grained titanium-containing ores separation. Sometimes it is also used in the concentration of coarse concentrates. Flotation is an effective method for recovering fine-grained ilmenite. Before ilmenite flotation, sulfide minerals must be separated by flotation, and then ilmenite flotation is carried out. Sulfide flotation adopts the conventional flotation agent system, that is, xanthate is used as the collector, 2# oil is the foaming agent, and sulfuric acid is the pH adjuster. Some processing plants also use copper sulfate as the activator for sulfide flotation. The flotation research on ilmenite is generally the research on flotation reagents. Commonly used collectors for ilmenite are mostly fatty acids. In foreign countries, they are mostly oleic acid and its salts, such as tar oil soap or collectors mixed with kerosene. Commonly used collectors include fatty acid collectors, arsenic-containing collectors, hydroxamic acid collectors, etc. The commonly used activators in ilmenite flotation are mainly lead nitrate, the pH adjusters are generally H2SO4, and the inhibitors mainly include water glass, oxalic acid, sodium hexametaphosphate, carboxymethylcellulose (CMC), etc. The single flotation method is a more effective beneficiation method for fine-grained titanium vein ore. The single flotation process is simple and easy to operate and manage. However, because the consumption of chemicals will increase costs and there are environmental protection issues caused by tailings discharge, it is currently widely used in industry.
Magnetic separation process
There are many kinds of titanium minerals. More than 140 titanium minerals with TiO2 content greater than 1% have been found. However, at this stage, only a few minerals have utilization value, mainly ilmenite and rutile, followed by leucoxene, anatase, red ilmenite, brookite, and perovskite. Ilmenite accounts for about 85-95% and is currently the main source of titanium and titanium products. 41.4% of ilmenite is found in mineral sand deposits, and 58.4% is found in vanadium titanomagnetite – titanium magnetite. Ilmenite: Hexagonal crystal system, the crystal shape is a thick plate, usually brown, has a metallic luster, medium magnetism, and is a good conductor. Due to the close symbiosis between ilmenite, magnetite, and hematite, the titanium content is lower than the theoretical value; in addition, due to partial oxidation, the ilmenite can be altered to increase the titanium content, forming leucoxene(TiO2·nH2O). The theoretical grade is 52.63%, Mohs hardness is 5-6, and specific gravity is 4.7-4.78. Ilmenite beneficiation is generally carried out using a magnetic gravity separation process. This combined beneficiation process has the advantages of large processing capacity, simple operation, low equipment investment, and good beneficiation effect.
According the different ilmenite mineral types, divide the beneficiation process into the following types:
- Ilmenite-magnetite beneficiation
Because ilmenite in the ore often appears as an independent inclusion in the magnetite and non-metallic minerals, the principle of processing this type of ore is to throw the tail as coarsely as possible, and then grind and magnetically separate to select the ilmenite concentrate. When there is sulfide, first float the sulfide concentrate, then float the fine-grained ilmenite. - Hematite-ilmenite type mineral processing
The hematite and ilmenite in this type of ore are fine-grained and closely symbiotic. Ore dressing can only select the titanium-iron mixed concentrate, and then pyrometallurgy to obtain pig iron and high-titanium slag. - Perovskite-titanium magnetite mineral processing
Wet weak magnetic separation is first used to select titanomagnetite, calcite is floated using fatty acid collectors, and ilmenite is floated after removing the medium ore.
The beneficiation process of ilmenite depends on the nature of the material. Since the specific gravity of titanium minerals is larger than non-metallic gangue minerals, gravity separation can be used for pretreatment, roughing, or tailing. The magnetic separation method is widely used in iron removal operations to improve the concentrate grade of ilmenite and can also be used to remove gangue. Ilmenite with a small specific gravity is used for enrichment operations. The electro-separation method is mostly used for purification operations when the ilmenite concentrate selected by other processes contains various non-conductive minerals. Flotation is more suitable for primary ilmenite fine-grained ores mineral processing operations.
