The best method for tailings gold beneficiation is gravity separation, which is also the most used method in gold tailings recovery and enrichment projects. This method is characterized by its non-polluting, low production cost, high recovery rate, and fully automatic tailings recovery. It’s welcomed by customers.
Tailings gold beneficiation also needs to be designed according to the condition, fineness, mud content, and previous beneficiation process of the ore material. It depends on which process is suitable for the ore material to be recovered. More than 95% of the ore material adopts the gravity separation method. Recycling, now the more advanced equipment can recover -400 mesh tailings because these gravity separation equipment developed for tailings recovery are not common gravity separation equipment, and common gravity separation equipment such as jig can not be recovered. For ultra-fine particles, only the gravity separation equipment customized for tailings recovery can recover this ultra-fine heavy metal.
There are dozens of equipment corresponding to the gravity separation method, and the tailings corresponding to each type are also different, and the effect of each type of tailings selection is also different. The equipment corresponding to the tailings gravity separation method is common as follows: felt machine, suspension vibration concentrator, reciprocating concentrator, tailings centrifuge, Nelson centrifuge, eddy current centrifuge, felt chute, cone concentrator, rotary Stream concentrator, etc. These equipment are relatively common ones used in tailings gold beneficiation projects. Following we will introduce some beneficiation processes to recover gold tailings.
Gravity Process of Beneficiation
First, the collected ore samples are sent to the spiral chute, and then the samples are processed. Generally, they are processed into three types, such as medium ore, coarse sand, and fine mud, and then the coarse sand is selected. The inlay of gold, minerals, and pyrite is very close, and the gold content of the ore sample is relatively small, about 0.13g per ton. Recycling of its metal substances.
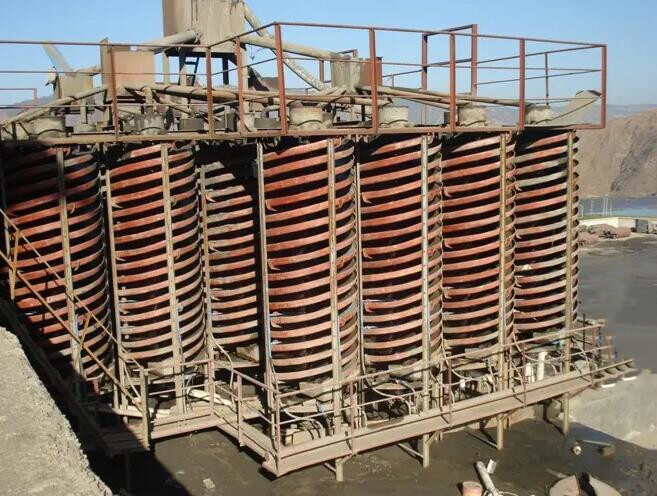
The most indispensable part of the ore process engineering is the shaking table operation so that the recovered products can not only be applied to metal ores or gold mines. After the shaking table and other processes, the gold content of the gold grade can reach per ton of gold ore, and the survival rate in the spiral chute will be between 0.09%, which means the survival rate of the ore sample for the tailings of the concentrator will be around 1.3%, but most of its production is metal concentrates with lower grades obtained by using shakers. The daily productivity in the concentrator can reach 1,000 tons of ore production, and then 30 grams per ton of concentrate can be obtained after processing by the shaking table process. The two are incorporated into the leaching system, which can effectively recycle and utilize the two and can also process them again.
Strong Magnetic Iron Removal Process for Beneficiation
The medium ore produced in the process of processing through the spiral chute is very rich in iron, sulfur, and other substances, which are not suitable for use as raw materials for ceramic production, so there is some gap in the technical standards of ceramic production. It is necessary to further remove iron minerals and sulfur minerals. Since iron minerals and sulfur minerals have their own forms, various removal schemes and process treatments can be adopted. One of the methods is to grind them and then adopt weak magnetic screening. After screening, they can be removed. Placed at the stage of the flotation process.
Another way is to select it by strong magnetic screening and give flotation after strong magnetic selection. After the whole process is completed, iron minerals and sulfur minerals can be removed. By comparing the two methods, strong magnetic screening is obviously much cleaner than weak magnetic screening, so most companies will choose the second method. The medium ore produced after the spiral chute treatment can be applied to the stencil medium. Although the toothed plate medium is more commonly used, it is not as effective as the stencil medium. The magnetic induction intensity used in iron removal is about 1.8T. This iron removal operation can effectively improve the work efficiency of the operation.
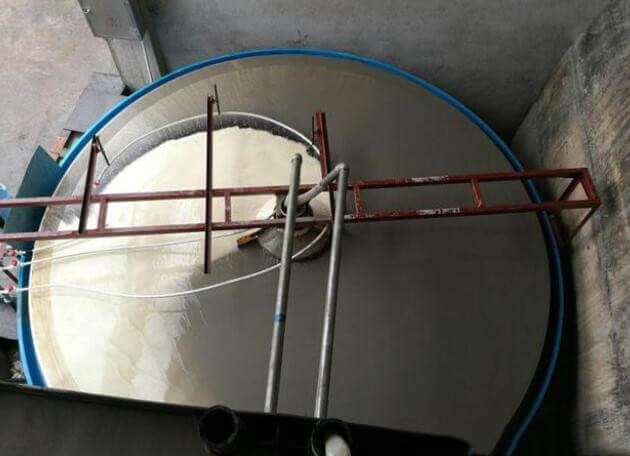
Desulfurization Process Test
After the strong magnetic treatment, there are even some residual sulfur impurities. The sulfur impurities contain pyrite. After the strong magnetic treatment, reverse flotation technology can be used to remove the pyrite. This technology is mainly Reverse flotation used to remove feldspar. If only xanthate is simply added, the sulfur cannot be removed. Therefore, some butyl xanthate can be appropriately added for flotation. Only in this way can the sulfur be better of removal.
Under normal circumstances, the more common dispensing method is 500 grams of lime per ton, 200 grams of copper sulfate, 300 grams of collector, BK413 is generally selected as the collector, 30 grams of butyl xanthate, and 27 grams of foaming agent.
Applied Effects
It can be seen from the above process application and analysis that the ore samples existing in the tailings of gold beneficiation are processed by the spiral chute, and the combination of the two technologies of strong magnetic and shaking table technology can effectively obtain the content of iron and sulfur. Relatively low feldspar powder. Among them, the shaking table tailings can be carried out by underground filling. In the various operations of the process, fine mud, etc. will be transported to the tailings dam through pipelines, and the remaining feldspar powder can be used for the production and production of ceramics middle.