The Democratic Republic of Congo (DRC), as one of the countries with the richest mineral resources in central Africa, possesses the world’s important tin ore resources. Its sand tin ore is famous for its high grade and easy to mine, but the prevailing problems of high mud content and complex mineral composition also bring great challenges to ore dressing. I’ve seen countless miners struggle with low recovery rates. What if I told you there’s a proven way to clean this ore effectively?
To beneficiate muddy tin ore in Congo, you need to first wash and deslime it thoroughly. Then, gravity separation methods like jigging or shaking tables help recover coarse tin. Fine tin requires advanced techniques like centrifugal concentrators. Finally, cleaning steps ensure high-grade concentrate. The exact process depends on your ore’s specific characteristics.
The Congo holds some of the world’s richest tin deposits, but they’re famously difficult to work with. Let me walk you through everything needed to turn this challenging resource into profitable production.
Table of Contents
What is The Overview of Congo (DRC) Tin Ore Resources?
Working in Congo’s tin mines for years has shown me their unique challenges. The deposits differ significantly from other global tin sources, making standard approaches often ineffective.
Geological Background and Deposit Characteristics
The tin resources of the DRC are mainly distributed in the Kivu, North Kivu, and Maniema provinces in the eastern region, which are part of the famous Central African Tin Belt. There are two main types of tin deposits in the country:
Primary tin deposits
- Type: mainly hydrothermal quartz vein deposits.
- Mineral composition: cassiterite (SnO₂) and quartz symbiosis, often accompanied by wolframite, and columbite-tantalite.
- Typical mining areas: Manono, Kalima.
The Manono-Kitotolo belt stretches over 60km and contains three main deposit types:
Deposit Type | Tin Grade | Key Characteristics | Processing Challenges |
Alluvial | 0.5-1.5% | Fine-grained, high clay | Clay removal, slime loss |
Eluvial | 1-3% | Coarser, less clay | Less washing needed |
Hard Rock | 2-4% | Coarse cassiterite | Requires crushing |
Secondary alluvial tin deposits
- Mechanism of formation: The primary ore deposit is formed by weathering, erosion, transportation, and sedimentation.
- Distribution characteristics: distribution along the rivers and floodplains.
- Mineral characteristics: cassiterite is in a free state, with particle size 0.1-2mm.
- Accompanying minerals: ilmenite, zircon, monazite, and other heavy minerals.
- Typical mining areas: Mwaha, Nyamulange.
Typical characteristics of mud-bearing alluvial cassiterite
Alluvial cassiterite ores of industrial value in DRC usually show the following characteristics:
Physical Properties
- High mud content: -0.074mm mud content usually reaches 30-50%.
- High moisture content: natural moisture content 20-35%.
- High viscosity: mud is mainly clay minerals such as kaolinite and montmorillonite.
Mineral Composition
- Main useful minerals: cassiterite (SnO₂), content 0.3-1.5%.
- Main chalcogenide minerals: light minerals such as quartz, feldspar, and mica.
- Accompanying heavy minerals: ilmenite, zircon, rutile, and monazite (often with comprehensive recycling value).
Cassiterite characteristics
- Nesting pattern: mostly angular or semi-circular particles.
- Grain size distribution: mainly concentrated in the range of 0.1-0.6mm.
- Dissociation: cassiterite is basically completely dissociated in the alluvial ores.
Current status of resource development
The current development of tin ores in DRC is characterized by the following features:
- Small-scale artisanal mining is predominant: accounting for 70% of the output.
- Low degree of mechanization: only a small number of medium-sized and large-scale mines have adopted modern mining equipment.
- Low recovery rate: the recovery rate of cassiterite from artisanal mining is usually only 30-50%.
- Outstanding environmental problems: uncontrolled mining has led to serious ecological damage.
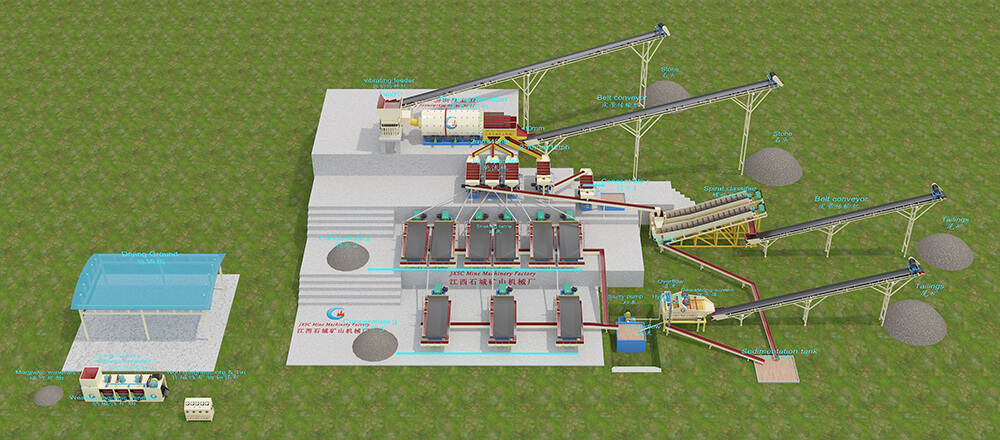
According to the statistics of the Congolese Ministry of Mines, the country’s annual production of tin concentrates (60% Sn) is about 15,000-20,000 tons, and the actual potential of the resources is far greater than this. With the rise of international tin prices and the adjustment of mining policies, more and more enterprises have started to invest in the construction of modernized mineral processing plants.