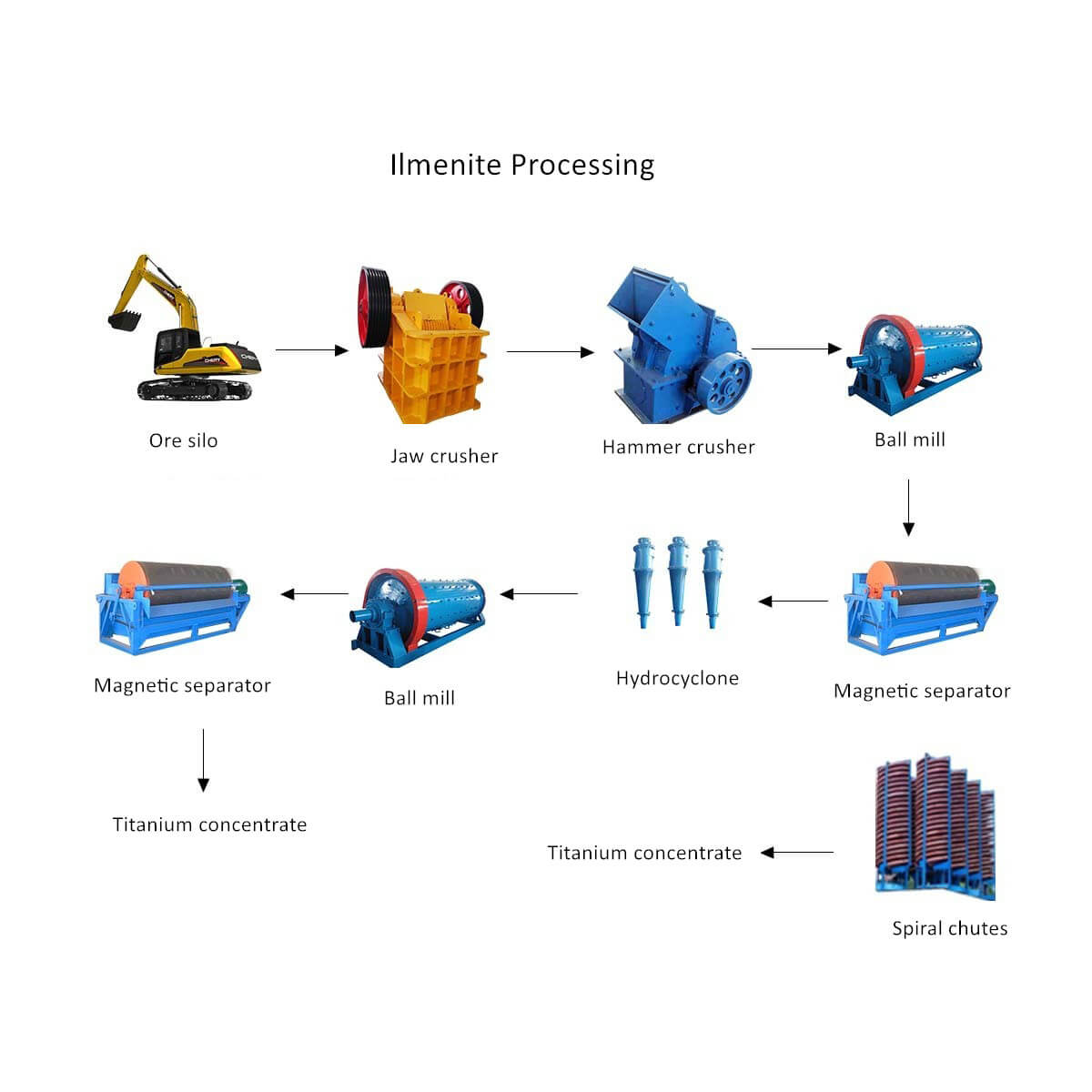
Combined Process
Since titanium mineral is a complex composed of multiple minerals, it is difficult to separate titanium with high-grade and low impurities using one mineral processing method based on the structural properties and compositional characteristics of the different mineral areas that make up it. The main methods of the combined separation process include gravity separation – flotation, gravity separation – electric separation, magnetic separation – flotation, and magnetic separation – gravity separation – flotation. Among them, the processes of adding dispersant, medium magnetic field to remove strong magnetic minerals, strong magnetic roughing, and electric separation are used. The grade and recovery rate of the obtained titanium concentrate are significantly improved. At the same time, strong magnetic – flotation is still a better method for treating fine-grained ilmenite. When selecting ilmenite, the main beneficiation processes include “gravity separation – strong magnetic separation – flotation” and “gravity separation – strong magnetic separation – electric separation (sulfur removal before separation)”. During the mineral processing process, it is necessary to strictly select according to the classification level and adopt different technological processes. The combined processes to separate ilmenite is the development direction of ilmenite beneficiation technology.
