Extracting silver from lead-zinc ores by heap leaching, it is necessary to determine whether the lead-zinc ore is a sulfide ore or an oxide ore. It is also essential to find out whether the silver is easily soluble in cyanide solution such as horny silver ore, natural silver,and Argentite, or hard soluble in cyanide solution such as insoluble dark red silver ore, light red silver ore, selenium silver ore, and sulfur-antimony copper-silver ore.
After clarifying the minerals’ physical phases, we determine the cyanide’s leaching conditions. If it is zinc oxide ore, zinc is easily dissolved in the cyanide solution, especially smithsonite (ZnCO3), red zincite (ZnO), Hydrozincite (3ZnCO3·2H2O) is particularly easy to dissolve in cyanide solution, consuming a large amount of cyanide. The generated Zn(CN)2 will be deposited on the surface of gold particles to hinder the dissolution of silver. If the ore contains a small amount of lead, it is beneficial to the cyanidation of gold and silver. Lead can eliminate the harmful effects of alkali metal sulfides in the cyanide solution. When leaching gyroscope (AgS), lead salts can cause the formation of S2- in Na2S precipitates into PbS, thereby promoting the dissolution of silver in cyanide solution. Still, it does not have the above effect for complex silver sulfate ores.
Excessive lead particularly impacts the leaching rate of gold and silver. The leaching rate of gold and silver will decrease with the increase in the amount of lime.
Measures for processing silver-bearing ores
- Use a high-concentration cyanide solution (0.2~0.6%NaCN) to leach to ensure the dissolution of silver.
- The heap-leaching ore must have good permeability and porosity to provide the oxygen needed to dissolve silver.
Heap Leaching Procedure
1. Construction of heap leach field
Generally, select the heap leach site in a gently sloping mountainous area close to mining and transportation. Remove weeds and floating soil first, then compact to build a foundation with a slope of 3 to 5% to facilitate the self-flow of the leaching liquid into the storage tank. We should make a lean solution pool, an expensive solution pool, and flood control facilities near the heap leach site.
2. Ore pretreatment
The purpose of pretreatment is, on the one hand, to make the ore reach a specific particle size. The cyanide leachate can fully contact the silver, and on the other hand, the ore has good permeability so that the leachate can evenly penetrate the ore pile.
Pretreatment methods include crushing to appropriate particle size and heap leaching; after crushing, granulation and heap leaching. We can crusher ores generally suitable for heap leaching below 30mm and above 10mm.
3. Build a pile
Pile building is one of the main links in the heap leaching process. The method of pile building is related to the permeability of the heap, the uniform distribution of coarse and fine particles, etc., and directly affects the leaching rate of silver.
Piles can be built manually or mechanically.
When building piles, efforts should be made to avoid crushing the ore to produce secondary sludge and to avoid local compaction and segregation of ore particles. This ensures uniform distribution of ore particle size and good water and air permeability of the ore pile so that cyanide solution and oxygen can flow through the entire ore pile and avoid channeling and siltation areas during leaching.
The methods of pile building include divided pile building method, layered pile building method, and segmented and layered pile building method.
The height of heap leaching depends on the scale, generally 2 to 5 meters.
4. After building the ore pile, set up pipelines and prepare for spraying
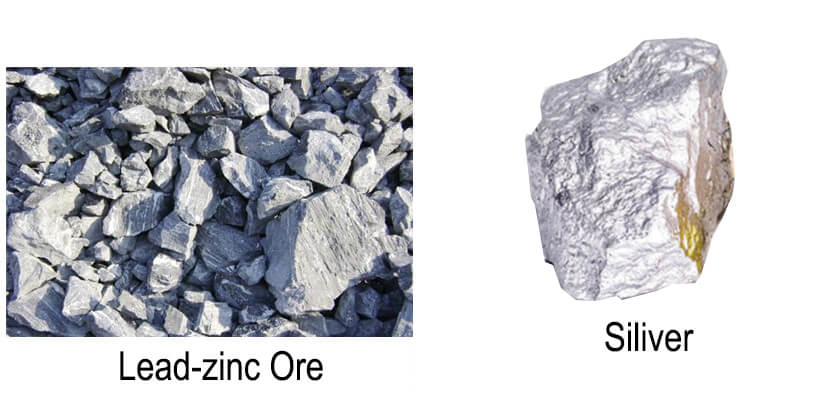
5. Spray leaching
Wash the ore pile with water and alkali before spraying the cyanide solution. When the pH value of the washing solution reaches 9.5 to 11, respray the cyanide solution.