How to Study The Process Mineralogy of Muddy Tin Ore?
When we first analyzed Congo tin ore, the mineralogy shocked us. Standard assumptions from other regions simply didn’t apply here.
Process mineralogy studies for muddy tin ore should focus on:
- Complete mineral identification using XRD and microscopy.
- Detailed particle size analysis including slimes.
- Liberation studies at different grind sizes.
- Surface chemistry analysis These reveal how to best liberate and recover the tin minerals.
Essential Analysis Steps
For reliable results, follow this sequence:
1. Sample Preparation
- Collect representative samples from multiple locations
- Preserve natural moisture content
- Avoid over-crushing initially
2. Mineral Identification
- XRD for bulk mineralogy
- SEM-EDS for individual grains
- Microscopy for textural relationships
3. Key Parameters to Measure
Parameter | Method | Importance |
Grain size | Sieving + Laser | Determines liberation size |
Liberation | QEMSCAN | Shows needed grind size |
Surface chemistry | Zeta potential | Affects flotation response |
Interpretation Guidelines
- For coarse tin (>0.1mm): Focus on gravity recovery early
- For fine tin (<0.1mm): May need enhanced gravity or flotation
- For slimes (<0.01mm): Consider scavenger circuits We found cassiterite often occurs as:
- Free grains in coarser fractions
- Composite grains with iron oxides
- Micro-inclusions in quartz
Ore material composition analysis
Quantitative analysis of mineral composition (typical mining area)
Mineral Name | Chemical Formula | Content (%) | Density (g/cm³) | Magnetic Properties |
Cassiterite | SnO₂ | 0.3-1.5 | 6.8-7.1 | None |
Ilmenite | FeTiO₃ | 1-3 | 4.5-5.0 | Weak magnetic field |
Zircon | ZrSiO₄ | 0.2-0.8 | 4.6-4.7 | None |
Monazite | (Ce,La)PO₄ | 0.1-0.5 | 4.9-5.3 | None |
Quartz | SiO₂ | 50-70 | 2.65 | None |
Feldspar | KAlSi₃O₈ | 10-20 | 2.5-2.6 | None |
Clay minerals | – | 15-35 | 2.4-2.8 | None |
Chemical composition analysis(%)
Ingredients | Sn | Fe₂O₃ | TiO₂ | ZrO₂ | SiO₂ | Al₂O₃ | Others |
Content | 0.2-1.0 | 3-8 | 0.5-2 | 0.1-0.5 | 60-75 | 10-15 | Remainder |
Cassiterite embedding characteristics
Particle size distributionParticle size (mm) | Cassiterite distribution rate (%) | Cumulative distribution rate (%) |
+1.0 | 5-10 | 5-10 |
1.0-0.5 | 25-35 | 30-45 |
0.5-0.2 | 40-50 | 70-95 |
-0.2 | 5-10 | 100 |
- Mostly irregular angular, some semi-rounded.
- The surface is often contaminated by iron film.
- Microcracks often surround fine-grained gangue inside.
Key factors affecting separation
High mud content
- Increases slurry viscosity and worsens the separation environment.
- Adsorbs mineral processing agents and increases consumption.
- Encapsulates fine cassiterite and reduces recovery rate.
Mineral density is similar
- Cassiterite has a similar density to zircon, monazite, etc. (6-7g/cm³)
- Conventional gravity separation is difficult to effectively separate.
Fine-grained cassiterite loss
- -0.074mm cassiterite accounts for about 10-15% of the total.
- Traditional processes are difficult to effectively recover.
What Are The Process Flows of Muddy Tin Ore Dressing?
After testing dozens of flowsheets in Congo, we’ve identified the most effective approach. It combines robust pre-treatment with targeted separation.