Gravity separation – electric separation
The gravity separation first discards low-density gangue or waste rock minerals, and electro-separation treats the obtained coarse concentrate to obtain ilmenite concentrate. For sulfur-containing ores, flotation removes the sulfide minerals before electro-separation. The characteristics of the gravity separation – electro separation process are rough selection by gravity separation and fine selection by electro separation. The equipment used in gravity separation is mainly a spiral concentrator (including a spiral chute), followed by a shaking table. The gravity separation use cone concentrator has reached the industrial trial stage but has not yet been officially used in production. In the gravity and rough separation stage, the purpose is to discard low-density gangue and obtain coarse concentrate for power supply selection. The equipment used in electric separation is a roller electric separator, to further enrich the gravity separation coarse concentrate, so that the product reaches the final concentrate standard. For sulfur-containing ores, flotation is usually used as an auxiliary process to remove sulfide ores between the coarse and fine concentration processes. The gravity separation-gravity separation method has attracted much attention because of its low production cost and low environmental pollution. Shaking tables are widely used in ilmenite beneficiation, especially in some small mines that use shaking tables to obtain qualified concentrates. As the final check operation in the production of titanium concentrate, electric separation has been widely used.
Gravity separation – magnetic separation – flotation
Send the materials to classify. The coarse particles are roughly separated by gravity and magnetic separation, and the fine particles are flotation to obtain titanium concentrate. The characteristic of the gravity separation-magnetic separation-flotation process is that the raw ore entering the titanium separation is first classified, the coarse-grained grade is roughly separated by gravity separation, the magnetic separation is used for fine selection, and the fine-grained grade is flotation. Gravity separation uses a shaker, and magnetic separation uses a dry magnetic separator. The flotation feed particle size is generally -0.074 mm, and the flotation machines used include sulfuric acid, sodium fluoride, oleic acid, diesel pine oil, etc. Magnetic separation includes weak magnetic separation and strong magnetic separation. The function of weak magnetic separation is to separate the titanium magnetite remaining in the magnetic separation tailings to facilitate the smooth progress of strong magnetic separation. The purpose of strong magnetic separation is to discharge qualified tailings, improve the selection grade of titanium flotation, and reduce the amount of titanium flotation ore. The use of high-gradient magnetic separation can effectively recover the fine-grained ilmenite in the ore, and throw away part of the fine mud in the ore, thereby achieving the purpose of roughing and discarding the raw ore. The ore is processed using a strong magnetic pre-selection process to improve its grade, laying the foundation for subsequent flotation to obtain the final titanium concentrate.
Coarse particle gravity separation-electric separation, fine particle magnetic separation-flotation
The characteristic of this process is that the selected materials are divided into coarse and fine parts. The coarse particles are processed by gravity separation(rough separation) and electric separation(fine separation). The fine particles are roughly separated by magnetic separation, and then fine particles of titanium concentrate are obtained by flotation.