1) Spray equipment
Uniform liquid distribution is an essential factor in improving the leaching rate. There are two methods of liquid distribution: spray liquid distribution and dripping liquid distribution. Regardless of the liquid distribution method, the leaching liquid should cover the entire ore pile. The flow at each point on the surface is balanced, and the evaporation and drift are slight. The liquid distribution system should use anti-corrosion materials like polyvinyl chloride plastic.
2) Leaching
① Ore washing
To reduce the consumption of cyanide and alkali, we use CaO aqueous solution or NaOH aqueous solution to perform alkali washing (water washing first and then alkali washing if necessary)before spraying the cyanide solution on the ore pile. The lime aqueous solution is cheap, but the ore washing time is long, and it is easy to form calcium, while NaOH aqueous solution has a short ore washing time and is expensive. When the pH value of the solution flowing out of the ore pile reaches 9.5 to 11 (usually 3 to 5 days), NaCN can be used as an alkali mixture for spray leaching.
② Spray leaching
- Keep appropriate cyanide, alkali, and oxygen concentrationsthroughout the heap-leaching process.
- Control the sodium cyanide concentration between 0.02 and 0.1% in the leaching solution.
- Control the concentration of NaCN in stages. Generally, it is08 to 0.1 at the beginning, 0.05 to 0.06% in the middle period, and 0.02 to 0.05% in the later period. During production, regularly measure the cyanide concentration and pH value of the leach solution and adjust promptly, usually 1 to 2 times daily.
③ Spray intensity
Spray intensity is generally 10 to 20 liters/m2.
The size of the ore pile is large, and the permeability is poor, which is a small value, and vice versa. The spray method can be continuous spraying of cyanide solution or intermittent spraying. Intermittent spraying is beneficial to oxygen supplementation and leaching of gold and silver. Spray cyanide solution for 2 hours, wait 1 hour, and then spray again.
Always check whether the nozzle pipe is blocked when spraying alkaline cyanide solution. Take measures for areas that cannot be sprayed so that the solution can be spread to every place to ensure the leaching rate of silver.
Add an appropriate amount of anti-scaling agent to the cyanide leachate to prevent nozzle pipes and ore piles from scaling.
④Heap leach time
The time required for heap leaching is determined by experiments depending on factors such as the nature and particle size of the ore, usually 1 to 2 months and up to 3 months in the longer term. Spraying can be stopped when the gold grade in the effluent is lower than 0.1 g/m3.
The leached gold and silver noble liquor flows into the precious liquor pool. It recovers gold and silver by carbon adsorption, zinc replacement, direct electroplating, and other methods.
6. Ore pile washing
After the heap leaching is completed, the ore pile is washed with clean water, and the washing liquid is recovered and used to prepare new leach liquid. After washing, the tailings are disinfected, usually by spraying bleaching powder solution, and the washing water can flow into the flood control pool and the lean liquid pool. After treatment, the cyanide concentration can be reduced to the national emission standard (<0.5 mg/L) before discharge.
Factors that affect the heap leaching process include cyanide concentration, oxygen content, pH value, spray intensity, ore properties, permeability of the ore pile, temperature of the leaching process, etc.
In order to improve the leaching speed and leaching rate of gold and silver in ores, the following aspects of research are currently being conducted.
- Use O2 instead of air. For example, 36 days after O2 ventilation, the gold leaching rate can be increased from 82% to 91%.
- Use hydrogen peroxide or calcium peroxide to increase the oxygen content of the ore pile.
7. Recovery of gold and silver from heap leach liquor
The zinc replacement precipitation method is generally used for noble liquor with high gold and silver grades and large noble liquor volumes. It is not advisable to use the activated carbon adsorption method because silver will compete with gold for adsorption, reducing its adsorption.
For mines with medium heap leaching scale and average gold and silver content, activated carbon or resin adsorption-desorption-electrodeposition processes can be used to obtain precious metals.
The gold and silver content in the heap leach liquor is relatively high (more than 30-50 mg per liter). After clarification, the gold and silver are directly extracted by electrodeposition.
The activated carbon adsorption method is simple and has a low investment cost, so it is widely used in heap leaching.
When the silver content in the gold-containing noble liquid is high, sodium sulfide can be used to precipitate the silver first, and the silver is precipitated in the state of silver sulfide. Before the noble liquid enters the adsorption operation, the silver (silver sulfide precipitation) is removed from the noble liquid by filtration to eliminate carbon. During the adsorption process, the high concentration of silver ions affects the adsorption of gold by activated carbon. It increases the gold adsorption capacity of the carbon, thus reducing the processing volume of desorption and electroplating and reducing production costs.