An optimal process flow for muddy tin ore includes:
- Washing and desliming to remove clays
- Screening to separate size fractions
- Gravity separation for coarse tin
- Fine tin recovery using enhanced gravity or flotation
- Concentrate cleaning steps Tailoring each stage to your ore’s characteristics maximizes recovery.
Detailed Process Breakdown
Pre-treatment Stage
- Log washer for clay removal
- Two-stage trommel screening
- Hydrocyclones for slime control
Gravity Separation Options
Method | Best For | Recovery % | Grade % |
Jigging | +1mm | 85-90 | 40-50 |
Shaking Table | 1mm-0.1mm | 75-85 | 50-60 |
Spirals | 0.1-0.05mm | 60-70 | 30-40 |
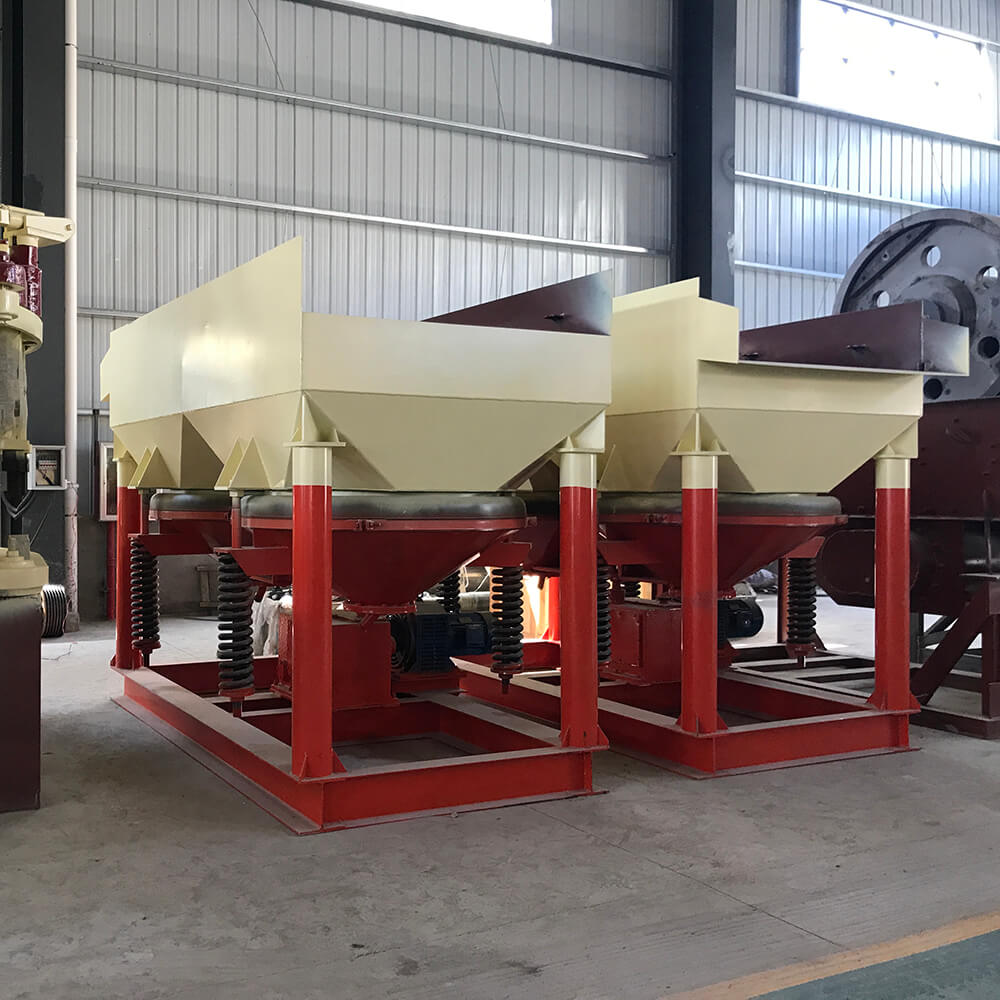
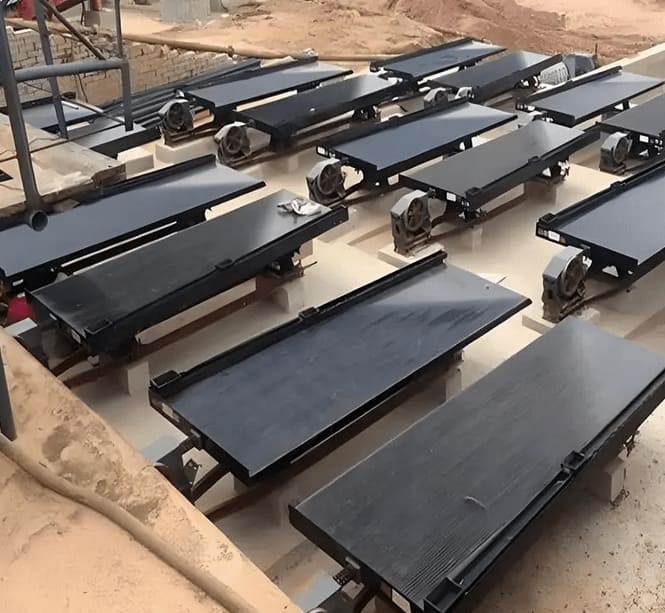
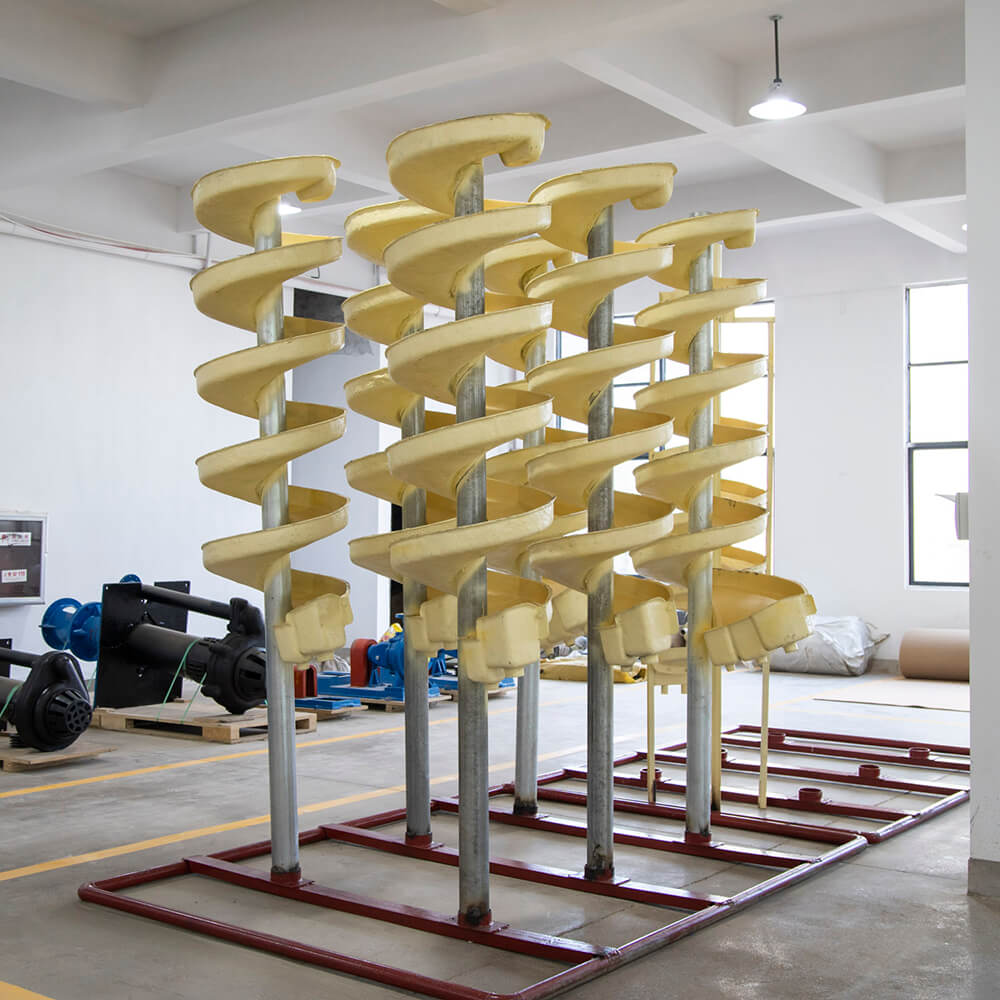
Fine Tin Recovery
- Centrifugal concentrators for 0.1-0.01mm.
- Considerations for <0.01mm: Froth flotation with specific collectors; Wet high-intensity magnetic separation.
Equipment Selection Guide
Based on Congo conditions, we recommend
- Rubber-lined equipment for wear resistance
- Simple, robust designs for maintenance ease
- Modular plants for remote sites
Key operating parameters
- Feed density: 30-35% solids
- Water requirements: 5-7 m³/ton
- Power: 15-25 kWh/ton
Conclusion
Muddy tin ore from Congo presents unique challenges but offers great potential. Successful beneficiation requires thorough mineralogy studies followed by tailored processing flows. The key lies in proper desliming, multi-stage gravity separation, and advanced fine tin recovery. With the right approach, recovery rates above 75% become achievable even for these difficult ores.